Полипропиленовые трубы армированные стекловолокном для отопления: выбор и монтаж
Трубы полипропиленовые армированные стекловолокном
В последний десяток лет применение полипропилена в отоплении стало наиболее популярным способом монтажа водяных систем. И неудивительно, ведь удобство, быстрота проведения работ, а главное, — низкая стоимость материалов и работ поставили трубы ППР вне всякой конкуренции. Кроме того, здесь устранено самое слабое место систем из металлопластика – металлические фитинги, которые отличаются приличной ценой, а при эксплуатации подводят чаще всего. Пластиковые фитинги и полипропиленовые трубы для отопления после сборки становятся единым целым, служат надежно и долговечно.
Виды труб ППР
Трубопроводы из этой пластмассы появились в Европе еще в 80-е годы, изначально они применялись только для прокладки трубопроводов для холодной воды. На горячее водоснабжение и отопление пластиковая труба не годится, и вовсе не оттого, что расплавится от высокой температуры.
Дело в том, то линейное тепловое расширение данного материала достаточно велико, например, простая ППР труба диаметром 20 мм при перепаде температур 50ºС на каждых 10 м длины прибавит еще 65 мм. Это очень много, компенсировать такое удлинение невозможно никакими методами.
Поэтому позже были изобретены полипропиленовые армированные трубы для отопления и ГВС, чьи показатели теплового расширения значительно ниже. Значения линейного удлинения труб из металла, различных пластмасс и с армировкой представлены в таблице.
Уменьшение теплового расширения достигнуто благодаря введению в тело пластмассовой трубы армировки из тонколистового алюминия или стекловолокна. Эти материалы имеют более низкий коэффициент расширения и сдерживают увеличение размера пластика. Соответственно, можно разделить типы полипропиленовых труб на группы:
- обычная цельнополимерная труба, применяемая для холодного водоснабжения;
- трубы ППР для ГВС и отопления, стабилизированные алюминием;
- полипропиленовая труба, армированная стекловолокном, также применяемая для горячей воды температурой до 100ºС;
- новинка: используемые для тех же целей трубы, армированные базальтовым волокном.
Примечание: армированный полипропилен имеет маркировку «STABI», оттого в народе его прозвали «штабированным».
Все эти изделия пришли к нам из Европы несколько позже, но уже прочно завоевали рынок. Особенно популярны продукты с алюминиевой вставкой.
Спустя некоторое время в качестве армирующего слоя стали применять такой материал, как стекловолокно, чей коэффициент расширения немного больше, нежели у алюминия. Вы спросите: а какой смысл в таком нововведении, если есть изделия STABI, чья надежность проверена годами? Ответ прост: удешевление материала и упрощение пайки стыков.
Труба из стекловолокна
Особого внимания заслуживают чешские полипропиленовые трубы бренда EKOPLASTIK, где в качестве армирования из стекловолокна применено базальтовое волокно. Этот материал практически не расширяется при нагреве и введен в тело трубы по новейшей технологии — в сплаве с пластмассой. Результат впечатляющий, — по сравнению с цельнополимерным продуктом изделие с базальтовым волокном при нагреве удлиняется в три раза меньше.
Рекомендации по выбору
Современный рынок насыщен полимерными изделиями различных производителей. Условно их можно разделить на «наших», турецких и европейских. В таком же порядке растет качественное исполнение и цена на полипропиленовые трубы, хотя в последнее время некоторые российские предприятия выпускают трубопроводы, не уступающие по качеству турецким. Поэтому здесь каждый должен решить для себя сам, продуктами какой фирмы ему пользоваться. Что же до стоимости разных типов труб, то самые доступные для прокладки отопления – это с армированием из стекловолокна. Дороже всех – изделия с базальтовой вставкой.
Следует отметить, что не всегда стоит стремиться к дешевизне. Если ваша армированная труба прокладывается в открытом взгляду, доступном месте, то есть смысл сэкономить на стоимости материала. Это касается обычных систем отопления и горячего водоснабжения, монтируемых открытым способом внутри помещений.
Другое дело, когда стояки уходят в подвал или на чердак, а то и вовсе закладываются внутрь цементной стяжки. В таком случае заводской брак или недоработки монтажников устранить будет очень сложно, не говоря уже о последствиях. Поэтому для прокладки в недоступных местах или закрытом пространстве лучше применить качественные трубы из полипропилена для отопления с армирующим слоем из алюминия.
Для устройства теплых полов, чья стоимость и ответственность выполнения работ значительна, лучше взять трубы со слоем базальтового волокна. Чешский производитель EKOPLASTIK декларирует срок их службы до 50 лет.
Прежде чем покупать выбранный материал, обратите внимание на технические характеристики полипропиленовых труб, особенно если бренд производителя вам незнаком. Имеют значение 3 параметра: пропускная способность, выражаемая диаметром трубы, максимальная рабочая температура и давление.
Первый параметр определяется заблаговременно, это отдельная тема для разговора. Но следует понимать, что вода течет внутри трубы, а не снаружи, оттого изначально надо определить необходимый внутренний диаметр. На изделии же указывается наружный размер и толщина стенки. Самые распространенные диаметры полипропиленовых труб – это 20, 25, 32, 40 мм, хотя тот же EKOPLASTIK предлагает линейку размеров до 110 мм включительно.
Важно! Заблаговременно узнайте рабочую температуру и давление в ваших сетях и подбирайте трубы по ним. Ориентируйтесь на то, что высокая температура бывает в отопительных системах, а давление – в сети ГВС.
