виды, классы теплостойких веществ, свойства и применение в домашних условиях
В основе производства огнеупорных материалов лежит определённое минеральное сырьё. В их структуре не происходит изменений при длительной эксплуатации или механическом воздействии, поэтому огнеупоры часто используют в разных сферах строительства и производства. Конструкции в результате работы получаются долговечными, надёжными и безопасными.

Свойства материалов
Жаростойкие материалы благодаря своим физическим свойствам широко применяются в сферах обработки металлов. Огнеупоры используются во время плавки, обжига, испарения, отжига и дистилляции на производстве. Изначальные свойства сохраняются даже под воздействием высоких температур, отсюда и название этих материалов.
Уже отработанные огнеупоры называют ломом. Их отправляют на переработку и создают из получившегося сырья новые изделия. Их основные физические показатели заключаются в прочности при воздействии огня, горячей жидкости или пара, а также в химической инертности.
В составе огнеупоров обязательно содержатся керамические смеси тугоплавкого оксида, силиката, нитрида, борида и карбида.
Классификация огнеупоров
Огнестойкие материалы принято классифицировать по размерам, формам и способу производства.

Общепринятые размеры и формы включают:
- прямые огнеупоры огромных и незначительных размеров;
- клиновые изделия нормальных габаритов;
- фасонные простые;
- специальные сложные;
- крупноблочные огнеупоры массой более 60 кг;
- вещества промышленного и лабораторного назначения, к которым относят тигли и трубы.
Различают несколько видов теплостойких материалов в зависимости от способа формирования, в результате которого получают огнеупоры.
В этом видео вы узнаете подробнее об огнеупорных материалах:
Таких видов несколько:
- прессованные термопластичные материалы;
- горячее прессование;
- электрическая плавка, литье из пеношликера или жидкого сырья для получения литых огнеупоров;
- обработка предварительно подготовленных блоков из естественных горных пород дает пиленые материалы.
Использование специальной машинной формовки и последующего прессования даёт эластичные огнеупоры. Сырьём могут послужить специальные массы, которые находятся в пластичном состоянии.
При производстве сначала тщательно подготавливают сырьё, обогащают его минеральными веществами, убирают из него посторонние примеси. После этого его измельчают, просеивают и готовят смеси, строго придерживаясь определённой дозировки. Смесь разливают по формам, обсушивают и обжигают. Сырьё выбирают по химическому и минералогическому составу.
В зависимости от плотности готовых изделий выделяют такие виды:
- максимально пористые;
- высокопористые;
- низкоплотные;
- среднеплотные;
- уплотнённые.
Область применения
Теплостойкие материалы используют для оборудования печи, обшивки стен производственных помещений, возведения приусадебных построек. Малопористые огнеупоры с высокими показателями подходят для конструирования печей в банях, зданиях пищевой промышленности.

В строительстве жилых помещений применяют листовые изделия. Особенно популярен сейчас гипсокартон. Им обшивают стены, оформляют конструкции сложных форм, возводят полки, межкомнатные перегородки и шкафы. Но этот материал нельзя использовать в помещениях с высоким уровнем влажности, т.к. гипсокартон от воздействия воды размокает. Листовые огнеупоры легко поглощают шум, просто монтируются, обладают минимальным уровнем кислотности.
Для строительства стен подойдёт огнеупорный бетон. Это изделие с высокой пористостью, чаще всего его применяют для теплоизоляции. Материал продаётся в виде порошка. Достаточно смешать порошок с жидкостью, покрыть им строительный материал, из которого возведены стены. Кроме защиты от пожаров, бетон предохранит помещение от проникновения громких звуков и попадания влаги.
Подробнее о новых огнеупорных технологиях:
Баню и другие постройки на участке лучше изготовить из огнеустойчивого кирпича, т.к. обычное строительное сырьё крошится из-за воздействия пара и горячего воздуха. Высокая температура внутри помещения часто приводит к деформации и расширению строительного материала. Кирпич не поддаётся этому воздействию. Производители предлагают сырьё в форме прямоугольника и клина. Первый вариант необходим в строительстве торцевых стен, второй применяют как ребровое изделие.

Несгораемый материал изготавливают с применением обжига и без него. В первом случае сырьё подвергают воздействию температуры свыше +600°С — только так возможно добиться нужных физических и химических свойств. Огнеупорные порошковые смеси уплотняют, вводя органические или минеральные вязкие вещества.
