Двухкомпонентное последовательное литье | Moldex3D – моделирование литья пластмасс
Двухкомпонентное последовательное литье (Sequential molding, multi-compound molding) – специальная технология литья, основанная на последовательной проливке элементов детали из различных полимеров. Последовательное литье по своей сути похоже на литье со вставкой, только здесь в качестве вставки выступает отлитая на первом этапе процесса полимерная деталь.
Moldex3D позволяет моделировать процесс двухкомпонентного последовательного литья с помощью модуля MCM. В качестве примера рассмотрим процесс литья тестовой детали, состоящей из двух частей (рис. 1)
Рис. 1. Тестовая модель
Интересно сравнение результатов моделирования литья одного и того же изделия методом двухкомпонентного последовательного литья и по технологии литья со вставкой. То есть в первом случае вставка рассматривается как результат проливки (учитывается, например, технологическая температура вставки после ее охлаждения).
Moldex3D позволяет оценить температуру расплава к каждой точке изделия на протяжении всего процесса охлаждения детали. Интересна температура внутри изделия, поэтому для построения полей распределения температуры выберем произвольное сечение (рис. 2).
Рис. 2. Исследуемое сечение изделия
Сопоставим поля распределения температуры по изделию в фиксированные моменты времени процесса охлаждения. В левом столбце – результаты, полученные по технологии литья со вставкой, в правом – с учетом предварительной проливки вставки (двухкомпонентное последовательное литье).
Как видно из приведенных выше полей распределения температуры, процесс охлаждения в рассматриваемых двух случаях протекает совершенно по-разному. Отличие в начальной температуре вставки оказывает очень серьезное влияние, особенно на начальном этапе процесса охлаждения.
Картина итогового распределения температуры хоть и отличается, отличия совершенно не существенные (десятые доли градуса).
Силотерм ЭП-120 Огнезащитный двухкомпонентный компаунд (пластик. ведро, 15 кг)
Производитель cерия
Ostec ОКП Огнестойкие кабельные проходкиАртикул производителя
СИЛОТЕРМ ЭП-120-15
Код в учетной системе
355781
Тип товара
Противопожарный компаунд/покрытие
Получить в
Магазин не выбран
Все магазины
Характеристики
Технические характеристики Силотерм ЭП-120 Огнезащитный двухкомпонентный компаунд (пластик.

Основные характеристики
Тип товара |
Противопожарный компаунд/покрытие |
Серия производителя Под серией подразумевается однотипный набор продукции, которую выделяет в ассортименте и производит определенный производитель.»/> |
|
Сведения РАЭК
Наименование |
ЭЛОКС-ПРОМ Силотерм ЭП-120 Огнезащитный двухкомпонентный компаунд (пластик. ведро, 15 кг) |
Дополнительные характеристики
Комплект поставки |
Ведро |
Тип позиции Складские позиции пополняются на регулярной основе. Заказные позиции мы везём от поставщика с выставленной кратностью товара. Этот тип товаров поставляется после предварительной оплаты.»/> |
Заказная |
Кол-во в транспортной упаковке |
15 |

Нашли неточность в описании? Выделите её и нажмите Ctrl+Enter или через форму
Наличие в магазинах
Наличие товара по области
Весь Сибирский федеральный округ
Остатки обновлены: 31.01.2022 18:30:02
Уважаемый клиент! Товары между торговыми залами не перемещаются. Пополнение с распределительного и региональных складов БЕСПЛАТНО!
Торгово-выставочные залы и электромаркеты
Отзывы
Написать отзыв
Рекомендации по выбору материалов для дорожной разметки: эмали, пластики, термопластики
В настоящее время существует широкий ассортимент материалов, которые используются для нанесения разметки на дорожное покрытие: эмали, пластики, термопластики, краски, полимерные ленты.
Краски и эмали
Это самый традиционный материал для создания дорожной разметки. Они отличаются ударопрочностью и устойчивы к истиранию. Срок службы подобной разметки составляет около года. Также важным параметром является скорость высыхания, которая составляет от 15 минут до получаса. Это особенно важно на оживленных магистралях. Третьим важным параметром является устойчивость к неблагоприятным погодным и климатическим условиям. Важно упомянуть невысокую стоимость этого материала. Краска для разметки дорог используется:
- на автомобильных дорогах и автодромах;
- в качестве разметки в складских помещениях;
- как разделитель парковочных мест и отметка парковку для инвалидов;
- на аэродромах;
- для разметки территории в воинских частях;
- как разметка на территориях возле школ и детских садов;
- обозначение велосипедных дорожек.
Краска наносится на предварительно очищенную поверхность. В большинстве своем, этот вид покрытия не требует предварительного разогрева поверхности, но бывают исключения. Именно холодные составы принято использовать в местах, где движение наиболее интенсивное.
Холодный пластик
Пластик холодного отвержения — это инновационный материал, использующийся для нанесения дорожной разметки. Он представляет собой двухкомпонентную смесь, которая отвердевает после прохождения химической реакции. Холодный пластик не нуждается в нагревании перед началом работы, а также не подвержен деформации ни в процессе нанесения и высыхания, ни в процессе эксплуатации. Он износостоек и устойчив к погодным условиям, отличается высоким коэффициентом сцепления с дорожным покрытием. При нанесении очень экономен. Расход холодного пластика на квадратный метр при толщине покрытия 1 миллиметр составляет 1,7-1,8 килограмм. Создает дополнительный шумовой эффект при соприкосновении с покрышками едущего транспорта. Срок службы данного вида дорожной разметки может составлять до двух лет.
Термопластик
Горячий пластик, который также называют термопластиком, представляет собой многокомпонентную смесь, которая перед нанесением нуждается в нагревании и вымешивании. В состав смеси также могут входить светоотражающие шарики. Существуют полиэфирные и нефтеполимерные смеси. В целом это покрытие также относится к современным материалам с повышенной стойкостью и длительным сроком эксплуатации.
Поскольку термопластик не содержит растворителей, его необходимо разогреть перед нанесением до температуры 150-220 °С. Затем пластик размешивают в особой таре до достижения однородной консистенции и проверяют на вязкость по специальной таблице значений. Термопластик может наноситься разными способами:
- гравитационным;
- путем экструзии;
- вручную с помощью готовых форм;
- при помощи пневматического инструмента по спрей-технологии.
Какой материал выбрать для нанесения дорожной разметки
Выбор материала для разметки на дороге осуществляется на основании ряда факторов:
- интенсивность движения;
- ширина полосы;
- разновидность разметки;
- скорость разрушения разметки на конкретном участке;
- качество и вид дорожного покрытия;
- как содержится дорожное покрытие.
В методических пособиях по выбору материала дорожной разметки учитываются также погодные условия, расход материала на квадратный метр, плотность и толщина слоя материала.
Дорожные эмали и краски стоят дешевле и не требуют никакого специального оборудования. Однако и срок их службы меньше, чем у более современных материалов. Дорожную разметку, нанесенную краской, требуется обновлять не реже раза в год. Пластиковое покрытие обладает лучшими эксплуатационными свойствами, широкими возможностями и более долгим сроком службы, но при этом требует больших финансовых вложений и особых технологий смешивания и нанесения.
Встраиваемые пластмассовые смесители | Двухкомпонентные смесители
Идеально подходя для однократного использования дозирования жидкости, одноразовые статические смесители Nordson EFD устраняют необходимость в беспокойстве по поводу преждевременного отверждения материалов.
Широкий выбор смесительных элементов, вылитых из ацеталя или полипропилена, и корпусов, вылитых из полиамида или нержавеющей стали.
Доступные варианты
Встраиваемые трубчатые спиральные смесители серии 85
Разработанные для использования в системах с высоким давлением, наши трубчатые смесители серии 85 оснащены прочными металлическими корпусами и одноразовыми пластмассовыми смесительными элементами серии 120.
Благодаря корпусам, изготовленным из толстостенной трубы из нержавеющей стали, они устойчивы к вмятинам и деформациям. Элементы смесителя можно выдавить и заменить, что упрощает плановое техническое обслуживание.