Несколько слов о цвете трубопроводов, мы знаем белый и серый. В действительности качество исполнения и срок службы не зависят от цвета, на это не стоит обращать особое внимание, хотя белый – конечно же, красивее.
Немного о монтаже
Процедура настолько проста, что отопление из полипропилена не паял, наверное, только ленивый. Для выполнения работ нужны следующие инструменты и приспособления:
- специальный паяльник с набором насадок под разные диаметры;
- ножницы для правильной обрезки трубы;
- приспособление, которым зачищают армирующий слой из алюминия, когда монтируются «штабированные» трубы;
- матерчатые перчатки.
Совет. Не следует игнорировать матерчатые перчатки, особенно новичкам. Температура паяльника достигает 300 ºС, а поверхности нагрева достаточно обширны. Лучше защитить руки, чтобы не получить ожогов.
Паяльник для соединения полипропиленовых труб
Монтаж выполняется в такой последовательности: сначала производится разметка и отрезка ножницами участков труб требуемой длины и раскладка их в соответствии со схемой. Перед включением к паяльнику прикрепляют насадку соответствующего диаметра либо сразу несколько насадок. Поскольку для соединения полипропиленовых труб необходимо пользоваться паяльником, разогретым до температуры не ниже 260 ºС, то его лучше включить и настроить заранее. Погасший светодиод на приборе покажет, что он готов к работе.
Места соединения на трубе и фитинге надо обязательно очистить от пыли и грязи, это очень важно. При наличии армирующего слоя из алюминия его придется снять с помощью специального приспособления для зачистки на длину стыка. Так как сварка полипропиленовых труб армированных стекловолокном или базальтом не требует зачистки, то их достаточно просто протереть от пыли.
Следующий этап – разогрев деталей, для чего трубу и фитинг одевают с двух сторон на насадку и выдерживают определенное время, зависящее от диаметра изделий. Для размера 20 мм это время 6 сек, 25 мм – 7 сек, 32 мм – 8 сек и 40 мм – 12 сек. Передерживать нельзя, иначе пластик «потечет» при стыковке и закроет половину проходного сечения. Затем детали снимают с насадки и осуществляют соединение полипропиленовых труб, продержав стык руками секунд 5—10.
Важно!
При снятии деталей с насадки паяльника и последующей стыковке не допускается их вращать вокруг своей оси.
Подробности процесса пайки труб можно посмотреть на видео.
Заключение
На практике выбор и монтаж полипропиленовых труб осуществить достаточно просто, тут главное, — четко определить параметры для правильного подбора материалов. Перед пайкой же не помешает немного потренироваться на коротких отрезках труб, сделав несколько пробных соединений с фитингами.
Зачистка для полипропиленовых труб. Ручные инструменты для зачистки
Трубы из полимерных материалов могут использоваться в разы дольше металлических аналогов. Но их срок службы во многом зависит от того, насколько грамотно были произведены монтажные работы. Одним из условий длительной и беспроблемной эксплуатации полипропиленовых труб является их правильная зачистка, так как неровности на срезе и заусенцы мешают качественному соединению. Уже на этапе планирования укладки полипропиленового трубопровода необходимо разобраться в том, зачем нужна такая процедура и с помощью каких инструментов её осуществляют. Особое внимание следует уделить трубам с армирующим слоем.
Зачистка края трубы — обязательная процедура перед соединением элементов трубопровода
Что дает армирование полипропиленовых труб
Положительные свойства армированных полипропиленовых труб достигаются за счёт наличия защитного слоя. В трубах, использующихся в домашних условиях, его толщина не превышает 0,1-0,5 мм. Армирование необходимо для:
- Снижения температурного воздействия на полимер. Вообще полипропиленовые трубы неплохо выдерживают высокие температуры. Верхним порогом является 95 градусов. По идее, для домашних систем отопления и водопровода этого должно быть достаточно. Но в некоторых ситуациях, в том числе и аварийных, температура транспортируемой жидкости может подниматься. Это вызывает деформации участков трубопровода. Алюминиевая фольга повышает способность трубы выдерживать высокие температуры и предотвращает разрывы системы.
- Компенсации теплового расширения. Главным недостатком полипропиленовых труб является существенное расширение при перепадах температур. При резком расширении, а затем – сужении, полипропилен теряет свои пластические качества и постепенно растрескивается. Это свойство не лучшим образом отражается на сохранности труб без армирования.
Но армировка также несколько затрудняет сварку полипропиленовых трубопроводов, поэтому при монтаже просто необходимо прибегнуть к зачистке трубы. Зачистка в случае с таким типом труб представляет собой удаление тонкого слоя алюминиевой фольги.
Армирующий слой придает трубе прочность, но для качественной сварки его нужно обрабатывать
Способы зачистки полипропиленовых труб
Существует несколько разновидностей зачистки, в зависимости от типа армирующего слоя.
Внешний слой. Если алюминиевая фольга представляет собой внешний защитный слой полипропиленовой трубы, она помешает процедуре соединения с фитингом. При монтаже плавится весь отрезок трубы, входящий в фитинг. Если труба не будет зачищена, произойдёт следующее: расплавленный алюминий не сварится с расплавом полипропилена, и соединение будет разгерметизировано сразу же после пуска системы.
Внутренний слой. Хоть алюминий, находящийся между полипропиленовыми слоями, не будет задействован во время сварки, зачистные работы всё равно стоит провести. Зачистка армирующей прослойки необходима для того, чтобы алюминий не вступал в контакт с водой. При любом скачке потенциалов внутри трубопровода могут начаться электрохимические процессы, которые в итоге приведут к полному разрушению алюминиевого слоя.
