Тонкости производства лего кирпича – ТПК Нано-СК
Кирпич Лего имеет много общего с всемирно известным детским конструктором, а именно имеет выступы и впадины, благодаря которым можно с легкостью собирать конструкцию. Чаще всего такой материал используется для облицовки поскольку помимо высоких прочностных характеристик, позволяющих поверхности выдерживать большие нагрузки и негативное воздействие окружающей среды, кирпич имеет отличный внешний вид.
Помимо всего этого лего кирпич позволяет значительно ускорить процесс строительства. Дело в том, что для использование в качестве строительного материала лего кирпича не нужен цементный раствор, достаточно плиточного клея, в результате чего отпадает необходимость замешивания. Плиточный клей наносится при помощи специального шприца, что гораздо удобнее, чем в случае с цементным раствором.
Существует несколько разновидностей данного строительного материала. В первую очередь кирпич Лего классифицируется исходя из исходного сырья.
- глиняно-цементная смесь, в которой 90% глины и 8% цемента, все остальное вода;
- глиняно-песчаная смесь, в пропорции 35% песка, 8% цемента, 55% глины и воды.
При производстве данного кирпича необходимо учитывать доступность сырья. Кирпичи, получаемые прессовым способом, необходимо производить с использованием сырья мелкой фракцией. Только таким образом можно достигнуть необходимых для долговечности строения прочностных характеристик.
Помимо хорошего сырья производство кирпичей Лего предполагает использование специальных форм-матриц. При помощи данных форм изделие приобретается ровность очертаний, точность размеров и гладкость поверхностей. Для полноценного производства необходимо иметь в своем распоряжении целый комплект матриц.
Процесс производства кирпича Лего
Смесь для производства материалов предварительно подготавливается. А именно тщательно перемешивается и просеивается, очищаясь таким образом от примесей и лишних включений.
После подготовки смесь поступает в специальный бункер, после чего отправляется в формовочный отсек. При воздействии гидравлического пресса, создающего большое давление, смесь сжимается, в результате чего и получается лего кирпич. Термической обработки, в отличии от многих других производственных технологий, не предполагается.
Для повышения производительности станка, необходимо привлекать к процессу изготовления данного строительного материала не менее двух человек, а также максимально автоматизировать производственный процесс. При полностью автоматизированном технологическом процессе может осуществляться при помощи одного оператора. К тому же автоматизация существенно повышает количество кирпичей, которые можно изготовить за определенный промежуток времени. Получение изделий высокого качества напрямую зависит от используемых в процессе производства компонентов, а также их пропорций в смеси. Необходимых технических характеристик можно достичь методом проб и ошибок.
Все о лего-кирпиче: производство, состав смеси, цена.
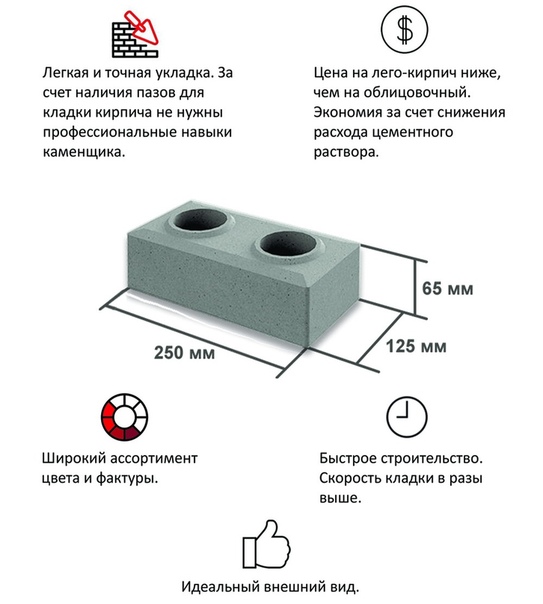
Лего кирпич – абсолютная новинка на рынке строительных материалов. Еще из названия можно понять о том, что форма изделия похожа на детали известного во всем мире конструктора Lego. Как просто ребенок собирает этот конструктор, также и Вы с применением лего кирпича можете построить дом. Само изделие представляет собой блок прямоугольной формы, в котором присутствует 2 вертикальных соосных отверстия, верхняя часто которых выступает над основной поверхностью.
В результате этого, при формировании кладки одного кирпича на другой, отверстия верхнего ряда кирпича плотно входит в отверстия нижнего ряда. Следует также учесть, что при работе используется не привычный цементный раствор, а специальный клей. Новинка индустрии!
- Объем бетона — 1,6 дм3
- Пустотность — 23%
- Масса камня — 3,3 кг
- Расчетная плотность — 2,1 кг/дм3
Производство лего кирпича основывается на технологии гипперпрессования и не только полностью включает в себя все её преимущества, но и выделяется своей большей экономичностью. Любое производство начинается с оборудования. В первую очередь необходимо приобрести станок для лего кирпича. В продаже Вы можете встретить станки как российского производства, так и зарубежного. Отметим для Вас тот факт, что в процессе работы матрица, которая формирует изделие, имеет постоянный износ и её замена в оборудовании российских производителей будет ощутима дешевле. В процессе работы по производству лего кирпича станок должен обеспечивать равномерное распределение смеси при вибропрессовании. Такое распределение гарантирует вибропресс Кондор, позволяющий получать оптимальный структурный состав блоков, при сохранении низкой себестоимости.
Оборудование для производства лего-кирпича
Стоит отметить тот факт, что цена оборудования для лего кирпича не высока и соизмерима с покупкой автомобиля среднего класса, при этом потребность рынка в материале очень высока, что позволит обеспечить быструю окупаемость вложенных средств и высокий рост доходов.
Оборудование для лего кирпича обеспечивает высокую производительность, которая может достигать порядка 1600 штук за одну смену. Дополнительным оборудованием при производстве может служить миксер, который позволит без лишних трудозатрат изготавливать рабочую смесь.
Из чего изготавливать?
Состав смеси для лего кирпича может изменяться в широких пределах и в первую очередь зависит от доступности на местном уровне наполнителя, который составляет порядка 85% от общего объема. Такими наполнителями могут служит песок, глину, известь, отсев щебня и отходы от каменоломни. Подбирая состав смеси следует учитывать сферу применения готовых блоков и климатический пояс, в котором они будут использоваться. Так глина достаточно сильно снижает морозоустойчивость изделия.