свойства огнестойких керамических материалов для бани и дымохода. Какие считаются кислыми? Классификация и основные виды
Огнеупорные материалы отличаются стабильностью структуры при воздействии высоких температур, пламени и химических веществ. Они используются на промышленных предприятиях, где производственный цикл предполагает применение теплового воздействия, а также в жилых домах, где установлены нагревательные приборы. За счет высоких эксплуатационных параметров такие материалы особенно актуальны на любых объектах, к которым предъявляются требования долговечности, надежности и безопасности.
Особенности
Потребность в применении огнестойких материалов появилась еще на самых ранних стадиях развития человечества, когда люди научились добывать и использовать огонь. Постепенно такие материалы становились основой для строительства сталеплавильных, доменных печей и прочего теплового оборудования.
Основное свойство подобных материалов — огнеупорность. Этот показатель определяет температуру, при которой изделие начинает деформироваться. Относительно его значения рассматривается эффективность эксплуатации материала в тех или иных видах работ. Кроме того, рассчитываются и другие характеристики, в частности:
- особенности поведения материала под действием повышенных температур;
- изменение формы и нарушение целостности при температурном воздействии;
- устойчивость структуры, которая определяется параметром механического усилия на сжатие при нагреве;
- сила реакции на воздействие агрессивных химических растворов.
Как правило, к огнестойким относятся материалы, которые выдерживают нагрев от 1580 до 3000 градусов Цельсия.
Любые огнеупорные изделия производятся на основе сочетания искусственного и натурального сырья, для этого подбираются оптимальные концентрации минеральных и химических компонентов.
Итоговые показатели плотности, прочности, а также пористости и структуры определяются применением конкретной технологии.
Классификация
Изделия, устойчивые к воздействию открытого огня, могут выпускаться в разных формах и с разными свойствами. Выделяют несколько оснований для их классификации.По огнеупорности
По огнестойкости выделяют материалы:
- обычные огнеупорные – выдерживают от +1580 до +1770 градусов Цельсия;
- высокоогнеупорные – до 2 тыс. градусов;
- изделия с высокой огнеупорностью – до 3 тыс. градусов;
- сверхогнеупорные – должны выдерживать нагрев свыше 3 тыс. градусов.
Самым огнестойким материалом в мире является карбонитрид гафния – температура его плавления составляет 4200 градусов Цельсия.
По способу формования
Существует несколько основных способов формовки огнеупорных материалов:
- жидкое литье;
- формовка из мягких составов с дальнейшей допрессовкой;
- формовка из спрессованных порошков;
- распил горных пород;
- способ горячего прессования;
- техника термопластического прессования;
- формовка из раскаленного расплава.
По химико-минеральному составу
Для создания огнестойких изделий используют несколько типов сырья.
- Органическое – эти разновидности продукции изготавливают из минерального сырья. Большая часть таких изделий может выдерживать существенный нагрев. Единственным исключением являются пенополистиролы. Они имеют слабую стойкость к огню, однако из них можно выложить печь со слабым прогревом.
- Неорганическое – самая внушительная категория продуктов с широким диапазоном огнеупорности. Сюда относят базальтовую и минеральную вату, стекловолокно, перлит и вермикулит.
- Композитное – к данной категории относят изделия из асбеста (асбестоцементные либо асбестоизвестковые составы), а также вспененные кремнеземные изделия.
В зависимости от основного действующего вещества различают несколько видов огнеупорных материалов.
- Огнеупоры, содержащие оксиды алюминия, спеченные в блоки, называют кислыми – основа в этом случае достигает 90% от общего количества массы. К данной группе относят муллитовые, а также шамотные кирпичи, которые считаются идеальным решением для печей и каминов, работающих на натуральном топливе.
- Магнезиальные – такие изделия изготавливают из оксидов разных металлов методом спекания при нагреве. Блоки отличаются устойчивостью к агрессивным растворам и могут выдерживать нагрев до 2000 градусов.
- Минеритовые – выпускаются с применением экологичного сырья. До 90% состава приходится на армированные цементы. При нагревании эти изделия немного увеличиваются в размерах, поэтому во время монтажа нужно оставлять между пластами небольшие зазоры.
- Асбестовые – плиты и панели из асбеста продолжительное время использовались в строительстве. Однако некоторое время назад было выявлено токсичное воздействие асбеста на здоровье человека. Вещества, входящие в состав материала, являются канцерогенами и приводят к онкологическим заболеваниям. Тем не менее огнестойкость таких изделий исключительно высока. Материала может на протяжении нескольких часов выдерживать нагрев до 500 градусов, не меняя прочности и плотности.
