Поливинилацетат — Википедия
Поливинилацетат | |
---|---|
![]() ( {{{картинка}}} ) | |
Общие | |
Систематическое наименование | poly (1-acetyloxiethene) |
Сокращения | ПВА, PVA |
Традиционные названия | Поливинилацетат |
Хим. формула | (C4H6O2)n |
Рац. формула | [—Ch3CH(OCOCh4)—]n |
Физические свойства | |
Молярная масса | 86.09 г/моль |
Плотность | 1,19 г/см³ |
Классификация | |
Рег. номер CAS | 9003-20-7 |
Рег. номер EINECS | 618-358-7 |
ChEBI | 32028 |
![]() |
Поливинилацетат (сокр. ПВА) — полимер винилацетата. Твердое бесцветное прозрачное нетоксичное вещество; не имеет запаха.
Химическая формула: [—CH2—CH(OCOCH3)—]n. Международное обозначение: PVAC.
- Молекулярная масса: 10—1500 тыс.;
- Плотность — 1,1—1,2 г/см³;
Растворяется в уксусной кислоте и многих органических растворителях: ацетоне, метаноле, этилацетате, бензоле, метилен-хлориде и др.
Мировое производство поливинилацетата в 1973 составило около 1 млн т.
Основной сферой применения поливинилацетата является производство поливинилацетатного клея (клей ПВА), водоэмульсионных и акриловых красок, а также дальнейшая переработка в поливиниловый спирт и поливинилацетали.
- Химическая энциклопедия
- Поливинилацетат
![]() | Для улучшения этой статьи по химии желательно:
|
Как получают поливинилацетат
У такого полимера, как поливинилацат, представляющий собой сложный эфир уксусной кислоты и винилового спирта, довольно узкая область применения по сравнению, скажем, с ПВХ, полиэтиленом или полиуретаном.
Однако это не снижает значимости данного полимера, поскольку клей, изготавливаемый на его основе, по массовости применения, справедливо можно назвать королём всех клеёв.
В быту клей ПВА практически вытеснил другие клеи, например, силикатный канцелярский, и не применяется он при склеивании лишь тех материалов, которые он не склеивает в принципе.
Кроме производства клея, ПВА используется для получения акриловых и водоэмульсионных красок, лаков, а также для получения поливинилового спирта.
Для получения ПВА используется полимеризация винилацетата. Поскольку виниловый спирт является химически очень нестойким веществом, легко окисляющимся до ацетальдегида, то и получение винилацетата прямой этерификацией невозможно.
Поэтому данный сложный эфир получают либо присоединением к уксусной кислоте ацетилена в присутствии сульфатов ртути, либо окислительным взаимодействием уксусной кислоты с этиленом на палладиевом катализаторе.
Полимеризация винилацетата выполняется тремя способами:
- Эмульсионным;
- Блочным;
- В растворе.
Поскольку ПВА наиболее часто используется в растворённом виде, то последний метод имеет наибольшее распространение. При его получении, применяемого в строительстве, немалую значимость имеет эмульсионный метод.
При промышленной полимеризации винилацетата в качестве растворителя, в основном используются:
- Бензол;
- Этанол;
- Этилацетат.
Для проведения реакции используются реакторы из никеля либо алюминия, оснащённые мешалкой, паровой рубашкой, а также обратным холодильником.
Исходная реакционная смесь содержит винилацетат, перекись бензоила, служащая инициатором процесса полимеризации, и растворитель.
Кроме того, в число компонентов входит уксусный либо пропионовый альдегид, количеством которого регулируется вязкость полимера.
Смесь нагревается до того момента, когда начнётся слабое кипение растворителя. Процесс длится от 12 до 18 часов.
Эмульсионную полимеризацию проводят двумя способами.
Первый метод. Заключается в применении водорастворимых инициаторов, обеспечивающих образование устойчивой суспензии или эмульсии,
Второй — в применении инициаторов, которые растворяются в мономере.
В результате полимеризации получаются гранулы ПВА.
Эмульгирование при использовании первого метода осуществляется сульфокислотами и мылами. Инициатором выступает пероксид водорода.
После двухчасового энергичного перемешивания смеси при температуре 70°С получается устойчивая эмульсия ПВА типа латекса.
В случае применения второго метода инициаторы, к примеру, перекись бензоила, растворяются в мономере.
Для эмульгирования используются:
- Полиакриловая кислота;
- Поливиниловый спирт;
- Другие полимеры, которые растворяются в воде.
Конечным продуктом является твёрдый чистый ПВА с молекулярной массой, достигающей 500000.
Процесс проводится в реакторах с пропеллерными (быстроходными) мешалками на протяжении 2-6 часов.
Температура при этом составляет 80°С.
В результате образуется продукт, называемый бисером, который после оседания, фильтруется, а затем промывается водой.
В заключении хотим подчеркнуть. Для предотвращения причинения вреда здоровью персонала, на таких предприятиях, рабочие должны периодически проходить обучение по охране труда, а руководством периодически производиться оценка профессиональных рисков, утвержденного в рамках трудового законодательства РФ.
Глава 4. Получение поливинилацетата

В настоящее время в промышленности используются следующие методы полимеризации винилацетата (ВА): в растворе, суспензии и эмульсии.
4.1. Производство растворов ПВА
Растворная (лаковая) полимеризация ВА применяется главным образом в производстве поливинилового спирта (ПВС) и поливинилацеталей. Она позволяет легко регулировать ММ и ММР конечных продуктов полимераналогичных превращений ПВА, растворы легко выгружаются из аппаратов, транспортируются по трубопроводам, отпадает необходимость в приготовлении раствора ПВА для проведения последующих операций.
Примерные рецепты для полимеризации ВА в растворе органических растворителей представлены в табл. 4.1.
Таблица 4.1 Рецепты для полимеризации ВА в растворе органических растворителей
Компоненты, масс.ч. | Рецепт 1 | Рецепт 2 | Рецепт 3 |
Винилацетат | 100 | 100 | 95 |
Растворитель | Метанол, 70 | Этанол, 100–1000 | Метанол, 5 |
Инициатор | ДАК, 0,03–0,5 | ПБ, 0,1–0,5 | ДАК, 0,30 |
Пропионовый альдегид | – | 0,01–0,3 | – |
Вместо метанола в рецепте 1 могут быть этилацетат или метилацетат, а вместо ДАК – пероксид бензоила (ПБ). Соотношения ВА:ДАК могут широко варьироваться.
Так как реакция омыления ПВА протекает в спиртовой среде, этот тип растворителя целесообразно использовать и для полимеризации ВА. Из алифатических спиртов чаще используют метанол, т.к. он доступен и практически не содержит воды, что важно для реакции омыления ПВА. Этанол применяется для изготовления нетоксичного ПВС медицинского и пищевого назначения. Оба спирта образуют с ВА азеотропные смеси, кипящие при более низкой температуре, чем чистые компоненты (Т.кип. азеотропа ВА – метанол 58,8 °С, а ВА – этанол 67,3 °С). Это облегчает отвод теплоты реакции в процессе полимеризации.
Молекулярная масса ПВА регулируется соотношением ВА:спирт:инициатор (ДАК) в реакционной среде. Для контроля процесса вместо ММ определяют динамическую вязкость молярного раствора ПВА в бензоле (86 г полимера в 1 л бензольного раствора). На
практике для определения молекулярной массы ПВА используют данные табл. 4.2.
Таблица 4.2 Зависимость молекулярной массы ПВА от вязкости молярных растворов в бензоле
Вязкость молярного | 6 | 9 | 15 | 20 | 25 | 40 | 50 | 65 | |||
раствора, мПа с | |||||||||||
|
|
|
|
|
|
|
| ||||
|
|
| 26,3 | 38,9 | 69,2 | 83,1 | 99,9 | 132 | 153,5 | 201,5 | |
| M 10−3 |
Для коррекции значений вязкости молярных растворов варьируют соотношение реагентов и завершенность полимеризации (табл. 4.3).