Примерный рецепт лего кирпича, на 1 кубический метр смеси:
Наименование |
Масса, в кг |
Для одного кирпича, в кг |
Цемент М400 Д20 |
315 |
0,53 |
Щебень |
690 |
1,15 |
Песок |
825 |
1,38 |
Вода |
92 |
0,15 |
В России наиболее популярен натуральный цвет лего кирпича серых тонов. Однако, в строительстве домов все чаще и чаще используют комбинированные цвета. Из-за этого спрос на цветной лего кирпич растет с каждым годом. Цвет кирпича зависит от материала который входит в его состав. Так например красные тона придает глина, известняк — белые тона, песок — бежевые оттенки. Единственный недостаток использования натуральных красителей это бледность тонов, для того что бы придать камню более яркий цвет используют пигменты. Иногда их распределят не равномерно в структуре кирпича, что придает естественный окрас натурального камня.
На фото вы можете увидеть насколько разнообразна цветовая палитра лего кирпича.
Как укладывать?Уникальная форма блоков с выступающими пазами и применение специального клея при создании кладки позволяет без применения специальных знаний и опыта обеспечить идеально ровную поверхность без дополнительного оштукатуривания. При кладке используется широко распространённый клей для наружных (фасадных) работ. Средний расход клеевой смеси составляет 50кг на 1000 блоков.
изготовление кирпича и блоков. Тестирование породы для подготовки состава смеси для образцов кирпича. Плотность изделий проверка в лаборатории.
.(цикл — статей о лего кирпиче)
Краткий перевод части диссертации
Доктора технических наук Университета «Warwick»
Simion Hosea Kintingu
«DESIGN OF INTERLOCKING BRICKS FOR ENHANCED WALL
Инженерная школа
май 2009
2.8
Процесс производства стеновых изделий, т.е. кирпича / блоков включает в себя либо прессование (обычно в изделиях, в которых в качестве вяжущего выступает цемент) или обжиг.
И в первом и во втором случае, процесс начинается с идентификации почвы и тестирования (на месте и в лаборатории), с последующей подготовкой (добыча/выемка грунта, измельчение и просеивание), смешивание и формование (вручную, машинным прессованием или уплотнением посредством вибрации), с последующими обработками для всех объектов – пропаривание для изделий содержащих цемент и обжиг для изделий из глины. Эти различные процессы хорошо освещены Montgomery (2002), Kerali (2001), Norton
В этом конкурентном мире, собственно сам процесс производства кирпича является одной из наиболее важных частей промышленного изготовления строительных материалов. В свою очередь, это гарантирует стандартизированное качество и соответствующее количество материалов для удовлетворения потребностей рынка при строительстве от дорогостоящих проектов до самых дешевых домов под ключ. В данной работе мы будем рассматривать производство Лего-кирпичей (IB), с применением в качестве основного сырья природные материалы имея в виду, что «..использование почвы, которая легко доступна для строительства, в экономическом спектре и на различных этапах социально-технологического развития, делает доступной соответствующую и устойчивую технологию для создания искусственной среды» (Моррис и

2.9 ВЫБОР ПОДХОДЯЩЕГО СОСТАВА СМЕСИ ДЛЯ ПРЕССОВАНИЯ
Низкое качество прессованных изделий является результатом отсутствия контроля или мониторинга материалов и всего производственного процесса. Отбор пород включает в себя идентификацию распределения гравия, песка и мелких частиц (ила и глины) в образце. Чтобы ограничить размер гравия и удалить другие крупные частицы, будучи сначала измельченной, породу пропускают через стандартизированное сито с отверстиями в 4-6 мм. Важным фактором при прессовании инертных является степень уплотнения породы, которое зависит от фракционного состава. Выбор породы часто воспринимается как разовый процесс тестирования, для подтверждения, что такая порода отвечает всем необходимым критериям для прессования и определения наилучшего соотношения гранулометрического состава для наилучшего уплотнения. Однако для обеспечения стабильного результата в ходе использования смеси, необходимо на практике постоянно контролировать свойства пород и учитывать любые изменения, которые происходят. Процедура испытания и последовательный план тестирования, описанные Гудингом (1993), для предварительного испытания на месте являются одним из основных этапов отбора пород. Хотя конус и линейные испытания усадки были рекомендованы в качестве «приблизительных лабораторных испытаний», автор считает, что такие испытания могут быть использованы на месте и способны быть надежным руководством для определения пропорций смешивания цемента и породы (Gooding 1993, Houben & Guillaud 1994, Norton 1997,Burroughs 2001). Информация, отображенная в таблице 2.2 показывает, что породы с усадкой менее 2,5% или более чем на 9% не должна применяться для уплотнения, если это не может как-либо быть изменено для достижения лучшей плотности (содержание глины от 10% до 35% BRU—B2 (1974).
Любая смесь, состав которой изменен путем смешивания различных фракций и составляющих, должна быть проверена несколько раз, пока не будет достигнуто необходимое уплотнение от 2,5 до 9%. Данные в таблице 2.2 являются результатом опыта работы на местах в соответствии с калибровками (по VITA (1975)) для пресса низкого давления до 2 МПа, и более высокого давления машины до 10 МПа (по Webb (1988)). Результаты испытаний линейного сжатия (LS) определяют пропорции, которые позволяют рассчитать количество используемого вяжущего, а также необходимого давления. Также соглашаясь с рекомендациями Уэбба и Локвуда (1987) в отношении выбора пресса:
— низкое уплотнение породы (высокое содержание песка) лучше уплотняется портландцементом (ПК) и прессуется высоким давлением (> 4 МПа) пресса, в то время как
— высокое уплотнение породы (с высоким содержанием глины) лучше уплотняется с применением извести и прессов малой мощности (до 2 МПа).
