Эпоксидным смолам, без использования которых трудно представить себе современное высокотехнологическое производство, часто приходится работать в очень жестких условиях. Это и повышенная радиация, и воздействие на изделия из эпоксидок химических реагентов, и широчайший диапазон температур, от минус 30 до 200°C градусов. Притом имеется в виду не разовое экстремальное понижение или повышение до указанных пределов, а постоянное воздействие таких температур на связывающий материал.
Нет нужды говорить, что бытовой клей ЭДП или смола ЭД-20, ЭД-22 для подобных температурных перепадов не годятся. Уже полностью отвержденные, они начнут сначала трескаться, потом, в зависимости от применимого когда-то отвердителя, вспенятся, не переходя в жидкую фазу, и начнут разрушаться на мелкие фракции, меняя цвет и структуру.
Могут и загореться, опять-таки в зависимости от исходных веществ и в каком виде были полимеризованы, в виде тонкого покрытия или монолита, занимающего определенный и большой объем в пространстве. Тонкая эпоксидная пленка может воспламениться с выделением огромного количества копоти, если она напрямую контактирует с открытым пламенем. Но горение будет продолжаться только до того момента, пока сохраняется такой контакт и идет интенсивная подпитка теплом. Уберите пламя от эпоксидной пленки, и она тут же погаснет.
Поэтому говорить о пожароопасности использования эпоксидных компаундов в быту или при ремонте не стоит. Горят они не лучше других искусственных материалов, и уж намного безопаснее того же вспененного полистирола или пенопласта, вспомните хотя бы ночной клуб «Белая лошадь» с его многочисленным жертвами от продуктов горения потолочной плитки, с выделением при этом фосгена.
Поэтому говорить о какой-то температуре плавления застывшей эпоксидной смолы нет смысла, в подавляющем большинстве случаев она не плавится, а просто разрушается, превращаясь в бесструктурную обугленную массу.
Огнеупорные смолы
Существуют огнеупорные смолы, это, в первую очередь, безгалогенные KDP-555MC80, KDP-540MC75, KDP-550MC65. Первые цифры в индексе после буквосочетания KDP означают критическую температуру, которую может выдержать эта смола, при ее использования в качестве связывающего каких-нибудь композитов. Основная область применения таких огнеупорных смол – авиационная и космическая промышленности, где материалы, сделанные с использованием KDP, применяются в изготовление внешних контуров крыльев, обтекателей, выдерживающих большие динамические нагрузки управляющих полетом стабилизаторов, элеронов и лонжеронов.
Немалую долю в огнестойкость таких материалов вносят углепластики, которые способны выдержать и кратно высокие температуры. Но сама основа приобретает огнеупорные свойства, в первую очередь, из-за вносимых в нее в процессе полимеризации добавок в виде элементоорганических соединений. В первую очередь – кремнийорганики.
Во время модификации эпоксидной смолы этими элементами происходит изменение многих свойств такой смолы, и часто весьма существенное. Изменения не проходят даром, при сохранении главного параметра в виде термостойкости требуется обычно еще какой-нибудь один. Например, сохранение некоторой пластичности или стабильности свойств смолы как диэлектрика, притом в широком температурном диапазоне. Обычно этого добиваются включением в полимерную цепочку ациклических диэпоксидов вместо основы диановых смол, но тогда увеличивается хрупкость изделий из такой смолы.
Обычно, чем больше числовой индекс у эпоксидных смол (ЭД 16, 20, 22) тем вернее под воздействием запредельно-высоких температур состоится переход застывшей, полимеризированной формы смолы сразу в деструктивно-кристаллическое состояние, с предварительным растрескиванием монолита. Перехода в какое-то жидкое агрегатное состояние в поведении смолы не предусмотрено. Возможно разве что некоторое предварительное размягчение, смолы деформируются.
Более стойким к воздействию высоких температур оказываются смолы с числовыми индексами ЭД-6 и ЭД-15. При воздействии относительно низких температур в пределах 200-250°C градусов изделия из такой смолы начинают выделять газообразные продукты и бесцветную вязкую жидкость. Это следствие процессов, обратных полимеризации, которая происходила при отверждении продукта. О полноценной обратной реакции речи, конечно, не идет, процессы деструкции преобладают над «расшивкой» молекул, а указанная температура в ее верхнем пределе является критической и предраспадной. При длительности ее воздействия более часа, а тем более при ее повышении, процессы распада эпоксидных компонентов делаются необратимыми, с резким падением всех присущих материалу свойств.
Самые термостойкие материалы эпоксидного ряда получают синтезом фторированных дифенилолпропанов. Эти вещества играют роль скрытых, или латентных отвердителей, химически-нейтральных к смоле при комнатной температуре, но начинающими активно работать на полимеризацию смолы при воздействии на нее температуры в 100°C и более градусов, когда начинают меняться ее химические и физические свойства. К ним относят дициандиамид, меломин, изофталилдигидразид.
Именно изделия из этих эпоксидных смол, с введенными в них пластификаторами кремнийорганического ряда, ставятся в качестве головок обтекателей у выводимых на орбиту кораблей, пускаются на армированные углепластиком элементы динамического управления ракетоносителями и сверхзвуковыми самолетами.
В перспективе разработка элементов силового каркаса элементов управления гиперзвуковыми аппаратами. Верхний предел температуры для них превышает на настоящий момент 550°C градусов. Хотя этого, конечно, мало, но и химики не стоят на месте, разрабатываются новые методы усовершенствования физических свойств олигомеров. Перспективным представляется направление с введением в состав эпоксидных полимеров мелкодисперсных порошков из тугоплавких металлов или их карбидов, например, карбида вольфрама.
Обычные составы
Впрочем, описываемые смолы сложны в производстве, требуют специальных боксов-реакторов для отверждения, огнеупорных форм, в которых делаются эти отливки, так что массовому потребителю они малоинтересны, да еще и чрезвычайно дороги. Более интересны для него были бы обычные смолы класса ЭД или его аналогов, в которых для отверждения использовались нестандартные вещества, да еще с введением в них наполнителей пластификаторов, повышающих термостойкость.
Наибольший спрос на жаропрочные материалы из эпоксидных смол отмечается у авто- и мотолюбителей. Камнем преткновения у которых чаще всего выступают компоненты соединений в глушителях, которые быстро выгорают. Вот здесь жаростойкость изделий из эпоксидки или материалов с нею может быть усилена применением армирования прокладок углепластиком или даже самым обыкновенным стеклопластиком.
С введением в застывающую смолу в местах соединения или прокладок дополнительного армирующего и цементирующего элемента в виде мелкодисперсных стальных опилок или даже алюминиевой пудры, которая в связке со смолой отлично держит температуру до 340°C градусов. Правда, страдает ударная прочность такой смолы.
Смолы с наполнителями, а тем более армированные, и подавно не поддаются плавлению. Речь может идти только о постепенном их обугливании и разрушении.
Если же говорить о полноценном плавлении эпоксидных материалов при воздействии высокой температуры, то оно возможно только с попеременным воздействием на них быстродействующих едких растворителей и высокой температуры. Тогда, наряду с физическими изменениями в кристаллической решетке полимера будет происходить и химическое ослабление межмолекулярных связей.
Очевидно, что температура эксплуатации эпоксидной смолы имеет широкий диапазон. Здесь все зависит от полимерного состава и добавок, внесенных в него.
На чтение 4 мин. Опубликовано
Без эпоксидных смол уже трудно представить современную промышленность и даже высокотехнологичное производство. А это значит, что с такими субстанциями порой приходится работать в достаточно жестких условиях. Например, встречаются следующие факторы: повышенный радиоактивный фон, воздействия агрессивных сред, химических реагентов и температурных скачков. А есть ли температура плавления эпоксидной смолы, ведь после полимеризации она превращается в жесткий и особо прочный материал — об этом в статье.
Технические характеристики эпоксидной смолы
Прежде чем выяснять, какую температуру выдерживает эпоксидная смола после застывания, стоит узнать об основных технических параметрах данной субстанции. Это следующие характеристики:
- полный процесс полимеризации происходит в течение 24–36 часов;
- ускорить процедуру отвердевания смолы можно путем увеличения температурного режима до +70⁰С;
- в условиях пониженных температур (до +15⁰С) время отвердевания смолистой субстанции понижается;
- при затвердевании эпоксидка не дает усадку и не расширяется;
- после отвердевания смолу можно подвергать любым обработкам: шлифовке, полировке, сверлению, обточке, окраске и пр.;
- рекомендованная температура эксплуатации эпоксидной смолы установлена в пределах от -50⁰С до +150⁰С;
- предельно допустимый температурный режим при эксплуатации составляет до +80⁰С;
- отвердевший материал показывает отличные показатели по устойчивости к агрессивным воздействиям, в том числе щелочам, растворителям и повышенной влажности.

Эпоксидная смола обладает ограниченным сроком хранения. Она должна быть использована не позднее 1,5 года с момента ее выпуска.
Температурный режим плавления вещества
По техрегламенту установлено, что температура, при которой происходит плавление эпоксидки, составляет +155⁰С. Но, учитывая заявленные технические характеристики, говорить о том, что эпоксидка станет плавиться, сложно. Даже термостойкий эпоксидный клей или привычная для бытовых работ эпоксидка ЭД-20 после полимеризации даже в условиях сверхвысоких температур будут вести себя следующим образом:
- растрескиваться;
- пениться;
- менять свою структуру, не переходя в жидкое состояние (крошиться и ломаться).
Некоторые смолы (в зависимости от типа используемого отвердителя) могут загораться, причем выделяя большое количество копоти. Процесс горения продолжится до момента тепловой подпитки (например, в условиях открытого пламени). Как только источник огня будет ликвидирован, застывшая смола гореть перестанет.
Несмотря на способность смолы гореть, такое вещество не относится к материалам повышенной пожароопасности.
Даже при горении эпоксидка намного безопаснее многих иных искусственных веществ. Например, пенопласта или вспененного полистирола. Поэтому говорить о том, какую температуру выдерживает эпоксидный клей до момента плавления, не имеет смысла. Практически всегда отвердевшая эпоксидка не плавится, а разрушается, превращаясь в обугленную бесформенную массу.
Есть ли быстрозастывающие смолы
Все эпоксидки подразделяются на две крупные группы. Это конструкционные смолы и декоративные (или ювелирные). Декоративные эпоксидные субстанции отличаются прозрачностью и более быстрым временем полимеризации. Используются они в основном для дизайнерских работ для изготовления сувенирной продукции.

Допустимая температура эксплуатации готовых изделий
Техническими регламентами приняты определенные нормы эксплуатации изделий и отремонтированных вещей, при работе с которыми использовалась эпоксидная смола. Это следующие показатели:
- постоянная температура: от -40⁰С до +120⁰С;
- предельно допустимая: от -40⁰С до +150⁰С.
Но некоторые марки эпоксидок, по оценкам производителей, обладают иными показателями. Например, такими экстремальными (предельно допустимыми) показателями:
- эпоксидный клей марки ПЭО-490К (ЛЗОС, г.Лыткарино): +350⁰С;
- эпоксидка ПЭО-13К (ЛЮМЭКС, г.Санкт-Петербург): +196⁰С;
- компаунд ПЭО-28М (ПЛАНЕТ, г.Великий Новгород): +130⁰С.
Подобные эпоксидные субстанции являются специфическими. Многие профессионалы относят их даже не к эпоксидным, а к эпоксиднокремнийорганическим. Дополнительное включение кремния и создает повышенную устойчивость субстанций к тепловому воздействию.
Полезные советы при работе с эпоксидкой
Температурный режим – один из важных и основополагающих факторов при работе с эпоксидными смолами. Поэтому при использовании смолистой субстанции обязательно следует придерживаться рекомендованных условий. В идеале, в помещении, где происходит процесс полимеризации и заливка эпоксидки, температура должна быть в пределах +24⁰–30⁰С. Следует придерживаться и иных рекомендаций:
- в рабочем помещении должно быть не только тепло, но и сухо;
- ингредиенты до момента смешивания (смолы и отвердитель) находятся в герметично закрытой упаковке;
- при замешивании смеси в смолу добавляется отвердитель, а не наоборот;
- при добавлении катализатора эпоксидку можно немного разогреть до +40⁰–50⁰С;
- стандартное время первой полимеризации смолистой субстанции — 1 сутки при температуре в +24⁰С;
- период набора максимальной прочности составляет до недели;
- при смешивании слишком больших доз смолы и отвердителя, эпоксидка может закипеть и потерять свои рабочие свойства.
Выводы
Эпоксидные смолы – популярный и удобный материал для работы. Но следует понимать разницу между промышленными составами и ювелирной эпоксидкой. При замешивании смолистой субстанции строго придерживайтесь инструкции и не выполняйте все рекомендации специалистов.
Эпоксидные смолы изготавливаются и применяются у нас в стране уже больше 60 лет. Использоваться такие материалы могут как в промышленности, так и в быту. Разновидностей таких средств на рынке сегодня имеется множество. К примеру, очень неплохие отзывы от потребителей заслужила эпоксидная смола ЭД-20. Характеристиками этот материал, как рабочими, так и эксплуатационными, отличается достаточно хорошими.
Форма выпуска
Представляет собой ЭД-20 плавкий и растворимый пластичный материал, являющийся продуктом конденсации дифенилпропана и эпихлоргидрина в щелочных средах. Имеется сегодня на рынке и раствор такой смолы в толуоле. Поставляется этот материал на промышленные объекты в стальных барабанах на 53 кг или флягах. Для бытовых целей эта смола расфасовывается в обычные флаконы. Внешне это средство представляет собой медоподобную вязкую прозрачную жидкость.
Поставляется на рынок ЭД-20 как двухкомпонентный состав. В качестве отвердителя для этого средства используются стандартные материалы. Это могут быть, к примеру, предназначенные для эпоксидных смол ТЭТА, ПЭПА и пр. В твердом виде этот материал является диэлектриком и отличается стойкостью к разного рода растворителям.