Таблица 4.3 Зависимость вязкости молярного раствора ПВА от состава реакционной смеси
| Вязкость молярного раствора | спирт: :ДАК, масс.ч. | Вязкость молярного раствора | ||
| ПВА, мПа с | ПВА, мПа с | |||
ВА:спирт:ДАК, | Полимеризация | Полимеризация | Полимеризация | Полимеризация | |
масс.ч. | до полной | до конверсии | до полной | до конверсии | |
| |||||
| конверсии | 50…60 % | ВА | конверсии | 50…60 % |
|
|
|
|
| |
|
|
|
|
|
|
Метанол |
|
| Метанол |
|
|
100:10:0,1 | 50 | 70 | 100:80:0,2 | 10 | – |
100:15:0,1 | 45 | 60 | 100:90:0,25 | 9 | – |
100:20:0,1–0,15 | 30 | 50 | 100:100:0,3 | 6 | – |
100:25:0,1–0,15 | 25 | 45 | Этанол |
|
|
100:36:0,1–0,15 | 20 | 35 | 100:50:0,019 | 3,5–5 | – |
100:50:0,15 | 15 | 25 | 100:56:0,019 | 3,0–4 | – |
Процесс полимеризации ВА в растворе периодическим методом осуществляется в полимеризаторе из хромоникелевой или хромистой стали вместимостью 10…20 м3, снабженном якорной или рамной мешалкой с частотой вращения 2…35 об/мин, рубашкой и конденсатором-холодильником.
В соответствии с заданной рецептурой из мерников в полимеризатор подают ВА, метанол и раствор инициатора в метаноле с концентрацией 4…5 % масс. Полимеризатор обогревается горячей водой, подаваемой в рубашку аппарата. Реакционная смесь закипает при 59…62 °С (в зависимости от содержания в ней растворителя) и избыток теплоты экзотермической реакции отводится за счет испарения азеотропной смеси ВА – метанол, а при подъеме температуры выше 65 °С в рубашку аппарата подают холодную воду. Пары, не сконденсировавшиеся в конденсаторе, охлаждаемом водой, поступают в холодильник, охлаждаемый рассолом с температурой от –10 до –13 °С.
По мере нарастания вязкости реакционной массы постепенно уменьшают частоту вращения мешалки. Через 2…3 ч при получении ПВА с молярной вязкостью 50…70 мПа с или через 4…8 ч при
получении более низкомолекулярного ПВА реакционную смесь разбавляют метанолом, и полимеризацию продолжают до конверсии ВА не менее 97 %. Полученный лак ПВА разбавляют метанолом до концентрации 25…40 % масс.
Полимеризацию ВА в этаноле осуществляют аналогично, но при 68…76 °С. Разбавление этанолом раствора низкомолекулярного полимера до концентрации 35…40 % масс. проводят после завершения реакции. Конверсия ВА достигает 93…98 %.
Полимеризация ВА непрерывным методом осуществляется в двух или трех последовательно соединенных реакторах, снабженных мешалками с переменным числом оборотов, рубашками и конденсаторами-холодильниками. Реакционная масса передается из одного реактора в другой самотеком или насосами в зависимости от их взаимного расположения. В рубашки аппаратов подается горячая вода.
Конверсия ВА после первого полимеризатора составляет примерно 30 %, а на выходе из третьего полимеризатора – 50…70 %, в зависимости от марки ПВА. Реакционная смесь после последнего полимеризатора представляет собой метанольно-винилацетатный раствор ПВА с концентрацией около 60 % масс. и динамической
вязкостью 104…107 мПа с, в зависимости от марки ПВС. Этот раствор разбавляют метанолом до концентрации 25…30 % масс.
4.2. Производство полимеров и сополимеров винилацетата эмульсионным методом
Процессы полимеризации ВА в водной эмульсии широко используются в практике. Эмульсии выпускают двух типов: мелкодисперсные (иначе тонкодисперсные или латексные) с размером частиц 0,05…0,5 мкм и крупнодисперсные (иначе грубодисперсные или просто дисперсные) с размером частиц от 0,5 до 10 мкм. В наибольших масштабах отечественная промышленность выпускает грубодисперсные ПВА эмульсии, т.к. они обладают высокой стойкостью к различным факторам: многократное замораживание и оттаивание, нагревание почти до 100 °С, введение различных наполнителей, электролитов, пластификаторов. Недостатком этих дисперсий является сравнительно невысокая водостойкость образуемых ими покрытий, их низкая прозрачность, отсутствие блеска. Мелкодисперсные ПВА-эмульсии образуют при высыхании блестящие водостойкие покрытия и применяются, прежде всего, в производствах высококачественных водоэмульсионных красок.
Характерной особенностью ПВА-эмульсий (как латексов, так и дисперсий) является невысокая вязкость при относительно большом содержании полимера. Они применяются для нанесения покрытий, изготовления водных красок, для пропитки бумаги и тканей, искусственной кожи, мастик для полов и т.д. Эмульсионную полимеризацию проводят в водной среде. Эмульгаторами при получении латексов ПВА служат различные мыла, соли жирных кислот, сульфокислоты, а при получении мелкодисперсного ПВА используют полимерные защитные коллоиды – поливиниловый спирт без ацетатных групп или с 5…25%-м их содержанием, метилцеллюлоза, гидроксиэтилцеллюлоза и др. Инициируют процесс водорастворимые инициаторы – пероксид водорода, персульфат калия, персульфат аммония, окислительно-восстановительная система «пероксид водорода – сульфат Fe (II)». Для поддержания рН среды используют буферные соединения – бикаронат натрия, муравьиную или уксусную кислоты и др. Рецепты получения ПВА эмульсионным методом приведены в табл. 4.4.
Таблица 4.4 Рецепты получения ПВА эмульсионным методом (масс.ч.)
Компоненты |
| Крупнодисперсная | Латексная |
| |||
1 |
| 2 | 3 | 4 | 5 | 6 | |
|
| ||||||
Винилацетат | 100 |
| 100 | 100 | 100 | 100 | 65 |
Вода | – |
| 150–200 | – | 90–100 | 100–150 | – |
Олеат калия | – |
| – | – | – | 0,1–0,5 | – |
Поливиниловый | – |
| 5–7 | – | – | – | – |
спирт |
| ||||||
|
|
|
|
|
|
| |
Перекись водорода | 1,2–2 |
| 1,0–2,5 | 1,0–3,0 | – | 0,5–1,5 | – |
(30%-я) |
| ||||||
|
|
|
|
|
|
| |
Сульфат железа (II) | 0,0005–0,0009 | 0,0005–0,0015 | – | – | – | – | |
Муравьиная кислота | 0,2–0,4 |
| – | – | – | – | – |
Водный раствор ПВС | 80–100 |
| – | – | – | – | – |
(5–9 % масс.) |
| ||||||
|
|
|
|
|
|
| |
Уксусная кислота | – |
| 0,1–0,2 | – | – | – | – |
Водная фаза, | – |
| – | 88 | – | – | – |
в т.ч.: |
| ||||||
|
|
|
|
|
|
| |
Вода | – |
| – | 80 | – | – | – |
дистиллированная |
| ||||||
|
|
|
|
|
|
| |
ПВС (100%-й) | – |
| – | 7–7,5 | – | – | – |
Муравьиная | – |
| – | 0,14–0,34 | – | – | – |
кислота (90%-я) |
| ||||||
|
|
|
|
|
|
| |
Сульфат железа | – |
| – | 0,0005–0,0014 | – | – | – |
95%-й |
| ||||||
|
|
|
|
|
|
| |
Эмульгатор С-10 | – |
| – | – | 5 | – | – |
Персульфат аммония | – |
| – | – | 0,5 | – | 0,5 |
Дибутилмалеинат | – |
| – | – | – | – | 35 |
Продолжение табл. 4.4
ПВА, содержащий |
|
|
|
|
|
| |
10–14 % масс. | – | – | – | – | – | 4 | |
ацетатн. групп |
|
|
|
|
|
| |
Сода | – | – | – | – | – | 0,25 | |
кальцинированная | |||||||
|
|
|
|
|
| ||
Оксиэтилцеллюлоза | – | – | – | – | 5–7 | – | |
Проксанол-168 | – | – | – | – | 0,5 | – |
Выбор рецептуры зависит от получаемой марки. Получают поливинилацетатные эмульсии как периодическим, так и непрерывным методом.