Характеристики
- Съемные смесительные элементы
- Низкий объем полимера в смесителе
- Жесткие металлические корпуса
- Повышенная прочность
В состав вспомогательных принадлежностей входят трубный переходник и муфта.
Одноразовые пластмассовые трубчатые смесители серии 140
Смесители серии 140, экономичные и собранные полностью из пластмассовых компонентов, являются идеальным решением для грязеобразующих адгезивов или адгезивов с коротким сроком хранения и позволяют утилизировать смеситель (вместо промывания растворителем и запекания).
Прозрачный корпус смесителя предоставляет возможность осмотра его внутреннего пространства для определения состояния смесителя. Внутреннее пространство, выполненное из ацеталя, придает прочность и химическую устойчивость, обеспечивая инертность к большинству обычных растворителей. Максимальная рабочая температура 250° F (121° C).
Для областей применений, связанных со смешиванием адгезива и герметика, предоставляются дополнительные смесительные элементы из полипропилена.
Вспомогательные
Жидкий двухкомпонентный пластик Poly Art 640 г. (А+Б)
ДВУХКОМПОНЕНТНЫЙ ЖИДКИЙ ПЛАСТИК POLY ART FAST (А+B) 640 гр.
Poly Art Fast- Двухкомпонентный жидкий пластик белого цвета, быстро полимеризующйся. Который предназначен для изготовления декоративных и технических изделий, имитаций изделий из бронзы и других металлов методом открытого литья или ротации.
Жидкий пластик Poly Art Fast отлично подходит для создания рекламно-презентационной продукции, эксклюзивной сувенирной продукции, мебельного декора, моделирования и дизайна, плит для фрезерования, элементов конструкций и т. д.
В КОМПЛЕКТ «Poly Art Fast (А+B)» ВХОДИТ:
Компонент А (полиол) — 0,400 г.
Компонент B (изоцианат) — 0,240 г.
Цвет изделия — слоновой кости.
ИНСТРУКЦИЯ ПО ПРИМЕНЕНИЮ:
Перед использованием тщательно встряхнуть два компонента в упаковочной таре в течение 2-3 минут.
Размешайте оба компонента до однородного состояния в фабричной таре.
Отлейте необходимое количество, предварительно перемешанного полиола.
Отлейте необходимое количество, предварительно перемешанного изоцианата.
Перемешайте смесь палочкой или миксером в течение 20-30 секунд.
Произведите заливку материала в форму.
Выдержите материал в течение 5-10 минут в состоянии покоя.
СВОЙСТВА ПРОЦЕССА ПОЛИМЕРИЗАЦИИ:
Время потери текучести при 230С – 2 минуты 20 секунд (масса замеса 200 грамм) При увеличении массы смешиваемых компонентов время может сокращаться т.к. в процессе реакции выделяется тепло. Изменение температуры в помещении, формы или компонентов, приводит к изменению времени потери текучести. Время формования 10± 5 минут в зависимости от изделия Температура формования при 23± 70С
ТЕХНИКА БЕЗОПАСНОСТИ:
Защищать от влаги. Попадание воды в емкость, содержащую компонент B (изоцианат) приводит к образованию углекислого газа, что может вызвать избыточное давление в закрытой емкости. Не хранить под открытыми лучами солнца и вблизи нагревателных приборов.
Работу производить хорошо проветриваемом помещении.
При попадании на кожу, тщательно промыть водой.
Свойства конечного изделия
Плотность отвержденного полимера при 23 0С (ASTM D 891) – 1240 кг/м3
Твердость по Шору Д при 230С (ASTM D 676) – 77±3 единицы
Свойства получены на пластинах толщиной 10 мм, после 48 часов экспозиции при температуре 230С
Ремонтируем бампер двухкомпонентным клеем | Журнал Кузов
Чем только на скорую руку не латают поврежденные пластиковые бамперы — и саморезами, и металлическими скобами. Но если говорить о более качественном ремонте, то часто применяют пластиковые прутки, которые впаиваются в трещину с помощью паяльника или газовой горелки. Эксперты канала Kuzov Lab отремонтировали трещины в бампере, используя двухкомпонентный клей немецкой компании Henkel.
Дело в том, что двухкомпонентный клей обладает одним важным преимуществом — возможностью работать со всем типами автомобильного пластика, будь то полиуретан, полипропилен или АБС (акрилонитрилбутадиеновый пластик). Данное свойство по достоинству оценят те, кому приходилось, к примеру, паять поврежденные бамперы автомобилей Mercedes-Benz, когда пруток для пайки нужно подбирать под каждый конкретный бампер. Еще один плюс двухкомпонентного клея — после полимеризации этот материал остается эластичным, благодаря чему при легких надавливаниях на место ремонта при последующей эксплуатации автомобиля это место не будет повреждаться. Что касается пайки, то эта технология влияет на пластик достаточно негативно: место пайки становится более хрупким.
Двухкомпонентный клей Henkel изготавливается на основе полиуретана и выпускается в трех вариантах: обычном (PU 9225), superfast (PU 9225 SF) и ultrafast (PU 9225 UF). Между собой составы различаются скоростью первичной полимеризации: обычный можно обрабатывать через двадцать минут после сушки, SF — через десять минут, UF — через две минуты. Полную прочность все они набирают через 24 часа.
1. После мойки автомобиля снимаем бампер и удаляем с него остатки грязи. Напыляем на нетканую салфетку очиститель Henkel TEROSON VR 10 — он позволяет и очистить, и обезжирить поверхность. Очищаем салфеткой место ремонта. Переворачиваем бампер и очищаем/обезжириваем это же место с обратной стороны.
2. В конце каждой трещины просверливаем отверстие диаметром 5 или 6 мм. Это позволяет снять напряжение, а также препятствует тому, чтобы трещина впоследствии расползалась.
3. Пневмопилой разделываем каждую трещину так, чтобы ее края не соприкасались между собой. Тем самым создается пространство для заполнения двухкомпонентным клеем и опять же снимается напряжение.
4. Пневмонапильником снимаем фаску на внешней стороне повреждения — на расстоянии порядка 10 мм от края разделенной трещины и по периметру всего повреждения. Ножом подрезаем по контуру куски оплавленной пластмассы. Сами трещины, которые также оплавились, расширяем лезвием ножа.
5. Шлифмашинкой расширяем фаску и делаем края более пологими, для того чтобы увеличить площадь соприкосновения материала клея с поверхностью ремонтируемого бампера. Брызгаем на нетканую салфетку очиститель TEROSON VR 10 и очищаем/обезжириваем подготавливаемую поверхность.
6. Переворачиваем бампер и шлифмашинкой обрабатываем внутреннюю часть повреждения. Если есть заусенцы, их также удаляем. Затем очищаем и обезжириваем поверхность нетканой салфеткой с очистителем TEROSON VR 10.
7. Наносим на обе стороны ремонтируемой поверхности праймер по пластику Henkel TEROSON 150. Распыление должно быть не обильным (предназначено только для того, чтобы активировать поверхность). Ждем примерно 10 минут, пока испарится растворитель.
8. Картридж с двухкомпонентным клеем Henkel (в данном случае PU 9225 SF) объемом 50 мл заряжаем в ручной пистолет TEROMIX.
9. Открываем крышку картриджа и, нажав на курок пистолета, выдавливаем некоторое количество материала на лист бумаги, убеждаясь, что материал равномерно выходит из обеих туб картриджа.
10. Закрепляем на картридже сменный носик-смеситель — он идет в комплекте с двухкомпонентным клеем Henkel. Опять выдавливаем некоторое количество материала на лист бумаги, проверяя, смешиваются ли оба компонента продукта равномерно.
11. Наносим материал непосредственно на поврежденную поверхность на внутренней стороне бампера. Носик-смеситель можно подрезать, ориентируясь по рискам, так чтобы отрегулировать количество наносимого материала.
