Состав силикатного кирпича, из чего состоит и сделан силикатный кирпич
Определяется состав силикатного кирпича по ГОСТу 379-95, в соответствии с которым в нужной пропорции в процессе производства добавляются необходимые ингредиенты. Изделие изготавливается из природных, экологических чистых компонентов, что делает его незаменимым в жилом строительстве.
Основные компоненты силикатного кирпича
Используются для изготовления продукта следующие материалы:
- кварцевый песок (очищенный) – изделие состоит из этого ингредиента на 95%. Материал добывается карьерным способом и подвергается тщательному дроблению и последующей очистке. Последняя стадия измельчения осуществляется непосредственно на производстве;
- воздушная взвесь – содержится в составе материала в количестве 8% от общей массы. Используемая взвесь обладает нужными характеристиками и требуемым химическим составом. Основным условием является ограниченное содержание MgO, которого не должно быть более 5%. Обязательно необходимо равномерное гашение;
- вода – обязательно в состав силикатного кирпича входит жидкость в количестве 7% от общей массы.
Процентное содержание отдельных компонентов может изменяться. Определяется этот фактор технологией производства, используемой для изготовления изделия. Например, чтобы придать материалу дополнительные качества, основная смесь может дополняться химическими, минеральными ингредиентами.
Из чего сделан силикатный кирпич?
Структура основных компонентов материала
Детально рассмотрим, из чего состоит силикатный кирпич, изучив составляющие кварцевого песка и воздушной взвеси. Преимущественно кварцевый песок состоит из кремнезёма, но также в нём присутствует глинозём.
Помимо этого имеются следующие химические соединения:
Это интересно:
Как отремонтировать фундамент кирпичного дома своими руками?
Инструкция, как правильно обложить банную железную печь кирпичом.
Как выполняется декоративная обкладка дома облицовочным кирпичом?
Очень редко случается, что в составе песка обнаруживается двуокись титана. Связующим компонентом является известь, состоящая из нескольких ингредиентов, таких как углекислый кальций, магний, а также глинистых примесей, а именно кремнезёма и глинозёма. Зная, из чего сделан силикатный кирпич, можно точно определить, как он будет реагировать на внешнюю среду, а также каковы будут его основные характеристики. Технология производства строительного материала, давно отработана и широко применяется на практике. Необходимо строго соблюдать технологический процесс, так как от этого зависят эксплуатационные характеристики.
Кирпич силикатный полнотелый
Несмотря на многообразие строительных материалов, при строительстве дома наиболее популярным и востребованным остается силикатный кирпич. Форма и структура такого строительного материала весьма разнообразна, что позволяет возводить не однотипные коробки для проживания, а уникальные по своей красоте архитектурные сооружения.
В случае, когда требуется повысить прочность здания, используют силикатный полнотелый кирпич.
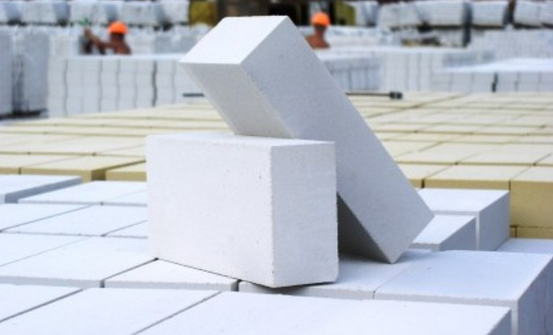
Что такое силикатный кирпич (СК)
Данный вид строительного материала представляет собой элемент, прямоугольной формы, который изготовлен из извести и кварцевого песка. СК отличается особой прочностью, и точной геометрической формой. Именно этот показатель обеспечивает плотность стыков, а также позволяет обеспечить правильные формы и контуры фасада.
На практике СК используется сравнительно недавно. Технология его производства была запатентована сравнительно буквально сто лет назад, однако, этого времени было достаточно, чтобы теория о высокой прочности такого строительного материала подтвердилась на практике.
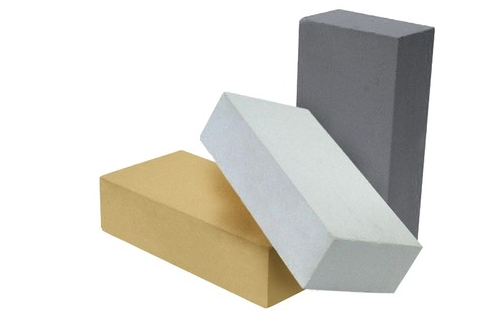
Положительные характеристики полнотелого СК
Сырье, используемое при производстве полнотелого силикатного кирпича, придает ему следующие положительные характеристики:
- Высокий показатель прочности. Силикатный полнотелый кирпич выдерживает нагрузки давлением до 30 МПа. Также полнотелый силикатный кирпич очень устойчив на изгиб. Это объясняет хорошую устойчивость к усадке строений. Стены из такого строительного материала практически не реагируют на движение грунта, и не покрываются трещинами.
- Хорошая устойчивость к появлению грибков и плесени. Это обусловлено тем, что известь, находящаяся в составе СК, сама по себе обладает высокими антисептическими качествами.
- Правильная геометрия возведенных стен. Четкие линии материала существенно облегчают процесс его укладки, а также сводит к минимуму количество пустот между швами.
- Абсолютная безопасность для жизни и здоровья человека.
- СК не горят, и не поддерживают процесса горения. Единственное что нужно помнить: при температуре нагрева свыше 500°С, элемент сохранят форму, но абсолютно теряет свою прочность.
- Доступная цена материала позволяет его активно использовать, независимо от величины бюджета стройки.