Таблица 2.2 Уровень усадки почвы с рекомендуемым давлением сжатия
(Данные получены с помощью термоусадочного ящика Alcock — 600x40x40 мм)
Источник | Размер усадки (мм) | Усадка (%) | Рекомендуемое соотношение цемента и породы (Ц:П) | Цемент (Ц%) | Примечание |
Gooding (1993) Hauben & Gullaud (1994) ILO (1987). Norton (1997), UN (1992) VITA (1975) Webb & Lockwood (1987) | 6 – 15 | 1 к 2,5 | 1:20 | 4,8 | Только для прессов с усилием прессования свыше 4 Мпа при условии, что в породе содержится достаточное количество глины |
15 – 25 | 2.5 к 4,17 | 1:18 | 5.3 | Удовлетворительно для нормального усилия прессования до 4 МПа | |
25 – 35 | 4.17 к 5.83 | 1:16 | 5.9 | Лучшая порода для усилия прессования всего 2 МПа | |
35 – 45 | 5. | 1:14 | 6.7 | Удовлетворительная порода для усилия прессования всего 2 мПа | |
45 – 55 | 7.5 к 9.17 | 1:12 | 7.7 | Чистая порода для усилия прессования менее, чем 2 Мпа, но низкие темпы производства за счет налипания (высокое содержание глины). | |
55 – 60 | 9.17 к 10 | 1:10 | 9.1 | Бедная почва; возможно, нуждается в смешивании, чтобы уменьшить прилипание или, возможно, нуждается в большем количестве цемента, таким образом, более дорогого. Приемлемый вариант только, когда нет альтернативы.
|
После определения фракционного состава породы, ее линейной усадки и подбора соответствующего соотношения (цемента к породе – Ц : П), заключительный этап состоит в подготовке пробных кирпичей; по крайней мере, десяти блоков от каждой партии. Это применяется для проверки пригодности почвы для стабилизации с помощью предлагаемых соотношений почвы и воды к цементу (табл. 2.3).
Были сделаны следующие наблюдения:
— Процесс смешивания: если он затруднен, то это означает слишком высокое содержание глины в смеси. Основные инертные требуют модификации: либо путем добавления дополнительного цемента, либо путем смешивания с песком.
— Уровень сколов и трещин при перемещении только что изготовленных кирпичей к месту их отверждения. Слишком высокий уровень (> 10%) указывает на слишком малое содержание глины в смеси.
— Появление трещин, короблений и существенной усадки в течение первых трех дней набора прочности. Если они слишком большие, это указывает на слишком высокое содержание глины, что может потребовать или дополнительного смешивания с песком или добавления большего количества цемента.
Тестирование производится для определения прочности на сжатие в три, семь и четырнадцать дней, чтобы проверить эффективность стабилизатора (минимальное значение прочности после 14 дней >1 МПа). Результаты зависят от наличия соответствующим образом оборудованной лаборатории и требования проекта Гудинг (1993). Вышеуказанные проверки контроля качества, как правило, должны продолжаться в течение всего периода производства для каждой новой партии смеси даже если инертные взяты из одного источника.
/
.23.04.2021
27.08.2018
27.08.2018
27.08.2018
27.08.2018
Состав гиперпрессованного кирпича / Статьи
8 апреля 2013 г.
Технология производства гиперпрессованного кирпича коренным образом отличается от таких способов получения искусственного камня, как обжиг, автоклавная обработка, вибропрессование и литье. Для выпуска продукции, используют метод холодной сварки (когезии). Подвергаясь мощнейшему давлению, более, чем в 20 мПа, исходное сырье изменяет молекулярную структуру, превращаясь в монолитный камень, по прочности и плотности идентичный натуральному.
Процесс гиперпрессования позволяет избежать выгорания органических элементов, благодаря чему конечный материал не имеет в своей структуре ячеек воздуха. Данная особенность наделяет кирпич способностью противостоять воздействию воды, что и является одним из многочисленных преимуществ этого вида искусственного камня перед всеми другими аналогами.
В состав гиперпрессованного кирпича входят, в первую очередь отсевы известняка, мрамора, ракушечника, мегеля, доломита, образующиеся при разработке каменных карьеров. Фракции, полученные дроблением щебня или других природных минералов, являются заполнителем, составляя до 92% общего объема прессмассы. Помимо известняковых пород, добываемых в карьерах, для производства гиперпрессованного кирпича могут использоваться отходы промышленных предприятий, например, доменные шлаки, твердые продукты сгорания каменного угля на теплоэлектростанциях, а также, бетонный и керамический бой.
Из этого легко заключить, что производство гиперпрессованного кирпича представляет собой экономически выгодный процесс, позволяющий одновременно избавляться от отходов, загрязняющих окружающую среду.
Вторым по важности ингредиентом состава гиперпрессованного кирпича выступает портландцемент высокой марки. Цемент играет роль вяжущего компонента, и занимает 7-15% прессмассы. Большое значение имеет и качество воды, входящей в состав смеси в объеме 8-15% в качестве агента химической реакции. Вода должна быть чистой питьевой, что необходимо для создания качественного материала. Помимо прочего, в состав гиперпрессованного кирпича входит около 1 % красящего пигмента, благодаря которому получают продукцию разных цветов и оттенков.
Дозирование всех элементов смеси происходит в автоматизированном режиме с высокой степенью точности, контролируясь весовым терминалом. После дозирования, компоненты поступают в дробилку, где происходит их тщательное измельчение и смешивание. Сюда же через дозировочный насос подается нужное количество воды. Так образуется прессмасса, которая по транспортеру, поступает в бункер пресса, где происходит формирование изделий.
Готовая продукция, вышедшая из-под пресса, аккуратно укладывается на поддоны и помещается на 8-10 часов в специальные камеры для пропаривания, в ходе чего набирает до 70% марочной прочности. Без использования пропарочных камер, изделия выдерживаются в складском помещении при комнатной температуре в течение 3-5 суток, а затем реализуются и транспортируются на строительный объект. Остаточную прочность изделия обретают в кладке.
Лего-кирпич
Одной из новаций последнего времени среди строительных материалов является лего-кирпич. Поскольку определение всех его плюсов и минусов даже у опытных потребителей подчас вызывает сложность, имеет смысл выяснить, что представляет собой лего-кирпич, а также определить его основные технические характеристики. Несколько упрощает задачу само название, заимствованное у популярной компании-производителя детского конструктора. Действительно, внешне лего-кирпич или кирпич с взаимно-сцепляемым элементом очень похож на его отдельные детали. Стремясь упростить систему монтажа каменной кладки, латиноамериканские студенты несколько лет назад и разработали рассматриваемый модульный строительный материал.
Технические характеристики лего-кирпича
Схема изготовления кирпича с замковым соединением практически не отличается от технологии производства традиционных блоков. В тщательно перемешанные исходные элементы: песок, цемент, известняк-ракушечник, воду добавляют специализированные пластификаторы и железооксидные красители, после чего процесс смешения продолжается вновь. Затем из полученной субстанции с использованием матрицы и специальных станков методом гиперпрессования формируются различные модули и блоки под нужный размер. Причем величина давления, оказываемого при спрессовывании смеси в заданную форму, оказывается решающим фактором, влияющим на качество получаемых лего-блоков.