12. Накладываем армирующую подкладку и утапливаем ее в материал. Подкладка должна быть из стекловолокна, как в данном примере, либо в виде пластиковой сетки. Ни в коем случае нельзя использовать металлическую сетку, поскольку впоследствии она начнет корродировать.
13. Наносим двухкомпонентный пластик на армирующую подкладку, так чтобы стекловолокно не торчало из-под материала. Пластиковым шпателем разравниваем материал по ремонтируемой поверхности. Сверху материал можно накрыть полиэтиленовым пакетиком — при этом двухкомпонентный клей быстрей сохнет, поскольку в процессе полимеризации выделяется тепло.
14. Переворачиваем бампер и выдавливаем материал на наружную поврежденную поверхность. Во время нанесения, во избежание попадания воздуха, держим носик-смеситель внутри клеевого шва.
15. Разглаживаем нанесенный материал, двигая пластиковый шпатель от центра к периферии. Ждем 10–15 минут.
16. Шлифмашинкой проводим абразивную обработку (зерно Р150/Р240) нанесенной поверхности до получения ровного и гладкого покрытия. Напыляем очиститель TEROSON VR 10 на нетканую салфетку и очищаем готовую поверхность. Через 24 часа можно приступать к покраске бампера. Кстати, перед покраской желательно также использовать праймер по пластику TEROSON 150.
Рекомендованные статьи
Литье пластмасс в силикон — доступное мелкосерийное производство в домашних условиях
Многие из тех, кто
печатаетна
3D-принтересталкиваются или с необходимостью получить партию моделей в короткие сроки, или скопировать удачно получившуюся деталь, или получить изделия с прочностными характеристиками, превосходящими таковые у пластиков для домашней
3d-печати.
3D-принтер далеко не всегда способен выполнить такие задачи, но отлично подойдет для создания единственного образца, или мастер-модели. А дальше на помощь нам приходят материалы производства компании Smooth-On, наверное, самого популярного производителя материалов холодного отверждения.
В этом обзоре мы сравним самые основные и популярные силиконы, полиуретаны и добавки к ним, кратко посмотрим на основные способы создания форм и изделий, подумаем, где это может найти применение и, наконец, создадим свою силиконовую форму и модель.
Перед написанием этого поста мы прошли трехдневный тренинг у официального дилера Smooth-On в России, чтобы разобраться во всех тонкостях литья в силикон.
Обзор процесса
Процесс создания изделий методом литья практически всегда одинаков: создаем модель, с её помощью создаем силиконовую форму, заливаем в нее материал, получаем изделие. Но в зависимости от модели, необходимых свойств, количества отливок, каждый этап может кардинально меняться. Существует несколько способов как создания формы, так и готового изделия.
Пару слов о подготовке моделей, напечатанных на 3D-принтере. Компания Smooth-On обратила своё внимание на эту технологию и выпустила специальный лак под названием XTC-3D. Он прекрасно сглаживает характерные для напечатанных моделей огрехи, видимые слои, которые обязательно перейдут на силиконовую форму, и придает поверхности гладкость и глянцевый вид.
Подробный обзор XTC 3D Вы можете прочитать здесь.
Методы создания форм
• Сплошная заливка
Самый простой способ: модель помещается в опалубку (специальную герметичную емкость из обычного оргстекла, пластика или другого материала), фиксируется в ней и заливается силиконом. Хорошо подходит для простых двухмерных моделей, рельефов, сувенирной и брендинговой продукции.
• Разрезная форма
Аналогичен предыдущему, только модель размещается с учетом того, что форма будет разрезаться полностью или частично для облегчения съема. Модель может быть подвешена с помощью проволоки или размещена на тонкой опоре. Способ предназначен для более сложной геометрии, технических изделий, сложных фигур.
• Двухсоставная форма
Это один из самых сложных способов. Заключается в помещении модели на глиняную или пластилиновую основу, которая делит силиконовую форму пополам.
На основе размещаются специальные замки, которые будут обеспечивать точное совмещение двух форм и отсутствие смещений. Вокруг основы собирается опалубка, герметизируется горячим клеем или пластилином, и в неё заливается первая половина формы. Затем, после отверждения силикона, форма переворачивается, глина или пластилин счищаются, силикон покрывается разделительным составом, и заливается вторая половина формы.
• Метод «в намазку»
Этим методом создаются так называемые «чулочные» формы, когда силикон точно повторяет форму объекта и имеет толщину от 3 мм до нескольких сантиметров. Для создания формы «в намазку» необходим достаточно вязкий силикон, который бы не стекал с модели.
Можно использовать как специально предназначенные для этого силиконы, называемые тиксотропными, так и обычные, но модифицированные с помощью загустителей.
Силикон наносится кисточкой или шпателем в несколько слоёв, в которых чередуется вязкость и скорость отвердевания, чтобы форма была максимально детализированной и прочной. После того, как все слои готовы, с помощью специального состава создается жесткая внешняя оболочка, которая будет держать форму.
Методы заливки пластиков
Самый простой метод заключается в обычной заливке пластика в форму, он подходит для домашнего использования и позволяет достичь приемлемого качества. Но, по необходимости, для более качественного результата возможно использование установок высокого давления, что позволит практически полностью убрать пузырьки воздуха.
Для этого форма вместе с залитым пластиком помещается в камеру, в которой создается повышенное до 4 атмосфер давление. Форма должна оставаться в камере все время отвердевания полиуретана. При таком давлении пузыри уменьшаются до почти невидимых глазу размеров, что значительно повышает качество изделия.
Еще один метод, так называемая заливка «в обкатку», используется для создания полых изделий. В форму заливается небольшое количество пластика, около 10% от общего объема, отверстие для заливки закрывается, и начинается вращение формы по всех плоскостях, вручную или на специальной ротационной машине. При этом пластик отвердевает на стенках формы, создавая полую модель, что позволяет существенно снизить вес изделия и экономить материал.
Обзор силиконов
• Серия Mold Star 15, 16, 30
Силиконы для создания форм на основе платины. Застывают при комнатной температуре, образуют прочную, гибкую и очень детализированную форму. Предназначены для литья силикона, полиуретана, смол, полиэстера, воска и других материалов. Химически чувствительны и не способны работать с латексом, серой и некоторыми другими соединениями.
Самые базовые и основные силиконы, способные решать большинство задач. Цифра в названии отражает твердость по шкале Шор А. Обладает низкой вязкостью, что позволяет в большинстве случаев работать без оборудования для дегазации. Материал двухкомпонентный, части смешиваются в удобном соотношении 1:1 по объему. В основном предназначены для создания форм методом сплошной заливки.
• Серия Rebound 25, 40
Серия силиконов для создания форм методом «в намазку», который состоит в том, чтобы наносить силикон кистью или шпателем на поверхность модели. Обладает высокой вязкостью, возможностью модификации свойств с помощью загустителей и ускорителей для создания качественной многослойной формы. Двухкомпонентный, смешивается в соотношении 1:1 по объему.
• Серия Equinox 35, 38, 40
Силиконовые пасты с временем жизни 1, 4 и 30 минут. Предназначены для ручного смешивания, по консистенции напоминают густое тесто. Цифры соответствуют твердости по Шору А. Обладает крайне высокой прочностью на разрыв и долговечностью. В отвержденном состоянии является безопасным для заливки шоколада, карамели и других ингридиентов.
• Серия SortaClear 18, 37, 40
Серия полупрозрачных силиконов. Такая особенность, как оптическая прозрачность, используется для создания сложных разрезных форм — изделие прекрасно просматривается, что позволяет сделать точный разрез. Как и серия Equinox, является безопасным при контакте с пищевыми продуктами.
Также к силиконам существует большое количество добавок, обладающих самыми разными эффектами. Accel-T и Plat-Cat являются ускорителями отверждения, Slo-jo — увеличивает время жизни силикона, Thi-Vex увеличивает вязкость силикона и позволяет намазывать его кистью или шпателем на модель, Silc-Pig — это концентрированные пигменты для окрашивания.