Периодический процесс проводят в реакторе из хромоникелевой стали емкостью 4…16 м3, снабженном якорной или якорно-рамной мешалкой, рубашкой для обогрева или охлаждения, а также системой из двух последовательно соединенных холодильников, один из которых охлаждается оборотной водой (зимой) или рассолом (летом). Водная фаза готовится в отдельном аппарате с мешалкой и рубашкой. Водная фаза содержит воду, ПВС и муравьиную кислоту. В реактор из мерников загружают водный раствор ПВС, ВА, водный раствор сульфата железа и пероксид водорода. Отвод теплоты осуществляется за счет испарения азеотропной смеси «ВА – вода», конденсирующейся в обратных холодильниках. 20 % теплоты отводится через рубашку аппарата. Для облегчения съема тепла пероксид водорода и ВА загружают в аппарат в 3…5 приемов. Температура полимеризации вначале определяется температурой кипения азеотропа (65…68 °С). По мере расходования ВА температуру повышают до 70…75 °С (но не выше 92 °С). При непрерывном перемешивании и температуре 65…75 °С процесс ведут 1,5…3 ч до остаточного содержания ВА
0,5…1,5 %. Остатки ВА удаляют при 75…85 °С и давлении 200…266 кПа в аппарате, вместимостью 6…40 м3 (стандартизаторе). Здесь дисперсию нейтрализуют аммиачной водой до рН 4,5…6 (во избежание коррозии оборудования при последующей переработке дисперсии). Целесообразно нейтрализовать ПВА-эмульсию порошкообразным оксидом или гидроксидом кальция. Для снижения температуры стеклования полимера дисперсию пластифицируют ДБФ, а если ПВА-эмульсии предполагается применять в пищевой промышленности (например, при изготовлении тары и др.) целесообразна пластификация менее токсичным дибутилсебацинатом. Введение пластификатора снижает морозостойкость, поэтому ПВА-эмульсии пластифицируют перед употреблением. Введение в ПВА 0,2…0,5 % масс. малеинового
Винилацетат — сырье для получения поливинилацетата
Винилацетат – это виниловый эфир уксусной кислоты с химической формулой СН3СООСН=СН2, представляет собой бесцветную прозрачную жидкость с характерным эфирным запахом, с температурой кипения 72,5 °С.
Получение винилацетата
Винилацетат получают из ацетилена и уксусной кислоты в присутствии катализатора:
В промышленности его получают газофазным и жидкофазным способами.
Газофазный способ имеет наибольшее распространение. Все большее значение приобретает способ получения винилацетата из этилена и уксусной кислоты, впервые разработанный в Советском Союзе. По этому способу смесь этилена и кислорода пропускают через раствор или суспензию хлорида палладия и ацетата натрия в присутствии окислительно-восстановительной системы в уксусной кислоте. При барботировании этилена через раствор хлорида палладия в уксусной кислоте образуется комплекс этилена с хлоридом палладия (PdCl2CH2=CH2). Этилен легко реагирует с растворами хлорида палладия в уксусной кислоте в присутствии ацетата натрия. Реакция протекает по уравнению:
Металлический палладий в присутствии окислительно-восстановительной системы хлорид меди (I) и (II) снова окисляется в ион Pd2+
Процесс протекает непрерывно, выход винилацетата составляет 97% от теоретического в расчете на этилен.
Полимеризация винилацетата
Винилацетат легко полимеризуется как в жидкой, так и в газовой фазе под влиянием света, тепла, инициаторов и катализаторов. Реакция протекает с большим выделением теплоты (89,2 кДж/моль). В зависимости от природы инициаторов и условий проведения полимеризации образуются различные продукты: от жидких и вязких до твердых полимерных веществ.
Полимеризация винилацетата в присутствии инициаторов протекает по радикальному механизму:
Элементарные звенья в цепи соединяются в основном по типу α,β-присоединения, т. е. «голова к хвосту». Однако в состав макромолекул поливинилацетата входит 1—2% звеньев, соединенных по типу «голова к голове» (α,α-присоединение).
При полимеризации винилацетата наряду с линейным может образоваться разветвленный полимер, преимущественно по месту отрыва водорода от метильных групп при протекании побочной реакции передачи цепи на полимер.
Винилацетат легко вступает в реакцию сополимеризации с различными мономерами. В большинстве случаев этот процесс протекает с меньшей скоростью, чем процесс гомополимеризации винилацетата.
В технике полимеризацию винилацетата проводят в растворе, эмульсии, суспензии и в массе. Наибольшее распространение в промышленности получил метод полимеризации винилацетата в растворе («лаковый» метод).
Список литературы:
Кузнецов Е. В., Прохорова И. П., Файзулина Д. А. Альбом технологических схем производства полимеров и пластмасс на их основе. 2-е изд. М., Химия, 1976. 108 с.
Лосев И. Я., Тростянская Е. Б. Химия синтетических полимеров. 3-е изд. М., Химия, 1971. 615 с.
Николаев А. Ф. Синтетические полимеры и пластические массы на их основе. 2-е изд. М. — Л., Химия, 1966. 768 с. Технология пластических масс. Л., Химия, 1977. 366 с.
Розеноерг М. Э. Полимеры на основе винилацетата. Л., Химия, 1983. 252 с.
Автор: Коршак В.В.
Источник: Коршак В.В., Технологии пластических масс, 3-е издание, 1985 год
Дата в источнике: 1985 год
Винилацетат — Википедия
Материал из Википедии — свободной энциклопедии
Винилацетат — органическое соединение класса сложных эфиров, прозрачная жидкость с характерным запахом.
- 2Ch3=Ch3+2Ch4COOH+O2→Pd2+2Ch4COOCH=Ch3+2h3O{\displaystyle {\mathsf {2CH_{2}{\text{=}}CH_{2}+2CH_{3}COOH+O_{2}{\xrightarrow[{}]{Pd^{2+}}}2CH_{3}COOCH{\text{=}}CH_{2}+2H_{2}O}}}
Процесс проводят преимущественно на стационарном твердом катализаторе (0,1—2,0 % Pd, нанесенного на Al2O3, SiO2 или др. и модифицированного, например CH3COONa, солями Сu) при 170—200 °С и 0,5—1,0 МПа. Объемное соотношение этилен: пары уксусной кислоты: O2 в исходной смеси ~ 8:4:1. Степень превращения этилена, уксусной кислоты и O2 за проход — 10, 20 и 60—70 %. Основной побочный продукт — CO2; ацетальдегида образуется менее 1 %.
Процесс на гомогенном катализаторе (PdCl2 с CuCl2 в уксусной кислоте с добавками CH3COONa или LiCl) осуществляют при 110—130 °С и 1—3 МПа. Суммарный выход винилацетата и ацетальдегида ~ 90 % в расчете на этилен. Недостаток процесса — высокая коррозионная активность катализатора (требуется аппаратура из титана).
Не утратил значения также способ синтеза винилацетата из ацетилена и уксусной кислоты в присутствии ацетата цинка на активированном угле при 170—220°С. Мольное соотношение Ацетилен:Уксусная кислота составляет (3-5):1; выход винилацетата 95—98 % по уксусной кислоте[2].