Без зачистки можно соединять только трубы, армированные стекловолокном
Полезный совет! Армирующий слой алюминия бывает цельным и перфорированным. Если стоит задача выбрать между этими двумя вариантами, следует всё же обратиться к последнему. Перфорированный внутренний слой фольги обладает лучшим сцеплением и не требует клея. Зачистка перфорированной армировки – более быстрый процесс.
Армировка стекловолокном. В данном случае зачистка для полипропиленовых труб не применяется. Тонкая сетка стекловолокна располагается между слоями полимера, не испытывает воздействие влаги и не контактирует с фитингом. Надёжное крепление стекловолоконных полипропиленовых труб можно получить и без дополнительных работ. Но коэффициент теплового расширения у таких конструкций будет выше, чем у труб, армированных алюминием.
Какие бывают инструменты для зачистки полипропиленовых труб?
Инструмент, с помощью которого можно произвести зачистку трубы, может быть ручным или механическим. Ручные приспособления – это оптимальный вариант для проведения зачистных работ в домашних условиях. Существуют такие разновидности зачистных инструментов для полипропиленовых труб:
- зачистки для наружного слоя. Для удаления внешнего слоя армирующей фольги используются муфты с лезвиями в середине. Зачистные муфты оснащены удобными ручками, что делает рабочий процесс быстрым и простым. Ручки также могут быть съемными;
- торцеватели. Лезвия в торцевателях размещены не на поверхности металлической муфты, а на её внутреннем торце. На инструмент надевается труба и проворачивается несколько раз. Уже через минуту получится идеальный срез, и полипропиленовая труба полностью готова для сварки. Такие инструменты используют и для обработки прочих типов пластиковых труб, в том числе без армирующего слоя.
- специальная насадка на электродрель — шейвер. В продаже можно найти приспособления, позволяющие зачищать одновременно и внешний, и внутренний слои трубы. Для разных типов армировки подбираются особые насадки, различные по диаметру.
С небольшим объемом работы вполне можно справиться обычным ручным приспособлением
Использование зачистных насадок на дрель необязательно: если предстоит выполнить малый объем работы, вполне можно справиться и своими руками. Кроме того, мощные дрели и шуруповерты сложны в эксплуатации. Если нет достаточного опыта в обращении с подобным оборудованием, лучше не прибегать к его помощи вообще.
Обратите внимание! Не стоит путать зачистку труб с процессом очистки металлических изделий. Это совершенно другой вид работы, и для него применяется особенное технологическое оборудование.
Также для зачистки и монтажа полипропиленовых труб своими руками пригодятся следующие инструменты:
- строительный или простой карандаш для разметки отрезка трубы, входящего в фитинг;
- рулетка;
- труборез, ножницы или ножовка для резки труб;
- паяльник для полипропиленовых конструкций;
- выбранный зачистной инструмент.
Ровный и гладкий срез полипропиленовой трубы достигается за счёт высоколегированной стали, из которой производятся ножи инструментов для зачистки. Лучше выбирать двусторонний ручной инструмент. Он позволит осуществить зачистку труб разных диаметров.
Зачистка полипропиленовых труб – это несложный технологический процесс, который можно выполнить своими руками без особой подготовки. Не стоит приобретать дорогой инструмент, если требуется подготовка к сварке нескольких изделий. Даже простые стальные приспособления способны обеспечить качественный и аккуратный результат.
Сварка полипропиленовых труб: правила и типичные ошибки
Одним из основных преимуществ полипропиленовых труб специалисты называют возможность легкой сварки и монтажа. Можно собственноручно собрать, модернизировать и отремонтировать трубопровод.
Трубы из полипропилена собираются методом пайки. При нагреве полипропилен становится эластичным, мягким, что позволяет соединять его.
Существует два основных способа стыковки спаиваемых деталей:
• Муфтами;
• Напрямую.
Давайте разберем подробнее каждый из них.
Сварка с помощью муфт
При стыковке деталей при помощи муфт часть расплавляется части трубы по внешней окружности и части муфты — по внутренней. После этого трубы плотно стыкуются. При застывании пластика образуется надежное соединение.
Результат спайки муфтойСварка напрямую
Технология прямой сварки предполагает точную обработку стыков деталей и установку их строго в соответствии осей. Торцы деталей нагреваются и соединяются. Этот метод требует большего опыта и подготовки, нежели муфтовый.
Кроме того, существует способ «холодной» сварки -когда размягчение полипропилена происходит за счет химических реакций.
Оборудование для сварки полипропиленовых труб
Любой из способов горячей сварки требует наличия специального оборудования. Основной прибор— это утюг для сварки. Он состоит из нагревательного элемента и сменных насадок, устанавливаемых на него.
Для стыковой (прямой) сварки используются более сложные утюги, которые включают в себя системы центровки деталей.
Кроме того, потребуются труборез, угольник, рулетка, шейвер для труб и средство для обезжиривания поверхностей.
Процесс сварки труб
Выполняется подготовка к процессу: установка на утюг насадок необходимого размера, нагрев утюга (обычно используется температура 260 градусов), подготовка свариваемых деталей (обрезка, снятие фаски, обезжиривание).
Затем свариваемые детали (например, труба и муфта) одновременно насаживаются на болванки утюга (труба — внутрь, муфта — снаружи болванки).
И здесь мы подходим к очень важному моменту — времени нагрева. Если детали недогреть — они не сварятся должным образом; перегрев же грозит деформацией, что также приведет к некачественной сварке.