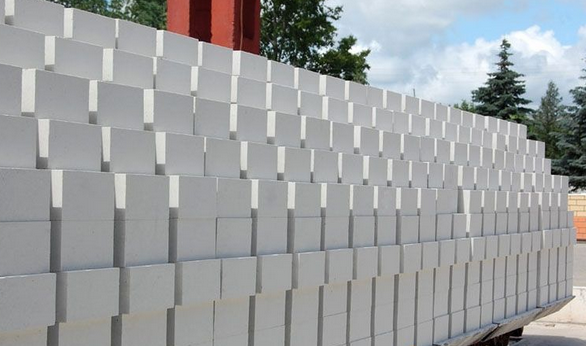
Отрицательные моменты в использовании СК
Недостатки накладывают некоторый отпечаток, на эксплуатацию сооружений выполненный из СК, и этот факт нужно учитывать еще на стадии планирования и закладки дома:
- Высокий показатель поглощения влаги. Пожалуй, это основной недостаток использования СК. Это приводит к тому, что возрастает риск разрушений при длительном воздействии морозов. Замершая влага, находясь внутри силикатного полнотелого кирпича, очень легко распирает его и разрушает. Из СК лучше не строить подвалы, гаражи или цокольные этажи.
- Низкая морозостойкость. Технология производства СК предусматривает использование его в южных регионах и областях средней полосы.
- Низкий показатель сохранности тепла. Стены, возведенные из силикатного полнотелого кирпича, нуждаются в хорошем утеплении. Возводить стены из такого материала очень большой толщины невыгодно экономически.
- Основные цвета полнотелого кирпича – белый и оттенки бежевого. Маленькая палитра материала ограничивает выбор дизайнерских проектов для отделки дома.
Рассмотрим более детально основные параметры СК согласно техническим нормам.
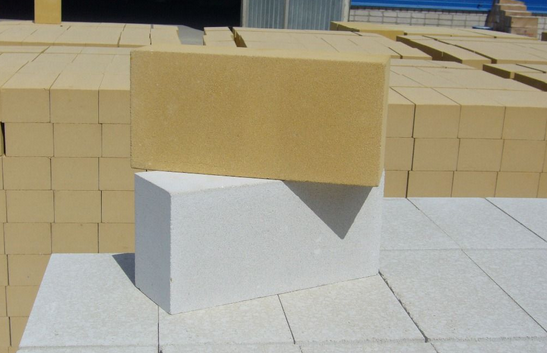
Состав и размеры
Нормы, указанные в государственной документации, гласят, что стандартные размеры одинарного полнотелого силикатного кирпича составляют: длина – 25 см, ширина — 12 см, толщина — 6,5 см. Вес отдельного элемента зависит от того полнотелый элемент или нет.
Полуторный полнотелый силикатный кирпич имеет несколько большую толщину. При стандартной ширине и длине вес полуторного полнотелого силикатного кирпича составляет порядка 8,8 см. Двойной силикатный кирпич имеет толщину 13,8 см.
Заводы по производству СК располагаются в основном возле песчаных месторождений. Это связано в первую очередь с тем, что основной элемент в составе СК – песок. Зернистость и форма песка, очень важные параметры для придания формы уже готовому раствору и обеспечению особой прочности материалу.
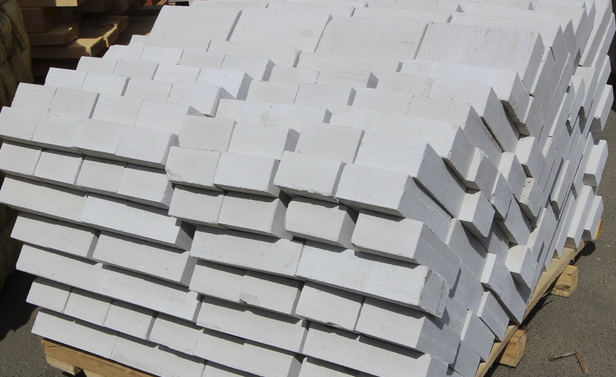
В производстве размер гранул песка играет ключевую роль. Так, например, соединяя три фракции песка в неравном соотношении (4:2:1) можно получить материал высокой пористости. Если параметры изменить до 162:16:1, то кирпич получится максимально плотным и прочным.
Перед тем как песок поступит в производство, его тщательно просеивают от различных примесей и мусора, которые абсолютно не допустимы в готовой продукции.
Еще одним немаловажным компонентом СК является известь. Они играют роль вяжущего элемента. На производстве используется, как правило, негашеная известь.
Внимание! Производство СК невозможно без использования воды. Она присутствует на всех этапах производства: формирование смеси, запаривании сырого материала, производстве технологического пара.
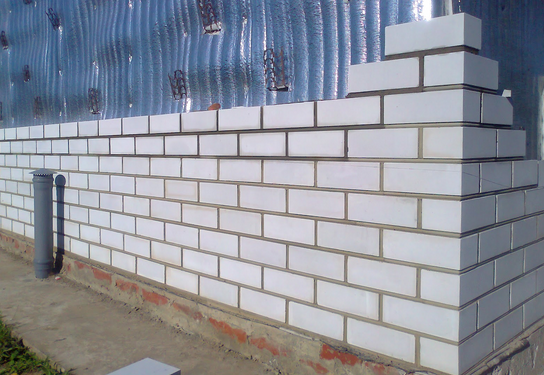
Основные технические характеристики СК
ГОСТ контролирует следующие параметры полнотелого силикатного кирпича:
- Прочность. Производитель СК выпускает продукцию многих марок, от М 75 до М 300. Если из СК выкладываются внутренние стены, то марка не имеет определенного значения. Но если речь идет о выкладке силикатным полнотелым кирпичом фасада здания, то лучше остановить свой выбор на марке М125.
- Устойчивость к морозам. В зависимости от класса изделия кладка может выдерживать от 25 до 50 периодов замораживания и размораживания. Данная маркировка обязательно указывается производителем.
- Показатель теплопроводности является обязательным при расчетах необходимой толщины стен.
- Устойчивость к огню. Определяется компонентами, которые входят в состав силикатного кирпича.