В органическом синтезе для введения винильной группы и как мономер для получения поливинилацетата и сополимеров. Например, из сополимеров винилацетата изготавливается универсальный полимерный клей для приклеивания потолочной плитки и плинтусов из пенополистирола.
Поливиниловый спирт — это… Что такое Поливиниловый спирт?
Структурная формула поливинилового спиртаПоливиниловый спирт (ПВС, международное PVOH, PVA или PVAL) — искусственный, водорастворимый, термопластичный полимер. Синтез ПВС осуществляется реакцией щелочного/-кислотного гидролиза или алкоголиза сложных поливиниловых эфиров. Основным сырьем для получения ПВС служит поливинилацетат (ПВА). В отличие от большинства полимеров на основе виниловых мономеров, ПВС не может быть получен непосредственно из соответствующего мономера -винилового спирта (ВС). Некоторые реакции, от которых можно было бы ожидать получения мономерного ВС, например присоединение воды к ацетилену, гидролиз монохлорэтилена, реакция этиленмонохлоргидрина с NaOH, приводят к образованию не винилового спирта, а ацетальдегида. Ацетальдегид и ВС представляют собой кето- и енольную таутомерные формы одного и того же соединения, из которых кето-форма (ацетальдегид) является намного более устойчивой, поэтому синтез ПВС из мономера — невозможен:
Кето-енольная таутомерия винилового спиртаИстория
Поливиниловый спирт впервые был получен в 1924 году химиками Германом (Willi Herrmann) и Гонелем (Wolfram Haehnel) реакцией омыления при омылении раствора поливинилового эфира стехиометрическим количеством гидроксида калия KOH. Исследования в области получения ПВС в начале прошлого века проводили ученые Гонель, Германн (Hermmann)и Херберт Берг (Berg). Классический способ омыления проводился в среде в абсолютизированного (осушенного) этилового спирта при соотношении 0,8 моль омыляющего агента на 1,0 моль ПВА, при этом происходило практически полное омыление ПВА. Было найдено, что поливиниловый спирт может быть получен реакцией переэтерификации поливинилацетата(ПВА) в присутствии каталитических количеств щелочи. Данная реакция является классическим примером — полимераналогичного превращения. За 80 лет исследований накоплен достаточно большой экспериментальный материал по проблеме получения ПВС. Детальный обзор литературы посвященной ПВС представлен в монографиях С.Н Ушакова (1960 г.) [1], А. Финча (1973, 1992 гг.) [2, 4], М.Э Розенберга (1983 г.) [3] и Т. Сакурады (1985 г.) [17].
Синтез и получение
В настоящее время промышленный синтез ПВС осуществляют путем полимераналогичных превращений, в частности, с использованием в качестве исходных полимеров простых и сложных поливиниловых эфиров, таких как ПВА. К основным способам получения ПВС можно отнести различные варианты омыления ПВА в среде спиртов или в воде в присутствии оснований и кислот. В зависимости от используемой среды и типа катализатора, процессы омыления ПВА можно представить следующей общей схемой:
Общие способы получения поливинилового спиртаПриведенные схемы реакций можно разбить на три группы: алкоголиз (1), щелочной или кислотный гидролиз (2,3) и аминолиз (4,5). Синтез ПВС через реакцию полиальдольной конденсации из ацетальдегида до настоящего времени оканчивался получением низкомолекулярного полимера. Из всего массива литературных данных, посвященных разработке методов синтеза ПВС, можно выделить пять основных направлений:
- Алкоголиз сложных поливиниловых эфиров в среде осушенных низших алифатических спиртов (C1-C3), в частности метанола, в присутствии гидроксидов щелочных металлов. Процесс щелочного алкоголиза сопровождается гелеобразованием.
- Алкоголиз в присутствии кислот. Количество заявленных работ для этого способа намного меньше, чем для щелочного омыления. Процесс кислотного алкоголиза, так же как и в случае омыления ПВА по механизму реакции щелочного алкоголиза, сопровождается гелеобразованием.
- Щелочной алкоголиз и гидролиз в смеси низших алифатических спиртов с другими растворителями (диоксан, вода, ацетон, бензин или сложные эфиры). При использовании смесей, компонентом которых является вода, практически во всех случаях ее концентрация не превышает 10 % и омыление сопровождается образованием геля.
- Получения ПВС по механизму реакции гидролиза в присутствии кислотных или щелочных агентов, где в качестве реакционной среды выступает вода.
- Разработка специального аппаратурного оформления, позволяющего решить технологические проблемы, связанные с гелеобразованием в процессе омыления ПВА.
Основным и главным недостатком используемых технологий является образование жесткого геля в полном объеме реакционного аппарата при достижении конверсии порядка 50 % и неполная степень гидролиза ПВА. Технологическое решение данной проблемы заключается в разбавлении реакционной системы или использованию поточной схемы получения ПВС, увеличению времени синтеза, нагрев. Однако это приводит повышенному потреблению растворителя и, соответственно, необходимости его регенерации после синтеза, а нагрев в присутствии омыляющего агента к деструкции полимера. Другим способом является использование мешалок специальной конструкции (снабженных лезвиями) для измельчения геля, однако это использование специальных реакторов или мешалок удорожает конечную себестоимость ПВС. Кроме того, вышеуказанные методы используются для получения широкого спектра сополимеров поливинилацетат-поливиниловый спирт.
Щелочной алкоголиз сложных виниловых эфиров
Наиболее распространенным является алкоголиз сложных виниловых эфиров в среде осушенных низших алифатических спиртов (C1-C3), в частности метанола, в присутствии гидроксидов щелочных металлов. В качестве щелочных агентов наибольшее распространение получили гидроксид, метилат, этилат и пропилат натрия и калия. Считается, что обязательным условием проведения алкоголиза является тщательная осушка спирта [1,2,3].
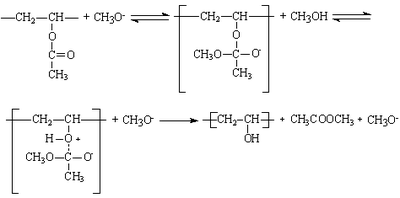
Процессы алкоголиза можно разделить по признаку гомогенности (добавление щелочи к гомогенному раствору ПВА) или гетерогенности (добавление щелочи к дисперсии ПВА) исходной системы. Процесс щелочного алкоголиза, сопровождается гелеобразованием. Известен способ омыления водных дисперсий ПВА водными растворами щелочей, которые можно провести в одну стадию. Щелочной гидролиз дисперсии ПВА с молекулярной массой 1·106 — 2·106 в этом случае проводят при температуре 0 — 20°С в течение 2 — 5 часов.
Щелочной алкоголиз в неспиртовых средах
В связи с тем, что гелеобразование затрудняет проведение процесса омыления ПВА, предпринимались попытки решить эту проблему путем изменения условий процесса. Так, в целях уменьшения плотности гелеобразной массы, в реакционную среду вводят: «…органическое соединение, которое имеет меньшее, в сравнении с метанолом, термодинамическое сродство к ПВС» [1]. В качестве осадителей сополимеров ВС и ВА предложены эфиры многоатомных спиртов и жирных кислот [5], метилацетат (MeAc) [6], алифатические углеводороды [7]. Введение в реакционную среду до 40 % метилацетата дает возможность снизить степень омыления ПВА в момент фазового перехода с 60 % до 35 % [3, стр.85]. Снижение вязкости реакционной массы в момент гелеобразования может быть достигнуто также введением ПАВ [8], например: ОП-7, ОП-10 или проксанолов. В литературе имеются сведения о том, что в качестве реакционной среды могут быть использованы не только спирты, но также смеси с диоксаном и тетрагидрофураном (ТГФ), которые являются хорошими растворителями для сложных поливиниловых эфиров. В работе [9] описан процесс омыления, который позволяет получать высокомолекулярный ПВС с низким содержанием остаточных ацетатных групп при использовании в качестве среды ТГФ. Данное изобретение было применено для омыления поливинилпивалата, с целью получения синдиотактического ПВС. При этом в примерах не приводится указаний о возможном омылении ПВА. Имеются указания [1, стр 215] на использование в качестве реакционной среды диоксана.