Воспользуйтесь таблицей оптимального времени сварки труб в зависимости от толщины стенки для достижения наилучшего результата:
После нагрева детали снимают с болванки и стыкуют. Стык должен произойти за указанное в таблице время. Допустимо производить в течении пары секунд корректировку осей, но ни в коем случае нельзя проворачивать детали относительно друг друга.
Нужно учитывать, что значения в таблице приведены для усредненных условий окружающей среды. Если работы производятся при отрицательной температуре — время нагрева увеличится.
Сварка труб, армированных алюминием
Самым важным моментом в сварке труб с армированием является снятие защитного материала в месте сварки. Также нужно учитывать, что алюминий, как теплоемкий материал, будет забирать часть тепла — потребуется дольший прогрев.
Обычно для зачистки таких труб используется шейвер.
Шейвер для зачистки труб, армированных алюминиемВнутри шейвера содержатся ножи. Шейвер надевают на трубу и вращательными движениями счищают армирование до пластика.
В случае, когда слой алюминия находится в середине трубы, используют торцеватель.
Торцеватель для пластиковых трубТорцеватель отличается от шейвера расположением ножей. При его использовании торец трубы выравнивается, а также на глубину 2 мм вырезается армированный слой.
Распространенные ошибки при сварке полипропиленовых труб
Далеко не всегда получается сделать все идеально — необходимо учесть множество факторов, и только со временем мастер приобретает опыт, позволяющий производить сварочные работы безошибочно.
Но если заранее знать, какие ошибки наиболее типичны — можно избежать их повторения. Давайте рассмотрим их:
• Значительное смещение деталей относительно друг друга после схватывания полипропилена
Смещение деталей во время застывания всегда приводит к нарушению соединения. Образуются слабые места, в которых спайка практически отсутствует. Такое соединение не сможет прослужить долго.
• Недогрев или перегрев свариваемых деталей
При недостаточном нагреве диффузия материала будет недостаточной, чтобы качественно «схватиться», что впоследствии может привести к разгерметизации и протечкам трубопровода в месте такой сварки. При перегреве деталь деформируется: зачастую труба внутри фитинга меняет свой диаметр, как следствие — частые засоры.
• Неровный срез стыкующихся поверхностей
При несоблюдении соосности торцов свариваемых деталей стык происходит в скошенной плоскости. Такая ошибка может стать заметна не сразу, а после монтирования нескольких метров после места такой сварки.
• Недостаточно тщательное снятие армирующего слоя
Армированный слой, который не был зачищен, забирает на себя часть тепла, которое передается трубе в месте стыка — как следствие, недогрев на этом участке и следующие за ним протечки.
• Недостаточно плотная посадка трубы в муфте (фитинге)
При совершении этой ошибки получается недостаточно плотная сварка, которая может подвести в самый неподходящий для этого момент.
• Отсутствие тщательной обработки (обезжиривания)
Обезжиривание — процедура, которой не следует пренебрегать! Загрязнения не позволят материалу схватиться в должной мере, что приведет, опять же, к протечкам. Свариваемые детали необходимо обрабатывать!
В Компании «Технология» Вы всегда сможете найти все необходимое для того, чтобы создать качественную и долговечную водопроводную систему! Ознакомьтесь с нашим ассортиментом полипропиленовых труб и комплектующих.
Производство полипропиленовых трубопроводов, фитингов и пластмасс
Новое поколение полипропилена для промышленности
AlphaPlus® Полипропилен подходит для более широкого спектра химикатов, чем другие материалы для трубопроводов, такие как FRP и CPVC, и может выдерживать температуры от 32 ° F до 200 ° + F в зависимости от области применения.
Эта запатентованная формула смолы AlphaPlus и эксклюзивная экструзия с поточным отжигом также значительно улучшают жесткость при высоких температурах и ударопрочность при низких температурах — намного лучше, чем полипропилен с β-ядрами и стандартный полипропилен. Никакой другой полипропилен не предлагает такого сочетания более длительного срока службы, большей функциональности, повышенной безопасности и низкой стоимости владения.
- Полипропиленовая труба для снятия напряжений: ½ ”- 48”
- Литые полипропиленовые торцевые фитинги: ½ ”- 4”
- Формованные полипропиленовые фитинги для стыковой сварки: ½ ”- 20”
- Сборные полипропиленовые фитинги: 18–48 дюймов
Трубы и фитинги AlphaPlus PP обладают преимуществами по сравнению с другими полипропиленами на рынке:
- Значительное снижение потерь давления благодаря улучшенным гидравлическим свойствам
- Значительно меньший риск отложений твердых частиц благодаря сверхгладким поверхностям
- Возможная экономия за счет увеличения интервалов между чистками
- Более длительный срок службы благодаря повышенной химической стойкости и минимальному риску образования трещин под напряжением
- Безопасный монтаж и монтаж труб благодаря повышенной ударной вязкости даже при низких температурах
- Большой запас прочности за счет улучшения качества сварки
- Повышенная безопасность при сварке труб в труднодоступных местах.
Полипропиленовые трубы AlphaPlus используются в широком спектре отраслей промышленности со специальными потребностями, включая:
- Химический процесс
- Полупроводник
- Целлюлоза и бумага
- Атомная энергетика
- Горное дело
- Подготовка и обработка металлов
- Нефтехимия
- Фармацевтическая
- Водоподготовка
- Продукты питания, напитки, пивоварение.