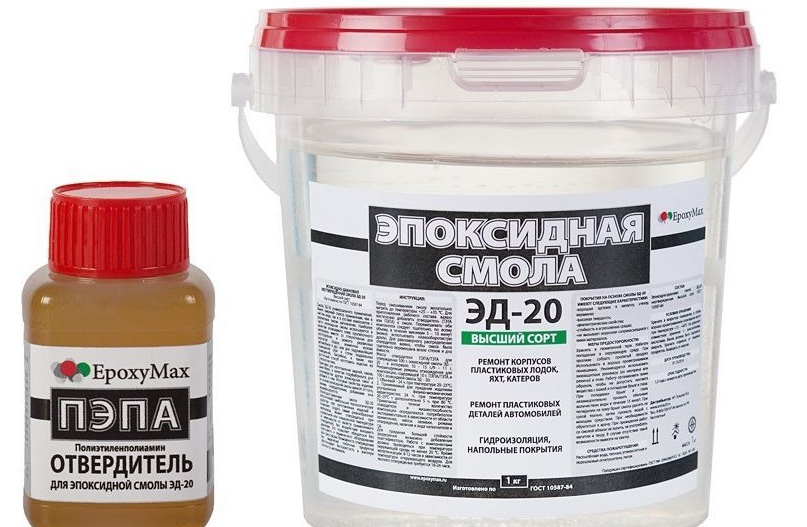
Состав по ГОСТ
Характеристики эпоксидной смолы ЭД-20, как и любого другого подобного материала, определяются, конечно же, в первую очередь ее составом. Согласно действующим нормативам, ЭД-20 должна содержать:
массовую долю эпоксидных групп — не более 20-22,5 %;
омыляемого хлора — 0,3-0,8 %;
иона хлора — 0,001-0,005 %;
гидроксильных групп — 1,7 %;
летучих веществ — 0,2-0,8 %.
Средняя многочисленная доля эпоксидных групп в этом материале равна 20 %, что отражено в его названии.
Производитель и срок хранения
Поставляет на рынок стран постсоветского пространства и за рубеж это средство ФПК «Завод им. Свердлова». Основано это предприятие было еще до революции — в 1916 г. В настоящий момент оно относится к объектам оборонного комплекса. Головной офис компании находится в г. Дзержинске. Также эту смолу выпускают и некоторые другие заводы на территории постсоветского пространства.
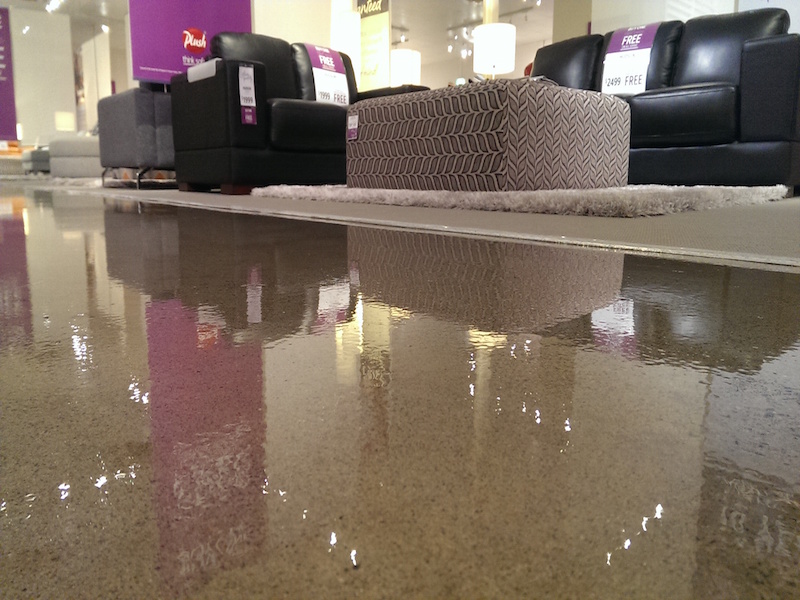
Гарантийный срок хранения этого материала составляет 18 месяцев со дня изготовления. Отвердитель ЭД-20 может при этом не терять свои свойства с даты выпуска в течение 2 лет. Храниться этот материал должен в темном месте при температуре не выше 40 °С.
Технические характеристики эпоксидной смолы ЭД-20
Одной из особенностей этого средства является неэластичность. Никаких пластификаторов в такую смолу при изготовлении не добавляется. При движении поверхностей под отвердевшим слоем этого материала на нем могут появиться трещины.
Вязкость у этой смолы в рабочем состоянии достаточно высокая. Поэтому очень часто ее перед использованием разбавляют растворителями.
Помимо этого, эпоксидная смола ЭД-20 отличается следующими характеристиками:
время полимеризации — 1,5 часа;
время полного застывания — 1 сутки;
ударная вязкость — 5-25 кдж/м2;
теплостойкость — 55-170 °С;
прочность при изгибе — 80-140 МПа;
плотность при 20 °С — 1,16-1,25 кг/м3.
Вот такие имеет эпоксидная смола ЭД-20 характеристики. Температура применения этого материала минимальная равна 20 °С. Такой способ использования называется холодным. В промышленных условиях затвердевание этого материала может происходить и при очень высоких температурах. Это так называемый горячий способ полимеризации.
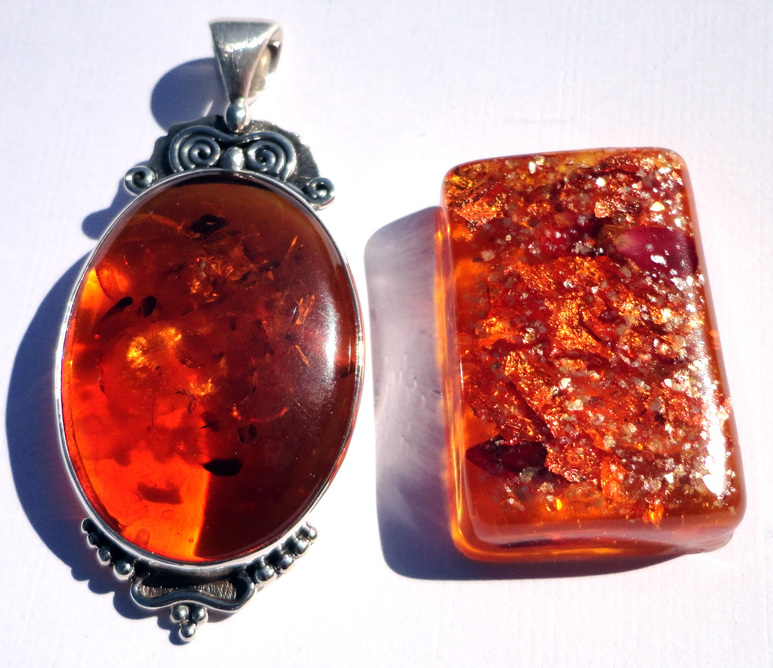
Традиционные сферы применения
Усадку при использовании ЭД-20 дает очень небольшую. К тому же, как мы выяснили, полимеризуется это средство достаточно быстро. Благодаря таким свойствам применение этот материал нашел очень широкое как в промышленности, так и в строительстве или быту. Использоваться смола ЭД-20, технические характеристики которой делают это средство практически универсальным, может, к примеру:
в приборостроении;
в авиапромышленности;
мебельной промышленности;
при ремонте элементов конструкции автомобилей;
в радиотехнической промышленности.
Очень широко этот материал применяется и дизайнерами. Из него могут создаваться, к примеру, столешницы, галантерейные изделия, разного рода влагостойкие товары, предназначенные для использования в ванных комнатах. Применяется эпоксидка и для грунтования разного рода поверхностей.
Еще одной областью использования ЭД-20 является изготовление эмалей, лаков, шпаклевок. Также с применением этого материала делают и эпоксидные смолы других марок. В быту этот материал часто используется в качестве клея. С его применением допускается скреплять как дерево, так и металл, пластик, керамику, стекло.
Где еще может использоваться
Технические характеристики эпоксидная смола марки ЭД-20, таким образом, имеет очень даже неплохие. Поэтому она нашла свое применение в том числе и при производстве разного рода современных материалов. К примеру, достаточно часто это средство используется для пропитки стеклотканей и стеклонитей. Также ЭД-20 применяют для:
гидроизоляции бассейнов;
создания углеволокна и пластмасс;
изготовления пластоцементов;
заливки 3D-полов;
герметизации плат компьютеров.
Используется этот материал и при изготовлении бронежилетов.
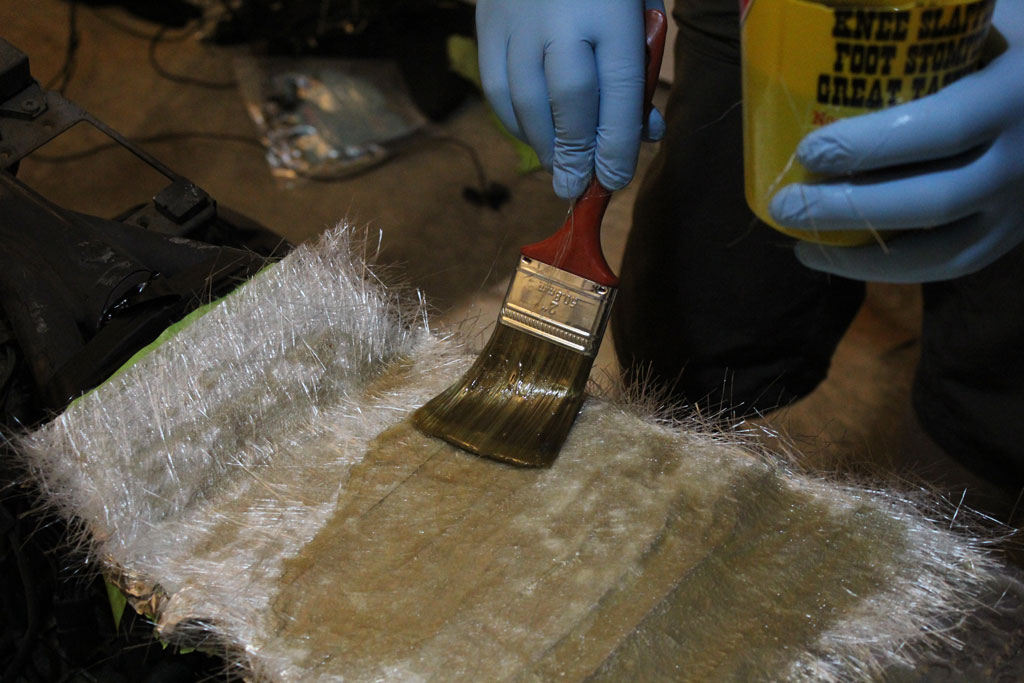
Важно
Как считают многие мастера, на самом деле имеет очень даже неплохие эпоксидная смола ЭД-20 характеристики. Заливку разного рода материалов и изделий с ее использованием, однако, нужно делать осторожно. Смешивать эпоксидную смолу ЭД-20 с отвердителем допускается только маленькими партиями. Сразу большой объем такого рабочего материала изготавливать нельзя. В противном случае смесь может закипеть и задымиться. К примеру, критический объем ЭД-20 с отвердителем ПЭПА в домашних условиях составляет не более 200-250 г.
Добавлять отвердитель в смолу этой разновидности нужно строго в количестве, рекомендованном производителем. В противном случае он не прореагирует и просто останется в массе. Регулировать скорость схватывания рабочего материала в данном случае, как при изготовлении полиэфирки, нельзя. Подвергать прессованию этот материал при производстве каких-либо изделий не требуется.
С какими средствами и материалами можно комбинировать
Смешивать ЭД-20 допускается со многими другими смолами. К примеру, достаточно часто ее комбинируют с полиэфиркой. В жидком виде при этом две эти разновидности смол никогда не смешивают. Поверхность сначала покрывают эпоксидкой, а затем — полиэфиркой. В обратном порядке эти материалы не применяют. В этом случае комбинирование, к сожалению, дает плохой эффект.
Положительные отзывы
Основным плюсом этого материала потребители, конечно же, считают, универсальность и широкую сферу использования, в том числе и в быту. У людей, предпочитающих ремонтировать разного рода домашние вещи самостоятельно, флакончик такой смолы под рукой имеется всегда.
Также достоинствами этого материала считаются:
простота в применении;
невысокая стоимость;
возможность окрашивания в любой цвет.
Многие мастера считают очень неплохими и другие технические характеристики эпоксидной смолы ЭД-20. Расход этого материала, к примеру, при его невысокой стоимости обычно является небольшим. При грунтовании, например, на 1 м2 пористой поверхности уходит около 150 г ее смеси с отвердителем, а глянцевой — не более 100 г.
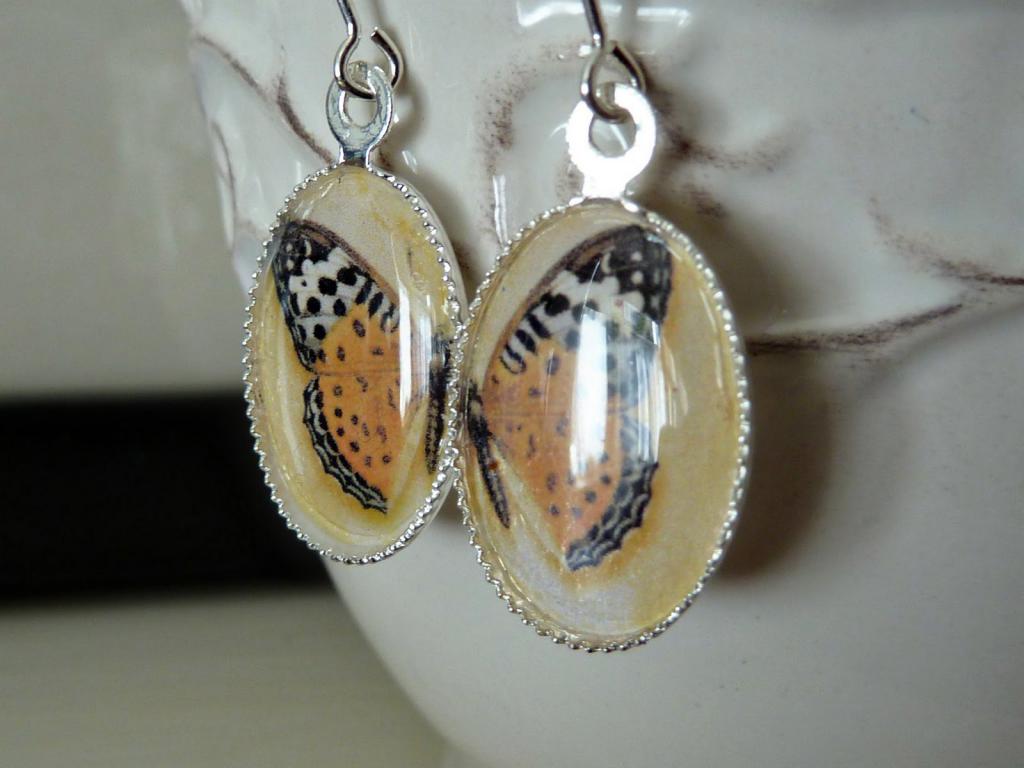
Отрицательные отзывы
Выше мы рассмотрели, какие имеет характеристики эпоксидная смола ЭД-20. Отзывы о ней в Сети, благодаря ее неплохим свойствам, действительно существуют в основном положительные. Но часто на разного рода специализированных форумах потребители отмечают и некоторые недостатки этого материала. Основным минусом такой смолы считается, конечно же, то, что из-за риска закипания ее нельзя заливать очень толстым слоем.