Особенности кладки лего-кирпича
Чтобы возведение стен с использованием лего-кирпича шло действительно быстро и легко, необходимо правильно и аккуратно выложить первый слой. Для сокращения времени сцепки слоёв между собой, вместо цементного раствора следует использовать специальный клей, наносимый кистью или валиком. Также следует отметить, что для упрощения и лучшего контроля процесса кладки целесообразно производить армирование.
Самостоятельное изготовление лего-кирпича
Для производства рассматриваемого строительного материала требуется соответствующий станок. В данном агрегате реализован прессовальный метод с использованием высокого давления. Обжиг изделий в термопечах при этом не требуется. Имея такое оборудование, можно производить лего- кирпич собственными силами. При этом стоит грамотно оценить все достоинства и недостатки такого способа, учесть затраты, оценить себестоимость. Данный вид производства относится к числу масштабных, поскольку требует большого количества производственных площадей. Это если речь идет о предпринимательской деятельности. В случае же самостоятельного изготовления, перед принятием решения необходимо определить рентабельность, после чего сделать правильный вывод о том, что легче — изготавливать самому или закупать на стороне.
Лего-кирпич в сравнении с традиционным. Достоинства и недостатки
Достоинства
Без ущерба прочности постройки, при общем объеме строительных работ, масса лего-кирпича ниже, чем у обычного. Соответственно, ниже и затраты на его подъем, и легче сам возводимый объект. Все это ведет к снижению общей стоимости всего проекта.
Недостатки
До настоящего времени не разработан ГОСТ на лего-кирпич. Также отсутствуют методики его испытаний и справочные таблицы для определения его марки. Чтобы изготовить гиперпрессованый кирпич в условиях реального производства, сначала необходимо утвердить его состав, затем разработать и зарегистрировать технические условия (ТУ), обязательные для соблюдения работниками. В ТУ, помимо всего прочего, должны быть отражены методы проверки качества исходного сырья и готовой продукции. Естественно, что на качество изготовленного кустарным способом кирпича гарантии нет. Поэтому он не может быть рекомендован для производства строительных работ и использования в проектах.
Эти новые детали Lego сделаны из экологически чистого пластика
Это не из-за отсутствия попыток. Кирпичи-прототипы сделаны из экологически чистого пластика (Lego не уточняет, какой именно), но Брукс говорит, что, хотя они хорошо выглядят на фотографиях, они страдают от мраморности цвета и им не хватает точной силы сцепления, которая удерживает сборки Lego вместе.
Итальянская компания Bio-On тем временем производит копии Lego из полигидроксиалканоатов, или PHA, полимера, полученного из штамма бактерий. Они выглядят как Lego и складываются как Lego, но в долгосрочной перспективе, по словам Хьюедж, они не действуют как Lego. И вот что важно.
«Они разработали продукт меньшего масштаба», — говорит он. «У них есть возможность сделать что-то, что выглядит как Lego. Проблема в том, что почти наверняка не будет требований Lego к материалам, независимо от того, как они это обрабатывают».
Потенциально более многообещающей альтернативой может быть ABL, недавно разработанная в Национальной лаборатории Ок-Ридж в Теннесси.ABL использует тот же акрилонитрил и бутадиен, что и ABS, но меняет лигнин, биологический материал, на стирол последнего, полученный из нефти.
«Вариант ABL может быть решением», — говорит соавтор ABL Амит Наскар, который также отмечает, что ABL в настоящее время не является идеальной заменой ABS; это не так сложно, и в нем больше растяжения. «Или, может быть, это другой вид возобновляемой энергии. Ученые всего мира работают над возобновляемым материалом». Наверняка один из них подойдет Lego.
Для этого — и да, становится все труднее — им также придется придумать полимер, который, как, вероятно, делает полиэтилен, подходит для существующего производственного процесса Lego.
«Это секретный соус. Во многом это то, как мы делаем кирпичи, как оптимизируем машины», — говорит Брукс. «Различные материалы работают по-разному. Некоторые материалы гигроскопичны, а некоторые гидрофобны. Некоторые из них пыльные, а некоторые нет. У некоторых высокий статический заряд, а у некоторых низкий. .Есть много разных соображений ».
2030 или Bust
У Lego есть еще 12 лет, чтобы выяснить, как использовать экологически чистые материалы для изготовления оставшихся 98 процентов своих пластиковых элементов. Скорее всего, уже собраны, это устрашающая цель. Однако это не невозможно. Вот как компания может к этому прийти.
Начните с того, что уже сделано: эти кусочки биополиэтилена. Для Lego, может быть, дороже, но нет. что-то, что можно перевести через остальную часть строки, но с чего-то нужно начинать. (Возникает также вопрос, насколько более экологически безопасен биополиэтилен, учитывая энергоемкость процесса, необходимого для его производства, но давайте пока отложим это.)
Далее: 19 других типов пластика, из которых состоит остальная часть строки. Важно отметить, что Lego не обязательно будет искать 19 идеальных замен один к одному.
«Мы можем получить больше, мы можем получить меньше», — говорит Брукс. «Некоторые материалы, которые мы находим, могут выполнять функцию некоторых, которые есть у нас сегодня, или может быть наоборот.Для функции, которую мы получаем от одного материала, в зависимости от его применения и формы, может потребоваться несколько материалов ».
Все эти условия, опять же, проистекают из того факта, что эти материалы еще не существуют, по крайней мере, в количестве. , и даже 2030 год может оказаться недостаточно долгим сроком для их поиска и массового производства.
«Даже через 12 лет они смогут изготавливать каждый кирпичик из заводов в лаборатории в небольшом масштабе, но продавать в магазинах каждый кирпичик будет непросто », — говорит Хьюедж, исследователь биохимии.
Но может и не нужно. Lego также считает переработанный пластик — не настоящие кирпичи Lego, которые, как правило, передаются из поколения в поколение, а пластик ABS в целом — как экологически безопасный источник. Использование переработанного материала сопряжено со своими проблемами, особенно с контролем качества и воспроизведением цвета. Но сочетания разработки достаточного количества полимеров на биологической основе и получения достаточного количества высококачественного переработанного АБС может быть достаточно, чтобы Lego добралась до финишной черты.
«Некоторые кирпичи будут из вторичного сырья, некоторые — на биологической основе», — говорит Брукс.«Вероятно, именно здесь мы и выберемся».
Другие придерживаются еще более оптимистичного взгляда. «Если они нацелены на 2030 год, это, безусловно, выполнимо», — говорит Наскар из Окриджа.
В этом пространстве делается слишком много работы, предполагает он, чтобы что-то не щелкнуло.
Подробнее WIRED Gear
Хотите больше новостей и обзоров, которые вы можете использовать? Подпишитесь на рассылку новостей Gadget Lab.