Обзор полиуретанов
• Серия Smooth-Cast
Самая основная и популярная серия полиуретанов для создания конечных изделий. Линейка включает в себя более 10 наименований различных пластиков с самыми разными свойствами, позволяющими подобрать материал именно для Вашего проекта. Например, Smooth-Cast 300 обладает коротким временем жизни в 3 минуты и временем отверждения в 10 минут, что позволяет быстро воспроизводить большие партии деталей. Smooth-Cast 305 аналогичен предыдущему, но «живет» уже 7 минут, что позволяет провести дегазацию смешанных компонентов и получить еще более качественное изделие. ONYX обладает глубоким черным цветом, которого не достичь с помощью красителей, 65D ROTO предназначен для создания полых моделей с помощью метода «в обкатку», 325 незаменим для точного воспроизведения цвета, 385 отверждается практически без усадки и максимально точно копирует изделие.
• Серия TASK
Серия полиуретанов специального назначения. Разработана для промышленного применения и обладает специфическими свойствами для конкретных задач.
Для Вашего удобства мы сформировали специальные фильтры по сферам применения:
• Пищевые:
Smooth-Sil 940, серия Sorta Clear, серия Equinox, TASK 11.
• Архитектурные, заливка бетона и других абразивных материалов:
Серия VytaFlex, серия Brush-On, серия Ez-Spray, серия PMC.
• Медицинские: симуляция тканей и органов
Серия Dragon Skin, добавки Slacker, Ecoflex 0030, Ecoflex Gel, Body Double.
• Прототипирование:
Практически любые полиуретаны и силиконы, в зависимости от задач и требований. Серии Mold Max, Mold Star, Smooth-Cast, TASK.
• Спецэффекты и грим:
Skin Tite, Body Double, Dragon Skin, Alja-Safe, Ecoflex, Soma Foama, Rubber Glass, Encapso K.
Стоит отметить, что это деление все же условное, и дано, чтобы примерно представить возможности широкого ассортимента компании Smooth-On.
Обзор процесса
Мы будем использовать только те материалы и оборудование, которые можно применить в домашних условиях. Мы попробуем создать самую сложную в изготовлении двухсоставную форму.
Нам понадобятся:
• Платиновый силикон Mold Star 30
• Заливочный полиуретан Smooth-Cast 300
• Лак для 3D-моделей XTC-3D
• Упаковка виниловых перчаток
• Несколько одноразовых пластиковых стаканчиков
• Емкости для смешивания
• Термоклеевой пистолет
• Материал для опалубки (пластиковые панели)
• Скульптурная глина
• Несколько малярных кистей
В роли мастер-модели выступит модель довольно популярного среди печатников тестового болта. Мы распечатали его черным PLA пластиком на Picaso 3D Designer с толщиной слоя 100 микрон. Сделали мы это специально для того, чтобы продемонстрировать эффект XTC 3D, поскольку далеко не каждый 3D принтер может печатать с качеством 50 микрон.
Далее — обработка, чтобы отлитая модель не переняла слоистость напечатанного объекта. Обрабатываем болт лаком XTC-3D (подробнее об этом процесс можно прочитать тут), а затем шкурим, чтобы получить гладкую матовую поверхность.
Теперь модель готова к заливке силиконом. Помещаем её на глиняную основу, с помощью которой мы создадим силиконовую форму из двух частей.
Модель должна быть погружена в глину ровно наполовину, так что начинаем процесс выравнивания глины. Края должны быть максимально ровными и полностью прилегать к модели, от этого зависит качество разделения силиконовых половинок. Убираем лишнюю глину и заключаем модель в пластиковую опалубку.
Все стыки пластика обрабатываем термоклеевым пистолетом и закрываем опалубку, окончательно обрабатываем глиняную основу, делаем в ней выемки для замков.
Все готово к заливке силикона. Поскольку двухкомпонентные силиконы и полиуретаны склонны к разделению на фракции, перед каждым использованием их необходимо тщательно перемешивать в емкости.
После перемешивания отмеряем равное количество двух компонентов по объему и приступаем к смешиванию.
Для данной марки силикона дегазация в вакуумной камере необязательна, что очень удобно: исключены появления пузырьков, которые могут испортить нашу форму. Медленно заливаем силикон в опалубку, в самую нижнюю её точку.
И оставляем застывать. Время застывания для этой марки силикона составляет 6 часов. По истечении этого времени освобождаем модель от опалубки.
Затем убираем глину, тщательно очищаем модель от её остатков, смазываем силикон разделительным составом. В случае его отсутствия, можно использовать и обычный вазелин, но качество будет немного хуже.
И дальше полностью повторяем процесс, заливая вторую половину силиконовой формы.
Спустя еще 6 часов силиконовая форма готова. С помощью лезвия аккуратно разъединяем половинки, вынимаем деталь и оцениваем, что у нас получилось.
Хорошо видны замки, закладывавшиеся в глиняной основе, хорошая детализация, несмотря на то, что разделительная линия проходила по довольно сложным местам, вроде вдавленных букв.
На самом деле, для данной модели это не самый оптимальный способ создания формы. Но нам было интересно протестировать именно этот метод, несмотря на сложности.
Итак, все готово к заливке полиуретана. Соединяем две половинки формы, используя элементы опалубки для жесткости, скрепляем с помощью резинок, скотча или другим способом, и приступаем к подготовке полиуретана.
Хорошо перемешиваем оба компонента, встряхивая их в течение 5-10 минут. После этого даем немного отстояться, чтобы вышли образовавшиеся пузыри. Все остальное точно так же, как и с силиконом: отмеряем равное количество по объему и смешиваем их. А дальше действовать нужно быстро: время жизни этого полиуретана составляет всего 3 минуты, а время начинает идти сразу, как вы смешали два компонента вместе. Так что мешаем быстро, но аккуратно, чтобы не создавать лишних пузырьков, и сразу заливаем в форму.
Примерно через 3 минуты, в зависимости от объема материала, произойдет быстрое схватывание пластика, а через 10 минут деталь готова к извлечению.
Модель готова. Переданы абсолютно все детали оригинала.
Заключение
Хочется отметить, что поистине огромные возможности использование материалов Smooth-On открывает в совокупности с 3D-печатью.
Теперь Вы можете получать изделия из огромного количества материалов с самыми различными свойствами, а не ограничиваться лишь классическими PLA и ABS. К тому же, доступным станет мелкосерийное производство: распечатав всего один экземпляр и должным образом его обработав, Вы сможете в довольно короткие сроки создать необходимое Вам количество копий в домашних условиях. Для достижения приемлемого результата вовсе не обязательно использование дорогостоящего оборудования.
В случае если Вам необходимы услуги мелкосерийного производства Top 3D Shop к вашим услугам.
Преимущества двухкомпонентного литья под давлением
Литье под давлением предлагает чрезвычайно универсальный диапазон производственных вариантов, поскольку характер процесса означает, что он подходит для множества конструкций и типов деталей и изделий. Помимо стандартного процесса литья под давлением, двухкомпонентное литье под давлением может обеспечить еще большую универсальность и эффективность. Как следует из названия, двухкомпонентное литье под давлением предполагает использование более одного материала при формовании одной детали. Это отличается от более типичного процесса однокомпонентного литья под давлением, когда в форму впрыскивается только одна базовая смола.Двухкомпонентное литье под давлением может быть достигнуто несколькими способами, каждый из которых дает разные результаты и эффекты. Ниже мы рассмотрим каждый из них:
Смешанные материалы: В том, что можно считать простейшей формой двухкомпонентного литья под давлением, два материала могут подаваться в машину для литья под давлением одновременно и смешиваться при нагревании. . Этот метод можно использовать в эстетических целях. Смешивание, например, красителя со смолой для получения другого цвета или более привлекательного внешнего вида.Его также можно использовать для достижения физических свойств, отличных от свойств одной смолы. Например, примешивание более твердой смолы для усиления детали, сделанной в основном из более мягкого пластика.
Совместное литье под давлением: При совместном литье под давлением две полных порции материала впрыскиваются в полость, одна сразу за другой, в результате чего материалы затвердевают вокруг друг друга и полностью склеиваются. Этот процесс полезен для создания, скажем, мягкой резиновой оболочки вокруг жесткого пластикового ядра.