Также к недостатком ЭД-20 относят и наличие в ее толще пузырей после застывания. Чтобы избежать появления такой проблемы, опытные мастера советуют при нанесении прогревать это средство горелкой.
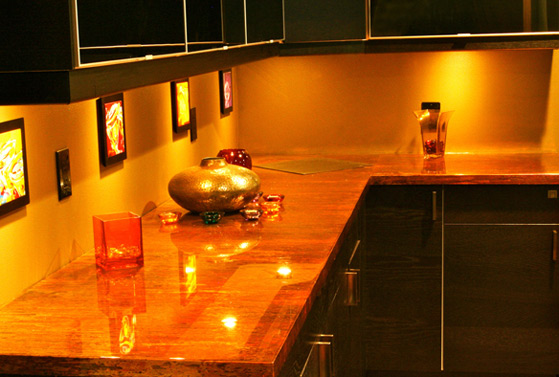
Многие потребители считают ЭД-20 все же прошлым веком. Судя по отзывам, современные аналогичные средства, имеющиеся на рынке, хотя и стоят дороже, в использовании все же могут считаться более удобными. К примеру, аналог ЭД-20 чешская смола CHS Epoxy 520 с отвердителем 921 ОП отличается прозрачностью и может заливаться достаточно толстым слоем без пузырей.
Какую температуру выдерживает эпоксидная смола?
Для получения качественного материала, обладающего высокой прочностью и другими полезными качествами, эпоксидная смола подвергается расплавлению. Для этого необходимо знать, какая температура плавления этой субстанции является оптимальной. Кроме того, важными являются и другие условия, необходимые для правильного отвержения эпоксидки.
Предельная температура эксплуатации
Безусловно, температура влияет на рабочее состояние и правильное застывание эпоксидной смолы, но, чтобы понять, какая температура является максимальной для эксплуатации вещества, стоит ознакомиться с её главными техническими характеристиками.
- Полимеризация смолистой субстанции происходит при нагревании поэтапно и занимает от 24 до 36 часов. Полностью этот процесс может завершиться через несколько дней, но его можно ускорить, осуществляя нагрев смолы до температуры +70°С.
- Правильное отвержение позволяет добиться того, что эпоксидка не расширяется, а эффект усадки фактически исключён.
- После того как смола застыла, её можно обрабатывать любым способом – обтачивать, окрашивать, шлифовать, сверлить.
- Высокотемпературная эпоксидная смесь в застывшем состоянии отличается отличными техническими и эксплуатационными свойствами. Она обладает такими важными показателями, как кислотостойкость, устойчивость к высокому уровню влажности, воздействию растворителей и щелочей.
При этом рекомендованной температурой рабочей смолы является режим в пределах от -50°С до +150°С, однако при этом установлена и предельная температура +80°С. Такая разница связана с тем, что эпоксидная субстанция может иметь разные составляющие, соответственно, физические свойства и температуру, при которой она твердеет.
Режим плавления
Многие производственные, высокотехнологичные процессы невозможно представить без применения эпоксидных смол. Исходя из технического регламента плавление смолы, то есть переход вещества из жидкого в твёрдое состояние и наоборот осуществляется при +155°С.
Но в условиях повышенного ионизирующего облучения, воздействия агрессивной химии и чрезмерно высоких температур, достигающих +100… 200°С, используются только определённые составы. Разумеется, речь не идёт о смолах ЭД и клее ЭДП. Такой вид эпоксидных смесей не плавится. Полностью застывшие эти изделия просто разрушаются, проходя стадии растрескивания и перехода в жидкое состояние:
- они могут растрескиваться или вспениваться из-за кипения;
- изменять цвет, внутреннюю структуру;
- становиться хрупкими и крошиться;
- в жидкое состояние эти смолянистые вещества тоже могут не переходить по причине особого состава.
В зависимости от отвердителя некоторые материалы способны воспламеняться, выделяют много копоти, но только при постоянном контакте с открытым огнём. В этой ситуации, вообще, нельзя говорить о температуре плавления смолы, так как она попросту подвергается разрушению, постепенно распадаясь на мелкие составные части.
Сколько выдерживает после застывания?
Конструкции, материалы и изделия, созданные с применением эпоксидной смолы, изначально сориентированы на стандарты температур, установленные согласно принятым нормам эксплуатации:
- постоянной считается температура от –40°С до +120°С;
- максимальной температурой является +150°С.
Но такие требования относятся не ко всем маркам смол. Для специфических категорий эпоксидных субстанций существуют свои экстремальные нормы:
- заливочный эпоксидный компаунд ПЭО-28М – +130°С;
- высокотемпературный клей ПЭО-490К – +350°С;
- оптический клей на эпоксидной основе ПЭО-13К – +196°С.
Подобные составы за счёт содержания в них дополнительных компонентов, таких как кремний и другие органические элементы, приобретают улучшенные характеристики. Добавки введены в их состав совсем не случайно – они увеличивают стойкость смол к термическому воздействию, разумеется, после того как смола застывает. Но не только – это могут быть полезные диэлектрические свойства или хорошая пластичность.
Повышенной устойчивостью к высоким температурам обладают эпоксидные субстанции марок ЭД-6 и ЭД-15 – они выдерживают до +250°С. Но самыми термостойкими признаны смолистые вещества, полученные с применением меламина и дициандиамида – отвердителей, способных вызывать полимеризацию уже при +100°С. Изделия, при создании которых применены эти смолы, отличаются повышенными эксплуатационными качествами – они нашли применение в военной и космической промышленности. Сложно представить, но предельная температура, которая не способна их разрушить, превышает +550°С.
Рекомендации при работе
Соблюдение температурного режима – главное условие при эксплуатации эпоксидных составов. В помещении тоже должен поддерживаться определённый климат (не ниже +24°С и не выше +30°С).
Рассмотрим дополнительные требования для работы с материалом.
- Герметичность упаковки компонентов – эпоксидки и отвердителя – вплоть до процесса их смешивания.
- Неукоснительным должен быть порядок замешивания – именно отвердитель добавляется в смоляную субстанцию.
- Если используется катализатор, смолу необходимо нагреть до +40.50°С.
- В помещении, где проводятся работы, важен не только контроль над температурой и её стабильностью, но и за тем, чтобы в нём сохранялась минимальная влажность – не больше 50%.
- Несмотря на то что первый этап полимеризации составляет 24 часа при температурном режиме +24°С, предельную прочность материал набирает в течение 6-7 дней. Однако именно в первые сутки важно, чтобы температурный режим и влажность сохранялись в неизменном состоянии, поэтому нельзя допускать малейших колебаний и перепадов этих показателей.
- Не стоит замешивать слишком большие порции отвердителя и смолы. В этом случае есть риск её закипания и утраты свойств, необходимых для эксплуатации.
- Если работа с эпоксидной смолой совпала с холодным временем года, нужно заранее прогреть рабочее помещение, поместив туда упаковки с эпоксидкой, чтобы она также приобрела нужную температуру. Холодный состав допускается подогреть, используя водяную баню.
Нельзя забывать, что в холодном состоянии смола становится мутной по причине формирования в ней микроскопических пузырей, а избавиться от них крайне трудно. К тому же субстанция может не застывать, оставаясь вязкой и липкой. При температурных перепадах также можно столкнуться с такой неприятностью, как «апельсиновая корка» – неровная поверхность с волнами, буграми и углублениями.
Однако следуя этим рекомендациям, соблюдая все необходимые требования, можно получить безупречно ровную, качественную поверхность смолы благодаря её правильному отвержению.
В следующем видео рассказывается о секретах эксплуатации эпоксидной смолы.
Эпоксидная смола, свойства, а также ее применение
Эпоксидная смола густая для рисования «Resin Art».
Resin Art Luxe — это средневязкая прозрачная Эпоксидная смола, для всех видов творчества.
Применяется для широкого спектра творческих работ, таких как:
- Изготовление бижутерии
- Рисование картин
- Декоративные напольные покрытия и т.п.
Характеристики простым языком
- Абсолютно прозрачная и устойчива к ультрафиолету (не желтеет со временем)
- Время полного отверждения 24 часа
- Поставляется в комплекте с отвердителем
Стоит отметить, что некоторые характеристики любых эпоксидных смол можно изменять, добавляя те или иные компоненты. Алюминиевая пудра или антипирен, например, увеличивают термостойкость, аэросил — тиксотропность, активные разбавители — прочность на разрыв, удар, изгиб, в большом количестве увеличивают эластичность. Существует масса отвердителей для эпоксидных смол с ускоренным или замедленным временем полимеризации, а также отвердители, работающие при температуре -5°С и даже под водой!
Применение эпоксидных смол
Мы на этом рынке вот уже несколько лет и за это время сформировали свой (точнее ВАШ) список применения эпоксидных смол. Он довольно широк — это строительство и ремонт лодок, яхт, изготовление велотранспорта, бамперов, обвесов, крыльев, корпусов, матриц, бензобаков и др. ёмкостей, дверных карт, торпедо, корпусов для сабов, металлодетекторов, микарты, в авиастроении и авиамоделировании, бижутерия, наливные покрытия, а также ремонт акриловых ванн, поддонов, затирка швов, заливка катушек, микросхем и многое другое!
Эпоксидная смола ЭД-20, тара от 0,5 кг.
Эпоксидная смола ЭД-20 представляет собой прозрачную вязкую жидкость желтоватого цвета без видимых механических включений.
Эпоксидная смола ЭД-20 – двухкомпонентная смола. Для её отверждения требуются отвердители для эпоксидных смол (ПЭПА, ТЭТА, и т.д.).
Смола ЭД-20 используется в промышленности в чистом виде, или в качестве компонентов композиционных материалов — заливочных и пропиточных компаундов, клеев, герметиков, связующих для армированных пластиков, защитных покрытий.
Малоэластична, при движении поверхностей под эпоксидным покрытием, может возникнуть трещина, для повышения эластичности в смолу добавляются пластификаторы.
Эпоксидная смола ЭД-20 достаточно вязкая, поэтому при работе приходится зачастую использовать различные растворители.
Существует два способа временного понижения вязкости смолы: один представляет собой нагревание смеси, а второй – добавление к ней растворителя. В обоих случаях смола становится более текучей. Смола с низкой вязкостью более текуча, ее проще наносить кистью или валиком, она быстро пропитывает стеклоткань и глубже проникает в пористые поверхности.
Характеристики простым языком
- Прозрачная, вязкая, желтоватого цвета
- время полимеризации на отлип – 1,5 часа
- время первичной полимеризации при t 24°С — 24 часа
- время полимеризации для механической обработки — 6-7 дней
- максимальная температура нагрева «сырой» смолы — 60°С
- температура вспышки — 300°С
- температура разрушения отвержденной смолы (плавления) — 90°С
Стоит отметить, что некоторые характеристики любых эпоксидных смол можно изменять, добавляя те или иные компоненты. Алюминиевая пудра или антипирен, например, увеличивают термостойкость, аэросил — тиксотропность, активные разбавители — прочность на разрыв, удар, изгиб, в большом количестве увеличивают эластичность. Существует масса отвердителей для эпоксидных смол с ускоренным или замедленным временем полимеризации, а также отвердители, работающие при температуре -5°С и даже под водой!
Применение эпоксидных смол
Мы на этом рынке вот уже несколько лет и за это время сформировали свой (точнее ВАШ) список применения эпоксидных смол. Он довольно широк — это строительство и ремонт лодок, яхт, изготовление велотранспорта, бамперов, обвесов, крыльев, корпусов, матриц, бензобаков и др. ёмкостей, дверных карт, торпедо, корпусов для сабов, металлодетекторов, микарты, в авиастроении и авиамоделировании, бижутерия, наливные покрытия, а также ремонт акриловых ванн, поддонов, затирка швов, заливка катушек, микросхем и многое другое!
Заливочная прозрачная эпоксидная смола с прозрачным отвердителем Оптик.
Компаунд Оптик успешно применяется при изготовлении прозрачных фрагментов деревянной и металлической мебели — столешниц, подоконников, массивных деталей столов в сочетании с искусственными и натуральными песками, камнями, галькой, щебнем, раковинами моллюсков, зернами кофе, бисером и другими декоративными наполнителями.
Соотношение смола-отвердитель оптимально 10:4, но его можно менять в достаточно широких пределах регулируя скорость отверждения. При изменении соотношения следует помнить о возможной порче изделий при избытке или недостатке отвердителя. При избытке возможна деформация и пожелтение изделия. При недостатке изделие может остаться резиноподобным, липким, или вообще не затвердеть. Наша рекомендация — соблюдать заданное соотношение и взвешивать компоненты на электронных весах. Точность весов должна быть достаточной для того, чтобы зафиксировать вес стаканчика, в котором дозируются компоненты.
В объеме до 200 грамм из Оптик возможно получение прозрачных отливок с гладкой ровной поверхностью. Заливка объемных изделий, объемом больше 200 мл, может осуществляться послойно — слоями. Первый слой может иметь толщину до 1,5 см. Каждый последующий не более 1,0 см. Время между заливкой каждого следующего слоя 12-18 часов.