Омыление по механизму аминолиза
Необходимо отметить работы российских исследователей, в частности, С. Н. Ушакова с сотрудниками, которые посвящены разработке новых способов получения ПВС. Предложен способ омыления ПВА в среде моноэтаноламина, этанола или смеси этанол-моноэтаноламин [10] под действием моноэтаноламина, применяемого в качестве омыляющего агента. Полученный данным способом ПВС содержит менее 1 % остаточных ацетатных групп и получается в виде тонкодисперсного порошка. Аналогично, в заявке [11] предлагается проводить гетерогенное омыление бисерного ПВА в метаноле под действием смеси моно-, ди-,триэтаноламинов или аммиака с образованием дисперсии ПВС.
Кислотный алкоголиз сложных виниловых эфиров
ПВА и другие сложные поливиниловые эфиры могут быть омылены по механизму алкоголиза в присутствии кислот [12].
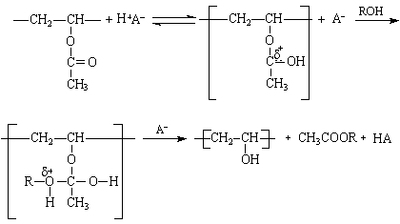
Наибольшее применение получили кислоты: серная, соляная и хлорная. Однако, при использовании серной кислоты в качестве катализатора, часть гидроксильных групп ПВС этерифицируется серной кислотой с образованием сернокислого эфира, который является причиной термической нестабильности ПВС. Применение соляной кислоты обычно приводит к получению окрашенного ПВС. Хлорная кислота в условиях омыления не образует эфиры с ПВС, но ее применение затруднено в связи с нестабильностью и склонностью к разложению со взрывом [1]. Кислотное омыление ПВА осуществляется в спиртовом растворе (метилового или этилового спирта). Применяется как 96%-й этиловый спирт, так и безводный этиловый или метиловый спирт, при этом необходимо отметить, что метанолу отдают предпочтение. «Кислотное» омыление ПВА может быть выполнено и в водной среде без добавки органического растворителя [13,14] .
Разработка специального аппаратурного оформления процессов омыления
Как отмечалось выше, гелеобразование в процессе синтеза ПВС создает серьёзные технологические проблемы, связанные с перемешиванием и выделением полимера. Для решения этой проблемы предложено проводить процесс омыления в реакторах, снабженных мешалками особой конструкции [15,16] или в экструдерах [17] при 20-250С. Омыление в таких реакторах проводится по одной схеме: алкоголиз бисерного ПВА в спиртовом растворе омыляющего агента. Заявленные патенты отличаются модификацией аппаратуры и тем, что при омылении варьируется число оборотов мешалки/шнека, геометрия реактора и мешалки/шнека. Во всех случаях авторы констатируют, что ПВС, полученный по такой технологии, представляет собой белый порошок с низким содержанием остаточных ацетатных групп. Однако следует заметить, что гелеобразование при омылении не может исключить ни одно перемешивающее устройство. Большинство способов получения ПВС являются периодическими, однако существует достаточное число патентов посвященных непрерывной технологии омыления ПВА. Одна из подобных технологий была разработана в НПО «Пластполимер» (г. С.-Петербург) [3, стр.83].
Технология получения ПВС в системе метанол-бензин
Для решения технологических трудностей, связанных с гелеобразованием на промежуточных стадиях омыления ПВА, предложен подход, связанный с введением в реакционную систему в качестве осадителя бензина [3, стр. 84]. При добавлении бензина к метанольному раствору ПВА, содержащему обычно до 1%-масс. воды, образуется гетерогенная система. В зависимости от количества бензина, добавляемого в омыляющую ванну, реакция щелочного алкоголиза ПВА может начинаться в гомогенной или гетерогенной системе. При введении более 30 % бензина от массы всей жидкой фазы в метанольный раствор ПВА образуется неустойчивая эмульсия. При увеличении содержания бензина в омыляющей ванне сокращается длительность реакции до начала гелеобразования и снижается степень омыления выделяющегося полимера. Увеличение содержания бензина до 45%-масс. приводит к образованию крупнозернистого порошка. При введении бензина в омыляющую ванну скорость реакции щелочного алкоголиза ПВА увеличивается, особенно после разделения раствора на две несмешивающиеся фазы. По мнению авторов [3] ускорение реакции может быть вызвано уменьшением степени сольватации ацетатных групп ПВА метанолом вприсутствии бензина. Предлагаемый авторами способ омыления ПВА дает преимущество в технологии получения полимера (особенно на стадии сушки), содержащего более 25 % (мол.) ацетатных групп, а также низкомолекулярных сополимеров BC и BA. Оно заключается в том, что на стадии сушки происходит обогащение жидкой фазы бензином, и частицы сополимера оказываются в среде осадителя, что предотвращает слипание частиц и приводит к образованию сыпучих порошков.
Альтернативные способы получения ПВС
Перспективным и многообещающим способом получения ПВС может являться разработка получения ПВС из ВС. Однако настоящий уровень развития науки и техники не позволяет сдвинуть равновесие в сторону образования ВС в паре «ВС-Ацетальдегид». Поэтому слово «альтернативный» употребляется в контексте разработки способа, который уменьшает или исключает недостатки предыдущих методов синтеза. С 1924 года до 2002 года было придумано и воплощено много различных способов получения ПВС, однако главным неразрешимым, и основным, недостатком процесса являлось гелеобразование на стадии омыления. Именно этот недостаток приводит к необходимости разработки нового аппаратурного оформления или применения различных технологических новшеств. Решение проблемы гелеобразования обсуждалось выше.
Безгелевый способ получения поливинилового спирта
В 2002 года в научной группе Института Синтетических Полимерных Материалов им. Ениколопова (ИСПМ РАН, Москва) под руководством Бойко Виктора Викторовича был разработан [23] и запатентован [20-22] новый, высокоэффективный способ омыления ПВА. Особенностями данного способа являются:
- Высокая производительность
- Низкие энергозатраты
- Малое время синтеза
- Отсутствие гелеобразования
- Возможность проведения процесса в высококонцентрированных системах
- Получены впервые аморфизованные образцы ПВС со степенью кристалличности не более 5%
- Способ пригоден для омылении высокомолекулярного ПВА без резкого снижения молекулярной массы полимера
В основе способа открытого Бойко В.В лежит анализ диаграмм фазового состояния для исходного, промежуточного и конечного продукта в системе «Спирт-Вода». На основании фазовых диаграмм (аналогичных диаграммам для омыления в системе «Бензин-Метанол») были подобраны условия для проведения синтеза не только в безгелевом режиме (получение товарного полимера в виде порошка), но также в полностью гомогенном режиме (получение готового прядильного раствора). Главным отличием данного процесса является проведение синтеза в области спинодального распада (классические методики основаны на проведении синтеза в области бинодального распада). При таком режиме, скорость роста образовавшихся частиц новой полимерной фазы превышает скорость образования новых частиц, что приводит, в свою очередь, к образованию в реакционном объеме не пространственной сетки с узлами в частицах (центры кристаллизации), а единичных частиц. Растворитель используемый в синтезе служит так же и пластификатором для образующегося ПВС. Степень кристалличности такого ПВС может искусственно варьироваться от 5 до 75% [23]. Данный способ безусловно является новым и революционным.