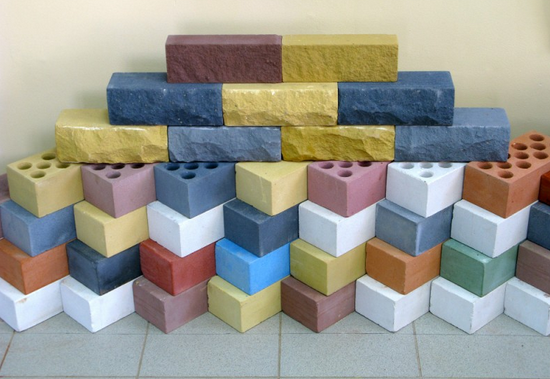
Состав и структура
Для любой марки силикатного полнотелого кирпича первоначальный состав ингредиентов один и тот же. Что касаемо структуры материала, то она может отличаться, что непосредственно сказывается на эксплуатационных свойствах изделия.
Полнотелый кирпич – это изделие, выполненное монолитным способом. По итогу в элементе нет пустот, даже если при производстве использовалось сырье, обладающее повышенной пористостью. Полнотелый СК очень плотный и прочный. Он не очень хорошо поглощает влагу, имеет самый большой вес и характеризуется самым длительным сроком эксплуатации.
Полнотелые кирпичи могут быть только утолщенного вида, чего нельзя сказать о пустотелых материалах.

Они имеют очень пористую структуру. Он более легкий, лучше поглощает посторонние звуки, хорошо сохраняет тепло. Но большим минусом пустотелых элементов является высокий показатель поглощения воды.
Также есть отличия между облицовочным и строительным силикатным полнотелым кирпичом.
Облицовочный СК должен обладать точной геометрией, одинаковым цветом поверхности и повышенным показателем прочности. В облицовочном силикатном полнотелом кирпиче идеально гладкими должны быть как минимум две стороны.
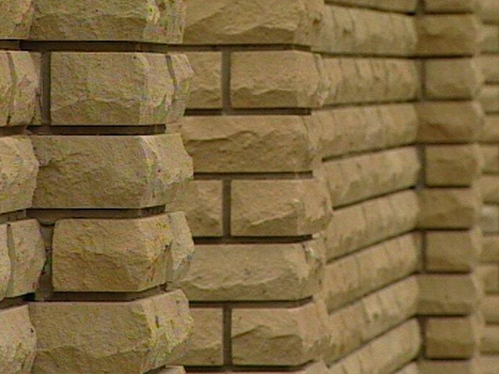
Внимание! Материал для отделки фасада может быть как пустотелым, так и полнотелым. Приятно радует и разнообразие цветовых решений поверхности СК для отделки зданий.
Строительный силикатный полнотелый кирпич используют в основном для возведения внутренних стен дома. Для него снижены требования в гладкости поверхности и четкости контора элемента. Допускаются такие погрешности, как: сколы, ребра и шероховатость поверхности. Такой СК также может быть полнотелым и пустотелым. Окрас материала в основном белый.
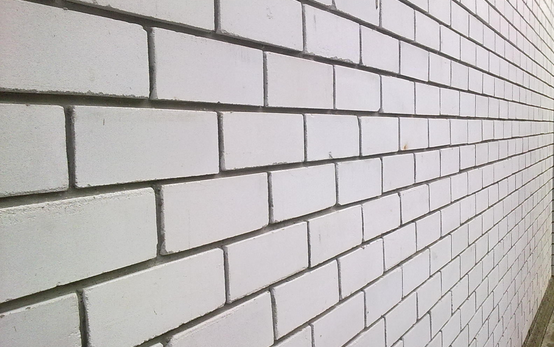
Транспортировка материалов
Так как СК относится к материалу высокой прочности, его можно перевозить в кузове самосвала навалом. Но все же, это относится только к строительному силикатному полнотелому кирпичу, внешний вид которого не играет особой роли.
Материалы для облицовки здания укладывают в специальные поддоны, скрепляют ремнями и упаковывают специальной пленкой. Для транспортировки такого строительного материала используют только длинномерные грузовики, которые загружают при помощи крана.
Внимание! Очень важно подбирать маршрут таким образом, чтобы во время движения не было больших встрясок. Именно от них, качество силикатного полнотелого кирпича для облицовки страдает больше всего.
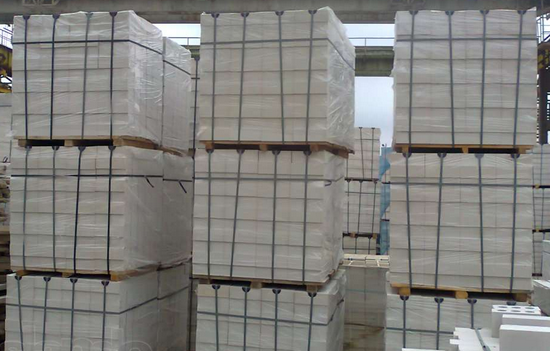
Заключение
Силикатный полнотелый кирпич – это незаменимый материал для строительства частных коттеджей, многоквартирных домов. Исключения составляют только гаражи, подвальные помещения и цокольные этажи.
Дополнительно о том, как изготавливают силикатные кирпичи, узнаем в следующем видео
Из чего делают силикатный кирпич
Кирпич силикатный из чего делаютИзготовление силикатного кирпича интересует многих предпринимателей. Ведь строительные материалы не мало стоят и на них есть постоянный спрос. Поэтому как делают силикатный кирпич мы сегодня и поговорим.
В производстве надо знать всю цепочку и следует сказать, правильная технология довольно важна, ведь без нее не получить качественный продукт. Все можно будет сделать своими руками, но тогда производство будет не большое.
При серийном, надо будет приобретать мощное оборудование. Весь технологический процесс вы сможете просмотреть на видео в этой статье.
Изготовления силикатного кирпича
Для начала надо знать из чего делают силикатный кирпич. Любой производственный процесс начинается с подготовительных операций, связанных с подготовкой сырья.
Основой такой подготовки является получение исходного сырья, которое состоит из входящих в него компонентов, таких, как известь и песок.
Схема производства силикатного кирпича- Процентное содержание извести в составе смеси определяется в зависимости от активности самой извести, которая зависит от количественного содержания в извести окиси кальция.
Внимание: Каждое предприятие может устанавливать свое процентное содержание извести в зависимости от показателей ее активности, но, как правило, эти показатели находятся в пределах 6-8%.