Перед применением нагреть до комнатной температуры и тщательно промешать механической мешалкой 5 минут. Смола и отвердитель Оптик имеет вязкость не выше, чем у подсолнечного масла. Он легко перемешивается, но требует хорошего совмещения смолы и отвердителя. Рекомендуется после тщательного перемешивания состава перелить его в другую тару и вновь перемешать. Затем произвести заливку изделия.
Стоит отметить, что некоторые характеристики любых эпоксидных смол можно изменять, добавляя те или иные компоненты. Алюминиевая пудра или антипирен, например, увеличивают термостойкость, аэросил — тиксотропность, активные разбавители — прочность на разрыв, удар, изгиб, в большом количестве увеличивают эластичность. Существует масса отвердителей для эпоксидных смол с ускоренным или замедленным временем полимеризации, а также отвердители, работающие при температуре -5°С и даже под водой!
Применение эпоксидных смол
Мы на этом рынке вот уже несколько лет и за это время сформировали свой (точнее ВАШ) список применения эпоксидных смол. Он довольно широк — это строительство и ремонт лодок, яхт, изготовление велотранспорта, бамперов, обвесов, крыльев, корпусов, матриц, бензобаков и др. ёмкостей, дверных карт, торпедо, корпусов для сабов, металлодетекторов, микарты, в авиастроении и авиамоделировании, бижутерия, наливные покрытия, а также ремонт акриловых ванн, поддонов, затирка швов, заливка катушек, микросхем и многое другое!
Германская эпоксидная смола DER-330.
Эпоксидная смола DER 330 — стандартная (базовая) не модифицированная эпоксидная смола, аналог ЭД-20, превышающая её в качестве по некоторым показателям! Эпоксидная смола DER 330 практически прозрачная, более текучая смола без примесей, с эпоксидным эквивалентом 182-192 g/mol. При нагревании до 40-50°С (не выше 60°С) теряет вязкость окончательно и легко смешивается с пластификаторами, пигментами и другими модифицирующими присадками и наполнителями. У нас она всегда свежая, а срок её хранения в правильных условиях до 5 лет и более.
Характеристики простым языком
- цвет практически отсутствует (зависит от партии)
- при температуре 24°С не имеет запаха
- время полимеризации на отлип — 2-3 часа
- время первичной полимеризации при t 24°С — 24 часа
- время полимеризации для механической обработки — 6-7 дней
- максимальная температура нагрева «сырой» смолы — 60°С
- температура вспышки — 300°С
- температура разрушения отвержденной смолы (плавления) — 90°С
Стоит отметить, что некоторые характеристики любых эпоксидных смол можно изменять, добавляя те или иные компоненты. Алюминиевая пудра или антипирен, например, увеличивают термостойкость, аэросил — тиксотропность, активные разбавители — прочность на разрыв, удар, изгиб, в большом количестве увеличивают эластичность. Существует масса отвердителей для эпоксидных смол с ускоренным или замедленным временем полимеризации, а также отвердители, работающие при температуре -5°С и даже под водой!
Применение эпоксидных смол
Мы на этом рынке вот уже несколько лет и за это время сформировали свой (точнее ВАШ) список применения эпоксидных смол. Он довольно широк — это строительство и ремонт лодок, яхт, изготовление велотранспорта, бамперов, обвесов, крыльев, корпусов, матриц, бензобаков и др. ёмкостей, дверных карт, торпедо, корпусов для сабов, металлодетекторов, микарты, в авиастроении и авиамоделировании, бижутерия, наливные покрытия, а также ремонт акриловых ванн, поддонов, затирка швов, заливка катушек, микросхем и многое другое!
Эпоксидная смола для объемных заливок «Hi Tech Epoxy»
Полимерная смола «Hi Tech Epoxy» — это новый, современный и универсальный компонент, с улучшенными характеристиками, отвечающим широким спектром задач, при производстве материалов и конечных продуктов.
Рабочий диапазон данной смолы при заливке или нанесении, от 1 до 100 мм в практически неограниченном объёме
«Hi Tech Epoxy» используется для:
- Заливки в древесину (Слэбы)
- Отливок ночников (ламп)
- Отливок декоративной бижутерии
- Покрытия бетона, древесины
- Пропитки стеклотканей и углетканей и т.п.
Характеристики:
- 100 % прозрачная
- 100 % устойчива к Ультрафиолету
- 100 % без остатка пузырьков в массе
- Время жизни (желатинизации) : 5 часов
- Время полного отвердения: до 76 часов
- Соотношение компонентов А/Б: 100/35 грамм
- Твердость по ШОР: 77-78
- Хранить в прохладном месте, плотно закрытой таре, избегать попадание прямых солнечных лучей.
Стоит отметить, что некоторые характеристики любых эпоксидных смол можно изменять, добавляя те или иные компоненты. Алюминиевая пудра или антипирен, например, увеличивают термостойкость, аэросил — тиксотропность, активные разбавители — прочность на разрыв, удар, изгиб, в большом количестве увеличивают эластичность. Существует масса отвердителей для эпоксидных смол с ускоренным или замедленным временем полимеризации, а также отвердители, работающие при температуре -5°С и даже под водой!
Применение эпоксидных смол
Мы на этом рынке вот уже несколько лет и за это время сформировали свой (точнее ВАШ) список применения эпоксидных смол. Он довольно широк — это строительство и ремонт лодок, яхт, изготовление велотранспорта, бамперов, обвесов, крыльев, корпусов, матриц, бензобаков и др. ёмкостей, дверных карт, торпедо, корпусов для сабов, металлодетекторов, микарты, в авиастроении и авиамоделировании, бижутерия, наливные покрытия, а также ремонт акриловых ванн, поддонов, затирка швов, заливка катушек, микросхем и многое другое!
Свойства и применение эпоксидных смол
Эпоксидная смола — это химическое соединение, которое после добавления отвердителя превращается в очень прочный полимер (подробнее о химии смол).
Свойства эпоксидной смолы зависят от марки смолы, отвердителя, условий отверждения и т.д. Здесь мы приводим основные свойства эпоксидных смол, характерные для большинства из них:
— Высокая прочность. Именно это свойство обеспечивает стабильный спрос на эпоксидные смолы в течение многих лет. Прочность застывшей смеси на растяжение и на сжатие сопоставима с прочностью типовых марок тяжелого бетона (варьирует в пределах 40-90 МПа).
— Отличные клеящие свойства: эпоксидные смолы обладают прекрасными адгезивными свойствами, что в сочетании с прочностью делает их превосходным клеем.
— Хорошие водозащитные свойства: отверждённая эпоксидная смола практически водонепроницаема.
— Устойчивость к большому ряду агрессивных химических веществ (подробнее здесь).
— Небольшая масса готовых изделий (см.ниже).
Основные области применения:
— Изготовление композитных соединений (стеклопластик, углепластик). Стеклоткань и углеткань, пропитанная эпоксидной смолой, обладает очень высокой прочностью при небольшом весе. Это делает композиты незаменимыми соединениями, применяемыми в судостроении, авиастроении, ракетоостроении и автомобилестроении.
— Наливные (полимерные) полы, ставшие очень востребованными в последнее время.
— Дизайнерская мебель.
— Электроизоляция. Эпоксидная смола — диэлектрик и способна выдерживать серьёзные электрические нагрузки.
— Гидроизоляция. Это свойство ценится как в судостроении, где смола интенсивно применяется, так и для создания водозащитных покрытий при постройке, например, бассейнов.
— Декоративно-прикладное искусство: из эпоксидных смол изготавливают броши, кулоны, кольца, серьги и другие украшения.
— Ремонтные работы (смола в сочетании со стеклотканью поможет отремонтировать кузов автомобиля или катер, а со стеклолентой — течь в трубе). Всем с детства знаком эпоксидный клей, которым можно починить самые безнадёжные поломки.
— Диорамы, модели, поделки. Незаменима в стендовом моделизме.
— Изготовление прочных пропиток и покрытий для древесины и других материалов.
Работа с эпоксидными смолами несложная (куда проще чем, к примеру, с металлом) и требует лишь небольшой практики (здесь подробнее о том, как работать с эпоксидной смолой). Благодаря этой простоте и широкому спектру применения можно быть уверенным, что в ближайшем будущем количество сфер применения смол и композитов будет только увеличиваться.
Назад в справочник
В раздел «Эпоксидные смолы»
В раздел «Руководства»
Эпоксидная смола ЭД-20: характеристики
На чтение 6 мин. Опубликовано
Эпоксидные смолы представляют собой олигомерный, универсальный материал. Эпоксидка получила широкое одобрение и активно используется в самых разных сферах промышленности. Благодаря хорошим техническим показателям и безопасности такое вещество применимо и в быту. Из богатой линейки данных композитов отдельное место занимает эпоксидная смола ЭД-20, характеристики которой подтверждают неординарность такого материала.
Области применения эпоксидки ЭД-20
Эпоксидка ЭД-20 или эпоксидно-диановая смола – это тягучая и вязкая субстанция коричневого окраса без дополнительных включений. Этот продукт создается на базе эпихлоргидрина и дифенилолпропана. ЭД-20 отлично комбинируется с различными катализаторами-отвердителями, иногда требуется и дополнительное присутствие пластификаторов (для уменьшения показателей жесткости готовой продукции).
Число «20» в название вещества обозначает долю присутствия эпоксидных составляющих, которая равняется 20%.

ЭД-20 славится широкими возможностями и используется в многочисленных областях промышленности. Она применяется для:
- ремонтных работ радио, электроники, ПК, корпусных деталей парусников, катеров, лодок;
- производства различной мебели;
- создания оригинальных украшений, столешниц, различных сувениров;
- машиностроения и приборостроения;
- авиационной промышленности и строительства;
- монтажа наливных половых и настенных покрытий.
Уникальный состав эпоксидки-20 позволяет включать ее в различные заливочные смеси, грунтовки, эмалей и лакокрасочные материалы. На основе субстанции изготавливают стекловолокно, стеклопластик и армированный пластик.
Основные технические параметры
В среднем время полного застывания массы составляет сутки. Плотность эпоксидки варьируется и зависит от варианта отвердевания:
- холодное: 1110-1230 кг/м3;
- горячее: 1200-1270 кг/м3.
Для размягчения смолы ее следует подвергнуть нагреванию до +60⁰С. Основные технические параметры данного материала таковы:
- высокая вязкость и жесткость;
- беспористость итоговой массы;
- отсутствие усадки и маленький удельный вес;
- повышенная устойчивость к повреждениям, истираниям и влаге;
- отличные антикоррозийные, диэлектрические и термостойкие показатели;
- хорошие показатели адгезии с практически любой поверхностью: керамика, металл, плитка, дерево, стекловолокно, стекло, пластик, углеволокно и пр.
ЭД-20: инструкция по применению
К каждой упаковке продукта прилагается инструкция по применению эпоксидной смолы ЭД-20, которую необходимо внимательно изучить. Эпоксидка начинает процесс полимеризации только после соединения ее с катализатором-отвердителем. Причем на итоговый результат станут влиять такие факторы, как:
- пропорции составляющих;
- условия окружающей среды;
- используемая тара.
Знайте, что не все производители точно указывают в аннотации, как замешивать отвердитель со смолой, чаще кратко пишется допустимое соотношение прилагаемых компонентов и условия для полимеризации. Поэтому рекомендуется самим методом пробы установить оптимальное соотношение отвердителям и основной массы (в классическом варианте на 10 частей смолистого вещества берется 1 часть катализатора).

Предварительная подготовка
При выполнении отвердения ЭД-20 холодным методом предварительная подготовка не нужна. А вот для горячего метода масса прогревается. Нагреть эпоксидку можно на водяной бане, но следите, чтобы при нагревании ни одна капля влаги не попала на смолу, иначе она испортится. Нельзя допускать и перегрев субстанции – кипение приводит эпоксидку в негодность.
Совет. Оптимальный температурный режим прогрева эпоксидки ЭД-20 составляет до +55⁰С.
При долгом хранении смолистого вещества оно затвердевает и кристаллизуется. Для последующего использования массу подогревают при температурном режиме в +40⁰С. Можно просто опустить емкость со смолой в горячую воду. При разогревании смолу следует регулярно перемешивать.
Применение пластификатора
Иногда к эпоксидной смоле добавляется пластификатор. Это вещество необходимо для повышения упругости изделий, обрабатываемых эпоксидкой. Например, если необходимо, чтобы изделие было устойчиво к ударным и механическим нагрузкам. Также пластификаторы применяют для повышения эластичности (гибкости) швов. Чаще применяют следующие типы пластификаторов:
- Дибутилфталат (или ДБФ). Наиболее распространенный пластификатор. Он помогает приобретать изделию высокую стойкость к сильным холодам и ударам. Субстанцию вмешивают в эпоксидку не более 2–5% от объема смолы.
- Диэтиленгликоль (или ДЭГ-1). Рабочая концентрация субстанции укладывается в 3–10%, причем, чем больше оказывается пластификатора в смолке, тем сильнее эпоксидка начинает походить на резину. При применении ДЭГ-1 учитывайте, что масса обладает ярко-оранжевым окрасом и окрашивает смолу.
Применение отвердителя
Отвердитель – необходимое вещество для включения процесса полимеризации эпоксидки. При сочетании его с пластификатором добавляется в смолу вторым. В классическом варианте отвердитель добавляется в эпоксидку в соотношении 1х10. Это вещество добавляют в смолу аккуратно и постепенно, иначе можно спровоцировать процесс стремительного нагревания и закипания смолы, что портит ее. Чаще всего используют катализаторы-отвердители марки ПЭПА, ТЭТА, ДЭТА и ЭТАЛ-45.
При использовании ЭТАЛ-45 дополнительное применение пластификатора уже не нужно, этот отвердитель обладает всеми необходимыми качествами.
От чего зависят показатели склеивания
После добавления катализатора-отвердителя смолу необходимо сразу использовать. От этого зависят заявленные показатели адгезии и качества склеивания. У эпоксидки разных марок и качества этот период различен. В среднем он равен от получаса до часа. А при добавлении ЭТАЛ-45 этот период возрастает до 2–3 часов. Полная полимеризация эпоксидки составляет 1–3 суток.