Из чего сделаны кубики Lego и почему наступать на них так больно? — Сложный процент
нажмите, чтобы увеличитьLego — одна из самых популярных и узнаваемых детских игрушек.Вы когда-нибудь задумывались, из чего сделаны эти кирпичи или как они сделаны? Или, если на то пошло, почему так больно, если ты наступишь на кого-то? Этот рисунок смотрится!
Кирпичи Lego всегда делали из пластика, но не всегда из одного и того же пластика. С 1949 по 1963 год использовался ацетат целлюлозы. Это то же самое вещество, которое когда-то использовалось в киноиндустрии для фильмов. Он также используется в пластиковой оправе некоторых очков и по сей день.
В 1963 году компания Lego заменила пластик, из которого производились кирпичи, на другой полимер, акрилонитрилбутадиенстирол (сокращенно АБС).ABS имеет несколько преимуществ перед ацетатом целлюлозы: он прочнее, меньше коробится со временем и более устойчив к выцветанию. Единственным недостатком было то, что, в отличие от ацетата целлюлозы, ABS непрозрачен, поэтому из него невозможно сделать прозрачные детали Lego. В этих случаях вместо этого используется поликарбонатный пластик. Чтобы получить различные цвета деталей Lego, в ABS добавляются красители Macrolex.
Процесс производства Lego начинается с крошечных гранул АБС, которые грузовиком доставляются на фабрики.Здесь их сбрасывают в гигантские металлические бункеры, затем загружают в формовочные машины, где нагревают до 230 ° C (450 ° F). Это плавит гранулы, образуя пластиковую слизь, которая автоматически подается в формы деталей Lego. Формовочная машина прикладывает давление, чтобы детали Lego были идеально сформированы, затем они охлаждаются и выталкиваются. После этого добавляются необходимые украшения и собираются детали, которые нужно собрать, например, мини-фигурки.
В 2014 году компания Lego произвела поразительное количество деталей — 60 миллиардов.Из этих деталей не менее 318 миллионов — это миниатюрные шины для автомобилей Lego, что делает Lego крупнейшим производителем шин в мире! Эти шины изготовлены из полимера, который немного отличается от АБС — стирол-бутадиен-стирола (SBS).
Когда дело доходит до боли, когда вы наступаете на кусок Lego, виноват АБС. Тестовые образцы Lego в процессе производства в рамках мер контроля качества Lego. Испытания включают в себя сжатие между дисками с силой 15 кг и падение предметов на кирпичи, чтобы убедиться, что они не разбиваются при ударе.Один тест даже имитирует 50-килограммового ребенка, наступающего на деталь Lego, чтобы убедиться, что причиняет максимум боли, не ломается и не раскалывается. Средняя сила, которую может выдержать конструктор Lego 2 × 2, составляет 4240 Ньютонов, что эквивалентно тому, как на него стоит кто-то весом около 430 килограммов. Короче говоря, кирпичи Lego созданы так, чтобы по ним было больно наступать.
Lego есть и другие риски, кроме опасности при наступлении. Старые кирпичи Lego 1970-х и 80-х годов содержали кадмий, который помогал окрашивать красный и желтый кирпичи.Те, кто разбирается в химии, знают, что кадмий и его соединения ядовиты и могут оказывать токсическое действие. Исследования показали, что уровни кадмия в этих старых кирпичах превышают текущие ограничения ЕС. Важно рассматривать это в контексте количеств, которые находятся на уровне микрограммов. Обращение с этими старыми кирпичами сопряжено с минимальным риском воздействия, но вы можете не класть их в рот! Компания Lego постепенно отказалась от кадмия, поскольку его токсичность стала очевидной, и новые кубики Lego не содержат его.
Есть еще одна проблема со всеми деталями Lego: они сделаны из пластика нефтяного происхождения. Нефть — ресурс ограниченный, и создание Lego из нефти оказывает значительное влияние на окружающую среду. В 2012 году группа Lego поставила перед собой цель найти и использовать более экологически чистое сырье для своей продукции к 2030 году. Они сделали небольшой шаг к этой цели в начале этого года, объявив, что с этого года и далее зеленые листья, кусты и деревья в их продуктах будет использоваться полиэтилен, полученный из экологически чистых источников сахарного тростника. Однако этот полиэтилен далеко не прочен и не достаточно долговечен, чтобы заменить АБС, поэтому поиски его замены продолжаются.
Какой пластик используется в наборах Lego? — Craftech Industries — Высокоэффективные пластмассы
Примерно 4 года назад в наш дом попал первый набор Lego. Думаю, все началось с подарка на первый день рождения, который пригласили и моего сына. После этого было лишь вопросом времени, когда я уступил просьбам сына о создании собственного набора Lego.Я признаю, что с годами я привил своему сыну зависимость от Lego. Да, вы правильно прочитали, зависимость. Моим последним подарком на прошлое Рождество был поезд с дистанционным управлением, построенный из Lego.
Во время одной из моих многочисленных попыток привести в порядок «Комнату Лего» я сделал себе заметку, чтобы узнать, какой пластиковый материал использует компания Лего. Я работаю в индустрии пластмасс, поэтому мне было естественно любопытно. Есть так много кирпичей разного размера и цвета, опорных частей, дверей, окон и фигур в самых разных темах — несметное количество предметов невероятно. «Дизайн и производственный процесс должны быть, мягко говоря, впечатляющими», — подумал я. Итак, вот краткое изложение истории Lego и того, как они сделаны.
Плотник из Биллунда, Дания, по имени Оле Кирк Кристиансен начал делать деревянные игрушки в своей мастерской в 1932 году. Его компания получила название «Лего» в 1934 году от датского словосочетания «leg godt», что означает «хорошо играть». В 1947 году компания расширилась до производства пластиковых игрушек. Ранняя версия знаменитых блокировочных кирпичей начала производиться в 1949 году.К 1954 году сын Кристиансена Годфред увидел огромный потенциал кубиков Lego, которые могут стать системой для творческой игры. (Я бы сказал, ударил по этому поводу.) В 1958 году была разработана современная кирпичная конструкция, призванная решить проблему ограниченной способности запирания и универсальности. На поиск подходящего материала, АБС, ушло еще 5 лет. В 1958 году был запатентован современный кирпич Lego.