Литье под давлением: В этом процессе разные материалы подаются в полость формы в разных точках через разные ворота. Они начинают затвердевать до точки их встречи внутри полости, что приводит к эффекту слоистости. При совместном литье под давлением материалы не предназначены для физического смешивания. Точку встречи двух материалов и, следовательно, внешний вид и функцию готовой детали можно регулировать путем точной настройки скорости впрыска каждого материала.
Многоэтапное формование: При многоэтапном формовании эффект «слоения» достигается за счет последовательного впрыскивания частичных порций материала в полость формы. Материалы не смешиваются и не затвердевают друг вокруг друга. Вместо этого они «укладываются» в готовое изделие. Многоэтапное формование также известно как последовательное формование.
Многокомпонентное формование: При многокомпонентном формовании многокомпонентные детали изготавливаются с помощью процесса «добавления», при котором один компонент создается и полностью охлаждается и затвердевает, а затем используется в качестве основы или сердцевины в качестве другой части. часть куска формуется вокруг (или «поверх») него.Многослойное литье обеспечивает большую гибкость в отношении материалов и конструкции, поскольку основная часть даже не обязательно должна быть отлита под давлением (или изготовлена из пластика). Например, резиновая рукоятка может быть отформована вокруг металлической детали.
Когда выгоден двухкомпонентный процесс?
Двухкомпонентное литье под давлением может быть правильным выбором в ряде сценариев, в зависимости от требований и конструкции детали или продукта.
Некоторые ситуации включают:
- Индивидуальные составы смолы: Как упоминалось выше, двухкомпонентное литье может помочь в точной настройке или придании материалу свойств, которые иначе могут не существовать.В дополнение к приведенному выше примеру упрочнения формование из смешанных материалов может помочь достичь, например, большей термостойкости или устойчивости к ультрафиолетовому излучению. Или формование из смешанных материалов может повысить гибкость рецептуры.
- Эстетические соображения: Если продукту требуется определенный внешний вид, двухкомпонентное литье может быть более быстрым и эффективным способом достижения этого (с помощью нескольких из вышеперечисленных методов) вместо покраски или другой отделки однокомпонентного изделия.
компонентный литой продукт.Двухкомпонентный процесс также может обеспечить более высокое качество в таких сценариях.
- Очень сложные конструкции деталей: Многокомпонентное литье может быть идеальным решением для сложных или многокомпонентных конструкций деталей, когда изготовление одной пресс-формы может быть слишком дорогим или невозможным. С помощью многослойного формования относительно простые детали можно комбинировать для создания более сложных деталей с гораздо большей экономической эффективностью.
- Сборки: Как и в предыдущем случае, многослойное формование может быть эффективной альтернативой физической сборке сложных деталей.Сборки, созданные с помощью многокомпонентного формования, а не вторичного процесса, часто будут более надежными и более качественными.
- «Стержневые» конструкции: Многокомпонентное литье и двухкомпонентное литье под давлением являются идеальным способом создания продуктов, в которых требуются отдельные «внутренние» и «внешние» элементы, например, твердая, жесткая внутренняя часть для структурной целостности; и более мягкий внешний материал для сцепления, защиты и / или эстетических целей.
- Любое применение, требующее различных компонентов, внешнего вида или качества материалов: Двухкомпонентное литье может быть высокоэффективным способом эффективного объединения двух процессов в один для любого проекта, который в противном случае потребовал бы сборки и других вторичных и отделочных процессов.
- Есть ли недостатки при использовании двухкомпонентного процесса?

Почему RevPart?
Компания RevPart специализируется на оказании помощи нашим клиентам в поиске наилучшего решения для их продукции. Нашими основными целями для вас являются инновации, качество и эффективность.Наши обширные возможности и услуги по созданию прототипов, включая прототипы, изготовленные методом литья под давлением, означают, что мы можем экономически эффективно работать с вами, чтобы точно настроить наилучший дизайн для вашего продукта, включая методы двухкомпонентного литья. Преимущества прототипов для литья под давлением позволяют нам работать вместе, чтобы понять, как в конечном итоге может и должен работать полный производственный процесс — преимущество, которое невозможно получить с помощью других методов прототипирования.
Обладая обширными знаниями и опытом работы с материалами и различными методами литья под давлением и других производств, мы предлагаем наш опыт для создания наилучшего продукта для вас.
Уникальная пресс-форма, скорость материалов LSR двухкомпонентная формовка
Engel и Elmet представляют новый низкотемпературный процесс отверждения силикона, который сокращает время обработки двухкомпонентных деталей, полученных литьем под давлением, для медицинских и других целей. В основе технологии лежит инновационная форма со встроенными УФ-лампами и вставками из прозрачного пластика.
УФ-лампы встроены в пресс-форму Elmet, показанную на машине для литья под давлением Engel. |

«Усовершенствования силиконовых каучуков за последние два года открыли двери для новых применений в многокомпонентных технологиях для этого класса материалов», — сказал Георг Штайнбихлер, руководитель отдела исследований и разработок Engel Austria.
Возможность использования полипропилена
«В двухэтапном формовании мы видим самую большую возможность в сочетании с низкотемпературными пластиками, такими как полипропилен», — сказал PlasticsToday Клеменс Трумм, менеджер Немецкого центра разработки приложений компании Momentive Performance Materials. «Это относится к маскам для лица, затворам, клапанам, мягкому прикосновению… Весь двухкомпонентный портфель более или менее».
Силиконовые эластомеры, используемые в двухкомпонентных материалах, обычно отверждаются при нагревании или при комнатной температуре с использованием процессов сшивания, таких как отверждение перекисью, отверждение гидросилилированием или отверждение конденсацией. В новом подходе недавно разработанные материалы отверждаются ультрафиолетовым светом с помощью системы отверждения, чувствительной к ультрафиолетовому излучению, которая является неотъемлемой частью пресс-формы Elmet.
Применение технологии для литья под давлением является совершенно новым.
В традиционном процессе стандартный LSR для литья под давлением может быть отвержден при температуре около 356-392ºF. Однако для больших деталей необходимо снизить температуру отверждения, чтобы можно было полностью заполнить формы и исключить попадание воздуха. Примерами являются изоляторы, кабельные муфты, кабельные наконечники или разрядники для защиты от перенапряжения.Для нового процесса, показанного Элметом и Энгелем, требуется «прозрачная для УФ-излучения» форма. Примерами материалов, которые можно использовать вместо стали, являются кварцевое стекло или акрил.
Во время демонстрации на Симпозиуме в прошлом месяце полипропилен был залит жидким силиконом для изготовления винных пробок. Время облучения для вулканизации силиконовых компонентов составляло 20 секунд.
В ходе демонстрации технологии LSR была отлита двухкомпонентная винная пробка. |
Важно для экструзии
Новая технология также имеет важное значение для экструдированных силиконов. Существует несколько применений экструзии, хотя «вся эта технология является совершенно новой для рынка», — сказал Трумм PlasticsToday.
«Движущей силой этой технологии экструзии является экономия энергии, лучшая стабильность профиля и низкотемпературное отверждение, что позволяет производить соэкструдированные/покрытия из устойчивых к низким температурам полимеров, лекарств или электроники», — сказал Трумм.
Разработка важна из-за растущего использования силиконов из-за их уникального профиля:
- Термостойкость выше 392ºF,
- Эластичность при температурах ниже -76ºF,
- Хорошая стабильность к старению и атмосферостойкость, а также
- Биоинертность.
Трумм считает, что большую роль на медицинском рынке в сфере экструзии получат лекарственные препараты, интегрированные в силикон.