Структура и свойства
Химическая структура
В связи с тем, что исходный полимер (поливинилацетат) для получения поливиниловго спирта получают реакцией полимеризации по типу «голова к хвосту», то и полученный ПВС имеет подобное строение. Общее число мономерных звеньев присоединенных по типу «голова к голове» находится на уровне 1-2 % и полностью зависит от их содержания в исходом поливинилацетате. Звенья присоединенные по типу «голова к голове» оказывают большое значение на физические свойства полимера, а также на его растворимость в воде. Как правило, ПВС является слаборазветвленным полимером. Разветвленность обусловлена реакцией передачи цепи на стадии получения поливинилацетата. Центры разветвленности являются наиболее слабыми местами полимерной цепи и именно по ним происходит разрыв цепи при реакции омыления и, как следствие, уменьшение молекулярной массы полимера. Степень полимеризации ПВС составляет 500—2500 и не совпадает с степенью полимеризации исходного ПВА.
Степень гидролиза ПВС зависит от будущего его применения и лежит в области 70 — 100-моль%. В зависимости от условий и типа частичного омыления, остаточные ацетатные группы могут быть расположены по цепи полимера статистически или в виде блоков. Распределение остаточных ацетатных групп влияет на такие важные характеристики полимера как температура плавления, поверхностное натяжение водных растворов или защитных коллоидов и температура стеклования.
Поливиниловый спирт, полученный из поливинилацетата, является тактическим полимером. Кристалличность ПВС обусловлена наличием большого числа гидроксильных групп в полимере. На кристалличность полимера оказывают так же влияние предыстория получения полимера, разветвленность, степень гидролиза и тип распределения остаточных ацетатных групп. Чем выше степень гидролиза, тем выше кристалличность образца ПВС. При термической обработке полностью омыленного продукта его кристалличность повышается и приводит к снижению его растворимости в воде. Чем выше число остаточных ацетатных групп в ПВС, тем меньше образование кристаллических зон. Исключением для растворимости является ПВС полученный по методике Бойко В.В. Ввиду малой исходной кристалличности, полимер (не зависимо от молекулярной массы) превосходно растворяется в воде [23].
Физические свойства
Поливиниловый спирт является превосходным эмульгирующим, адгезионным и пленкообразующим полимером. Он обладает высокой прочностью на разрыв и гибкостью. Эти свойства зависят от влажности воздуха, так как полимер адсорбирует влагу. Вода действует на полимер как пластификатор. При большой влажности у ПВС уменьшается прочность на разрыв, но увеличивается эластичность. Температура плавления находится в области 230 °C (в среде азота), а температура стеклования 85 °C для полностью гидролизованной формы. На воздухе при 220 °C ПВС небратимо разлагается с выделением СO, CO2, уксусной кислоты и изменением цвета полимера с белого на темно-коричневый. Температура стеклования и температура плавления зависят от молекулярной массы полимера и его тактичности. Так, для синдиотактического ПВС температура плавления лежит в области 280 °C, а температура стеклования для сополимера ПВС-ПВА с содержанием звеньев ПВА 50-моль% находится ниже 20 °C. Аморфизованный ПВС полученный по методике Бойко В.В не имеет характерной эндотермической области отвечающей за плавление кристаллической фазы, однако его термическое разложение идентично ПВС полученному классическим способом [23].
Химические свойства
Поливиниловый спирт стабилен в отношении масел, жиров и органических растворителей.
Применение
- Сгуститель и адгезионный материал в шампунях, клеях, латексах
- Барьерный слой для СО2 в бутылках из ПЭТФ (полиэтилентерефталат)
- Составная часть продуктов гигиены для женщин и по уходу за детьми
- Продукт для создания защитного слоя шлихты в производстве искусственных волокон
- В пищевой промышленности в качестве эмульгатора
- Водорастворимые пленки в процессе изготовления упаковочных материалов
- Иммобилизация клеток и энзимов в микробиологии
- Производство поливинилбутиралей
- В растворах для глазных капель и контактных линз в качестве лубриканта
- При нехирургическом лечении онкологических заболеваний — в качестве эмболизирующего агента
- В качестве поверхностно-активного веществаа для получения капсулированных наночастиц
Торговые марки поливинилового спирта Alcotex®, Elvanol®, Gelvatol®, Gohsenol®, Lemol®, Mowiol®, Rhodoviol® и Polyviol®.
Источники
- Ушаков С.Н «Поливиниловый спирт и его производные» М.-Л.; Изд-во АН СССР, 1960, т.1,2.
- «Polyvinyl alcohol, Properties and Application» // J. Wiley: London — NY — Sydney — Toronto, 1973.
- Розенберг М. Э. «Полимеры на основе поливинилацетата» — Л.; Химия ленинградское отделение, 1983.
- Finch C.A. «Polyvinyl Alcohol — Developments», Wiley, John and Sons, Incorporated, 1992.
- Авт. свид. СССР 267901
- Авт. свид. СССР 211091
- Авт. свид. СССР 711045
- Пат. США 6162864, 2000 Polyvinyl alcohol
- Авт.свид. СССР 141302
- Авт.свид. СССР 143552
- Пат. США 2513488, 1950 Methanolysis of polyvinyl esters
- Пат. Франции 951160, 1949
- Пат. США 2668810, 1951 Process for the saponification of polyvinyl esters
- Пат. Германии 3000750, 1986.
- Пат. Германии 19602901, 1997.
- Пат. США 3072624, 1959 Saponification process for preparation of polyvinyl alcohol
- Lee S., Sakurada I., “Die reactionskinetik der Fadenmoleküle in Lösung. I. Alkalische Verseifung des Polyvinylacetates”, Z.physic.Chem., 1939 vol. 184A, p. 268
- «Энциклопедия полимеров» — М.; Советская энциклопедия, 1972. т.1-3.
- Линдерман М. «Полимеризация виниловых мономеров» — М.; Химия, 1973.
- Авт.свидетельство России RU12265617
- Авт.свидетельство России RU22234518
- Авт.свидетельство России RU32205191
- Бойко Виктор Викторович. Синтез поливинилового спирта в водно-спиртовых средах : Дис. … канд. хим. наук : 02.00.06 : Москва, 2004 112 c. РГБ ОД, 61:04-2/321
Ссылки
малоразветвленный высокомолекулярный поливинилацетат, способ его получения и поливиниловый спирт на его основе — патент РФ 2265617
Изобретение относится к малоразветвленному высокомолекулярному поливинилацетату, способу его получения, а также поливиниловому спирту, полученному на его основе. Описывается малоразветвленный высокомолекулярный поливинилацетат, полученный водно-эмульсионной полимеризацией винилацетата в присутствии эмульгатора и инициатора, в качестве инициатора используют комплексы алкилкобальта(III) с тридентатными лигандами общей формулы I в количестве 0,04-0,2 мас.ч., и процесс полимеризации проводят при температуре 10-40°С и рН 3,5-8. Полученный по такому способу поливинилацетат обладает молеклярной массой не менее 850000 и степенью разветвлённости 0,39-0,7. Омыления указанного малоразветвлённого поливинилацетата получают поливиниловый спирт со степенью полимеризации не менее 6000 и степенью омыления 98- 99,9 %, пригодный для изготовления высокомодульных волокон. 3 н.п. ф-лы, 3 табл.
Изобретение касается малоразветвленного высокомолекулярного поливинилацетата, способа его получения и поливинилового спирта, из которого изготавливают высокопрочные волокна, полученного из этого поливинилацетата.
Одна из сфер применения поливинилацетата (ПВА) — получение из него высокомолекулярного поливинилового спирта, из которого изготавливают сверхпрочные высокомодульные волокна. Для этой цели, как известно, необходим ПВА с высокой молекулярной массой (патенты US 5310790, US 5403905). Такая молекулярная масса трудно достижима из-за высокого значения константы передачи цепи. Так, например, в реакциях передачи цепи на мономер активность винилацетата (ВА) в 3-4 раза выше, чем стирола, а при передаче цепи на полимер — в 50 раз. Это приводит к образованию разветвленного поливинилацетата, не пригодного для получения высокомолекулярного поливинилового спирта (ПВС), предназначенного для изготовления высокомодульных волокон (ПВС).