Правила хранения, перевозки и безопасности при работе с ЭД-20
Смолу ЭД-20 упаковывают в специальные барабаны (емкости по 50-220 кг). Встречается и фасовка по пластиковым контейнерам от 500 г. Средство можно транспортировать в закрытом виде, а хранить в условиях температурного режима в +15–40⁰С. Не следует допускать попадания на смолу открытых солнечных лучей и хранить ее вдали от окислителей и различных кислот. При работе с эпоксидкой обязательно используют средства защиты: перчатки, очки и маску.
Аналоги эпоксидной смолы этой марки
В качестве идентичных по показателям эпоксидных смол выступают несколько марок. Более подробно они описаны в таблице:
Марка аналога | Область применения | Отличия от ЭД-20 |
ЭД-8 | машиностроение, авиационная и судостроительная промышленность, создание лаков и красок, ремонт оргтехники, строительство | пониженное содержание эпоксидной группы (8%) и периода желатинизации (около 3 часов) |
ЭД-16 | массовая доля эпоксидных включений 16%, более низкая вязкость, повышенное содержание хлора | |
ЭД-22 | высокое время желатинизации (порядка 18 часов), показатели вязкости8-12 ПА/секунду | |
Э-40 | изготовление лаков, шпаклевок и грунтовок с повышенными защитными показателями | более высокая влагостойкость и пластичность |
Выводы
Эпоксидно-диановая смола – превосходный и востребованный материал, активно используемый в различных областях современной промышленности. С ее помощью создают композиты, многочисленные составы, отличающиеся высокими показателями надежности и прочности, заливаются поверхности. ЭД-20 отличается от ряда своих аналогов отличными техническими показателями и доступной стоимостью.
Эпоксидная химия— Понимание эпоксидной смолы морского класса
WEST SYSTEM
По мере отверждения смешанная эпоксидная смола проходит через жидкое состояние, через гелеобразное состояние, в твердое состояние.
Понимание химии эпоксидной смолы важно для безопасного и эффективного использования эпоксидной смолы. Смешивание эпоксидной смолы и отвердителя начинает химическую реакцию, которая превращает объединенные жидкие ингредиенты в твердое вещество. Время, необходимое для этого химического превращения из жидкого в твердое, называется , время отверждения .По мере отверждения эпоксидная смола проходит из жидкого состояния через гелеобразное состояние, прежде чем она достигает твердого состояния.
По мере отверждения смешанная эпоксидная смола переходит из жидкого состояния через гелеобразное состояние в твердое состояние.
Эпоксидная химия и стадии отверждения
Стадия 1: Жидкость — эпоксидная смола
Открытое время (также рабочее время или время влажной укладки) — это часть времени отверждения, после смешивания смолы и отвердителя, чтобы вызвать химическую реакцию эпоксидной смолы, что смесь остается жидкой и пригодной для обработки и пригодной для применения.Вся сборка и зажим должны выполняться в течение открытого времени, чтобы обеспечить надежное соединение.
Стадия 2: гель — начальное эпоксидное отверждение
Эпоксидная смесь переходит в начальную фазу отверждения (также называемую «зеленой стадией» в химии эпоксидных смол), когда она начинает превращаться в гель или «начинать». Эпоксидная смола больше не пригодна для работы и будет переходить от липкой гелевой консистенции к твердости твердой резины, которую вы будете втирать с помощью миниатюры.
Поскольку эпоксидная смесь отверждается только частично, новое нанесение эпоксидной смолы все еще будет химически связываться с ней, поэтому поверхность все еще можно будет связывать или перекрывать без специальной подготовки.Однако эта способность уменьшается, когда смесь приближается к своему окончательному отверждению.
Стадия 2: Твердое — окончательное отверждение эпоксидной смолы
Химическая реакция эпоксидной смолы завершена. Смесь затвердела до твердого состояния и может быть отшлифована и отформована сухим способом. Вы не должны быть в состоянии вмятины с вашим эскизом. На данный момент в эпоксидной химии, продукт достиг примерно 90% от его предельной прочности, поэтому зажимы можно снять. Он будет продолжать отверждаться в течение следующих нескольких дней при комнатной температуре.
Новое нанесение эпоксидной смолы больше не будет химически связываться с ним, поэтому поверхность эпоксидной смолы должна быть надлежащим образом подготовлена и отшлифована перед повторным нанесением покрытия для достижения хорошей механической вторичной связи. См. Подготовка поверхности.
Вы можете улучшить тепловые характеристики эпоксидной смолы и уменьшить вероятность «сквозного» отпечатка ткани, применяя умеренное тепло к эпоксидной смоле после ее отверждения до твердого состояния. Свяжитесь с нашим техническим персоналом для получения дополнительной информации о постотверждении.
Понимание времени отверждения эпоксидной смолы
Открытое время и время отверждения определяют основную часть деятельности по строительству и ремонту с использованием эпоксидной смолы. Открытое время диктует время, доступное для смешивания, нанесения, сглаживания, формирования, сборки и зажима. Время отверждения определяет, как долго вы должны ждать, прежде чем снимать зажимы, или прежде чем вы сможете шлифовать или перейти к следующему этапу проекта. Два фактора определяют время раскрытия эпоксидной смеси и общее время отверждения: скорость отверждения отвердителя и температуру эпоксидной смолы.
Эпоксидный отвердитель Speed
Каждый эпоксидный отвердитель имеет идеальный диапазон температур отверждения. При любой данной температуре каждая комбинация смолы / отвердителя будет проходить одни и те же стадии отверждения, но с разными скоростями. Выберите отвердитель, который дает вам достаточно рабочего времени для работы, которую вы выполняете при температуре и условиях, в которых вы работаете. Руководство по продукту и этикетки на контейнерах описывают срок годности и время отверждения отвердителя
Жизнеспособность — это термин, используемый для сравнения скоростей отверждения эпоксидной смолы различных отвердителей.Это количество времени, в течение которого удельная масса смешанной смолы и отвердителя остается жидкой при определенной температуре. (Смесь массой 100 г в стандартном контейнере при температуре 72 ° F). Поскольку жизнеспособность является мерой скорости отверждения определенной содержащейся массы (объема) эпоксидной смолы, а не тонкой пленки, жизнеспособность отвердителя намного короче, чем его время раскрытия.
температура эпоксидной смолы
Чем выше температура отверждения эпоксидной смолы, тем быстрее она отверждается (рис. 1). Тепло ускоряет эпоксидную химию или химическую реакцию эпоксидных компонентов.Температура отверждения эпоксидной смолы определяется температурой окружающей среды плюс экзотермическое тепло, выделяемое при его отверждении.
Температура окружающей среды — это температура воздуха или материала, контактирующего с эпоксидной смолой. Температура воздуха чаще всего является температурой окружающей среды, если эпоксидная смола не нанесена на поверхность с другой температурой. Обычно эпоксидная смола затвердевает быстрее, когда температура воздуха выше.
Экзотермическое тепло вырабатывается в результате химической реакции, которая приводит к отверждению эпоксидной смолы. Количество выделяемого тепла зависит от толщины или открытой поверхности смешанной эпоксидной смолы.В более толстой массе больше тепла сохраняется, вызывая более быструю реакцию и больше тепла. Форма емкости для смешивания и количество смеси оказывают большое влияние на эту экзотермическую реакцию. Содержащаяся масса отверждающейся эпоксидной смолы (8 жидких унций или более) в пластиковой чашке для смешивания может быстро генерировать достаточно тепла, чтобы растопить чашу и обжечь вашу кожу. Однако, если такое же количество распространяется в тонком слое, экзотермическое тепло рассеивается, а время отверждения эпоксидной смолы определяется температурой окружающей среды. Чем тоньше слой отверждающейся эпоксидной смолы, тем меньше на него воздействует экзотермическое тепло, и тем медленнее он затвердевает.
Контроль времени отверждения эпоксидной смолы
В теплых условиях, по возможности, используйте более медленный эпоксидный отвердитель. Смешайте небольшие порции, которые можно быстро израсходовать, или вылейте эпоксидную смесь в емкость с большей площадью поверхности (например, с роликовым поддоном), позволяя экзотермическому теплу рассеиваться и увеличивая время открытия. Чем раньше смесь будет перенесена или нанесена (после тщательного перемешивания), тем больше полезного времени открытия смеси будет доступно для нанесения покрытия, укладки или сборки.
В прохладных условиях используйте более быстрый отвердитель или дополнительное тепло, чтобы поднять температуру эпоксидной смолы выше минимальной рекомендуемой температуры применения отвердителя. Используйте пистолет с горячим воздухом, нагревательную лампу или другие источники тепла, чтобы нагреть смолу и отвердитель перед смешиванием или после нанесения эпоксидной смолы. При комнатной температуре дополнительное тепло полезно, когда требуется более быстрое отверждение.
Внимание! Эпоксидная смола генерирует тепло. Не заполняйте пустоты или отливки эпоксидного слоя толщиной более ½ дюйма — разбавителя, если он покрыт пеной или другим изоляционным материалом.Несколько дюймов смешанной эпоксидной смолы в замкнутой массе (такой как стакан для смешивания) будут генерировать достаточно тепла, чтобы расплавить пластиковый стакан, обжечь вашу кожу или воспламенить горючие материалы, если оставить их на весь срок годности. По этой причине не используйте пенопластовые или стеклянные емкости для смешивания и не разливайте в замкнутые пространства. Если кастрюля со смешанной эпоксидной смолой начинает экзотермироваться (нагреваться), быстро переместите ее на улицу. Избегайте вдыхания паров. Не выбрасывайте смесь, пока реакция не завершится и не остынет.
Для получения подробной информации о работе с эпоксидной смолой при низких температурах, обратитесь к разделу Холодное соединение.
Дегазация
ВНИМАНИЕ! Нагревательная эпоксидная смола, которая не загущена, снизит ее вязкость, позволяя эпоксидной смоле легче прогибаться или провисать на вертикальных поверхностях. Кроме того, нагревание эпоксидной смолы, нанесенной на пористую подложку (мягкая древесина или материал сердцевины с низкой плотностью), может привести к выходу газа из подложки и образованию пузырьков в эпоксидном покрытии. Чтобы избежать выделения газов, подождите, пока эпоксидное покрытие не загустеет, прежде чем нагревать его. Никогда не нагревайте смешанную эпоксидную смолу в жидком состоянии при температуре выше 120 ° F (49 ° C).
Независимо от того, какие шаги предпринимаются для контроля времени отверждения, базовое понимание химии эпоксидной смолы и тщательное планирование нанесения и сборки позволит вам максимально использовать время раскрытия эпоксидной смолы и время отверждения.
Для вопросов и ответов химика по эпоксидной химии, прочитайте Спросите Химика на Epoxywork.com.
,прозрачная эпоксидная смола
Вода Прозрачная Эпоксидная Литьевая Смола
Продукт № 214
Настольная смола Описание
Продукт № 214 Water Clear Epoxy Casting — Настольная смола — Bar Bar Resin — универсальная, с низкой вязкостью система эпоксидной смолы для покрытия дерево и бетонные столешницы, столешницы, барные стойки и аналогичные приложения.
Продукт № 214 Water Clear Casting-Tabletop-Epoxy Bar Top Смола обычно используется в качестве прозрачного самовыравнивающегося напольного материала объемом л, где требуется очень ровный и ровный пол поверх бетона и дерева. Продукт # 214 Эластичная эпоксидная смола для столешниц-эпоксидных смол широко используется для ультраплоского выравнивания поверхностей под оборудование , где очень прочная сверхплоская опорная поверхность является обязательной. Он также успешно используется для ультраплоских полов для сцены, танцпола и чистые комнаты.
Продукт № 214 Прозрачная литьевая столешница Смола используется в качестве прозрачной клейкой матрицы для стекла специального цвета и цветного Напольные покрытия и плитка.Продукт # 214 Прозрачная литьевая прозрачная смола — Смола Clear Bar Top Resin образует глянцевую твердую поверхность, которая устойчив к пятнам. Он также широко используется в качестве чистой воды литейная смола .
Продукт № 214 Clear Casting — Прозрачная столешница — Ясная верхняя часть Смола обладает отличной прозрачностью и сохранением цвета. Продукт № 214 Очистить Смола для литья столешниц из смолы и столешницы из смолы имеет ноль (0) VOC , что делает его по существу без запаха и, следовательно, может использоваться в помещениях с большим количеством людей.
Преимущества прозрачной настольной смолы № 214
- Слабый запах для использования в населенных пунктах
- Низкая вязкость — хорошие смачивающие свойства
- Соответствует стандартам USDA для использования в пищевой промышленности
- Глянцевая отделка
- пятен
- Ноль (0) ЛОС — отсутствие летучих органических соединений означает, что он соответствует самым жестким низким ЛОС стандарты.
При использовании прозрачной настольной смолы
- Минимальная температура нанесения Продукт № 214 Прозрачная эпоксидная смола Смола Casting-Tabletop-Bar Top составляет 50 ° F.
- Подложка для получения Продукт № 214 Water Clear Resin не должен содержать отвердителей и посторонних материалов.
Подготовка поверхности эпоксидной смолы для столешницы
Подготовка поверхностиявляется наиболее важной частью любой успешной эпоксидной смолы применение.Все субстраты для получения Продукт # 214 Смола Water Clear Casting-Tabletop-Bar Top должна быть должным образом очищена и подготовлена. подложка не должно быть масла, краски, герметика, герметика и других загрязнений, будет мешать склеиванию этого материала. Посмотри пожалуйста Подготовка поверхности. Связаться с нами Больше подробностей.
Инструкция по смешиванию прозрачной смолы № 214
Размешайте каждый компонент отдельно. Объединить 2 части A в одну часть B по объему в чистый контейнер.Перемешать в течение трех минут, перемешивая веслом, соскребая дно и бока Контейнер часто. Не добавляйте разбавители.