В процессе экструзии время воздействия УФ-излучения для отверждения может составлять всего 0,5 секунды, в зависимости от скорости линии и интенсивности УФ-излучения. |
404 Не найдено | Фройденберг Медикал EN
Фройденберг — Инновации вместеМедицинский
Поиск
- Филиалы
- Freudenberg Medical United States
- Freudenberg Medical Europe
- Freudenberg Medical China
- VistaMed
- Hemoteq
- Cambus Medical
- Главное меню
- Компания
- О нас
- Инновации
- Руководящие принципы
- Корпоративная ответственность
- Глобальные местоположения
- Карьера
- Наши люди и культура
- Наш подход
- Обзор
- Развитие дизайна
- Производственные решения
- Бережливые системы
- Качество и нормативные требования
- Что мы предлагаем
- Материалы и технологии
- Катетеры
- Решения для продуктов
- трубки
- Формование и экструзия
- Сборка и дополнительные операции
- Лекарственное покрытие
- Рынки
- Терапевтические рынки
- Фарма
- Диагностика in vitro
- Новости и ресурсы
- Пресс-релизы
- В новостях
- Отраслевые события
- Брошюры
- Белые бумаги
- Истории успеха
- Видео
- Контакт
Запрошенный документ не найден на этом сервере.

© 2022 Фройденберг Медикал
- Условия
- Политика конфиденциальности
- КАЛИФ. Закон о прозрачности цепочки поставок
- Официальное уведомление
- Карта сайта
Подписывайтесь на нас: LinkedIn Твиттер Ютуб Инстаграм
Двукратное формование vs.Формование | Ресурсы
Литье под давлением — это популярный производственный процесс, который идеально подходит для быстрого создания точных деталей сложной формы без большого количества отходов материала. Общие области применения включают упаковку, автомобильные приборные панели, механические детали, такие как шестерни, и даже популярные детские игрушки.
Под литьем под давлением подпадают многие различные процессы, включая двухэтапное литье и многослойное формование. Эти два процесса похожи, но имеют несколько ключевых отличий — вот что нужно знать инженерам и проектировщикам:
Что такое двухэтапное формование?
Двухэтапное литье, также известное как двойное, многоэтапное или двухэтапное литье, представляет собой подкатегорию литья под давлением, которая позволяет инженерам создавать многокомпонентные или разноцветные детали без добавления дополнительных этапов сборки.
Двухэтапный процесс литья под давлением лучше всего понять с точки зрения различных слоев материалов или цветов, которые создаются машиной для литья под давлением. Первый материал впрыскивается в форму для создания подложки, вокруг которой будет формоваться другой материал или материалы. Подложка затвердевает и охлаждается перед тем, как ее перенесут — вручную, с помощью робота-манипулятора или вращающегося самолета — в другую камеру пресс-формы.
Оттуда форма открывается, и сторона с подложкой поворачивается на 180°, чтобы встретиться с другой камерой формы и соплом для литья под давлением. Как только подложка находится на месте, впрыскивается второй материал, который связывается с подложкой, образуя прочную фиксацию. Когда второй слой остынет, последняя часть выбрасывается.
Инженеры должны знать, что двухэтапное литье под давлением может быть ускорено или замедлено в зависимости от того, как субстрат переносится в другую камеру пресс-формы. Перенос вручную и манипулятором робота занимает больше времени, чем на ротационном самолете, но формование с помощью вращающейся плиты дороже и, как правило, является эффективным вариантом только для крупносерийных производственных циклов.
Кроме того, очень важно, чтобы формы были изготовлены из материалов, которые легко соединяются друг с другом, и чтобы формы были правильно выровнены, чтобы предотвратить деформацию детали.
Преимущества и недостатки двухэтапного формования
Двухэтапное литье пластмасс под давлением — превосходный метод эффективного и рентабельного производства. Этот процесс также позволяет производить очень прочные концевые детали и компоненты.
Общие области применения включают захваты для электроинструментов, петли, герметичные уплотнения и прокладки и многое другое.
С точки зрения дизайна двухэтапное литье предлагает дизайнерам большую гибкость, поскольку этот процесс позволяет создавать сложные геометрические формы и сочетать несколько цветов, что делает детали более эстетичными.
Кроме того, поскольку деталь изготавливается на одном станке и не требуется постобработка, инженеры могут значительно сократить время производства, что, в свою очередь, снижает затраты.Тем не менее, стоит отметить, что первоначальные затраты на двухкомпонентную форму могут быть высокими, а машина для двухэтапного литья дороже, чем стандартная машина для литья под давлением. К счастью, эти затраты часто компенсируются экономией труда и затратами на сборку при крупносерийном производстве.
Что такое многослойное формование?
Многокомпонентное формование, как и двухэтапное литье, представляет собой многоэтапный процесс литья под давлением, в ходе которого производится один конечный продукт из двух или более различных термопластов. Этот процесс идеально подходит для инженеров, которые хотят создавать прочные, функциональные, эстетически привлекательные детали, которые не будут отделяться со временем.
Чтобы начать процесс литья под давлением, инженер отливает подложку из более жесткого материала для литья под давлением. Затем подложку помещают в многоформовочный инструмент или полость многовкладыша внутри того же инструмента. Затем расплавленный формовочный материал выбрасывается в подложку, на нее или вокруг нее. После охлаждения расплавленного материала подложка и наплавляемая форма химически или механически соединяются.Весь процесс многослойного формования может занять всего 30 секунд.
Производственные группы должны помнить, что все термопласты, используемые в процессе многослойного формования, должны быть химически или термически совместимы друг с другом. Совместимость, как правило, не является проблемой для металлических подложек, потому что они могут использоваться с любым пластиковым формованием, но группы разработчиков могут столкнуться с проблемами совместимости при формовании пластика с пластиком. Если подложка и наплавка несовместимы, конечный продукт может быть деформирован или плохо связан.
Однако, если необходимо использовать два пластика с далеко не идеальной совместимостью, команды могут разработать элементы механического соединения детали после ее изготовления, хотя это, вероятно, приведет к более высоким затратам.
Преимущества и недостатки литья под давлением
Многокомпонентное формование и двухэтапное литье под давлением имеют много общих преимуществ. Оба они идеально подходят для быстрого создания прочных, надежных и виброустойчивых деталей со сложной геометрией, но литье под давлением лучше всего подходит для мелкосерийного производства.
По сравнению с двухэтапным формованием, многослойные конструкции также проще в изготовлении, поскольку инженеры могут использовать для проведения этого процесса любую стандартную машину для литья под давлением.
Общие области применения включают эргономичные захваты для ножниц и других инструментов, автомобильную отделку, электронику и даже военную технику.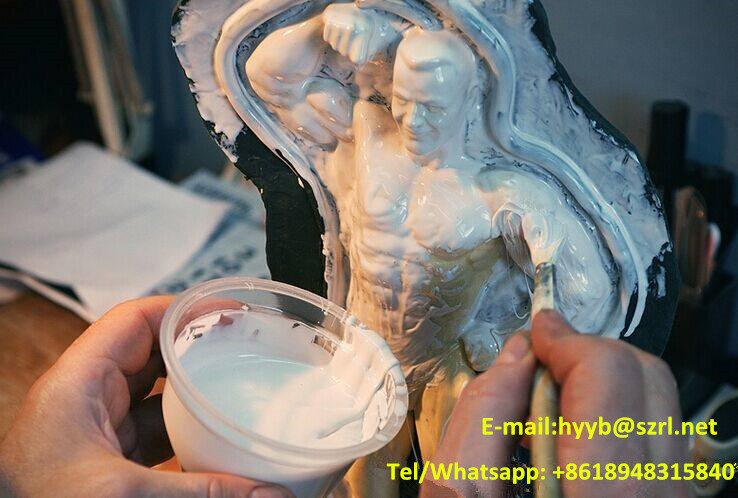
Что касается недостатков, то допуски деталей, изготовленных методом многокомпонентного формования, часто уступают допускам, которые могут быть достигнуты при двухкратном литье под давлением. Также важно помнить, что требования совместимости с пластиком могут ограничивать дизайнеров.
Выбор между двухэтапным формованием и многослойным формованием
Двукратное формование и многослойное формование — простые и эффективные процессы для создания прочных деталей из двух или более материалов или двух или более цветов. Чтобы выбрать между ними, инженеры должны учитывать размер своего производственного цикла.