- Если на предприятии используют свежеобожженную известь, то процентное содержание такой извести может быть меньше, если не свежеобожженная и с примесями, то ее может быть больше. В любом случае, недостаток извести в готовой смеси, как и ее избыток, отрицательно влияют на качество готовой продукции. В связи с этим, постоянно проводят лабораторные испытания активности извести перед тем, как ее добавить в силикатную смесь.
- Перед заготовкой смеси, необходимое количество песка отмеривается на весах, а затем, отмеривают нужный объем извести, после чего в смесь добавляется вода. В результате получается пластическая масса, из которой делаются заготовки силикатного кирпича. Вода не только помогает завершить процесс гашения извести, но и позволяет обеспечить нормальное протекание различных процессов на этапе запаривания.
- На этапе заготовки силикатной массы необходим точный контроль количественного состава всех ингредиентов, в том числе и воды. Ее должно быть ровно столько, сколько может обеспечить получение качественного конечного продукта.
Внимание: При недостатке воды не смогут закончиться процессы гашения извести, а при ее избытке силикатная масса будет слишком мягкая и процесс формирования кирпича-сырца будет затруднительным.
- Количество воды, также зависит, насколько влажный песок поступает на производство. Поэтому, влажность песка регулярно проверяют в лабораторных требованиях. Расчет количества воды производят на определенный объем готовой продукции или на 1 метр кубический силикатной смеси. Исходя из расчетов, вода в определенном объеме распределяется следующим образом: 2,5% уходит на процесс гашения извести, 3,5% воды испаряется в процессе гашения, 7% – это естественная влажность готовой массы.
- Силикатный состав может быть приготовлен двумя способами: силосным и барабанным. Силосный способ более простой и более выгоден экономически, так как не требует больших потреблений энергии.
- Известь и песок поступают в мешалку и тщательно перемешиваются с добавлением нужного количества воды, после чего состав выдерживают в течении 4-10часов, для полного гашения извести. В это время в воздух выделяется огромное количество продуктов гашения, что делает не возможным пребывание людей в помещении. Поэтому, процесс разгрузки силоса автоматизирован, чтобы не подвергать обслуживающий персонал опасности.
- После полной готовности и разгрузки силикатной массы, она поступает на процесс прессования. Этот технологический процесс имеет свои особенности, которая напрямую оказывает влияние на качество конечного продукта. При этом, большую роль играет сила давления. Она должна быть такой, чтобы внутри кирпича не было пустот, заполненных воздухом или влагой, а частицы кирпича соединялись между собой лишь за счет вяжущих свойств вещества. Только при таких условиях можно получить максимально качественный продукт.
- Если сила давления окажется слишком резкой, то формования не получится, и заготовка может разрушиться. Исходя из этого, сила давления должна увеличиваться постепенно до величины 150-230кг на 1 см кубический. Не последнюю роль играет влажность готовой силикатной смеси. В процессе прессования ее влажность должна находиться на уровне 7%. Это оптимальная величина влажности и уменьшение или увеличение не желательны.
- Если влажность будет меньше, то трудно будет формовать массу, если показатели влажности будут выше, то эластичность массы будет хуже, и заготовки будут разламываться.
- Прессование – это многоступенчатый технологический процесс, включающий в себя следующие этапы: наполнение пресс-форм силикатной смесью, процесс прессования, выталкивание заготовок из пресс-форм и погрузка их на вагонетки, после чего кирпич-сырец отправляется в пропарочную камеру.
- Кирпич-сырец на выходе должен соответствовать размерам, установленным ГОСТом, иначе он бракуется и отправляется на повторную переработку. Плотность кирпича можно регулировать путем количества силикатной массы, наполняемой пресс-формы. Чтобы получался кирпич одинаковой плотности, необходимо подавать в пресс-формы постоянно одинаковую массу, что делается путем автоматизации данного процесса.
- После прохождения этапа прессования кирпич-сырец загружается в вагонетки и отправляется в автоклав для обработки паром. Этот процесс состоит из трех этапов. Первый этап характеризуется поступлением кирпича в автоклав, где начинается процесс выравнивания температуры пара и температуры кирпича.
- На второй стадии поддерживается температура постоянной определенное время, что позволяет завершить все физико-химические процессы в толще изделия. В этот период происходит процесс выпаривания лишней влаги, а также происходит образование гидросиликата кальция.
Внимание: На втором этапе происходят процессы, обеспечивающие силикатному кирпичу основные прочностные характеристики. Третий этап характеризуется процессом остывания кирпича, после чего его отправляют на склад готовой продукции.
Разновидности силикатного материала
Технология изготовления силикатного кирпича может несколько отличаться, поэтому материал можно разделить и на несколько видов. Существуют такие разновидности кирпичей, как зольный и шлаковый, которые также относятся к группе силикатных.
Итак:
- Шлаковый кирпич производят из домашних шлаков, добавляя к ним различные добавки, а зольный делают из золы. Они имеют несколько иные свойства, характеризующиеся более низкой плотностью и более низкой теплопроводностью. Очень часто используют эти виды кирпича, в силу их меньшей стойкости. К сожалению, они уступают по прочности силикатному кирпичу и их применение ограничивается малоэтажным строительством не выше 3-х этажей. Этот вид кирпичей можно использовать для кладки верхних этажей многоэтажек.
- Существует еще один подвид кирпича, который изготавливается аналогичной технологии, но отличается от него по размерам, но не по составу. Его называют силикатным блоком или камнем.
- Различные специалисты называют его по-разному, хотя технология изготовления практически одинакова. Такое изделие похоже больше на блоки, с размерами 225, 250, 512 на 88-248 мм и на 44-188 мм. Он значительно больше кирпича и тяжелее, вес такого камня может достигать 21кг. Такие блоки изготавливаются пустотелыми, но могут иметь различную фактуру поверхности: могут быть гладкими или рельефными, рядовыми и лицевыми.
- Достоинство таких блоков заключается в том, что они в 4-5 раз уменьшают время на строительство и экономят кладочный раствор, где-то в полтора раза. Что касается основных эксплуатационных характеристик, то они схожие с обычным силикатным кирпичом. Но если сравнить их с другими стройматериалами, то их характеристики несколько лучше, если взять, например, гипсоблоки или бетонные перегородки. Они прочнее и имеют хорошие звукоизолирующие характеристики, при этом, они могут быть дешевле других типов блоков.