12 «SDR11 Многослойная полипропиленовая труба Clima ND 315 мм PP-RCT
12 «SDR11 Многослойная полипропиленовая труба Clima Grey ND 315 мм PP-RCT
- Многослойная (трехслойная труба с добавлением стекловолокна в средний слой) Труба
- Цена указана за фут
- Доступен в 20-футовых палках
- Мы можем вырезать изделия меньшей длины по индивидуальному заказу.
Может взиматься плата за резку
Трубопроводы Niron PP-RCT напрямую совместимы с трубами и фитингами Aquatherm
ИНФОРМАЦИЯ О ПРОДУКТЕ
- Торговая марка NIRON идентифицирует полипропилен со случайным сополимером (PP-RCT) система труб и фитингов производства Nupi Americas, изготовленная в соответствии со стандартами ASTM F2389 и CSA B137.11.
- NIRON — это система трубопроводов, используемая для всех видов водоснабжения, включая горячее и холодное питьевое водоснабжение, системы водяного отопления, а также циркуляционные трубы охлажденной воды и градирни.
- Систему можно использовать для больших многоквартирных жилых домов, гостиниц, больниц, торговых центров, церквей, школ, спортзалов, круизных лайнеров и торговых судов.
- Система NIRON также используется в промышленных установках для транспортировки сжатого воздуха и некоторых широко используемых химических веществ.
- Фитинги Niron совместимы с системами трубопроводов PPR и PP-RCT.
- Может использоваться с большинством марок полипропиленового PPR, труб, фитингов и оборудования для сварки плавлением, включая Aquatherm.
Спецификация многослойных полипропиленовых труб Clima
РАСШИРЕННЫЙ МАТЕРИАЛ PP-RCT
Niron изготовлен из 100% бета-материала PP-RCT, высококристаллической формы полипропилена
, которая позволяет в два раза превышать номинальное давление
при более высокие температуры и превосходная стойкость к хлору.
АБСОЛЮТНАЯ НАДЕЖНОСТЬ
Производимая с 1982 года система NIRON была продана на всех 5
континентах. Было отгружено более 150 000 миль труб и фитингов
, что полностью удовлетворило заказчиков и установщиков.
СЕРТИФИЦИРОВАННОЕ КАЧЕСТВО
Система NIRON получила самые престижные международные сертификаты качества
, но для нас качество
означает полное удовлетворение потребностей клиентов. Это достигается исключительно за счет поставки
продуктов, функции которых полностью соответствуют требованиям приложений
.
ПОЛНЫЙ АССОРТИМЕНТ
Трубы и фитинги NIRON — от 1/2 до 24 дюймов — доступны
с широким спектром фитингов и способов соединения, чтобы решить любую проблему установки
.
НИЗКОЕ ТЕПЛОВОЕ РАСШИРЕНИЕ
Это достигается благодаря новым композитным трубам NIRON FG и NIRON
CLIMA, произведенным с использованием инновационной технологии соэкструзии.
Их внутренний слой изготовлен из сополимера ПП, армированного стекловолокном, чтобы уменьшить линейное тепловое расширение
до 73%.
СКОРОСТЬ УСТАНОВКИ
Несомненно, самое большое преимущество NIRON заключается в скорости установки.
Благодаря простым способам соединения время установки
может быть сокращено от 30 до 50%.
ОТСУТСТВИЕ КОРРОЗИИ И НАКИПИ
Полипропилен плохо проводит электричество, поэтому система NIRON не подвержена коррозии.
Кроме того, благодаря гладкой внутренней поверхности исключается образование известкового налета.
ЭКОНОМИЯ ЭНЕРГИИ
Низкая теплопроводность полипропилена
позволяет значительно экономить энергию
по сравнению с металлическими материалами и снижает стоимость изоляции
.
УСТАНОВКА С НИЗКИМ ШУМОМ
Шумопоглощающие свойства и эластичность материала
смягчают шум и вибрации, вызванные потоком воды
и эффектом гидравлического удара.
УСТОЙЧИВОСТЬ К ЭКСТРЕМАЛЬНЫМ ТЕМПЕРАТУРАМ И ТЕРМИЧЕСКОМУ РАСШИРЕНИЮ
Система NIRON испытана на устойчивость к температурам вплоть до кипящей воды и условиям замерзания. Трубопровод
NIRON FG позволяет снизить тепловое расширение до уровней, аналогичных медным трубам.
СОПРОТИВЛЕНИЕ АБРАЗИИ
Высокая стойкость труб NIRON устраняет проблемы эрозии и обеспечивает высокую скорость потока воды.
БЕЗ ТОКСИЧНОСТИ
Система NIRON абсолютно нетоксична и соответствует национальным и международным стандартам здравоохранения
.
ГАРАНТИЯ 30 ЛЕТ
На систему NIRON распространяется страхование гражданской ответственности в соответствии с
Gas Welding — обзор
16.3.1.12 Газовая сварка и резка
Газовая сварка осуществляется пламенем, получаемым путем сжигания примерно равных объемов кислорода и ацетилена, которые подаются при одинаковом давлении из газовых баллонов в сварочную горелку. Температура пламени составляет приблизительно 3100 ° C, что достаточно для плавления стали и других металлов.При необходимости присадочный металл добавляется путем подачи стержня вручную в переднюю кромку сварочной ванны при перемещении горелки вдоль стыка. Продукты горения обеспечивают достаточную защиту от атмосферы при сварке стали. При сварке других металлов, таких как чугун, нержавеющая сталь, алюминиевые и медные сплавы, используются флюсы для очистки и защиты металла от окисления.