Двухэтапное формование обычно имеет смысл только для больших производственных циклов, тогда как многослойное формование лучше подходит для небольших производственных циклов.Тем не менее, команды должны проявлять должную осмотрительность и оценивать все критические соображения каждого потенциального производственного процесса в соответствии с их конкретными проектными требованиями, чтобы убедиться, что они делают правильный выбор.
Работа с опытным партнером-производителем, таким как Fast Radius, может значительно упростить процесс принятия решений. Наша команда инженеров, дизайнеров, машинистов и консультантов с многолетним опытом помогает нашим клиентам на всех этапах производственного процесса — от проектирования и прототипирования до производства и реализации.Мы готовы помочь каждой группе разработчиков выбрать правильный производственный процесс и вывести их проект на новый уровень с гибким обслуживанием по запросу по конкурентоспособным ценам и в кратчайшие сроки. Свяжитесь с нами сегодня для цитаты.
Чтобы узнать больше о литье под давлением, а также о других производственных услугах, которые мы предлагаем, ознакомьтесь с соответствующими статьями блога в учебном центре Fast Radius.
Двухкомпонентный молдинг для мягких на ощупь деталей
Двумя наиболее важными факторами при проектировании автомобильных деталей являются стоимость и время выхода на рынок, и они особенно важны, когда речь идет о многоэтапных процессах. Производитель машин для литья под давлением Engel и несколько его партнеров разработали технологию двухкомпонентного литья «Dolphin», позволяющую изготавливать мягкие на ощупь детали на одном прессе за меньшее время, чем при использовании традиционных технологий, и с меньшими затратами. На церемонии вручения наград SPE Automotive Innovation Awards 2012 первые коммерческие компоненты внутренней отделки Dolphin, установленные на Mercedes Actros, вышли в финал в категории «Внутренняя часть кузова».
Мягкий салон в грузовике Mercedes Actros (фото: Daimler)
Процесс Dolphin конкурирует в области автомобильных интерьеров с традиционными методами изготовления мягких на ощупь материалов.В них используются твердые подложки, пенополиуретан и формованные виниловые покрытия, каждое из которых изготавливается в отдельном процессе перед сборкой и не подлежит вторичной переработке. Традиционный метод производства требует отдельного изготовления различных элементов и последующей сборки с помощью пенополиуретана для сварки двух элементов.
Dolphin осуществляется на одной машине для литья под давлением и в один этап. Первое коммерческое применение технологии Dolphin — четыре панели, из которых состоит приборная панель, установленная в кабине грузовика Mercedes-Benz Actros производства Daimler.
Грузовик Mercedes-Benz Actros оснащен первым коммерческим приложением технологии Dolphin (фото: Daimler)
Вот как это работает
Приборная панель Actros также включает нижнюю часть и выдвижные ящики. Он имеет общую ширину более 2 м и доступен в двух цветовых версиях с различными цветовыми сочетаниями: светло-бежевым, черным и серым.
Процесс разработки включал в себя несколько лет сотрудничества между Engel Austria, швейцарским изготовителем форм Георгом Кауфманном, производителем смолы So.ф.тер. (ранее P.Group из Феррары, Италия) и американской компании Trexel, которая поставила технологию производства микроячеистой пены MuCell, являющуюся неотъемлемой частью процесса Dolphin.
Dolphin используется пресс-форма, разработанная Кауфманном, которая устанавливается на вращающемся столе двухплитного пресса Engel Duo Combi M с двумя узлами впрыска. Жесткая опорная конструкция приборной панели отлита из сплава Reblend, PC/ABS от So.f.ter. Форма сначала вращается горизонтально, а на втором этапе термопластичный эластомер Pibiflex от So.f.ter формуется на подложке с использованием процесса MuCell и связывает два материала, формируя мягкий на ощупь слой на структурной подложке. На этапе формования пенопласта на противоположной стороне изготавливается еще одна подложка.
Включение процесса MuCell компании Trexel (который создает микроячеистую структуру материала за счет введения точно отмеренных количеств атмосферных газов) в форму для мягкого на ощупь слоя устраняет необходимость в отдельном производстве различных деталей и их последующей сборке и сварке. по пенополиуретану.Дополнительным преимуществом является то, что детали, вспененные с помощью процесса MuCell, могут быть переработаны в пределах их исходных полимерных групп, в отличие от изделий из химически вспененного пластика.
Поперечное сечение комбинированных материалов, используемых в этом применении процесса Dolphin (фото: Trexel)
Готовая деталь Dolphin представляет собой многослойную конструкцию из подложки, сердцевины из микропористой пены и мягкой на ощупь кожи. Можно использовать текстурированные вставки, чтобы придать поверхности вид зернистой кожи.
Переработка на заводе и по окончании срока службы автомобиля облегчается за счет использования (в основном) структуры полиэфирной смолы и отказа от термореактивной полиуретановой пены, обычного компонента литых деталей. В процессе Dolphin нет брака, а литники могут быть переработаны в продукт (носитель) в качестве модификатора ударопрочности.
Помимо технологии, Dolphin предлагает экономические преимущества, которые отличают его от конкурирующих процессов. К ним относятся снижение капитальных вложений в формы и оборудование, поскольку для изготовления требуется только одна формовочная ячейка. Партнеры проекта оценивают достижимость экономии от 30% до 40% от общей стоимости системы; нет разделения между прямыми и косвенными затратами из-за очень разных методов производства. Процесс Dolphin может быть переведен на всех OEM-производителей.
Производство с одной ячейкой обеспечивает упрощенный контроль процесса, меньшее количество рабочих, меньшую занимаемую площадь, отсутствие вторичных процессов, таких как обрезка и сборка, а также более эффективную поставку и обработку сырья.
www.trexel.com
Двухкомпонентный (2-C)
Двухкомпонентные клеи представляют собой 100% твердые системы, стабильность при хранении которых достигается за счет разделения реакционноспособных компонентов. Они поставляются как
«смола» и «отвердитель» в отдельных контейнерах. Важно соблюдать предписанное соотношение смолы и отвердителя, чтобы
получить желаемое отверждение и физические свойства клея.Два компонента смешиваются вместе для образования клея незадолго до
применение с отверждением, происходящим при комнатной температуре. Поскольку реакция обычно начинается сразу после смешивания двух компонентов, вязкость смеси
адгезия увеличивается со временем до тех пор, пока клей больше нельзя будет наносить на подложку, или прочность сцепления не уменьшится из-за уменьшения смачивания
подложка. Доступны рецептуры с различной скоростью отверждения, что обеспечивает различное рабочее время (срок службы) после смешивания и скорость набора прочности.
после склеивания.Окончательная прочность достигается через несколько минут или недель после склеивания в зависимости от состава. Клей необходимо очистить от смешивания и нанесения
оборудования до того, как отверждение достигло точки, когда клей больше не растворяется. В зависимости от срока службы двухкомпонентные клеи можно наносить
шпатель, валик или лента, распылитель или валик.
Сборки обычно фиксируются до тех пор, пока не будет достигнута достаточная прочность для дальнейшей обработки. Если более высокая скорость
отверждение (наращивание прочности) желательно, для ускорения отверждения можно использовать тепло.Это особенно полезно, когда детали необходимо обрабатывать быстрее после
требуется склеивание или дополнительный срок службы, но более медленная скорость нарастания прочности не может быть обеспечена. После отверждения двухкомпонентные клеи обычно становятся прочными.
и твердый с хорошей температурой и химической стойкостью.