Цветовые решения
Как правило, после всех технологических операций силикатный кирпич имеет светлый оттенок, что дает огромные возможности для дизайнерских задумок.
Такому кирпичу можно придать любой оттенок, хотя разноцветного силикатного кирпича никто еще не видел. Дело в том, что в его состав входит известь, которая может вступить в реакцию с красителем, и тогда не известно, какой оттенок получится в конечном итоге. Здесь нужны очень серьезные исследования.
Применение
Можно встретить несколько видов силикатного кирпича, в зависимости от предназначения:
- Для выкладки обычных и несущих стен применяется рядовой силикатный кирпич, а для кладки фасадных поверхностей можно применять лицевой. При этом, производят кирпич с гладкой или фактурной поверхностью, а также кирпич с декоративным покрытием. Такой кирпич применяется для облицовки оконных проемов и решения различных дизайнерских идей.
- Силикатный кирпич имеет ряд недостатков, которые и определяют область его применения. Основной недостаток – это способность поглощать влагу. Поэтому, он не пригоден для проведения строительных и облицовочных работ в помещениях с повышенной влажностью, таких как бассейны, бани, санузлы и т.д.
- Ограничено его применение в условиях, повышенных температур, больших перепадов температур, в условиях действия агрессивных сред, а также агрессивных веществ, находящихся в грунтовых водах. В этой связи, нельзя выкладывать силикатным кирпичом цоколя зданий, фундаменты, возводить печи и камины.
- При использовании силикатного кирпича встает вопрос применения скрепляющих растворов. В данном случае, лучше проконсультироваться с производителем силикатного кирпича, на предмет использования состава растворной смеси, что позволит более качественно осуществлять строительные работы. Не исключено, что простым цементно-песчаным раствором обойтись не удастся.
- В случае применения силикатного кирпича, как основного строительного материала, а керамический кирпич использовать в качестве облицовочного, то следует учесть тот факт, что они имеют различные коэффициенты теплового расширения. Это значит, что нельзя соединять элементы кладки этих кирпичей между собой, так как впоследствии возможно появление трещин. Лучший вариант в таком случае, это обеспечение зазора в 1-2 см между двумя кладками.
Внимание: Если вы делаете жилье из данного материала тогда сразу надо подумать о теплоемкости помещения. Данного материала потребуется гораздо больше по сравнению с глиняным кирпичом. Или придется делать обязательное утепление. Поэтому цена постройки значительно возрастает.
Правила перевозки
Силикатный кирпич не нуждается в особых условиях хранения и перевозки. Главное, чтобы он как можно меньше контактировал с условиями с повышенной влажности, в силу своей гигроскопичности.
Его можно складировать или грузить как вручную, так и с помощью специальной техники.
Итак:
- Как правило, современные предприятия, как государственные, так и частные стремятся автоматизировать все процессы производства силикатного кирпича, в том числе и процессы хранения и упаковки, и транспортировки.
- Готовая продукция укладывается на специальные деревянные поддоны, позволяющие использовать для перемещения и погрузки, автопогрузчики, а сам кирпич пакуется в полиэтиленовую пленку, которая обеспечивает герметичность кирпича, как в процессе хранения, так и в процессе транспортировки.
Внимание: При его складировании на участке следует выбирать возвышенность. Иначе после дождя он набирает много влаги. Так же надо сверху накрыть не промокающими материалами.
Из чего сделан силикатный кирпич вы теперь знаете и теперь имеете об этом не плохое представление. Инструкция поможет вам понять весь объем работ, которые надо будет сделать для производства. Так что посмотрите фото, изучите весь процесс и можете уже думать и от производстве.
Технология производства силикатных кирпичей
Производство силикатного кирпича освоено многими компаниями, чтобы покрыть постоянно растущий спрос на данный стройматериал. Такой кирпич имеет многочисленные достоинства, а внешний вид и характерная правильность форм особо покоряет покупателей. В настоящее время он реализуется в широком ассортименте с декорирующими добавками, что дает возможность выбора. Кроме того, можно освоить технологию изготовления кирпича в домашних условиях, что позволить заняться бизнесом или обеспечить строительство собственного дома.
Особенности материала
Силикатный или белый кирпич (проще, силикат) представляет собой спрессованную и обожженную смесь кварцевого песка с известью. Его основными преимуществами считаются:
- белый, декоративный цвет, что дает возможность получения различных оттенков при добавлении пигмента;
- правильные геометрические формы;
- высокая прочность.
К недостаткам следует отнести достаточно высокую влагопроницаемость, что ограничивает применение такого материала в среде с высокой влажностью или требует использования надежной гидроизоляции. Несмотря на наличие отрицательных качеств, силикат широко применяется при кирпичной кладке стен зданий различного назначения (как жилого, так и производственного фондов), причем достаточно большой этажности.
Технология производства силикатного кирпича не отличается большой сложностью, а потому оно осваивается крупными предприятиями, небольшими фирмами, частными предпринимателями. Можно организовать изготовление белого кирпича и в домашних условиях, своими руками.
Из чего делают рассматриваемый стройматериал? Когда изготавливается силикатный кирпич, состав его в корне отличается от строения обычного, красного. В его структуре не используется глина. Основу состава составляет высококачественный кварцевый песок (до 90-92 %). Связующим веществом выступает известь (8-9 %). Вступая в реакцию с песком, она обеспечивает однородность структуры и высокую прочность. Смесь готовится с добавлением воды, причем она используется на всех производственных стадиях.
В состав силикатного кирпича для придания определенных свойств могут вводиться ингредиенты, способствующие быстрому отвердению смеси, а также пигменты для обеспечения нужной окраски. Чаще всего используется белый кирпич, в котором отсутствуют пигменты.
Технологические процессы
Как делают силикат? В принципе, когда нужен силикатный кирпич, производство его может базироваться на 2 основных способах:
- Смешанная технология изготовления. Она подразумевает подачу сырья на каждый формовочный станок. Такой способ применяется на малых производствах и в домашних условиях.