ABS или акрилонитрилбутадиенстирол — это пластик, который используется в самых современных элементах Lego. Это лишь один из материалов, с которыми мы знакомы в компании Craftech, где мы производим детали из прутков АБС и формуем полимерную форму под давлением.Бутадиеновый компонент (производное натурального каучука) в значительной степени отвечает за прочность и ударопрочность этого пластика. Современная формула ABS была разработана в ходе военных действий в середине 1940-х годов. Немецкая химическая компания Bayer AG долгое время была эксклюзивным поставщиком группы LEGO. В 2004 году она выделила большую часть своего бизнеса по производству пластмасс в недавно созданную Lanxess AG. Практически весь пластик, используемый LEGO, является патентованной версией Lanxess Novodur ABS, поликарбоната Makrolon (для прозрачных элементов) и красителей Macrolex для окрашивания.Варианты из делрина или нейлона используются для изготовления тканевых и струнных элементов.
Лего изготовлены методом литья под давлением. Бункеры с материалом доступны с трубами, по которым пластиковые гранулы поступают к формовочным машинам. Каждый силос вмещает до 33 тонн гранул. Процесс формования практически полностью автоматизирован. Формовочные машины нагревают гранулы до температуры около 450 ° F (230 ° C). Затем пластик загружают в формы. Машина оказывает давление в сотни тонн, чтобы кирпичи были сформированы с идеальной точностью.Затем они охлаждаются и выбрасываются, что занимает около 10 секунд. Готовые изделия по конвейерной ленте попадают в коробки. Когда ящики заполнены, формовочная машина посылает радиосигнал на грузовики-роботы, которые патрулируют цех. Тележки-роботы управляются канавками в полу. Коробки доставляют в актовый зал, где гигантский принтер штампует декоративные детали на лицах, панелях управления, числах и словах. Последний шаг — собрать правильные компоненты, чтобы сделать набор LEGO. Ящики, называемые «кассетами», катятся по конвейерной ленте под бункерами, в которых хранятся детали каждого типа.В каждую кассету автоматически загружается нужное количество штук. Операторы упаковки закрывают коробки и добавляют дополнительные детали и инструкции по сборке.
Теперь я немного больше осведомлен об этом продукте и о том, что нужно, чтобы его поставить на полку. Этот продукт может быть у меня дома еще на несколько лет, так как сын №2 уже усердно трудился над шедеврами своих братьев.
Ваши дети любят Lego? Расскажите мне свою историю Lego в разделе комментариев ниже.
Ищете дополнительную информацию об АБС и других пластмассах с высокими эксплуатационными характеристиками? Загрузите наше бесплатное руководство по материалам!
www.ChemistryIsLife.com — Химия Legos
Состав …
ABS: основной пластик, используемый сегодня в Legos
- Акрилонитрил-C8H8
- Бутадиен-C4H6
- Стирол
CA: был основным пластиком, который использовался в Lego до 1963 года.
- Ацетат целлюлозы-C76h24O49
Поликарбонат: используется для изготовления эластичных деталей, таких как стержни, флажки и зажимы.
- 1 / n (OC (OC6h5) 2CMe) n + 2C6H5OH
Делрин: нейлоновый вариант, из которого изготовлены детали, похожие на ткань и нити
Основные химические вещества, соединения, компоненты
ABS : акрилонитрил-бутадиен ) (C4H6) (C3h4N) представляет собой термопласт, состоящий из мономеров акрилонитрила, бутадиена и стирола.Мономер — это молекула, которая способна связываться с другими идентичными молекулами с образованием полимера. ABS выдерживает предел прочности на разрыв 4300 фунтов на квадратный дюйм и обладает отличной сопротивляемостью глицерину, неорганическим солям, многим кислотам и большинству спиртов и углеводородов. В Legos акрилонитрил обеспечивает блокам отличную термостойкость, бутадиен обеспечивает хорошую ударную вязкость, а стирол обеспечивает жесткость блоков.
CA : Ацетат целлюлозы C76h24O49, представляет собой ацетатный эфир целлюлозы. CA использовался в оригинальных блоках lego, но в шестидесятых был заменен на ABS в пользу его стабильности и улучшенных цветов. Целлюлоза — это природный полимер, получаемый из волокон древесины и семян хлопка.
Роль химии
Бутадиен получают из фракции C4 парового крекинга (процесс разложения насыщенных углеводородов на более мелкие, обычно ненасыщенные углеводороды). Акрилонитрил — это синтетический мономер, производимый из пропилена (C3H6) и аммиака (Nh5).Стирол — это мономер, полученный в результате дегидратации органического соединения этилбензола (C6H5Ch3Ch4). АБС можно изготовить двумя разными способами. Первый способ изготовления АБС — растворение полибутадиена в жидких мономерах акрилонитрила и стирола, а затем полимеризация мономеров. Второй способ производства АБС — сначала приготовление полибутадиена до состояния водянистого латекса, затем добавление акрилонитрила и стирола и их сополимеризация.
Предпосылки исследования
Чтобы начать создавать Lego, вы сначала начнете с ABS. АБС нагревают до достижения консистенции теста при 450 градусах Фаренгейта. Затем АБС впрыскивают в формы Lego под давлением от 25 до 150 т. Затем блоки оставляют охлаждаться в течение 10-15 секунд. Затем кирпичи проверяются на допуск до двух миллиметров, чтобы убедиться, что кирпичи остались нетронутыми. Средний кирпич 2 на 2 весит около 1,152 г и выдерживает до 4240 ньютонов. Лего могут быть собраны с большинством других Лего, сцепляясь друг с другом.Их можно построить, разобрать, а затем реконструировать во что-то новое.
Ресурсы
http://en.wikipedia.org/wiki/Lego
История лего
Краткое описание того, как они сделаны
фактов о лего
http://lego.wikia.com / wiki / Acrylonitrile_Butadiene_Styrene
производство ABS
история
http://en.wikipedia.org/wiki/Acrylonitrile_butadiene_styrene
химические формулы для ABS
информация об ABS
// www 9000.dynalabcorp.com/technical_info_abs.