Двухкомпонентные клеи можно смешивать и наносить вручную для небольших работ. Однако это требует значительной осторожности, чтобы обеспечить правильное соотношение
компонентов и достаточное перемешивание для обеспечения надлежащего отверждения и производительности.Обычно при ручном смешивании также возникают значительные отходы. Как результат,
поставщики клея разработали упаковку, которая позволяет хранить компоненты отдельно друг от друга, а также предоставляет средства для дозирования смешанного клея,
например бок о бок шприцы, концентрические картриджи. Упаковка обычно вставляется в ручку аппликатора, и клей распределяется через
одноразовая насадка для смешивания. Правильное соотношение компонентов поддерживается за счет конструкции упаковки, а правильное смешивание обеспечивается использованием
смесительная насадка.Клей можно отливать из этих упаковок несколько раз при условии, что время между применениями не превышает срока годности клея. Если
срок службы превышен, необходимо использовать новую смесительную насадку. Для более крупных применений доступно дозирующее оборудование для дозирования, смешивания и дозирования клея.
расфасованы в контейнеры от кварт до бочек.
Четыре основных типа двухкомпонентных клеев включают:
- Эпоксидные смолы
- Метилметакрилаты
- Силиконовые клеи
- Уретаны
1.Эпоксидные смолы
Двухкомпонентные системы на основе эпоксидной смолы являются наиболее широко используемыми конструкционными клеями. Они могут быть включены в состав систем быстрого отверждения за 2-5 минут. срока службы, которые дают жесткие линии скрепления, которые несколько хрупкие. Системы с более длительным сроком службы обычно содержат добавки для обеспечения гибких или прочных линий склеивания. Два
Компонентные эпоксидные клеи используются для склеивания металла, пластика, пластика, армированного волокном (FRP), стекла и некоторых каучуков.
2. Метилметакрилаты
Метилметакрилатные (ММА) клеи могут обеспечить более быстрое наращивание прочности, чем эпоксидные клеи, и более устойчив к маслу на подложке.Клеи ММА используются для склеивания пластмасс друг с другом и для склеивания металлов с пластмассами. Классические приложения для этого тип клея в автомобильной промышленности и в вагоностроении.
3. Силиконовые клеи
Двухкомпонентные силиконы обычно используются для сборки производственных линий, т.е. в электронной и электротехнической промышленности, а также в производстве
бытовой техники, в автомобильной промышленности и для производства окон. Свойства отверждения аналогичны однокомпонентным силиконам, отверждаемым влагой.Два
компонентные силиконы используются вместо однокомпонентных силиконов, когда требуется толщина клеевой пленки более 0,25 дюйма (6 мм).
требуется или для больших площадей склеивания. Этот тип силиконового клея также используется, когда имеющаяся влажность воздуха недостаточна для полной фиксации.
отверждение однокомпонентного силикона.
4. Уретаны
Двухкомпонентные уретановые клеи могут иметь широкий диапазон свойств отверждения, начиная от мягкости и эластичности, на жесткие и эластичные, на твердые и жесткие.Они используются для склеивания материалов с различной гибкостью или различными коэффициентами термического расширения, в том числе стекло к металлу, армированный волокном пластик (FRP) к металлу и алюминий к стали.
Для получения дополнительной информации о клеях химического отверждения посетите:
(PDF) Двухкомпонентное микролитье под давлением для изготовления MID
выстрел, и во втором выстреле эти детали были отформованы другим материалом во второй полости. из
форма.
Материалы и метод
Для исследования прочности сцепления двух
различных пластиковых материалов использовалась тестовая геометрия стержня на растяжение 2k
(показана на рис. 3). Для изготовления демонстрационного образца MID
тестовая геометрия была выбрана из промышленного продукта
(обсуждается позже). Пластмассовые материалы, использованные для исследований
, перечислены в таблице 1. Для селективной металлизации
использовалась пара материалов PEI100 и Noryl GTX810
из-за их пригодности для селективной металлизации
, обнаруженной в предыдущих исследованиях.
3
Результаты и обсуждение
Двумя важными вопросами для производства MID методом литья 2k
являются сцепление полимер-полимер и качество поверхности раздела полимер-
полимер. Экспериментальное исследование
показывает, что связь полимер-полимер в двухкомпонентном формовании
определяется многими факторами, перечисленными на рис. 4. Подробное обсуждение факторов и их влияния можно найти в другом месте.
1
Помимо вышеупомянутых факторов, последовательность нанесения материала
при формовании 2k (при которой материал
формуется первым) имеет большое значение для склеивания двух материалов
.На рис. 5 показана прочность сцепления различных комбинаций материалов
в зависимости от их последовательностей выстрелов
, найденных в ходе экспериментального исследования (параметры процесса литья под давлением
для пластиковых материалов перечислены в таблице 1
). Это явление может быть объяснено температурой поверхности раздела
между частью вкладыша первой порции и
полимерным расплавом второй порции во время формования 2k.
1
Для достаточно хорошей адгезии
температура поверхности раздела
должна быть достаточно высокой, чтобы два полимера могли расплавить
вместе и образовать связь на границе раздела. При отсутствии
достаточно высокой температуры поверхности раздела между двумя полимерами не будет
связи.
Одним из важных аспектов двухкомпонентного литья является отношение
между прочностью связи полимер-полимер и поверхностью раздела
между двумя материалами. Для успешной работы MID требуется достаточное сцепление между двумя материалами; с другой стороны,
также требуется четкий и четко определенный интерфейс для полной селективности в процессе металлизации.Сравнительный анализ
между исследованием поверхности раздела и
исследованиями прочности связи полимер-полимер (проведенный
авторами и представленный в ссылке 1) выявил дилемму
между двумя аспектами параметров качества для 2k
формованных пластиковых деталей. На рис. 5 показано, что прочность связи
между поликарбонатом (ПК) и полиэфирэфир-
кетоном (PEEK) составляет 26 МПа, когда поликарбонат формован в первом впрыске
, и та же комбинация материалов имеет прочность связи
0 МПа при обратной последовательности выстрелов
(PEEK в первом выстреле). Исследование поверхности раздела показывает, что эта пара материалов
имеет лучшее качество поверхности раздела, когда сначала формуется PEEK
.
1
Это означает, что последовательность выстрелов, которая
имеет низкую прочность сцепления, дает
четкую и хорошо различимую границу раздела двух полимеров. То же наблюдение
было сделано с комбинациями полиэфиримида (PEI) и
PEEK.
Когда полимерная пара имеет слабую адгезию, граница раздела
содержит зазор (четкая разделительная линия с
трещинами) в несколько микрометров между двумя полимерами
.Этот микрозазор между двумя полимерами делает границу резкой и различимой после
литья под давлением. Однако, когда два полимера
прочно слипаются, зазор между двумя материалами уменьшается или
исчезает (пример комбинации материалов PEEK-PC
представлен на рис. 6). На рис. 6а,
Для более прочного соединения двух полимеров температура поверхности раздела
во время второго впрыска должна быть настолько высокой
, чтобы поверхность вкладыша (первый всплеск) расплавилась,
и два полимера могли смешаться вместе.
2
С другой стороны,
для геометрической правильности и качества интерфейса
2k детали, вставка должна выдерживать тепло и
давление второй порции расплава, чтобы она могла сохранять свою
форму и сохранить геометрию неискаженной. В экспериментальном случае
температура теплового изгиба ПК на
ниже, чем PEEK (температура теплового изгиба для ПК
и PEEK составляет 146 и 315 uC соответственно).Когда
PEEK используется в качестве материала первой порции, он может выдерживать
условия литья под давлением второй порции PC,
Таблица 1 Список пластиковых материалов, использованных в экспериментах*
T
T
MO
, UCT
, UCT
, UCP
, Бар V
, Бар V
INMEC
, MMS
21
PEEK VICTREX 150GL30 VICTREX 180 380 2210 112
PEI ULTEM 2312 GE 160 390 2210 112
PEI ULTEM 1000 GE 160 390 2210 112
PC Lexan 500R GE 90 300 2210 112
PS POLYSTYROL 143E BASF 60 240 2210 112
PPEZPA NORYL GTX810 GE 120 280 2210 112
ABS Terluran 997ve BASF 60 250 2210 112
*PEEK, полиэфирэфиркетон; PEI, полиэфиримид; ПК, поликарбонат; ПС, полистирол; PPEzPA, смесь полифениленового эфира; ABS,
акрилонитрилбутадиенстирол.