Оборудование Сварочная горелка имеет две ручки управления с накаткой, которые регулируют расход кислорода и ацетилена, так что получается нейтральное или слегка окисляющее или восстанавливающее пламя, в зависимости от области применения.Горелка имеет ввинчиваемое сопло из набора сопел с отверстиями разного диаметра, которые обеспечивают соответствующий размер пламени и, следовательно, необходимую подводимую теплоту для конкретного металла и толщины свариваемого материала. Шланги для кислорода и топливного газа подсоединяются между сварочной горелкой и газовыми баллонами, при этом газы проходят через пламегасители и регуляторы давления. Гасители обратного пламени — это предохранительные устройства, которые предотвращают возврат пламени в цилиндры в случае обратного возгорания.Для использования в мастерских газовые баллоны обычно устанавливаются парами на тележке, которую можно перемещать туда, где это необходимо.
Присадочный металл и флюсы Химический состав присадочных металлов определен в BS 1453: 1972 и включает ферритные стали, чугун, аустенитные нержавеющие стали, медь и медные сплавы и алюминиевые сплавы. Ферритные стали не требуют использования флюса, но для других материалов доступны запатентованные флюсы.
Области применения Газовая сварка используется в основном для ремонта и технического обслуживания, особенно при ремонте кузовов автомобилей и сельскохозяйственных орудий, хотя постепенно ее заменяет небольшое оборудование для сварки TIG и MIG.Газовая сварка в определенной степени используется для работы с листовым металлом (например, для обогрева и вентиляции воздуховодов) и до сих пор используется для прокладки корневых проходов в трубах, где она особенно полезна для перекрытия зазоров.
Два применения, в которых газовая сварка имеет явные преимущества по сравнению с другими процессами, — это сварка и ремонт отливок из серого чугуна и наплавка дорогими сплавами. Отливки из серого чугуна можно успешно сваривать, используя высокие температуры предварительного нагрева до 600 ° C и газовую сварку с присадочными стержнями из чугуна.Осаждение дорогостоящих износостойких сплавов, таких как кобальт-хромовольфрамовые сплавы или сплавы на основе карбидов хрома или вольфрама, можно проводить с минимальным плавлением основного металла, так что разбавление осажденного сплава и последующее уменьшение исключается износостойкость. Газовая сварка также успешно применяется в ювелирном производстве с миниатюрными горелками и небольшими газовыми баллонами.
Ацетилен — единственный горючий газ, пригодный для газовой сварки из-за его благоприятных характеристик пламени как при высокой температуре, так и при высокой скорости распространения.Другие горючие газы, такие как пропан, пропилен или природный газ, выделяют недостаточно тепла для сварки, но используются для резки, пайки горелкой и пайки. Они также используются для газовой правки деформированных деталей и для предварительного нагрева перед сваркой и последующего нагрева после сварки.
Газовая резка Газовая резка, иногда называемая газовой резкой или кислородной резкой, включает в себя активное экзотермическое окисление разрезаемой стали, когда материал был предварительно нагрет пламенем кислородно-топливного газа до температуры воспламенения около 900 ° С.Оборудование для газовой резки такое же, как и для сварки, за исключением того, что требуется специальная режущая насадка. Сопло имеет внешнее кольцо с отверстиями, через которые подается смесь подогреваемого газа, и центральное отверстие, через которое проходит струя кислорода. В результате экзотермической реакции окисления стали образуется жидкий шлак из оксида железа, и через несколько секунд, в зависимости от толщины металла, происходит пробивка сечения. Оксид железа и расплавленный металл удаляются из разреза потоком кислорода. Перемещение резака по заготовке обеспечивает непрерывное резание, резаком можно управлять вручную или с помощью моторизованной каретки.Таким способом можно резать сталь толщиной до 300 мм.
Стойкие к окислению стали, такие как нержавеющая сталь, можно резать специальными методами, включая введение железного порошка или других запатентованных порошков в поток кислорода. Эти порошки вступают в реакцию с тугоплавкими оксидами хрома, снижают их температуру плавления и повышают текучесть, что позволяет производить резку. Для получения дополнительной информации обратитесь к ссылке 40.
Нержавеющая сталь, цветные металлы и сплавы обычно режут с помощью процесса плазменной резки, который не требует экзотермической реакции.
Возможна ручная газовая резка, а точность резки может быть улучшена за счет использования небольшого колеса, установленного на резак. Колесо может быть автономным или моторизованным. Для общей резки и профилирования (в том числе снятия фаски на кромках листов) обычно используется механизированная резка. Для механизированной резки распространены электронные отслеживающие устройства, которые состоят из фотоэлемента, который повторяет контур чертежа и направляет режущее сопло с помощью приводных двигателей, которые регулируют движение каретки и траверсы, к которой прикреплен резак.
Доступны станки для резки с числовым программным управлением, которые используют программы, хранящиеся или перфорированные на магнитной ленте, которые посылают соответствующие сигналы на приводные двигатели.
Низкотемпературная пайка титана с использованием присадочных сплавов на основе алюминия
Пайка титана с использованием присадочных сплавов с низкой температурой плавления является предпочтительным выбором с точки зрения стоимости и сохранения его механических свойств. Однако пайка титана при низкой температуре все еще является проблемой, особенно в отношении присадочных сплавов на основе алюминия.В течение последних лет было разработано несколько методов пайки и наполнителей на основе алюминия для удовлетворения промышленных требований; некоторые из них могут соответствовать некоторым из этих требований. Использование ультразвука при пайке в последнее время привлекло повышенное внимание, что помогает сократить время и необходимость в специальной среде для пайки, что впоследствии снижает стоимость и увеличивает применимость. В обзоре представлена пайка титана ниже температуры превращения с использованием промышленных и экспериментальных наполнителей на основе алюминия различного состава; включая процедуры традиционной и ультразвуковой пайки.Соответственно, исследуется влияние условий пайки и легирующих элементов на механические свойства и образование интерметаллических соединений.