ПВА получают путем радикальной полимеризации ВА в массе, растворе, эмульсии или суспензии. Однако полимеризация ВА в массе и растворе трудно управляема, поэтому в основном ПВА получают в эмульсии или суспензии.
Известен способ получения высокомолекулярного ПВА блочной или суспензионной полимеризацией ВА в присутствии инициатора радикального типа (А.С. СССР №507590, 1976 г.). Процесс проводят при постепенном введении мономера в реакционную зону по ходу процесса и в качестве инициатора используют олигоперекись алканоил—замещенного алканоила общей формулы [-С-(СН2)n-С-O-O-С-СН-(СН 2)m-С-O-O-]k, где n=4-12, m=3-12, n+m>9, k=6-28, х=Н, СН3, С2Н5 , Br, Cl или I.
Недостатком этого метода являются технологические трудности, связанные с проведением синтеза, высокая температура процесса (72°С) (полимеризацию проводят при кипении реакционной смеси). Кроме того, получаемый ПВА обладает высокой степенью разветвленности (2,0-4,5), что плохо сказывается на физико-химических свойствах ПВС, полученного на его основе.
Известен способ получения неразветвленного поливинилацетата (А.С. СССР №712823, 1980 г.). Полимеризацию проводят в массе в присутствии триэтилборана, инициатор применяют в количестве 0,019-0,296% от веса мономера. Недостатком этого способа является низкая молекулярная масса ПВА (ММ<540000), а также то, что полимеризация в массе трудно управляема.
Наиболее близким к данному изобретению по технической сущности и достигаемому результату является способ получения высокомолекулярного ПВА водно-суспензионной полимеризацией в присутствии перекисных инициаторов и ПВА, полученный этим способом (А.С. СССР №704946, 1979 г.). В качестве инициаторов здесь используют полимерные перекиси двухосновных алифатических кислот общей формулы:
[-C-(CH2)m-C-O-O-]n m=5-16, n=5-40
или перекиси тетрацилов общей формулы
R-C-O-O-C-(CH 2)4-C-O-O-C-R, где R=СН3, С 2Н5, С3Н7, С6 Н13, С10H21.
Недостатками этого способа также является высокая температура процесса (60-70°С) и высокая разветвленность получающегося ПВА (=2,4-3,4), что, как указывалось выше, плохо сказывается на свойствах получаемого ПВС, а именно не позволяет его использовать для изготовления высокомодульных волокон.
Задачей данного изобретения является разработать способ получения малоразветвленного высокомолекулярного поливинилацетата, а также получить из него высокомолекулярный поливиниловый спирт для изготовления высокомодульных волокон.
Указанный технический результат достигается тем, что в способе получения ПВА водно-эмульсионной полимеризацией винилацетата в присутствии эмульгатора и инициатора, в качестве инициатора используют
комплексы алкилкобальта(III) с тридентатными лигандами общей формулы, где R = алкил от С2 до C16 , в количестве 0,04-0,2 мас.ч., и процесс полимеризации проводят при температуре 10-40°С и рН 3,5-8.
Указанный технический результат достигается также тем, что получаемый малоразветвленный высокомолекулярный ПВА имеет молекулярную массу не менее 850000 и степень разветвленности 0,39-0,7, что позволяет его использовать для получения ПВС, пригодного для изготовления высокомодульных волокон.
Кроме того, технический результат достигается тем, что получаемый омылением ПВА ПВС пригоден для изготовления высокомодульных волокон и имеет степень полимеризации не менее 6000 и степень омыления 98-99,9%.
Сопоставительный анализ с прототипом позволяет сделать вывод о том, что при проведении эмульсионной полимеризации винилацетата использован новый тип инициатора — комплексы алкилкобальта(III) с тридентатными лигандами. Таким образом, заявляемое техническое решение соответствует критерию «новизна».
Анализ известных технических решений показал, что использование комплексов алкилкобальта(III) с тридентатными лигандами в качестве инициаторов эмульсионной полимеризации ВА позволяет проводить процесс в экономически выгодных и технологически удобных условиях, при невысоких температурах и в одну стадию, без добавок компонентов по ходу процесса. Также неожиданным образом оказалось, что в присутствии комплексов алкилкобальта(III) с тридентатными лигандами удается получить малоразветвленный высокомолекулярный ПВА. Таким образом, заявляемое техническое решение соответствует критерию «существенные отличия».
Указанные комплексы — алкил{2-[(2-аминоэтил)имино]-пент-3-ен-4-олят}(1,2-этандиамин)кобальт(III) бромиды (символическая формула [RCo(acacen)(en)]Br) — синтезированы авторами по нижеприведенной методике (пример — R=Et).
Синтез проводят в атмосфере аргона при температуре 15-25°С при постоянном перемешивании. В реактор последовательно вводят 430 мл метанола, 12,3 мл (120 ммолей) ацетилацетона, 10,3 мл 70%-ного водного раствора этилендиамина (120 ммолей), 14,1 г (60 ммолей) кобальт(II) хлорида гексагидрата, 19,3 мл 50%-ного водного раствора NaOH, 1 мл 2%-ного раствора PdCl2 в 1 М водном растворе KCl, 21 мл (273 ммоля) этилбромида. Равномерно прикапывают раствор 3,2 г NaBH4 (85 ммолей) в 25 мл 5%-ного водного раствора NaOH в течение 5 часов. После окончания газовыделения реакционную смесь перемешивают в течение 1 часа. Затем ее профильтровывают, раствор упаривают до объема 100 мл при остаточном давлении 10-20 мм рт.ст. и температуре бани не выше 40°С. Затем добавляют 20 г NaBr и при охлаждении 100 мл воды и смесь упаривают таким же образом до объема 100 мл. Кристаллизацию проводят при 0°С, осадок отфильтровывают, промывают 15 мл ледяной воды и сушат на воздухе. Затем его промывают дихлорметаном (всего 150-200 мл) до исчезновения зеленой окраски промывной жидкости. Снова сушат продукт на воздухе. Целевой продукт представляет собой кристаллический порошок красного цвета. При необходимости проводят кристаллизацию из метанола с добавкой бромистого натрия. Для идентификации используют ионообменную ТСХ на SiO2 (пластинки силуфол, эдюент — 0,1 н раствор ацетата натрия в смеси метанол — вода 4:1 по объему). Критерием чистоты является наличие одного пятна на пластинке, а также практически полное обесцвечивание раствора комплекса при добавлении соляной кислоты. Выход и значение фактора разделения Rf приведены в таблице 1.
При синтезе комплексов, указанных в таблице 1, используют следующие галоидные алкилы: этилбромид, н-бутилбромид, изопропилбромид, н-амилбромид, н-октилбромид, н-цетилбромид, циклогексилбромид, втор.-октилбромид.
Структуру комплексов доказывают, исходя из данных 1Н-ЯМР, ИК-спектров и анализа продуктов ацидолиза. Спектры 1H-ЯМР (растворитель — D2 O, 200 МГц, внутренний стандарт — натрий 2,2-диметил-2-силапентан-5-сульфонат) синтезированных комплексов алкилкобальта сходны между собой. Данные для комплекса 1 (табл.1) приведены ниже (идентифицированный сигнал, (м.д.), мультиплетность): СН3СН2Со, 0,60, t; СН3-С=Н, 1,70, s; СН3-СО, 1,94, s; =CH, 4,98, s. ИК-спектры комплексов 1-8 имеют характерные полосы поглощения в области 3100-3350 см-1 (узкие), относящиеся к валентным колебаниям N-H.
Анализ продуктов ацидолиза синтезированных комплексов 1-8, проведенный методами газожидкостной хроматографии, ТСХ и проб на функциональные группы подтверждает вышеприведенную структурную формулу. Состав комплексов подтвержден также данными элементного анализа (табл.2).