- Централизованный способ изготовления силикатного кирпича. Сырье поступает по конвейеру в большие смесительные камеры, а затем распределяется по нескольким аппаратам. Естественно, что без такой технологии не могут обойтись крупные предприятия.
В общем случае технологическая схема производства силикатного кирпича включает такие этапы:
- хранение и предварительная подготовка ингредиентов;
- подготовка известкового компонента;
- приготовление смеси;
- гашение извести в смешанном состоянии;
- формование кирпичных элементов;
- изготовление кирпича в автоклаве;
- контроль качества и складирование готовой продукции.
При налаженном промышленном производстве используется следующее оборудование:
- Дробилка щепкового типа для измельчения крупных компонентов.
- Нория или специальный транспортер, обеспечивающий вертикальную подачу сырья и компонентов.
- Силосный аппарат для проведения процесса гашения извести.
- Мельница шарового типа для окончательного (тонкого) измельчения ингредиентов.
- Песчаный силосный аппарат для приготовления смеси.
- Винтовой конвейер для перемещения сыпучих компонентов.
- Дозирующая установка для подачи ингредиентов в непрерывном режиме.
- Смеситель двухвалкового типа, обеспечивающий приготовление смеси.
- Ленточный транспортер — основное оборудование для перемещения смеси и готовой продукции.
- Мост, предназначенный для загрузки сырого полуфабриката в автоклав.
- Пресс гидравлического типа обеспечивает формовку кирпичей.
- Автоклав — основное оборудования для изготовления кирпича под высоким давлением и температурой.
Приготовление сырья
В вопросе, какого качества будет сделан силикатный кирпич, важную роль играет стадия подготовки ингредиентов и смеси. К компонентам предъявляются такие требования:
- Кварцевый песок в основном используется в немолотом виде. Можно применять смесь из крупнозернистого и тонкомолотого песка. Содержание кремнезема в нем должно составлять более 69-72 %.
- Известь во многом определяет свойства готового изделия, а потому она должна быть высокого качества. Основное условие — она должна иметь способность к ускоренному гашению.
- Вода используется на всех стадиях производства: подготовка смеси, гашение извести, при формовке элементов и в процессе тепловой обработки. Она не должна иметь никаких примесей.
Приготовление смеси для формовки кирпича начинается с дозировки ингредиентов, которая должна строго соответствовать выбранной рецептуре. Известь может добавляться в количестве 6,5-9 % по объему. Чем выше качество извести, тем меньше ее потребность в составе. Вода добавляется после смешивания компонентов из расчета следующего расхода: испарение — 3-4 %, на гашение извести — 2,4-2,7 %, на увлажнение смеси — 6,5-7,5 %. Рецептура кирпича оговаривается техническими условиями, принятыми на данном предприятии.
Приготовление песчано-известкового раствора обеспечивается 2 основными способами:
- Барабанный способ. Используется известь после тонкого измельчения. Песок и тонкомолотая известь поступают в специальный бункер с барабаном для перемешивания ингредиентов. В этой же камере производится и гашение извести с добавлением воды. Завершает процесс барабанной подготовки тепловая обработка при вращении в герметичном объеме, которая осуществляется с помощью пара.
- Силосный способ. Подготовка смеси проводится в специальных емкостях цилиндрической формы, которые называются силосами. В них обеспечивается и гашение извести. Весь процесс приготовления сырья занимает 11,5-13 часов, после чего смесь увлажняется и направляется на формовку в пресс.
Процесс формовки кирпича
Приготовленное сырье в виде увлажненной смеси подается в специальные формы, устанавливаемые в гидравлический пресс. Четкость геометрии готового кирпича зависит от давления, которое обеспечивается в формовочной установке. Чем больше мощность пресса и выше развиваемое давление, тем плотнее структура кирпича и выше качество. Остатки воздушных включений и водяных капель негативно сказываются на свойствах готового изделия.
2 важный параметр процесса формовки — скорость приложения давления. При резком сдавливании массы не удастся обеспечить равномерную, качественную структуру кирпича. Хорошее оборудование позволяет регулировать данный параметр. Производственная практика показала, что оптимальное давление в прессе при формовке силикатного элемента находится в пределах 160-210 кг/см².
На стадии формовки кирпича решается вопрос о его конструкции. Дело в том, что современные прессы способны обеспечить производство монолитных и пустотелых элементов, а также кирпичей с пазогребневым профилем.
Автоклавная обработка
После формовки полуфабрикат (кирпич-сырец) выгружается из пресса и направляется в автоклав, где обеспечивается его отвердение в специальных условиях. В этой специальной камере осуществляется тепловая обработка и увлажнение, а самое главное, выдержка под высоким давлением.

Автоклав для обработки силикатных заготовок
Изготовление силикатного кирпича высокого качества требует обеспечения следующих условий:
- В течение 140-150 минут в автоклаве постепенно увеличивается давление до 1,1-1,3 МПа и температура 165-185ºС.
- В указанном режиме обеспечивается выдержка заготовок в течение 6,5-8 часов.
- Завершающая стадия процесса предусматривает постепенное снижение давления до атмосферного значения в течение 85-95 минут.
Только после выполнения указанных условий автоклав открывается, и готовые кирпичи отправляются на хранение. Сразу после извлечения из камеры следует провести тщательный контроль качества полученной продукции.
Возможности домашнего производства
Силикатный кирпич можно изготавливать своими руками. Для этого придется приобрести ручной пресс и печь-автоклав. При организации мини-производства в домашних условиях придется полностью повторить вышеописанную технологическую схему. Другое дело, что объемы производства значительно меньше, а значит, все работы можно производить вручную.
Прежде всего подбирается место, где можно самостоятельно добыть крупнозернистый кварцевый песок. Известь лучше приобрести в готовом виде. Далее тщательно перемешиваются песок и известь в пропорции 9:1. Смесь засыпается в металлическую емкость, где производится гашение извести путем добавления воды при перемешивании состава. Вода добавляется из расчета 25 л на 1 м³ смеси.