Устойчивость ABS
Прочность на разрыв
http://en.wikipedia.org/wiki/Polycarbonat
Информация о поликарбонате
Формула поликарбоната
http: //en.m..m.wikipedia .org / wiki / Polyoxymethylene
информация о Delrin
Formula
http://en.wikipedia.org/wiki/Cellulose_acetate
краткая информация об ацетате целлюлозы и истории
http: //pubchem.ncbi.nlm.nih.gov/compound/3084039#section=Top
формула для CA
http://en.wikipedia.org/wiki/Cracking_(chemistry)#Steam_cracking
информация о паровом крекинге и определении
www. britannica.com/EBchecked/topic/101663/cellulose-acetate
информация об ацетате целлюлозы
как производится CA
http://www.britannica.com/EBchecked/topic/4259/acrylonitrile-butadiene-styrene-copop -ABS
Как сделать ABS
http: // en.wikipedia.org/wiki/Ethylbenzene
Химическая формула этилбензола
http://en. wikipedia.org/wiki/Propene
Химическая формула пропилена
http://en.wikipedia.org/wiki/Monomer
Определение мономера
Об авторе
Хейли Ларсен в настоящее время учится в старшей школе. После окончания учебы Хейли планирует поступить в колледж Университета Миссулы. Там она планирует изучать предварительную физиотерапию и спортивную медицину.Она надеется сделать свою карьеру физиотерапевта, специализирующегося на спортивных травмах.
Разноцветные пластиковые кубики Lego, которые станут зелеными
Lego стремится улучшить используемые материалы, а не отказываться от пластика.Может произойти глобальный бунт против пластика, но датский производитель игрушек Lego, известный своими разноцветными пластиковыми кирпичиками, остается бешеным успехом, даже если он тоже стремится к экологизации.
Когда-то революционный, а затем повсеместный материал, пластик все чаще избегают из-за длительного вреда, который его химические компоненты наносят планете.
В результате компания Lego пообещала, что к 2030 году ее культовые кирпичи будут на 100% экологически безопасными.
Из частей, которые практически невозможно сломать и использовать повторно в течение нескольких поколений, Lego — чье название в переводе с датского означает «Leg Godt» или «Играй хорошо» — всегда имело лейтмотивом устойчивость, — сказал AFP Тим Брукс, глава отдела корпоративной ответственности. .
Теперь компании просто нужно адаптироваться к экологическим и потребительским требованиям.
Исследование, проведенное исследовательской группой NPD, показало, что 47 процентов рождественских покупателей во всем мире предпочли не покупать игрушки из соображений экологичности.
«Производители игрушек действительно занимаются этой темой … Есть много инноваций как в упаковке, так и в материалах для игрушек», — сказал AFP Фредерик Тутт, эксперт по индустрии игрушек из NPD.
Компания Lego, базирующаяся в городе Биллунд на западе Дании, не планирует отказываться от пластика. Скорее, он нацелен на улучшение материалов, которые он использует.
В настоящее время большая часть его деталей изготовлена из акрилонитрил-бутадиен-стирола (АБС), вещества на нефтяной основе, которое также используется для изготовления бытовой техники.
«Мы хотим использовать пластик ответственно, особенно там, где он находится в высококачественном, прочном и многоразовом применении. Именно это и есть кирпичики Lego», — сказал Брукс.
На данный момент два процента его пластиковых деталей, или 80 из примерно 3600 строительных деталей, изготовлены из материала биологического происхождения — полиэтилена на основе сахарного тростника.
Компания Lego пообещала, что к 2030 году ее легендарные кирпичи будут на 100% экологически безопасными.Это в основном деревья, листья и кусты в наборах, которые не должны соответствовать тем же требованиям к долговечности, что и кирпичи, которые должны плотно склеиваться.
Это техническая проблема, так как Lego хочет, чтобы покупатели не заметили никакой разницы между старым пластиком и любыми новыми материалами.
«Мы не хотим, чтобы вы это замечали», — настаивал Брукс.
Новые изделия должны иметь те же физические свойства, что и старые: прочность, стойкость цвета и сила прилипания, чтобы оставаться совместимыми со старыми изделиями.
Кирпичный проход
За прошедшие годы датская компания превратилась из простых наборов кирпичей в сложные конструкции, такие как наборы, посвященные Гарри Поттеру или архитектуре, и сделала сильный набег на видеоигры, приложения, фильмы, мультфильмы и парки развлечений.
Такая диверсификация помогла группе оправиться от финансовых проблем начала 2000-х годов. В 2019 году продажи выросли на шесть процентов.
Lego призывает покупателей передавать свои кирпичи молодому поколению.
«Кирпич совместим с 1958 года. Сегодня на полках можно купить что-нибудь, что будет подходить к чему-то из конца 1950-х годов», — сказал Брукс.
По оценкам компании, 96 процентов потребителей либо держатся за свои наборы Lego, либо передают их, подчеркивая различие между кубиками Lego и одноразовыми пластиками.
По оценкам компании, 96 процентов потребителей либо держатся за свои наборы Lego, либо передают их.Переработка и ветряные электростанции
Помимо разработки биопластиков, компания Lego, которая возглавляет проект в США по предоставлению подержанных комплектов для детей из неблагополучных семей, осторожно продвигается в области переработанного пластика.
«Вторичные материалы — очень интересная область, но вы должны понимать, откуда они берутся», — сказал Брукс.
Компания отказывается разглашать секреты производства, но настаивает на повторном использовании собственных пластиковых отходов в производстве.
В 2014 году Lego пообещала сократить свой углеродный след, сотрудничая с экологической группой WWF. В нем говорится, что с 2017 года он полагается исключительно на возобновляемые источники энергии.
«Они сэкономили на климате и перешли на новые ветряные машины, теперь они ищут альтернативы своему пластику», — сказал об усилиях компании глава WWF Дании Бо Окснебьерг.
Киркби, материнская компания Lego, тем временем инвестировала почти 1 миллиард долларов в ветряные электростанции.
Lego также работает над улучшением своей упаковки, уменьшая количество пластиковых пакетов, разделяющих части, и уменьшая размер коробок, чтобы уменьшить объемы транспортировки.
Он нацелен на использование только переработанных или возобновляемых материалов к 2025 году.
Antidia Citores, пресс-секретарь экологической группы Surfrider Europe, тем временем подчеркнула, что Lego необходимо также обратить внимание на производственный этап, поскольку замена одного пластика другим не приведет к снижению выбросов.
«Замена одного пластика на другой — это не революция, ни с точки зрения загрязнения окружающей среды, ни с точки зрения выбросов углерода», — сказала она.
«Устойчивое» Lego — пластмасса, полученная с растений, не решит проблему загрязнения окружающей среды
© 2020 AFP
Ссылка :
Разноцветные пластиковые кубики Lego станут зелеными (2020, 8 марта)
получено 2 октября 2021 г.
с https: // физ.org / news / 2020-03-lego-colorful-plastic-bricks-green. html
Этот документ защищен авторским правом. За исключением честных сделок с целью частного изучения или исследования, никакие часть может быть воспроизведена без письменного разрешения. Контент предоставляется только в информационных целях.