СВОЙСТВА ПРИМЕНЕНИЯ @ 77 ° F | ||
Соотношение смешивания | 2: 1 по объему | |
Вязкость (смешанная) | 950 сПз | |
Жизнеспособность (200 гр.) | 30-40 минут при 70 ° F | |
VOC | 0 | |
Время отверждения (грунтовка) | 10-14 часов | |
Окончательное лечение @ 74 градуса F. | 5 дней | |
Цвет | Очистить | |
Размер упаковки | 3 галлона единиц | |
Производительность | ||
ASTM D-638 | 8500 фунтов на квадратный дюйм | |
Удлинение ASTM D-638 | 5,5% | |
Адгезия к металлу | 2500 фунтов на квадратный дюйм | |
Адгезия к бетону ACI Комитет 403 | 350 фунтов на квадратный дюйм (Бетон не выдерживает) | |
Твердость ASTM D-2240 | 80 (Shore D) | |
Сопротивление истиранию ASTM С-501 | потеря 35-40 мг (Колесо CS-17, нагрузка 1 кг, 1000 циклов) | |
Рабочая температура MIL-D-3134F | 160 F
(Погружение) 185 F (сухой жар) | |
Ударопрочность MTI-D-3134F§ 4.7.3 | Выдерживает
16 футов / фунт без трещин, расслаивание или сколы. | |
Отступ MIL-D-3134F § 4.7.4 | Выдерживает 2000
lbs./sq. в течение 30 минут без отступа | |
Повышенная температура
Сопротивление MIL-D-3134F § 4.7.5 | Нет скольжения или потока
при требуемой температуре в 158 F. | |
Водопоглощение ASTM
D-570-63 (24 часа погружения) | 0.10% максимум | |
Прочность на изгиб ASTM D-790 | 8000 фунтов на квадратный дюйм | |
Прочность на сжатие ASTM D-695 | 11000 фунтов на квадратный дюйм |
Применение столешницы / эпоксидной смолы для столешницы
Нанесение Продукт № 214 Water Clear Resin зависит от способа нанесения. Будьте осторожны, чтобы не включать пузырьки в покрытие. Типичные наливы имеют толщину от 1/16 до 1/2 дюйма в Пальто.Если желателен второй слой, удалите всю пыль, если через 24 часа после последнего слоя слегка отшлифовать, а затем нанести второй слой.
Меры предосторожности при использовании эпоксидной смолы
Хранить в недоступном для детей месте. Обратитесь к материалу безопасности Паспорта (формы MSDS), относящиеся к данному продукту, перед его использованием. Избежать контакта с кожей или глазами. Длительное или повторное воздействие может привести к поражению глаз и кожи раздражение. При попадании на кожу немедленно промыть водой с мылом.Если происходит контакт с глазами, промывайте глаза чистой водой и при необходимости медицинская помощь. Используйте защитные очки с боковыми щитками и носите защитную резину перчатки.
Очистка эпоксидной столешницы — барная смола
Удалить Продукт № 214 Water Clear Resin со всех инструментов и оборудования до гелирования системы. Используйте MEK, Ацетон или любой лаковый растворитель.
Химическая стойкость смолы № 214 Top Bar
Уксусная кислота 5% | л | молочной кислоты — 15% | R |
Ацетон | л | Метилэтилкетон | л |
Метилэтилкетон | л | Азотная кислота 10% | R |
Отбеливатель | л | Гидроксид натрия 50% | R |
лимонная кислота 30% | R | Skydrol | R |
Сырая нефть и Дизельное топливо | R | Серная кислота 20% | R |
Этиленгликоль | R | Толуол | R |
жирных кислот | л | Мочевина | R |
Бензин | R | Уксус | л |
соляная кислота 15% | R | ксилол | R |
R = Рекомендуется для непрерывной работы L = Ограниченная рекомендация, иногда разливы.
Покрытие: 231 кубических дюймов на галлон. В 1/8 дюйма толщиной 12,8 SF за галлон.
Используйте Топ калькулятор смолы, чтобы проверить ваш оценить.
Дополнительная информация
Информация об использовании настольной смолы в Река Симуляция.
,Этот инструмент для решения проблем эпоксидной смолы и FAQ предназначен для выявления и предотвращения потенциальных проблем, связанных с использованием эпоксидной смолы WEST SYSTEM®. Если вы не нашли решения своей проблемы с эпоксидной смолой в этом удобном руководстве по решению проблем с эпоксидной смолой, пожалуйста, свяжитесь с нашим техническим персоналом.
Отверждение
Эпоксидная смесь не затвердела по истечении рекомендованного времени отверждения
ВОЗМОЖНЫЕ ПРИЧИНЫ И РЕШЕНИЯ
Отношение: слишком много или слишком мало отвердителя повлияет на время отверждения и тщательность отверждения.
- Удалить эпоксидную смолу. Не наносите дополнительный материал поверх неотверждаемой эпоксидной смолы. См. Очистка и удаление.
- Убедитесь, что вы используете правильное количество ходов насоса: используйте равные ходы эпоксидной смолы и отвердителя. НЕ добавляйте дополнительный отвердитель для более быстрого отверждения эпоксидной смолы!
- Проверьте правильность насоса (соотношение 5: 1 или 3: 1) и размер группы насосов (эпоксидная смола группы B и эпоксидный отвердитель группы B).
- Проверьте соотношение эпоксидного насоса (см. 300 Инструкции по мини-насосу). См. Дозирование и смешивание.
Низкая температура: эпоксидные смеси отвердевают медленнее при низких температурах.
- Дайте эпоксидной смоле дополнительное время отверждения в прохладную погоду.
- Подайте тепло для поддержания химической реакции эпоксидной смолы и ускорения отверждения.
- Используйте 205 Fast Hardener, разработанный для отверждения эпоксидной смолой при более низких температурах.
- См. Склеивание при низких температурах.
Недостаточное перемешивание.
- Удалить эпоксидную смолу. Не наносите дополнительный материал поверх неотверждаемой эпоксидной смолы.См. Очистка и удаление.
- Тщательно смешайте эпоксидную смолу и отвердитель, чтобы избежать областей, богатых смолой и отвердителем. См. Дозирование и смешивание.
- Добавляйте только наполнители или добавки только после того, как эпоксидная смола и отвердитель были тщательно перемешаны.
Неверные продукты.
- Удалить эпоксидную смолу. Не наносите дополнительный материал поверх неотверждаемой эпоксидной смолы. См. Очистка и удаление.
- Проверьте совместимость эпоксидной смолы и отвердителя.Эпоксидная смола не будет отверждаться должным образом с эпоксидным отвердителем других марок или с полиэфирными катализаторами.
Склеивание
Эпоксидная связь отказ
ВОЗМОЖНЫЕ ПРИЧИНЫ И РЕШЕНИЯ
Недостаточное отверждение.
См. Выше.
Смоляное голодное соединение: эпоксидная смола впиталась в пористые поверхности, оставляя пустоту в суставе.
Смочить склеиваемые поверхности аккуратной эпоксидной смесью от до с применением загущенной эпоксидной смолы.Смачивайте очень пористые поверхности и концы зерна. См. Склеивание и закрепление.
Загрязненная эпоксидная связующая поверхность.
Очистите и отшлифуйте поверхность, следуя процедуре подготовки поверхности. Зашлифовать деревянные поверхности после строгания или соединения.
Область склеивания слишком мала для нагрузки на соединение.
Увеличьте площадь склеивания, добавив эпоксидные филе, скрепленные скобы или шарфовые соединения. См. Склеивание и Зажим.
Слишком сильное давление прижимной эпоксидной смолы из соединения.
Используйте достаточное зажимное давление, чтобы выдавить небольшое количество эпоксидной смолы из соединения. См. Склеивание и Зажим.
Покрытие
Прозрачное эпоксидное покрытие стало мутным
ВОЗМОЖНЫЕ ПРИЧИНЫ И РЕШЕНИЯ
Влага от конденсата или очень влажных условий вступает в реакцию с компонентами в неотвержденном эпоксидном отвердителе.
- Нанесите умеренное тепло на частично отвержденное эпоксидное покрытие для удаления влаги и полного отверждения.Смотрите Out-Gassing Осторожно в эпоксидной химии.
- Используйте специальный прозрачный отвердитель 207 для нанесения прозрачных покрытий и для склеивания тонких виниров, где эпоксидная смола может вытекать на поверхность.
Захваченный воздух в эпоксидной смоле от агрессивного нанесения валика.
- Наносить эпоксидное покрытие при более высокой температуре — эпоксидная смола при более высоких температурах.
- Нанести эпоксидную смолу тонкими слоями.
- Подайте умеренное тепло, чтобы освободить захваченный воздух от эпоксидной смолы и полностью отвердеть.Смотрите Out-Gassing Осторожно в эпоксидной химии.
Blush — решение проблем с эпоксидной смолой
Восковая пленка появляется на поверхности отвержденной эпоксидной смолы
ВОЗМОЖНЫЕ ПРИЧИНЫ И РЕШЕНИЯ
Аминные румяна образуются в результате процесса отверждения эпоксидной смолы.
- Румяна растворим в воде. Удалить с водой. См. Специальную подготовку — отвержденная эпоксидная смола при подготовке поверхности.
- Используйте 207 Специальный прозрачный отвердитель.207 краснеет.
Изменение цвета
Отвердитель покраснел после нескольких лет хранения
ВОЗМОЖНЫЕ ПРИЧИНЫ И РЕШЕНИЯ
Влага в контакте с отвердителем и его металлическим контейнером.
Красный (или коричневый или фиолетовый) цвет является нормальным состоянием. Это не повлияет на обработку эпоксидной смолы или прочность отверждения. Избегайте использования для прозрачного покрытия или открытых областей, где цвет не желателен.
Application — Решение проблем с эпоксидными смолами
Пробежки или провалы в эпоксидном покрытии
ВОЗМОЖНЫЕ ПРИЧИНЫ И РЕШЕНИЯ
Эпоксидная смола нанесена слишком густой.
- Используйте 800 валиков и раскатайте эпоксидное покрытие в более тонкую пленку. Тонкая пленка будет вытекать намного более гладкой, чем более толстая, после того, как она будет очищена щеткой с пенным валиком.
- Нагреть эпоксидную смолу, чтобы разбавить ее или нанести покрытие при более высокой температуре. См. Склеивание при низких температурах.
См. Барьерное покрытие.
Эпоксидное покрытие отверждается слишком медленно.
- Нанести эпоксидное покрытие при более высокой температуре.
- Нагрейте эпоксидную смолу и отвердитель перед смешиванием, чтобы ускорить отверждение в прохладную погоду.
- Переключитесь на более быстрый отвердитель, такой как 205 Fast Hardener, если это возможно.
См. Контроль времени отверждения по эпоксидной химии.
Шлифование
Облицовочный состав (эпоксидная смола / смесь 407 с низкой плотностью или 410 микролайт) провисает и трудно шлифуется
ВОЗМОЖНЫЕ ПРИЧИНЫ И РЕШЕНИЯ
Материал обтекателя недостаточно толстый.
- Добавить больше наполнителя в эпоксидную смесь, пока она не достигнет консистенции «арахисового масла»; чем больше наполнителя добавлено, тем жестче и легче будет шлифоваться.
- Перед нанесением обтекателя на вертикальные поверхности дайте смочить эпоксидную смолу в геле.
См. Обтекатель.
Живопись / Лакировка
Краска или лак не будут наноситься поверх эпоксидной смолы
ВОЗМОЖНЫЕ ПРИЧИНЫ И РЕШЕНИЯ
Эпоксидная смола не полностью отверждена.
Дайте окончательному эпоксидному покрытию полностью отвердеть. Разрешить несколько дней при необходимости для медленных отвердителей при более низких температурах. Примените умеренную высокую температуру, чтобы закончить лечение при необходимости. См. Контроль времени отверждения в разделе Эпоксидная химия.
Краска несовместима с эпоксидной смолой.
- Используйте другой тип краски. Некоторые краски и лаки могут быть несовместимы с некоторыми отвердителями. Если вы не уверены, проверьте совместимость на кусочке материала с покрытием.
- Используйте 207 отвердителя. Совместим с большинством лакокрасочных материалов.
Эпоксидная поверхность не полностью подготовлена.
Удалите все аминные румяна и тщательно отшлифуйте эпоксидную поверхность перед нанесением красок или лаков. См. Окончательная подготовка поверхности.
Перегрев — Решение проблем с эпоксидной смолой
Эпоксидная смола стала очень горячей и слишком быстро застыла.
ВОЗМОЖНЫЕ ПРИЧИНЫ И РЕШЕНИЯ
Слишком большая партия.
- Смешайте меньшие партии эпоксидной смолы.
- Перенесите эпоксидную смесь в емкость с большей площадью поверхности сразу после смешивания.
См. Понимание времени отверждения в разделе «Химия эпоксидных смол», «Дозирование и смешивание».
Температура слишком высокая для отвердителя.
Используйте очень медленный отвердитель 206 или дополнительный медленный отвердитель 209 с 1-5 эпоксидной смолой в очень теплую погоду.
Эпоксидное покрытие слишком густое.
Нанесите толстые участки заливки несколькими тонкими слоями эпоксидной смолы.
пузыри
Пузыри, образованные эпоксидным покрытием на пористом материале (голое дерево или пена)
ВОЗМОЖНЫЕ ПРИЧИНЫ И РЕШЕНИЯ
Воздух, задержанный в эпоксидной смоле, выходит через покрытие (выделяется газ) при повышении температуры материала.
- Покройте древесину эпоксидной смолой, когда температура падает — после нагревания дерева с нагревателями или в более позднюю часть дня.
- Нанесите более тонкое эпоксидное покрытие, чтобы воздух легче выходил.
- Соскайте эпоксидное покрытие с помощью щетки с валиком, чтобы разбить пузырьки. Смотрите Барьерное покрытие.
См. Предупреждение о выделении газа в эпоксидной химии.
Узнайте больше о покрытии без пузырьков на Epoxyworks.com.
Пинхолс
Отверстия появляются в эпоксидном покрытии поверх истертого стекловолокна или эпоксидной смолы
ВОЗМОЖНЫЕ ПРИЧИНЫ И РЕШЕНИЯ
Поверхностное натяжение приводит к тому, что эпоксидная пленка отрывается от отверстия до того, как она станет гелеобразной.
После нанесения эпоксидной смолы с крышкой ролика 800, вытолкните эпоксидную смолу в отверстия с помощью жесткого пластикового распределителя, удерживаемого под низким или почти плоским углом. Повторно покрыть и отогнать покрытие после того, как все отверстия будут заполнены.