Обшивка такими панелями используется в технических сооружениях, при этом требует обязательного покрытия экологичными материалами.
- Суперизол – материал из силиката кальция, он легковесный и хорошо поддается резке. Суперизол выдерживает нагрев до 1000 градусов, при этом имеет сниженную теплопроводность. Это востребованный при монтаже перегородок и защитной отделки стен материал.
К минусам относят хрупкость: при механическом воздействии такие изделия бьются.
- Стекломагниевые панели – это материал, состоящий из хлористого магния, стеклоткани и вспученного перлита с добавлением синтетических волокон. Обладает высокой адгезией, пониженной теплопроводностью, к тому же легко обрабатывается.
- Вермикулит – плиты на базе силикатной слюды, смешанной с синтетическими компонентами. Это экологичный и нетоксичный материал, удерживающий тепло. К минусам относят низкую влагостойкость, поэтому при эксплуатации требуется дополнительная защита от воды.
- Металические экраны – листовой огнестойкий материал со светоотражающей поверхностью. Такие изделия не только защищают стены от чрезмерного перегрева, но и позволяют поддерживать комфортную температуру в помещении, отражая его внутрь.
Обычно такие листы изготавливают из нержавеющей стали.
- Клинкер – этот керамический материал изготавливают из мелкопористой глины. Он отличается стойкостью к перепадам температур, способностью выдерживать не только огонь, но и сильные морозы.
- Керамогранит – материал на основе мраморной, гранитной и кварцевой крошки с присутствием солей и окислов металла. Отличается способностью выдерживать нагрев до 100 и более градусов, характеризуется высокой влагостойкостью.
По пористости
В зависимости от степени открытости пор выделяют:
- до 3% — сверхплотные;
- до 10% — высокоплотные;
- до 16% — плотные;
- до 20% — уплотненные;
- до 30% — среднеплотные;
- до 45% — низкоплотные;
- до 75% — высокопористые;
- более 75% — ультапористые.
Формы и размеры
Огнеупорные материалы предлагаются в разных формах и размерах:
- клиновые либо прямые – могут иметь малые, нормальные или крупные размеры;
- фасонные, простые, а также сложные – с массой свыше 60 кг.
Наибольшую востребованность получили листовые панели. Их функциональное предназначение зависит от габаритов и набора эксплуатационных характеристик продукции. Они незаменимы для футеровки котельных, домашних каминов, печных блоков, является теплоизоляционным для колонок, котлов, а также отопительных систем в банях и саунах. Выполняют роль защитных экранов и повышают производственный эффект оборудования в целом и его отдельных частей.
Формовочная и порошкообразная продукция актуальна в приборостроении. Она решает задачу регулировки эксплуатационного режима в соответствии с ТУ. Неформованное сырье идет на изготовление одежды сотрудников литейных цехов.
Сферы применения
Все виды огнестойких материалов повсеместно используются в промышленной сфере. Они задействованы в цветной и черной металлургии – на эту сферу приходится порядка 60% изделий из жаростойких материалов в целом, а также в изготовлении керамики и стекла. Огнестойкие составы являются основой для изготовления кислото- и теплоизоляторов. Ими облицовывают производственные печи, а также другие установки с открытым пламенем.
В быту такие изделия нашли применение при обустройстве каминов и печек, мангалов и дымоходов. Эти отделочные материалы получили широкое распространение при возведении и обустройстве зданий. Они применяются при выполнении обивки потолков и стен в помещениях. Подобное решение многократно повышает пожарную безопасность конструкции, поэтому их используют в сооружениях с повышенными требованиями по ППБ.
Важно иметь в виду, что большая часть строительных огнестойких материалов не могут противостоять возгоранию, поэтому могут гореть. Выделяют жаростойкие и огнеупорные изделия. Последние могут длительное время выдерживать источник открытого пламени на близком расстоянии – они широко востребованы при строительстве бань и саун.
Жаростойкие материалы могут выдержать интенсивный нагрев, но открытый огонь нарушает их структуру.
Жаропрочные, жаростойкие и композиционные материалы
К таким материалам относятся:
- тугоплавкие металлы;
- спеченные сплавы тугоплавких металлов;
- дисперсно-упрочненные материалы;
- волокнистые композиционные материалы.