Lego делает радикальное заявление, которое опозорит другие компании, производящие игрушки
Если это звучит как загадка, отчасти так оно и есть — особенно для исследовательской группы, которой поручено выполнить обещание. Lego пополняет ряды Starbucks и McDonald’s, уменьшая свою зависимость от пластмасс на нефтяной основе.
Кроме Лего хочу пойти еще на миллион шагов. Согласно New York Times , компания к 2030 году обещает построить свои игрушечные блоки полностью из растительных или переработанных материалов. И вот что интересно: они еще точно не поняли, как это сделать.
Но если они это сделают, Lego полностью изменит будущее их компании — и ее основного продукта. В настоящее время Lego производит около миллиона тонн углекислого газа ежегодно, и это значительно сократит их углеродный след.
Когда пластик — это продукт
Если Lego добьется успеха, они сделают удаление пластиковых соломинок детской забавой. Пластиковые соломинки, которые подают с газированными напитками и кофе со льдом, — это малая толика от количества упаковок, которые используют McDonald’s и Starbucks.
Для Лего пластик это их продукт. Все игрушечные блоки Lego изготовлены из прочного, упругого пластика, который называется акрилонитрилбутадиенстиролом (АБС). Их состав практически не изменился за более чем 50 лет, сообщает Times .
Обновление материала будет непростым делом для Lego. Их новые экологически чистые игрушечные блоки должны выглядеть и действовать точно так же, как сегодняшние Lego. От этого зависит будущее компании. Вряд ли кто-то захочет покупать менее производительный продукт, даже если он лучше для окружающей среды.
Для начала компания начала выпуск некоторых заводских компонентов Lego. Ранее в 2018 году компания объявила, что «ботанические элементы» — также известные как деревья, листья и кусты Lego — будут производиться из пластика на растительной основе, полученного из сахарного тростника. Это больше похоже на аксессуары, а не на хлеб с маслом компании.
Но сами кирпичи еще не подверглись экологической переработке. Lego работает над этим. Это просто совершенно другая задача, и несколько устрашающая.
Самые большие препятствия на пути к устойчивому развитию Legos
Почему использование растительных материалов в Legos является такой сложной задачей? Представьте себе скромный кирпичик Лего. Или, на самом деле, это: представьте, каково это — ступить босиком по кубику Lego. Позвольте боли маленького прочного игрушечного кирпича толщиной 1,6 мм болезненно погрузиться в вашу ногу. Несмотря на то, что это больно, нельзя отрицать, что Лего в основном неразрушимы.
Лего могут выдержать бесчисленные часы, когда их кладут друг на друга, а потом разрывают на части в детском безумии.Они выживают, когда их бросают в гигантские урны и выбрасывают. Они выживают, когда на них наступают.
И все это благодаря прочному материалу на основе пластика. К сожалению, большинство переработанных и экологически чистых материалов слишком мягкие и податливые. Они не могут противостоять такому же износу, как сегодняшние пластиковые блоки Lego.
Компания Lego экспериментировала с более прочными материалами, но иногда они ломаются, оставляя острые края, которые совершенно не летают с детскими игрушками. Сохранение фирменных цветов Lego — тоже непростая задача.Яркие красные, синие и желтые цвета часто выглядят размытыми при использовании материалов на растительной основе.
Несмотря на то, что Lego еще не нашла подходящий материал для выполнения своего обещания по производству экологически чистых кирпичей к 2030 году, Тим Брукс, вице-президент по экологической ответственности, сказал, что они не перестанут пытаться, пока не получат все правильно. Lego ежегодно выбрасывает миллион тонн углекислого газа. Треть этой суммы приходится на сырье, которое фабрики используют для производства Lego. Брукс сказал Times , что компания стремится создать игрушку, которая не ставит под угрозу будущее детей.
Мнения, выраженные здесь обозревателями Inc.com, являются их собственными, а не мнениями Inc.com.
ПЕРВЫЙ УСТОЙЧИВОЙ КИРПИЧ LEGO® БУДЕТ ВЫПУЩЕН В 2018 ГОДУ — О нас
Строим будущее детей по кирпичику
LEGO Group заключила партнерские отношения с WWF для поддержки и повышения спроса на пластик из экологически чистых источников и присоединилась к Альянс биопластического сырья (BFA), инициатива WWF, направленная на обеспечение полностью устойчивых источников сырья для индустрии биопластиков.Пластик на растительной основе, используемый для изготовления ботанических элементов LEGO, сертифицирован третьей стороной в соответствии с мировыми стандартами для сахарного тростника, полученного из ответственных источников.
«Очень важно, чтобы компании в каждой отрасли находили способы ответственно использовать материалы для своей продукции и помогать обеспечивать будущее, в котором процветают люди, природа и экономика», — сказала Аликс Грабовски, старший программный директор WWF. «Решение LEGO Group заняться производством пластмасс на основе биопласта из экологически чистых источников представляет собой невероятную возможность снизить зависимость от ограниченных ресурсов, а их сотрудничество с Альянсом биопластикового сырья позволит им связаться с другими компаниями, чтобы продолжать творчески мыслить об устойчивости.”
Об элементах LEGO, изготовленных из растений
• Полиэтиленовые элементы составляют 1-2% от общего количества пластиковых элементов, производимых LEGO Group; Ассортимент экологически чистых продуктов включает в себя ботанические элементы LEGO®, такие как листья, кусты и деревья, полностью сделанные из пластика растительного происхождения.
• Полиэтилен растительного происхождения, используемый в элементах LEGO, сделан из этанола, полученного из сахарного тростника.
• Используемый сахарный тростник получен из экологически чистых источников в соответствии с рекомендациями Альянса по биопластическому сырью (BFA) и сертифицирован в соответствии с мировыми стандартами для сахарного тростника, полученного из ответственных источников.
• Все поставщики должны соблюдать Кодекс поведения LEGO Group, который устанавливает строгие требования в отношении этических норм, стандартов охраны окружающей среды, здоровья и безопасности, основанные на ведущих мировых нормах.
• LEGO Group тесно сотрудничает со своими поставщиками, чтобы обеспечить проведение оценок жизненного цикла, которые отображают воздействие на окружающую среду от производства биоматериалов.
Что такое экологичный материал?
Общепринятого определения экологически безопасного материала не существует.Несколько аспектов влияют на устойчивость материала. Он в значительной степени определяется его источником, химическим составом, его использованием (в продукте) и управлением (в конце срока службы), а также воздействием, которое он может оказать как на окружающую среду, так и на социальную сферу.