Рыбий глаз
Рыбий глаз в покрытии
ВОЗМОЖНЫЕ ПРИЧИНЫ И РЕШЕНИЯ
Загрязнение покрытия или поверхности или неправильное истирание покрытия.
- Убедитесь, что эпоксидное смесительное оборудование чистое.Избегайте вощеных контейнеров для смешивания.
- Убедитесь, что поверхность должным образом подготовлена. Для покрытия используйте подходящую наждачную бумагу, например, 80-эпоксидную. См. Инструкции производителя краски или лака для правильной подготовки поверхности. После подготовки поверхности избегайте загрязнения — отпечатки пальцев, выхлопные газы, ветошь с кондиционером для белья (силикон). Пальто в течение нескольких часов после приготовления. После мокрого шлифования промыть воду следует листом, не оставляя бусин (бусинки указывают на загрязнение) Протрите подходящим растворителем и промойте до тех пор, пока промывочная вода не перестанет образовываться.
Если вы не нашли решение своей проблемы в этом решении проблем с эпоксидной смолой, пожалуйста, свяжитесь с нашим техническим персоналом по телефону 866-937-8797 по рабочим дням с 9:00 до 17:00 по восточному стандартному времени или напишите нам.
,Epoxy Рабочая инструкция | Эпоксидная смола
**** ПРЕДОСТЕРЕЖЕНИЕ ХОЛОДНОЙ ПОГОДЫ ****
ИДЕАЛЬНАЯ РАБОЧАЯ ТЕМПЕРАТУРА — 75–80 ГРАДУСОВ.
ПЕРЕД СМЕШИВАНИЕМ УБЕДИТЕСЬ, ЧТО ПРОДУКТ ПРИНИМАЕТСЯ ПО МЕНЬШЕ 75 УРОВНЕЙ.
ТЕМПЕРАТУРЫ НИЖЕ 75 ПРИЗНАЮТ, ЧТО СМЕШИВАНИЕ БУДЕТ ОЧЕНЬ ТРУДНЫМ
, КАК ХОРОШО, КАК ИЗБЕЖАТЬ ПУШЕК ВОЗДУХА, КОТОРЫЕ НЕ МОГУТ УДАЛИТЬ.
Информация о продукте и инструкции
CRYSTAL CLEAR EPOXY — это 100% твердое твердое прозрачное полимерное покрытие, которое обычно можно увидеть на столешницах и столешницах
.Каждый набор содержит бутылку смолы и бутылку отвердителя, которые смешаны в соотношении 1 к 1 по объему.
Этот продукт отверждается до прозрачного, подобного стеклу конца, который противостоит царапинам и не будет искажаться с возрастом. Предметы, покрытые им, станут
на постоянной основе и будут защищены для вашего удовольствия на протяжении всей жизни. Этот продукт противостоит пожелтению и является водостойким. Тем не менее, он не обеспечивает 100% защиту от ультрафиолета. Это следует тщательно рассмотреть перед нанесением
на открытом воздухе, в условиях сильного ультрафиолетового излучения.CRYSTAL CLEAR EPOXY не будет покраснеть или потеть даже в условиях высокой влажности
и.
Этот продукт лучше всего применять в два этапа. Первый этап называется герметизирующим слоем. Герметизирующее покрытие наносится тонким слоем
и используется для герметизации любой пористости на поверхности, которая предотвращает рост пузырьков воздуха в последующих слоях затопления. Как только герметизирующий слой отстаивается в течение не менее 4 часов, наносится заливочный слой. Покровный слой должен быть залит на поверхность
и позволен вытекать и самовыравниваться.Вы можете использовать резиновую швабру или пенопластовую щетку, чтобы помочь
инанести эпоксидную смолу. Обычно для большинства покрытий столов и брусков наносится от одного до трех слоев, однако необходимо подождать
от 4 до 10 часов, прежде чем наносить последующие покрытия.
Что вам нужно:
• Защитные перчатки — эпоксидная смола очень липкая.
• Градуированные стаканчики для смешивания — Точные измерения чрезвычайно важны для достижения оптимальных свойств отверждения.
• Чистые палочки для перемешивания — грязные палочки могут вызвать загрязнение эпоксидной смолы.
• Резиновые швабры — Эти разбрасыватели не оставляют пузырьки воздуха, как это могут делать щетки.
• Щетки — пенные или нейлоновые щетки, которые не теряют щетины
• Растворитель — денатурированный спирт или ацетон для очистки и протирания
• Пропановая горелка, тепловая пушка или сушилка для волос — Используется для подвода тепла или пламени по поверхности неотвержденная эпоксидная смола
для выпуска захваченных пузырьков воздуха
• Капельные салфетки — следует использовать, чтобы избежать разливов на поверхностях пола
Примечания для начинающих:
Этот продукт будет давать профессиональные результаты при правильном применении.Не торопитесь, чтобы рассмотреть некоторые из этих распространенных проблем
, с которыми пользователи могут столкнуться впервые.
1. ОЧЕНЬ ВАЖНО: Чтобы избежать большинства этих распространенных проблем, вы всегда должны выполнить пробный запуск
с продуктом, чтобы убедиться в правильном понимании того, как смешивать и применять.
2. Всегда следите за тем, чтобы ваш контейнер для смешивания был чистым, а ваше измерительное устройство — точным. Этот продукт
требует смешивания в соотношении 1 к 1 по объему. Любые отклонения от этого соотношения приведут к тому, что эпоксидная смола никогда не затвердеет полностью.
3. Тщательное перемешивание является наиболее важной частью этой процедуры. Даже если у вас есть опыт работы с другими типами
исмол, очень легко недооценить количество смешивания, которое требуется для этого продукта. В зависимости от количества
, которое смешивается, может потребоваться от 3 до 7 минут непрерывного перемешивания без взбивания. Во время смешивания продукт
станет мутно-белым, и вы должны продолжать перемешивать, пока все признаки помутнения и белые полосы в смеси
не станут полностью прозрачными.
4. Не взбивайте этот продукт во время смешивания. Подъем палки во время перемешивания может чрезмерно взбить продукт и
добавит огромное количество пузырьков воздуха, которые трудно удалить.
5. Всегда очищайте стороны контейнера для смешивания и придерживайтесь во время процесса смешивания. Если какой-либо несмешанный материал
останется на боковой стороне контейнера и упадет на вашу поверхность во время заливки, это приведет к образованию неотвержденного мокрого или липкого пятна
.
6.При заливке эпоксидной смолы на поверхность, НИКОГДА не царапайте и не чистите стороны или дно емкости, которую вы только что смешали
, чтобы удалить каждую последнюю каплю, потому что независимо от того, насколько тщательно вы смешали,
всегда будет застрявшей не смешанной частью. который может быть смещен и оставит влажное или липкое пятно.
7. Никогда не оставляйте смешанную эпоксидную смолу в вашем ведре без присмотра. Чем дольше эпоксидная смола находится в вашем ведре, тем больше вероятность того, что эпоксидная смола будет генерировать избыточное тепло, начнет курить и затем быстро затвердеть в ведре.
8. Очистка отвержденного покрытия должна выполняться только с помощью мягкого мыла и воды. Использование жестких чистящих средств или кухонных химикатов
может привести к тому, что отделка станет липкой.
Начало работы
Подготовка проекта:
Для достижения наилучших результатов продукт следует использовать в условиях от 72 ° F до 85 ° F. Помещение, в котором вы работаете в
, должно быть чистым, сухим, без пыли и насекомых. , Отстойная пыль может часто вызывать дефекты на поверхности эпоксидной смолы, так как она отверждается.Убедитесь, что поверхность вашего проекта ровная. Если нет, эпоксидная смола будет в самой нижней точке.
Безопасность:
Всегда надевайте перчатки при работе с эпоксидной смолой. Этот продукт нетоксичен и безопасен для использования внутри помещений, потому что
практически не имеет запаха. Продукт может нанести вред коже, поэтому следует всегда надевать средства защиты глаз и кожи.
Подготовка поверхности:
Для большинства применений поверхность дерева на брусе или столе должна быть сначала отшлифована, очищена и очищена от пыли.
также важно, чтобы любые предшествующие пятна или покрытия были полностью сухими перед началом. Любые типы влаги, масел, смазок или неотвержденных покрытий
могут потенциально вызвать рыбий глаз или проблемы с отверждением продукта.
Информация, содержащаяся в этом бюллетене, основана на данных, которые считаются точными, и предназначена для использования лицами, имеющими технические навыки и ноу-хау, на свое усмотрение и риск. Поскольку условия использования находятся вне нашего контроля, мы не можем взять на себя ответственность за полученные результаты или ущерб, причиненный в результате неправильного использования, а также мы не можем взять на себя ответственность клиента.
Использование продукта
1. Охват:
Чтобы определить, сколько нужно смешать, вы должны знать свои квадратные метры (длина х ширина). При работе с большими проектами
инет необходимости смешивать все количество сразу, так как трудно смешать более двух галлонов одновременно.
Смешивание нескольких партий для одного слоя допустимо, когда они разливаются сразу друг за другом. Крупные проекты, как правило, требуют от
доболее одного человека, чтобы облегчить правильное смешивание и заливку в отведенное количество рабочего времени.
Руководство по покрытию герметизирующего покрытия (48 кв. Футов на галлон)
Площадь покрытия общего объема эпоксидной смолы (количества смолы + отвердителя)
_____________________________________________________________________________
1 кв. Фут. Всего 3 унции (1½ унции смолы + 1½ унции отвердителя 11 000 унций 11000 унций 4 000 унций 2 000 фунтов стерлингов 4 000 унций 2 000 фунтов стерлингов 4 000 унций 2 000 фунтов стерлингов 4 000 унций 9000 унций 4 000 унций в год 2 000 000 р. Всего (5½ унции смолы + 5½ унций отвердителя)
10 кв. Футов 26 унций Всего (13 унций + 13 унции отвердителя)
16 кв. Футов 42 унции Всего (21 унция смолы + 21 унция отвердителя)
24 кв. Фута 64 унции Всего (32 унции) смолы
Для больших проектов: используйте формулу 48 кв. Футов на галлон (½ галлоновой смолы + полуглянцевый отвердитель)
2.Измерение:
Очень важно, чтобы продукт был точно измерен и тщательно перемешан. Чистые градуированные чашки или
ванны должны использоваться для измерения. Отмерьте 1 часть смолы до 1 части отвердителя. НЕ меняйте это соотношение, эпоксидные смолы разработаны для отверждения
допри определенной пропорции смешивания, и любые отклонения могут привести к полному отверждению продукта. Мы рекомендуем всегда наливать
HARDENER в ваш смесительный контейнер, а затем смолу. Это поможет двум компонентам смешаться более тщательно.
3. Смешивание
— Объедините два компонента в один большой контейнер. Контейнер для смешивания должен быть примерно на 30% больше, чем количество
продукта, который вы смешиваете, так что полное перемешивание может быть выполнено без пролива через край контейнера.
— Смешивание продукта должно производиться вручную чистой палочкой для перемешивания. Чем больше продукта вы смешиваете, тем дольше будет
, чтобы получить полную смесь. Начинающим следует, как правило, смешивать только 2 кварты на одну порцию, это должно занять от 4 до 5 минут
смешивания.Обычно один галлон смеси занимает ок. 5-7 минут перемешивания. Два галлона смеси занимают ок. 6-8 минут
смешивания. Только опытные пользователи должны пытаться смешивать два галлона в партии. Сроки это с часами это хорошая идея.
— Процесс смешивания длительный и утомит запястье, но это самая важная часть проекта. Когда вы начнете смешивать
и, смолы почти сразу станут мутно-белого цвета. Это представляет два отдельных компонента, начинающих смешиваться.
По мере продолжения перемешивания уровень белизны начнет становиться более прозрачным, а конечным результатом будет полностью прозрачная смесь
, в которой вы можете видеть дно контейнера для смешивания. Смешивание должно продолжаться до тех пор, пока все признаки помутнения и неясных линий
полностью не исчезнут. Некоторые пузырьки воздуха являются нормальными в смеси, однако не взбивайте смесь. В результате взбивания смеси
иобразуются многочисленные крошечные пузырьки воздуха, которые превращают эпоксидную смолу в полностью белый от пузырьков, что может привести к тому, что пузырьки воздуха останутся в отвержденном продукте до
—.Будьте уверены, что вы очищаете стороны ведра и палки во время перемешивания. Может быть полезно использовать
яркий свет рядом с контейнером, чтобы смесь тщательно перемешалась. После того, как вы убедитесь, что в вашей смеси больше нет тонких туманных линий
и, пришло время налить. [Совет 1: Если вы не хотите рисковать недостаточным смешиванием, вы можете подождать, пока емкость для смешивания
не станет слегка теплой на ощупь, что обычно обеспечивает достаточно продолжительную смесь.Однако это также уменьшает ваше рабочее время, особенно при смешивании 1 галлона или более. Совет 2: быстро налейте после полного смешивания. Не оставляйте большое количество
смешанного материала в вашем ведре, это вызовет ускоренную химическую реакцию из-за выделяемого тепла
, и ваша партия может начать курить из-за этого избыточного тепла.]
4. Разлив.
ВНИМАНИЕ: При заливке смол на поверхность НИКОГДА не соскребайте и не вычищайте из контейнера
, из которого вы только что смешивали.Просто вылейте смолы и оставьте материал в контейнере.