Тугоплавкие металлы
К тугоплавким металлам относятся цирконий, гафний, ванадий, ниобий, тантал, хром, молибден, вольфрам, рений. Наибольшее применение в качестве высокотемпературных конструкционных материалов нашли вольфрам, молибден, тантал, ниобий. В последнее время все шире применяются хром, ванадий и рений, которые хотя и менее тугоплавки, но благодаря своим специфическим свойствам начинают играть большую роль в производстве жаропрочных материалов.
Технология получения тугоплавких металлов включает получение порошков, формование заготовок и дальнейшая обработка.
Так, изделия из спеченного вольфрама изготовляют из порошка, полученного восстановлением водородом вольфрамового ангидрида или карбонильным методом. Порошки прессуют в стальных пресс-формах. Для улучшения прессуемости к порошку добавляют смазывающие и склеивающие вещества. Процесс спекания изделий проводят в две стадии. Первую стадию осуществляют в водороде при сравнительно для вольфрама, невысоких температурах (1100 –1300 °С). Вторую стадию спекания проводят при
температурах 2900 –3000 °С, которая создается пропусканием электрического тока через изделие, упрочненное предварительным спеканием. Эту стадию спекания, получившую название «сварка», осуществляют в водороде в специальных печах, которые называют сварочными аппаратами. Режим спекания в этом случае обычно контролируют не измерением температуры, а величиной пропускаемого тока. Крупногабаритные заготовки спекают в индукционных печах при температурах 2400 –2500 °С.
Аналогичная технология изготовления изделий из порошка молибдена. Порошок, полученный восстановлением молибдена водородом прессуют, как правило, со смазкой. Предварительное спекание проводят в водороде при 1100 –1200 °С. Затем изделия подвергаются сварке при силе тока, составляющей 90% от силы тока переплавки, что соответствует 2200 –2400 °С.
Спекание крупных заготовок можно проводить в вакуумной методической печи с графитовыми нагревателями, позволяющей обеспечить одновременно предварительное и окончательное спекание при температурах 1900 –1950 °С.
При изготовлении танталовых изделий исходный порошок, полученный натриетермическим восстановлением или электролизом, прессуют в заготовки. Перед прессованием в порошок тантала вводят раствор глицерина в спирте или какую-нибудь другую жидкую связку, которая при спекании удаляется полностью. Спекание заготовок проводят в вакууме. Заготовки предварительно спекают при 1000 –1200 °С. Спеченные заготовки охлаждают вместе с печью. Сварку проводят в вакууме, подбирая режим таким образом, чтобы обеспечить полное разложение и испарение примесей. При температуре сварки 2600 –2700 °С делают выдержку до полного удаления всех газов.
Заготовки после сварки охлаждают в вакууме и проковывают. Затем проводят вторичное спекание (отжиг) в вакуумном сварочном аппарате. В результате такой обработки получается беспористая заготовка с плотной структурой.
Аналогично рассмотренному получают спеченный ниобий и рений.
Изделия из порошков циркония и ванадия изготавливают по схожим технологиям. Порошки прессуют в пресс-формах и заготовки спекают в вакууме. Циркониевые заготовки спекают при 1200 – 1300 °С, а ванадиевые – при 1400 –1700 °С.
Спеченные сплавы тугоплавких металлов
Спеченные сплавы тугоплавких металлов обладают более высоким комплексом механических свойств при повышенных температурах чем чистые тугоплавкие металлы. Повышение этих свойств достигается легированием.
Структура большинства жаропрочных сплавов на основе тугоплавких металлов представляет собой гетерогенные сплавы, основой которых является твердый раствор. Упрочение при легировании объясняется тем, что в результате взаимодействия растворенных атомов с дислокациями происходит закрепление или блокирование дислокаций. В многих сплавах на основе тугоплавких металлов, содержащих повышенное количество примесей внедрения, образуются избыточные фазы типа карбидов, нитридов и других соединений, которые также способствуют упрочению сплавов.
Повышение свойств сплавов тугоплавких металлов достигается также применением термической обработки, заключающейся в закалке с высоких температур с последующим старением при температурах, близких к рабочим. В этом случае карбиды, нитриды и другие химические соединения, образуемые металлами (титан, цирконий, тантал, ниобий) с элементами внедрения, выполняют роль фаз — упрочнителей.