После гашения раствор увлажняется и засыпается в деревянные или металлические формы. Их можно сделать своими руками или использовать готовые, покупные. В качестве формовочного аппарата можно использовать стандартный пресс для полусухого формования кирпича. Важно обеспечить давление порядка 150-160 кг/см², причем сдавливание формы проводится вручную, постепенно.
Кирпич-сырец после формовки закладывается в печь-автоклав. В ней надо обеспечить давление не менее 8-9 атм, можно воспользоваться способностями пара. Температура поддерживается на уровне 160-180ºС. В таком режиме заготовка должна находиться не менее 6-7 часов.
Силикатный кирпич, несмотря на некоторые недостатки, широко применяется для возведения стен построек разного типа. При покупке такого материала следует обратить внимание на его качество, что является следствием соблюдения технологических приемов. Изготовить кирпич можно и самостоятельно, но для этого необходимо приобрести пресс для формовки и автоклав.
Силикатный кирпич
Размер и вес в любом строительном материале имеет первоначальное значение для определения множества вспомогательных факторов. Тот же силикатный кирпич необходимо купить, правильно посчитать, нанять перевозчика с грузчиками и доставить материал к месту стройки. Все это требует оплаты труда, напрямую связанной с весом, размерами и количеством стройматериала.
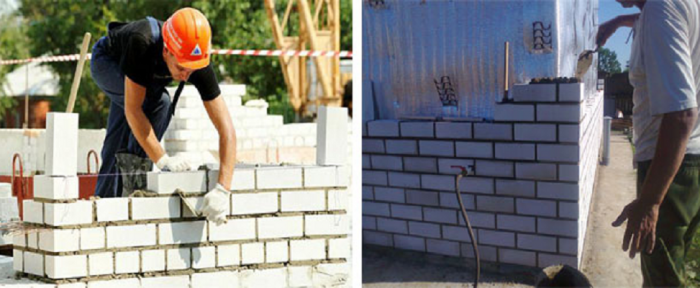
Определяем размер и количество силикатного кирпича
Основной учет работы каменщика выполняется из расчета количества штук уложенного материала, реже – в кубометрах кладки. Силикатный кирпич в сравнении с керамическим блоком очень тяжел, выше физические нагрузки и затраты при его кладке. Расценки могут колебаться и меняться в зависимости от марки, класса средней плотности, размера и качества кладки.
Никому нет желания вычислять после завершения работ, какой силикатный кирпич положен в стену, сколько реально использовано материала, а сколько отбраковано. Поэтому размер, марку и вес необходимо проверить до начала работ. Сделать это можно тремя способами:
- Измерив штангельциркулем линейный размер высоты, ширины и длины стройматериала;
- Довериться информации о блоках силиката на этикетке или маркировке производителя;
- Взвесить стандартный силикатный кирпич на паллете, вычесть вес поддона и рассчитать вес одного делением на количество штук, указанное в накладной или на маркировке.
При этом в современной маркировке стройматериала обязательно приводится информация о его наименовании, марке, классе, средней плотности, морозостойкости, увеличенный размер или одинарный, сведения о наличии специальных пустот, фото. Информации о габаритах или весе стандартного одиночного блока в маркировке нет, но она может присутствовать в качестве дополнительных сведений от производителя наряду с весом брутто всей упаковки.
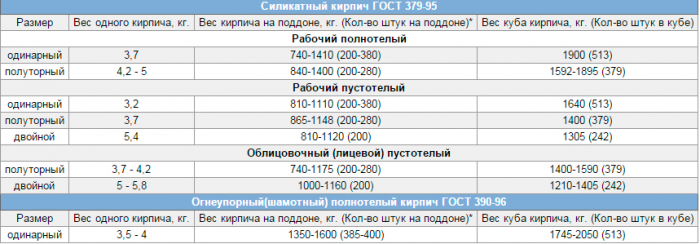
Кроме того, современные условия предпродажной подготовки товара требуют упаковки паллет с материалом в плотную прозрачную полиэтиленовую пленку, из-под которой сложно вытащить пару блоков, чтобы их измерить или осмотреть.
Стандартные размеры
ГОСТом №379-2015 определены две основные размерные группы кирпича из силиката – одинарный и увеличенный, ранее назывался полуторным. Размер обоих в длину -250 мм, в ширину – 120, а высота различается – увеличенный строительный материал -88 мм, одинарный – 65 мм.
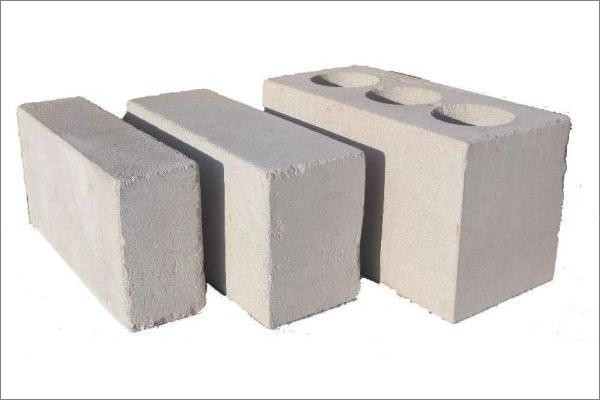
Эти размеры имеют все разновидности лицевого и рядового стройматериала, независимо от наличия пустот или декоративных элементов на лицевой поверхности.
Важно! Не стоит путать силикатный кирпич с иными материалами из массы силиката. Так, при увеличении высоты до 138 мм материал 250х120х138 будет правильно называться камнем, а с шириной тычковой грани более 130 мм – силикатным блоком.
Выбор в пользу одинарного или увеличенного формата материала зачастую делается из соображений обеспечения привлекательного внешнего вида кладки. Одинарный блок легче, и в кладке выглядит зачастую эффектнее, тогда как полуторный материал из силиката позволяет увеличить скорость возведения стен чуть ли не вдвое с меньшим расходом раствора на швы.
Вес силикатного кирпича конкретной марки
Самым сложным и плохо контролируемым параметром стройматериала из силиката является его вес. Известно, что средний вес экземпляра рядового одинарного кирпича может колебаться от 3,2-3,7 кг. Полуторный экземпляр в среднем потянет на 4,3-4,8 кг, в зависимости от конструктивных факторов.