а. Заливка герметизирующего слоя. Герметизирующий слой предназначен для проникновения и покрытия любых пористых поверхностей, с которыми вы будете работать. Герметизирующий слой отрезает любые потенциальные воздушные карманы в древесине, которые будут выпускать пузырьки воздуха. Лучший способ нанести герметик
— это начать с одного конца и залить смолу по всей длине поверхности. Положите контейнер вниз, а затем используйте резиновый валик
или пенопластовую кисть, чтобы перетянуть смолу по всей поверхности и добиться равномерного покрытия.Пожалуйста, имейте в виду, что вы не хотите, чтобы
желали добиться какого-либо наращивания с этим покрытием, оно предназначено только для того, чтобы покрыть зерна древесины или подложки. Обычно требуется только одно уплотнение
ислой. Однако иногда чрезвычайно пористая древесина или сучки в древесине нуждаются в нескольких слоях для полного уплотнения поверхности
и. Вы должны подождать как минимум 4 часа, прежде чем приступить к нанесению покрытия от наводнения. [Плотная древесина: необходимо соблюдать осторожность с плотной древесиной
и, чтобы избежать слишком большого скопления в герметизирующем слое.Если вы окажетесь в такой ситуации, вам следует уменьшить количество наносимого эпоксидного материала
, либо уменьшив количество эпоксидного материала, которое вы смешиваете для герметизирующего покрытия, либо отожмите излишки эпоксидного материала после того, как вы залили его
. Если ваш слой герметика становится слишком толстым, вы можете получить пузырьки воздуха, оставшиеся в отвержденной эпоксидной смоле.]
b. Заливка заливочного слоя: каждый заливочный слой выравнивается примерно на 1/8 ”. Если глубина больше, чем 1/8 ”-
или, необходимо несколько слоев.Однако вы должны подождать как минимум 4 часа между слоями покрытия. Наилучший способ нанесения покрытия Flood
: Для таблиц: залить эпоксидную смолу посередине и дать ей вытечь. Для баров: Начните с одного конца и залейте смолу
по всей длине. После того, как вы закончите налив, установите контейнер вниз. НЕ пытайтесь соскрести что-нибудь еще из ведра. Поскольку
вы наливаете примерно в три раза больше продукта, чем вы сделали с герметизирующим слоем, материал немедленно начнет вытекать.
Тем не менее, вы все равно захотите использовать резиновую швабру или пенопластовую щетку, чтобы перемещать материал вокруг. Чем меньше вы используете кисть
, тем лучше. Слишком сильное перетаскивание кисти приведет к появлению на поверхности сотен воздушных пузырьков, которые невозможно полностью удалить.
Как только вы достаточно покроете всю поверхность, вы начнете процесс выталкивания пузырьков воздуха. Лучший инструмент для удаления пузырьков
и— это небольшая пропановая горелка. Держа источник тепла примерно на расстоянии от 6 до 10 дюймов от поверхности и
, быстро проносясь через него, вы сразу увидите, как пузырьки начинают всплывать.Другие инструменты, которые можно использовать для всплытия пузырьков, — это тепловая пушка
или фен. Однако оба этих инструмента перемещают воздух, что увеличивает риск оседания пыли в покрытии.
— это хорошая идея, чтобы поддерживать проект в течение не менее 30 минут после заливки, чтобы выбросить любые пузырьки воздуха, которые внезапно появятся.
Другие проблемы с заливным слоем:
— Рельсовые полосы и кромки: можно покрывать заливочный слой по сторонам, создавая покрытие на вертикальных кромках.
Эти края не будут создавать такое же толстое покрытие, как плоские поверхности, поэтому вы должны приложить все усилия с помощью кисти, чтобы материал оставался ровным.
-Нижняя кромка: под балкой или кромкой образуются капли, эти капли можно отшлифовать после того, как эпоксидная смола отвердит
Если вы поймали эпоксидную смолу в нужный момент в процессе отверждения, можно использовать бритвенный нож, чтобы отрезать капли.
5. Повторное покрытие:
При повторном покрытии в течение 4–12 часов не требуется подготовка поверхности.Слои будут соединяться вместе как
и. Если вы позволите предыдущему слою полностью высохнуть, необходимо очень легкое шлифование с помощью наждачной бумаги с зернистостью от 180 до 220 После легкого шлифования
следует протереть поверхность растворителем, таким как денатурированный спирт или ацетон. НЕ используйте разбавитель краски, aka
минеральные спирты. Процесс протирания растворителем следует проводить с чистой тряпкой, которая не оставит ворсинок на поверхности.
Продолжайте чистку, пока вся шлифовальная пыль не будет полностью удалена.Теперь вы готовы перекрасить. Не беспокойтесь о шлифовальных царапинах
и. Следующая заливка заполнит царапины и снова будет выглядеть как стекло.
Руководство по покрытию от наводнения (16 квадратных футов на галлон)
Площадь для покрытия общего объема эпоксидной смолы (количество смолы + отвердитель)
_____________________________________________________________________________
1 кв. Фут 8 унций всего (4 унции смолы + 4 унции отвердителя)
9000oz 2 унции 4 Sq 2 унции 4 Sq 2 унции 4 Sq 2 унций 4 Sq 2 унции 4 Sq 2 унции 4 Sq 2 унции 4 Sq 2 унции Всего (16 унций смолы + 16 унций отвердителя)10 кв. Футов 80 унций Всего (40 унций смолы + 40 унций отвердителя)
16 кв. Футов 128 унций всего (64 унции смолы + 64 унции отвердителя)
24 кв. Футов 192 унции всего (96 унций смолы + 96 унций)
Для больших проектов: используйте формулу из 16 кв. Футов на галлон (½ галлоновой смолы + полуглянцевый отвердитель) 6.Отверждение: После нанесения последнего слоя, продукт должен храниться как можно более чистым и без пыли.
При температуре 80 ° F продукт высыхает на ощупь примерно за 12-14 часов. Тем не менее, продукт не должен быть использован в любых
типа использования в течение по крайней мере 2-3 дней, что позволит ему достичь достаточной твердости. При температуре ниже 80 F продукт затвердевает на
дольше. Первые пару недель после отверждения поверхность более подвержена царапинам, поэтому мы рекомендуем по возможности использовать подставки
и салфетки.По мере старения продукта его твердость будет увеличиваться.
7. Очистка отвержденной поверхности: если продукт загрязняется от ежедневного использования, мы рекомендуем чистить его раствором
мягкого антибактериального мыла и воды. Использование агрессивных кухонных химикатов, не предназначенных для пластика, может привести к размягчению или липкости эпоксидной смолы.
Усовершенствованные методики
После ознакомления с правильными процедурами нанесения, эти методы можно попробовать.
1. Встроенные рисунки: в этот продукт могут быть встроены такие объекты, как рисунки, статьи и карты.Некоторые тонкие листы бумаги
, такие как газетная бумага и журналы, должны быть сначала запечатаны белым клеем или подобным продуктом. Это предотвращает проникновение эпоксидной смолы в бумагу и вызывает полупрозрачный эффект. В качестве альтернативы вы можете ламинировать тонкую бумагу в пластик, чтобы эпоксидная смола не вступала в непосредственный контакт с ней. Большая часть бумаги фотографического качества не требует этих дополнительных шагов. После того, как бумаги будут правильно запечатаны, их можно поместить
нана поверхность вашего проекта.Убедитесь, что ваша бумага будет лежать ровно, прежде чем положить ее. Как правило, вы должны подождать как минимум один час
после нанесения эпоксидного герметика перед тем, как ставить предметы. Последующие затопления покрывают и пропускают эти объекты.
2. Вложение твердых предметов: Дерево, камни, ракушки, крышки от бутылок, монеты и т. Д. Также могут быть встроены в этот продукт. Все
пористых объектов должны быть сначала запечатаны; либо с самой эпоксидной смолой, либо с другим типом герметика, такого как шеллак, лак или полиуретан.Если
объекты не будут должным образом запечатаны, они выпустят крошечные пузырьки воздуха, которые будут образовываться вокруг объекта во время затопления.
Размещение этих объектов может быть выполнено до того, как вы нанесете первый герметизирующий слой, или они могут быть помещены в ранее нанесенный герметизирующий слой
, который был отвержден в течение 30 минут. Легкие предметы, такие как крышки от бутылок, должны быть приклеены, чтобы предотвратить плавание.
3. Толстые наращивания: этот продукт можно использовать для создания неограниченной глубины.Каждый слой покрытия не должен превышать 3/16 ”.
Попытка залить толще может привести к чрезмерному нагреву эпоксидной смолы, что, в свою очередь, приведет к образованию пузырьков воздуха, возможно, к растрескиванию и усадке
. Желательно подождать как минимум 4 часа между заливками, чтобы обеспечить достаточное отверждение и охлаждение. Хотя этот продукт
считается прозрачным по стандартам эпоксидной смолы, у него очень слабый янтарный оттенок. Этот цвет практически незаметен на глубинах от
дотолщиной до 1/2 ”.Цвет эпоксидной смолы может стать заметным на больших глубинах, особенно на светлых поверхностях.
4. Глушение кромок: мы обычно рекомендуем, чтобы эпоксидная смола текла по краям вашей поверхности, так как она будет саморазрешать
на уровне примерно 1/8 ”за раз. Если ваше приложение требует строительства временной плотины, это должно быть сделано с большой осторожностью, чтобы ее можно было удалить после отверждения эпоксидной смолы. В идеале следует использовать гладкую, мягкую или гибкую пластиковую полосу, потому что эпоксидная смола
не будет прилипать к ней.В качестве альтернативы можно использовать деревянную отделку, но только если она сначала покрыта пластиковым листом толщиной от 2 до 4 мил. Подкладка
деревянной отделкой пластиком и прикрепление ее к краю должно препятствовать проникновению эпоксидной смолы между краем и пластиком.
Необходимо провести тестирование на небольшом макете, чтобы убедиться в отсутствии утечек или проблем с вашей техникой плотины.
Устранение неисправностей
1. Вся поверхность становится мягкой, влажной или липкой через 48 часов:
1.Продукт был недостаточно смешан. К сожалению, несмотря на то, что мы подчеркиваем это как самую важную часть проекта, он все еще может возникнуть и является самой распространенной причиной этой проблемы. Если вы не смешали достаточно долго или не поцарапали стороны и дно контейнера
во время перемешивания, вы найдете недостаточно отвержденную эпоксидную смолу. Пожалуйста, перечитайте Раздел 3 наших инструкций.
2. Продукт был измерен неточно. Вы должны соблюдать строгое соотношение 1 к 1 по объему. Не угадывайте и не проверяйте эти
измерения.Просто выгрузка продукта из оригинальной упаковки не является правильным измерением. Продукт ДОЛЖЕН быть измерен с довольно точной точностью, используя градуированную ванну.
Решения: 1. Если поверхность твердая, но слегка липкая, на всю поверхность может быть нанесен новый заливочный слой, а новый продукт
высохнет при условии, что процедуры смешивания были соблюдены должным образом.
2. Если поверхность влажная и мягкая, необходимо удалить как можно большую часть материала с помощью скребка для краски или ножа
.При необходимости используйте денатурированный спирт или ацетон, чтобы удалить влажную эпоксидную смолу. Ремикс и нанесите новый слой покрытия. Новое покрытие
покроет почти все последствия предыдущей ошибки. Обязательно соблюдайте правильные процедуры смешивания.
2. Липкие или мягкие пятна. Наиболее распространенной причиной этого является соскабливание или чистка со стороны или дна емкости для смешивания
во время заливки. Естественно хотеть использовать каждую последнюю каплю, которую вы смешали. Однако, когда вы выливаетесь на поверхность, вы должны
ипросто выбросить ее и поставить контейнер вниз.Если вы попытаетесь удалить каждую каплю с помощью палки или щетки, вы, скорее всего, получите
с липкими пятнами.
Решение для: 1. Если липкие пятна являются твердыми, но имеют незначительную липкость на поверхности, вы можете повторно залить всю поверхность
, и новый продукт высохнет сильно, при условии соблюдения правильных процедур заливки.
2. Если эти пятна мягкие и влажные, вам нужно будет поцарапать или вырезать как можно больше мягкого материала с помощью скребка или ножа для краски
.При необходимости используйте денатурированный спирт или ацетон, чтобы удалить влажную эпоксидную смолу. Если в результате у вас останутся глубокие впадины
и, ваш первый повторный слой должен использоваться только для заполнения областей, в которых вы царапали. После того, как эта заливка в течение
по меньшей мере 4 часа может быть завершена, полное повторное покрытие может быть завершено. Это скроет недостатки и оставит вас с твердой стеклянной поверхностью.
3. Воздушные пузырьки: существует множество типов и причин возникновения чрезмерных воздушных пузырьков. Мы перечислили несколько ниже.
1. Воздушные пузырьки по всей поверхности.
а. Как показано в разделе 4 наших инструкций, метод удаления пузырьков не использовался.
б. Неправильно нанесено или не использовалось герметизирующее покрытие.
c. Поверхность дерева внизу была чрезвычайно пористой, а слой герметика был недостаточно толстым, чтобы покрыть его. (Очень часто
в состаренном дереве).
д. Продукт взбивали или перемешивали чрезмерно, добавляя в смесь так много пузырьков, что их нельзя было удалить
с помощью техники пламени / нагрева.Очень часто для пользователей, использующих дрель-миксер в своей технике смешивания или
,перемешивают продукт слишком агрессивно.
эл. Сильно перетаскивая кистью эпоксидную смолу при нанесении. Эти крошечные пузырьки иногда появляются в облачных полосах
, где использовалась техника чистки. Подумайте об использовании резиновой ракели вместо того, чтобы распространять.
2. Пузырьки воздуха в одном месте.
а. Узлы, трещины или отверстия в древесине не были должным образом запечатаны, и пузырьки воздуха постоянно поднимаются в течение всего процесса отверждения.
б. Пропустил место во время нанесения покрытия.
Решение: Обычно пузырьки недостаточно заметны, чтобы гарантировать дальнейшую работу. Однако, если вы хотите, вы можете
отшлифовать или отшлифовать поверхность, чтобы удалить как можно больше пузырьков воздуха и повторно покрыть всю поверхность.
4. Поверхностное отверждение Неравномерно с помощью ряби или волн:
a. Деревянная поверхность имела слишком много перекосов или дефектов, и одного слоя эпоксидной смолы было недостаточно, чтобы покрыть эти проблемы.
б.Нанесение слишком тонкого слоя. Этот продукт должен быть нанесен в полных слоях покрытия 1/8 ”для правильного выравнивания.
c. Применение слишком большого количества тепла во время ваших методов удаления пузырьков вызовет волновой эффект. Нагрев или горелка должны быть быстро пройдены по поверхности, не удерживая ее в одном месте.
Решение: Нанесение еще одного слоя покрытия достаточной толщины должно скрыть практически все признаки волн или ряби
от предыдущего слоя.