Изобретение иллюстрируется примерами, приведенными ниже.
ПВС получают омылением ПВА любым известным способом, например, щелочью в среде, состоящей из этилового, или пропилового, или изопропилового спирта и воды при соотношении спирта к воде от 90:10 до 40:60, при этом количество щелочи составляет от 0,4 до 1 моль на 1 моль звена винилацетата, а омыление проводят в диапазоне температур от 0°С до температуры кипения растворителя. В качестве щелочи может быть использован гидроксид натрия или калия. Омыление ПВА осуществляют до степени конверсии 98,0-99,9%. В случае использования разветвленного ПВА процесс омыления сопровождается отщеплением боковых цепей, и получаемый при этом ПВС имеет низкую молекулярную массу (низкую степень полимеризации).
Пример 1 (по изобретению)
В реакторе с мешалкой смешивают 100 мас.ч. винилацетата с водной фазой, включающей 4 мас.ч. алкилсульфоната натрия (Е-30) с длиной алкильного заместителя С15, 0,1 мас.ч. инициатора — комплекса 1 (табл.1), 0,87 мас.ч. КН2PO4 и 1,24 мас.ч. Na2HPO4 (буферная система) и 200 мас.ч. воды. Процесс проводят при перемешивании в атмосфере азота при температуре 20°С в течение 210 минут до конверсии 93,8%. Характеристическая вязкость раствора полимера в бензоле (при 35°С) 2,16 дл/г, что соответствует молекулярной массе 850000 и степени полимеризации 9880. Из этого ПВА получают ПВС. ПВС получают омылением ПВА щелочью в среде, состоящей из этилового спирта и воды, при соотношении спирта к воде от 80:20, температуре 30°С, количество гидроксида натрия составляет 0,7 моль на 1 моль звена ВА. Степень полимеризации полученного ПВС = 6000, степень омыления — 99%. Степень разветвленности ПВА =0,65.
Примеры 2-10 (по изобретению).
Выполняют аналогично примеру 1, с изменением температуры, рН среды, типа и концентрации эмульгаторов, концентрации ингредиентов, наличием буферных соединений и использованием комплексов алкилкобальта(III) с тридентатными лигандами различной структуры. ПВС получают путем омыления ПВА так же, как в примере 1.
Пример 11 (прототип)
В трехгорлую колбу, снабженную обратным холодильником и мешалкой, помещают 300 мл раствора стабилизатора суспензии (0,1% раствора ПВС), прибавляют 50 мл ВА, в котором растворено 0,312 г (0,67%) полимерной перекиси 1,16-гексадекандикарбоновой кислоты. Суспензионную полимеризацию проводят при температуре 60°С 4 часа, конверсия 94%. Полученный полимер имеет характеристическую вязкость []=2,41 (ацетон, 30°С), молекулярную массу 1187000 и разветвленность =2,9.
Рецепты полимеризации ВА и параметры процесса, а также некоторые свойства полимеров (характеристическая вязкость ПВА, молекулярная масса, степень полимеризации и степень разветвленности, а также степень полимеризации и степень омыления ПВС) приведены в таблице 3.
Получаемый ПВС характеризуют степенью полимеризации и степенью омыления.
Степень полимеризации ПВС рассчитывают по величине характеристической вязкости, определенной в растворе ДМСО при температуре 30°С по формуле: []=kM , где k=1,58·10-4, =0,84 [А.Ф.Николаев и др. Водорастворимые полимеры. — Л.: Химия, Ленинградское отделение, 1979, стр.34].
Определение степени омыления (содержания ацетатных групп) в поливиниловом спирте проводят ацидометрически по ГОСТ 10779-78.
Высокая степень полимеризации ПВС (от 6000) свидетельствует о том, что он может быть использован для получения высокомодульных волокон.
Приведенные в таблице 3 данные свидетельствуют о том, что использование комплексов акилкобальта(III) с тридентатными лигандами при эмульсионной полимеризации винилацетата позволяет получать высокомолекулярный малоразветвленный поливинилацетат, который может служить для производства высокомолекулярного поливинилового спирта и высокомодульных волокон на его основе.
Таблица 1 Структура, выход и некоторые свойства комплексов алкилкобальта. | ||||||||||||||||
№ | R | Выход, % | Rf (TCX) | Tпл., °С | ||||||||||||
1 | Et | 66 | 0,34 | 200 | ||||||||||||
2 | i-Pr | 65 | 190 | |||||||||||||
3 | n-Bu | 64 | 0,40 | 190 | ||||||||||||
4 | n-Am | 60 | 0,40 | 180 | ||||||||||||
5 | cyclo-Hex | 41 | 195 | |||||||||||||
6 | n-Oct | 52 | 0,45 | 160 | ||||||||||||
7 | sex-Oct | 48 | 150 | |||||||||||||
8 | n-Cet | 36 | 0,47 | 120 | ||||||||||||
— плавление с разложением — комплексы втор-алкилкобальта разлагаются в условиях хроматографирования | ||||||||||||||||
Таблица 2 Элементный состав комплексов алкилкобальта | ||||||||||||||||
№ | Со Расч. | Со Найд. | С Расч. | С Найд. | N Расч. | N Найд. | O Расч. | O Найд. | Н Расч. | Н Найд. | Br Расч. | Br Найд. | ||||
1 | 15,97 | 15,92 | 35,79 | 35,93 | 15,18 | 15,22 | 4,34 | 4,30 | 7,05 | 7,00 | 21,66 | 21,71 | ||||
2 | 15,39 | 15,43 | 37,62 | 37,68 | 14,63 | 14,57 | 4,18 | 4,12 | 7,31 | 7,32 | 20,87 | 20,81 | ||||
3 | 14,84 | 14,90 | 39,31 | 39,28 | 14,11 | 14,07 | 4,03 | 4,10 | 7,56 | 7,50 | 20,14 | 20,12 | ||||
4 | 14,34 | 14,40 | 40,90 | 41,00 | 13,63 | 13,57 | 3,89 | 3,92 | 7,79 | 7,75 | 19,45 | 19,41 | ||||
5 | 13,87 | 13,92 | 42,37 | 42,32 | 13,18 | 13,27 | 3,77 | 3,73 | 8,00 | 8,03 | 18,81 | 18,73 | ||||
6 | 13,00 | 13,06 | 45,05 | 45,09 | 12,37 | 12,32 | 3,53 | 3,50 | 8,39 | 8,33 | 17,65 | 17,68 | ||||
7 | 13,00 | 13,06 | 45,05 | 45,09 | 12,37 | 12,31 | 3,53 | 3,52 | 8,39 | 8,34 | 17,65 | 17,67 | ||||
8 | 10,43 | 10,50 | 53,12 | 53,07 | 9,92 | 9,89 | 2,83 | 2,86 | 9,56 | 9,52 | 14,15 | 14,17 |
ФОРМУЛА ИЗОБРЕТЕНИЯ
1. Способ получения высокомолекулярного поливинилацетата водно-эмульсионной полимеризацией винилацетата в присутствии эмульгатора и инициатора, отличающийся тем, что в качестве инициатора используют комплексы алкилкобальта (III) с тридентатными лигандами общей формулы
где R — алкил от С2 до C16,
в количестве 0,04-0,2 мас.ч. и процесс полимеризации проводят при температуре 10-40°С и рН 3,5-8.
2. Малоразветвленный высокомолекулярный поливинилацетат с молекулярной массой не менее 850000 и степенью разветвленности 0,39-0,7, пригодный для синтеза поливинилового спирта, используемого для изготовления высокомодульных волокон, полученный способом по п.1.
3. Поливиниловый спирт для изготовления высокомодульных волокон со степенью полимеризации не менее 6000 и степенью омыления 98-99,9%, полученный путем омыления малоразветвленного высокомолекулярного поливинилацетата по п.2.