1. Введение
Пайка титана при температуре ниже температуры превращения имеет большое значение для предотвращения нежелательных изменений его исходной микроструктуры [1, 2]. Низкая температура пайки особенно важна для тонкостенных паяльных структур аэрокосмических компонентов и теплообменников [3]. Более короткий цикл пайки / меньшая температура пайки помогает предотвратить избыточное взаимодействие между компонентами соединения и рост интерметаллических соединений на границе соединения [2].Титан имеет сильное химическое притяжение кислорода; поэтому даже при комнатной температуре на его поверхности быстро образуется пассивный слой аморфного оксида [4]. Окисление поверхности затрудняет процесс соединения титана с точки зрения установления металлического соединения; кроме того, титан следует защищать от сильного окисления при температурах, превышающих 650 ° C [5]. Помимо склонности к укрупнению зерна и влиянию на прочность / пластичность основных компонентов, высокотемпературная пайка требует специального оборудования, условий и более длительного времени обработки, что приводит к более высокой стоимости обработки по сравнению с низкотемпературной пайкой.
Титановые соединения широко изучаются [6]. В отличие от пайки, сварка обычно не используется для титановых сотовых многослойных конструкций [7–10], которые требуют соединения многих точек без деформации. Кроме того, сварочный процесс не подходит для соединения алюминидов титана [11]. Для пайки титановых сплавов разработано и исследовано большое количество припоев-присадок; некоторые из них использовались в коммерческих целях. В 1950-х и 1960-х годах первые работы были сосредоточены на присадочных сплавах на основе Ag, Au, Cu и Pd для ∼ (316–427 ° C) и присадочных сплавах на основе Al для рабочих температур ∼204 ° C.Позднее были разработаны сплавы на основе Ti и Ti – Zr, которые показали лучшую металлургическую совместимость с титаном [12] и обеспечили более высокую прочность соединения по сравнению с другими системами припоя. В таблице 1 приведены некоторые примеры относительно высокопрочных и температурных паяных соединений с использованием присадочных сплавов на основе Ti и Ti – Zr. Однако низкотемпературная пайка с более свободными условиями может найти несколько применений: там, где нельзя применять инертную атмосферу, соединяемые детали не могут поместиться в ограниченных и особых условиях, таких как массовое производство путем непрерывной пайки, большие пайки пайки или для пайки на месте.
Кроме того, снижение стоимости соединения за счет снижения температуры важно для снижения общей стоимости изготовления и сохранения доли титана в общей конструкционной массе аэрокосмических систем [13].
|
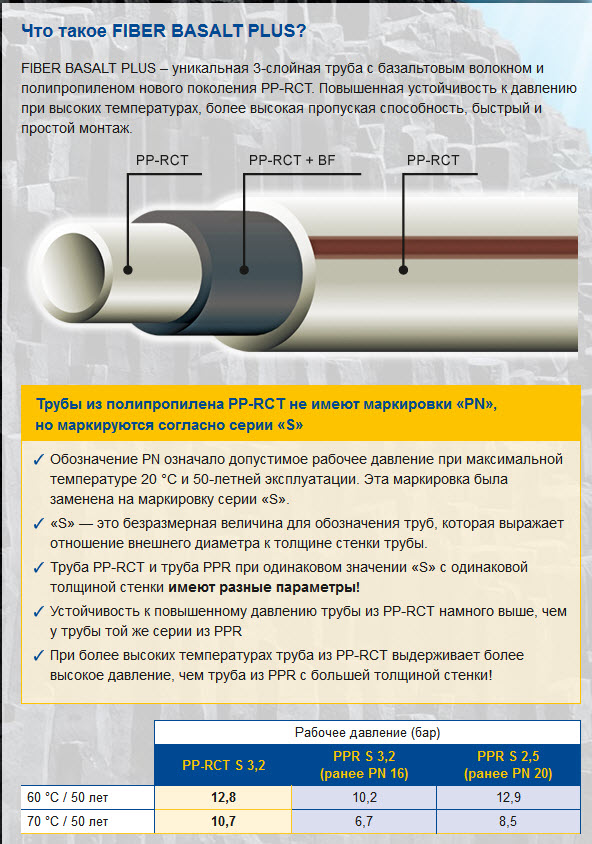
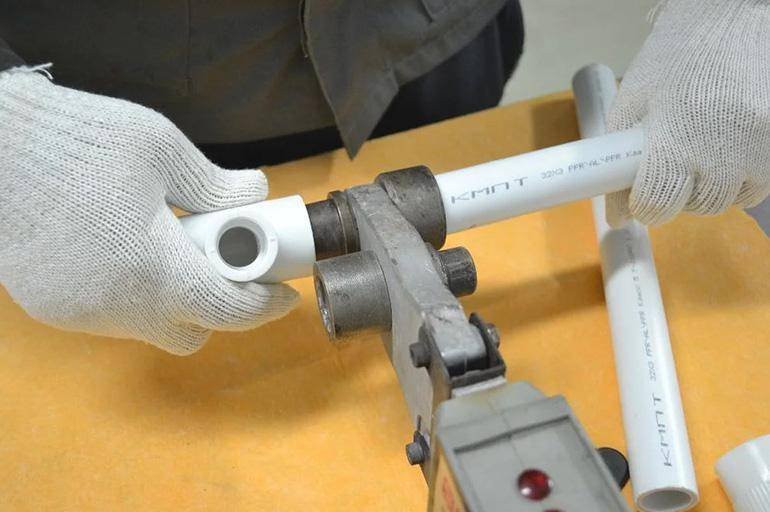
Разработанная микроструктура и механические свойства паяных соединений зависят от компонентного состава, температурно-временного цикла и конструкции соединения. Выбор правильных параметров цикла зависит, в свою очередь, от скорости и характера взаимодействия на интерфейсе родитель / наполнитель. Короткий цикл температурно-временной пайки защищает основной компонент от нежелательных металлургических изменений, которые могут происходить быстрее при повышении температуры; например, эффекты старения, которые проявляются через 4 часа при 537.8 ° C (1000 ° F) в Ti -– 6Al -– 4V будет происходить за ∼10 мин при 579,4 ° C (1075 ° F) [41]. Однако время пайки может быть увеличено в соответствии с составом исходного материала / присадочного материала, чтобы обеспечить возможность диффузии межфазного элемента до определенного предела, необходимого для достижения оптимальной прочности соединения. Распространение некоторых процессов пайки, обычно при высокой температуре, может происходить в течение относительно длительного времени выдержки до достижения гомогенизации микроструктуры по всему соединению, что особенно известно как диффузионная пайка.Matsu et al., Ganjeh et al. и Chang et al. [16, 17, 42] исследовали диффузионную пайку нескольких наполнителей на основе Ti и Zr, которая привела к специфической микроструктуре и высокой прочности на сдвиг (таблица 1). Эти процессы включают изотермическое затвердевание и гомогенизацию соединения [43].