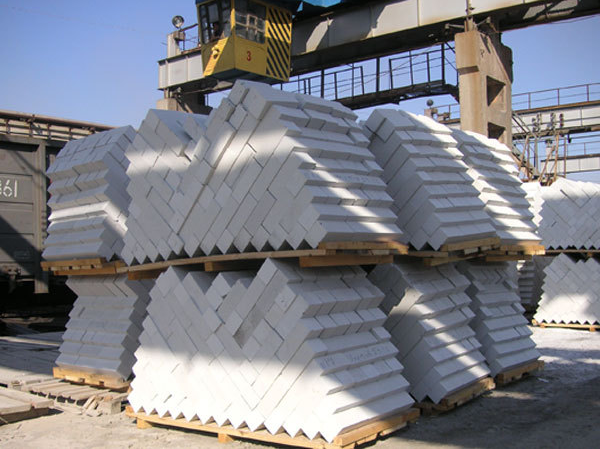
От чего зависит вес
Если задаться целью и проверить, сколько весит силикатный кирпич, и насколько не соответствует заявленным параметрам, необходимо предварительно учесть следующие факторы:
- Стандартом выделены семь основных классов средней плотности материала, которая может быть выбрана производителем в зависимости от используемого сырья от 1000 до 2200 кг/м3;
- В пределах одного класса силикатный кирпич по плотности может отличаться на 50 кг на куб материала;
- Разные условия хранения материалов из силиката дают различную влажность стройматериала и разный вес.
Важно! ГОСТом не оговаривается вес пустотелого варианта, размеры пустот и их форму определяет производитель, лишь бы толщина наружных стенок была не меньше 10 мм, да прочность блока из силиката соответствовала его марке.
Самыми популярными среди вариантов материалов из силиката для частного строительства считаются:
- Увеличенный или полуторный материал с 20% от объема пустот в виде мелких сот с классом средней плотности в 1.6. Это прочный, легкий материал с относительно приемлемыми теплоизоляционными характеристиками. Из него строят основные стены двух-трехэтажных построек;
- Одинарный облицовочный вариант классом средней плотности 2,0 с пазогребневым соединением и гидрофобной пропиткой.
Выбор силикатного кирпича исходя из веса
Вес экземпляра материала из силиката и его прочность – абсолютно взаимосвязанные вещи. Прочность во многом определена степенью размола исходных компонентов и сырья. Чем мельче фракция песка и извести, глубже и полноценнее перемешивание, тем плотнее получается силикатная масса кирпича и выше его вес.
В производстве такой материал сложнее, процесс автоклавной переработки требует повышенных затрат для обеспечения необходимой прочности камня, изготовление занимает больше времени. Но при этом в теле кирпича образуется значительно меньше воздушных пор, убийственно влияющих на срок службы силикатного материала.
Связано это, прежде всего, с глубинным намоканием материала. Чем больше пор и каверн в теле стройматериала из силиката, тем больше влаги он сможет вобрать в себя. Для этого не обязательно оставлять кирпич под дождем или погруженным в воду. Очень хорошо, практически как губка, материал из силикатной массы может поглощать влагу из тумана, влажного конденсата и, тем более, из влажного грунта.
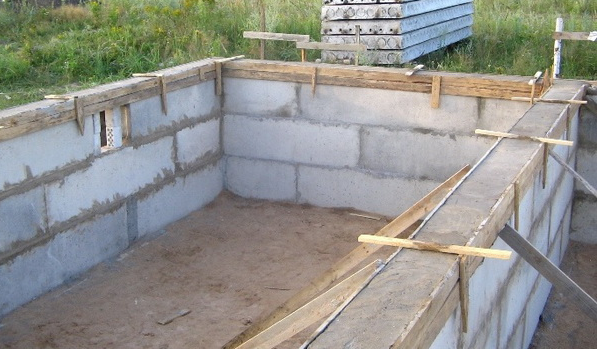
Чем больше площадь поверхности контакта, тем быстрее идет процесс намокания. И полиэтиленовая упаковка пачек на поддоне не может остановить этот процесс. Она скорее защищает от сильных осадков и сохраняет товарный вид кирпича от загрязнения. Поэтому купленный стройматериал из силиката следует хранить только в сухом, проветриваемом помещении.
Очень хорошо помогает гидрофобная пропитка, но ее хватает максимум на три-четыре года, чем жарче климат, тем быстрее исчезает водоотталкивающий эффект.
Важно! Благодаря высокой степени уплотнения силикатный кирпич с высокими значениями класса средней плотности значительно лучше противостоит намоканию.
Стандартом определен уровень минимального водопоглощения для силикатного кирпича в 6%. На практике максимальное водопоглощение составляет от 8 –для тяжелых и плотных кирпичей до 14% для легких и пустотелых. Это значит, что полуторный образец весом в 4,3 кг сможет набрать дополнительно почти 0,5 кг или литра воды. Теоретически, пребывая под дождем длительное время, пачка нового материала может потяжелеть минимум на 10%.
Соответственно, у вас вырастают транспортные расходы, но, что самое неприятное, – вместо плотного тяжелого варианта вы можете купить мокрый легкий силикатный кирпич и даже не подозревать об этом.
Чаще всего вес блока или камня рассчитывают, как среднее значение от взвешивания небольшой партии из десяти штук.
Кроме плотности и водопоглощения, на вес силикатного кирпича влияет количество циклов заморозки и разморозки, «пережитых» материалом. С каждым новым циклом часть внешней лицевой поверхности подвергается шелушению и осыпанию. ГОСТ требует, чтобы по указанной норме морозостойкости, например, наименьшей из существующих – F25, за двадцать пять циклов потери веса материала не превысили 5%.
Заключение
Вес и размеры силикатного кирпича требуют индивидуального контроля, хотя бы в пределах одной пачки. Это позволит избежать потерь, связанных с недобросовестностью производителей материалов из силиката-массы и, что чаще всего — импортеров некачественных или поддельных товаров.