Известны порошковые вольфрамоникелевые сплавы, применяемые для изготовления ракетных сопел, а также ванадиевые сплавы, используемые для изготовления деталей, работающих при температурах до 1250 °С. Свойства сплавов приведены в таблице 1.
Состав | Твердость | Предел прочности, МПа при температуре, °С | ||
20 | 1100 | 1200 | ||
V+20%Nb+5%Ti+0,5%C | 3400 | – | 235 | 140 |
V+20%Nb+5%Ti+0,5%C+0,1%B | 4800 | 760 | 280 | 225 |
V+20%Nb+3%Ti+0,5%C+0,1%B | 3900 | – | 363 | 179 |
V+10%Nb+7%Ti+10%Ta+5%Mo+0,5%C | 3400 | 670 | 405 | – |
Высокотемпературная прочность спеченных ванадиевых сплавов не уступает прочности литых аналогичного состава, а в некоторых случаях и превосходит их.
Дисперсно-упрочненные материалы
Дисперсноупрочненные материалы представляют собой композиционные спеченные материалы, содержащие искусственно вводимые в них высокодисперсные, равномерно распределенные частицы фаз, не взаимодействующих с матрицей и не растворяющихся в ней до температуры ее плавления.
Наиболее эффективное упрочение обеспечивается при содержании упрочняющей фазы в количестве 3 – 15%, размере ее частиц до 1мкм и среднем расстоянии между ними 0,1 –0,5 мкм.
Дисперсноупроченные материалы сохраняют микрогетерогенное строение и дислокационную структуру, а следовательно, и работоспособность до 0,9–0,95 Tпл матрицы. Высокая работоспособность дисперсноупроченных материалов при повышенных температурах объясняется тем, что при наличии в матрице второй фазы скольжение дислокаций в зернах металла становится возможным при больших напряжениях, границы зерен блокируются, а рост зерен затормаживается практически до температуры плавления матрицы.
При создании дисперноупроченных материалов выбирают фазу–упрочнитель и способ введения ее в матрицу.
Фаза–упрочнитель должна иметь высокую термодинамическую прочность, малую величину скорости диффузии компонентов фазы в матрицу, высокую чистоту и большую суммарную поверхность частиц. К упрочняющим фазам с такими свойствами относятся оксиды некоторых металлов (чаще всего Al2O3, SiO2, ThO2, ZrO2, Cr2O3), карбиды, нитриды и другие соединения.
Способ введения частиц фазы–упрочнителя в матрицу влияет на структуру дисперсно-упрочненного материала, которая может быть дисперсной или агрегатной. Способами введения фазы–упрочнителя и получения смеси является:
- механическое смешивание порошков оксидов металла и упрочняющей фазы с последующим восстановлением оксидов основного металла;
- механическое смешивание порошков металла матрицы и упрочняющей фазы;
- поверхностным окислением порошка основного металла;
- химическое смешивание, предусматривающее совместное осаждение солей и их последующее восстановление с образованием металла и сохранением фазы–упрочнителя;
- внутренним окислением или азотированием порошков.
Первые три метода приводят к образованию агрегатной структуры, а последние два – к дисперсной.
В настоящее время разработаны и применяется целый ряд дисперсно-упрочненных материалов. В различных отраслях техники успешно используются:
- алюминиевые,
- вольфрамовые,
- молибденовые,
- железные,
- медные,
- кобальтовые,
- хромовые,
- никелевые,
- бериллиевые,
- платиновые сплавы.
Дисперсно-упрочненные алюминиевые сплавы
В алюминиевых сплавах в качестве упрочняющей фазы используется оксид алюминия Al2O3, легко образующийся в результате высокой склонности алюминия к поверхностному окислению и позволяющий получать равномерное распределение его в матрице. Содержание упрочняющей фазы (Al2O3) обычно находится в пределах 4 – 14%.
Длительная прочность дисперсно-упрочненных алюминиевых сплавов, называемых сплавами САП (спеченные алюминиевый порошок), при повышенных температурах превосходит прочность всех деформируемых алюминиевых сплавов. Все сплавы хорошо обрабатываются, их можно сваривать и паять.
Алюминиевые сплавы применяются в авиационной технике (обшивка гондол силовых установок в зоне выхлопа, жалюзи).
Вольфрамовые сплавы упрочняют обычно оксидами тория (ThO2) в количестве 0,75–2,0%. Для повышения прочности и пластичности при низких температурах вводят рений в количестве 3–5%.