При литье металла ультразвуковая вибрация (USV) обеспечивает множество значительных эффектов, таких как дегазация [44–47], измельчение и изменение микроструктуры [48–51]. Использование USV при пайке — привлекательный вспомогательный инструмент [37–39, 52–58]; однако изучению комбинированного воздействия USV с технологическими параметрами процесса пайки и разработке стыковочного интерфейса, более совместимого с USV, еще не было уделено должного внимания. Основное внимание в этом обзоре будет уделено границе раздела титан / алюминий, которая включает в себя присадочные сплавы на основе алюминия для пайки исходных (базовых) компонентов титан / титан и титан / алюминий с учетом технологических параметров и процедур.
2. Присадочные сплавы на основе алюминия
Различные системы сплавов на основе алюминия были испытаны для пайки основных компонентов титана / титана и титана / алюминия. Легирующие добавки к присадочным материалам служат нескольким целям, таким как снижение температуры плавления, улучшение смачивания [28, 34], уменьшение толщины интерметаллидов [29], улучшение коррозионной стойкости [41] и улучшение статической / динамической прочности при рабочей температуре [29]. ].
Снижение температуры пайки и уменьшение времени контакта расплавленного присадочного сплава с исходным титановым сплавом снижает эрозию титана [26, 42] и повышает надежность тонкостенных титановых соединений [3]. Присадочные сплавы на основе алюминия могут быть подходящим кандидатом для пайки титана, удовлетворяющего следующим условиям: температура плавления значительно ниже температуры превращения титановых сплавов, хорошая металлургическая совместимость с титановыми сплавами, хорошее смачивание и растекание по поверхности титана, хорошая коррозионная стойкость [ 59], низкой плотности и приемлемой прочности для большой соединительной поверхности [2]. Были внедрены некоторые промышленные присадочные сплавы на основе Al систем Al – Cu, Al – Mg и Al – Si с добавками Cr и Ti [3, 19]. Однако алюминий приводит к быстрому образованию хрупкого интерметаллического слоя на стыке с Ti и обеспечивает относительно низкую прочность по сравнению с другими присадочными сплавами; активность Al с Ti считается основной проблемой при разработке наполнителей на основе алюминия и оптимизации процесса пайки.
2.1. Разработка условий / методов пайки твердым припоем Ti / Ti и Ti / Al с использованием наполнителей на основе алюминия
2.1.1. Вакуум, пайка горелкой и другие методы
Lewis et al. [33] первоначально протестировали многие из имеющихся в продаже присадок для пайки, используя процедуры тщательной подготовки образцов. Полученная прочность на сдвиг паяных соединений внахлест при пайке в печи с контролируемой атмосферой составила 73,77–115,69 МПа с использованием алюминиевого наполнителя 61S (6061). Дальнейшие испытания пайки горелкой были выполнены путем покрытия поверхностей образцов промышленным титановым флюсом и с использованием немного восстанавливающего пламени. В целом силовые результаты были ниже 44.82–88,94 МПа по сравнению с пайкой в печи в контролируемой атмосфере; Причина была объяснена захватом флюса в зоне стыка или недостаточным контролем температуры и защитой от окисления при пайке горелкой. Использование горелочной пайки всегда должно сопровождаться определенными флюсами, при выборе подходящего флюса следует учитывать легирующие элементы в расплавленном наполнителе и он должен подходить для всех элементов соединения. Флюсы для титана — это в первую очередь смеси фторидов и хлоридов щелочных металлов, натрия, калия и лития [4].
Takemoto et al. [28] исследовали пайку чистого соединения Ti / Al3003 (Al – 1Mn) в вакууме с использованием трех различных присадочных сплавов на основе алюминия. Время пайки было коротким (3–5 мин), а температура пайки не превышала. Таблица 2 показывает результаты прочности на сдвиг.