Дисперсно-упрочненные вольфрамовые сплавы
Дисперсно-упрочненные вольфрамовые сплавы широко используют в ракетно–космической технике.
Молибденовые сплавы упрочняют карбидами, нитридами, оксидами. Карбидное упрочнение дает возможность получить сплавы с высоким пределом прочности при температуре 1400 °С. При температурах выше 1500–1600 °С эти сплавы сильно разупрочняются из-за рекристаллизации.
Упрочнение сплава оксидом тория (ThO2) дает высокий эффект даже в рекристализованном состоянии, а легированние вольфрамом и упрочнение карбидом тантала (TaС) дает возможность получения сплава с высокими механическими свойствами при температурах 1600–2000 °С.
Дисперсно-упрочненные молибденовые сплавы
Дисперсно-упрочненные молибденовые сплавы применяются в авиационной технике. Упрочненные железные сплавы получают введением в железо около 6% Al2O3. Это обеспечивает хорошие прочностные характеристики сплавов при температурах 650–950 °С. Более высокие свойства имеют дисперсноупрочненные стали. Так, хромоалюминиевая сталь, упрочненная Al2O3, и сложнолегированная, упрочненная TiO2, имеют характеристики при температуре 650 °С почти вдвое выше, чем упрочненные железные сплавы.
Дисперсно-упрочненные стали
Дисперсно-упрочненные стали превосходят литые по длительной прочности. Кроме того, в них снижается эффект охрупчивания под действием облучения. Поэтому они используются в реакторостроении, даже если они не имеют преимуществ перед стандартными материалами по прочности.
Дисперсно-упрочненные медные сплавы
Медные упрочненные сплавы получают путем введения оксидов алюминия, бериллия и тория. Для сохранения электропроводности и пластичности содержание оксидов недолжно превышать 1,5–2,0%.
Дисперсно-упрочненная медь обладает высоким сопротивлением ползучести и высокой жаропрочностью, что позволяет использовать ее для изготовления деталей, работающих при повышенных температурах (детали теплообменников, электровакуумных приборов). Медь, содержащая включения тугоплавких соединений, применяется для изготовления электродов точечной и роликовой сварки.
Дисперсно-упрочненные кобальтовые сплавы
При получении кобальтовых сплавов в качестве упрочняющей фазы применяют в основном оксид тория (ThO2) с содержанием последнего 2–4%. Так, временное сопротивление кобальтовых сплавов с 2% ThO2 составляет 1020 МПа при 25 °С и 140 МПа при 1090 °С.
Для повышения пластичности сплавы кобальта легируют никелем, а для повышения окалиностойкости – хромом.
Никелевые сплавы получают путем упрочнения никеля оксидами тория (ThO2) или гафния (HfO2). Содержание упрочняющей фазы составляет 2–3%.
Дисперсно-упрочненные никелевые сплавы
Дисперсно-упрочненные сплавы никеля очень технологичны. Их можно ковать, штамповать, вытягивать в широком интервале температур. Они обладают хорошей жаростойкостью и используются для изготовления деталей газовых турбин.
Дисперсно-упрочненные хромовые сплавы
При получении дисперсно-упрочненных хромовых сплавов следует иметь ввиду, что хром при комнатной температуре имеет повышенную хрупкость, и температура перехода в пластичное состояние зависит от количества и формы примесей внедрения и размера зерна. Измельчение зерна при введении дисперсной фазы положительно влияет на технологические свойства хрома.
В качестве упрочняющей фазы могут использоваться оксиды тория (ThO2) и оксиды магния (MgO).
Положительно влияют на жаропрочность дисперсно-упрочненного хрома добавки марганца, молибдена, тантала, ниобия.
Дисперсно-упрочненные бериллиевые сплавы
Дисперсно-упрочненные бериллиевые сплавы получают путем введения оксида бериллия (BeO), используя склонность к поверхностному окислению промышленных бериллиевых порошков.
Высокое сопротивление ползучести достигается при упрочнении сплавов карбидом бериллия (Be2C). При содержании 2,5% Be2C величина 100σ возрастает в 3 раза при 650°С по сравнению с чистым бериллием.
Дисперсно-упрочненные бериллиевые сплавы обладают высокой прочностью, высоким модулем упругости и большим коэффициентом рассеивания нейтронов.
Дисперсно-упрочненные платиновые сплавы
Платиновые сплавы хорошо работают при высоких температурах в окислительной среде. Упрочнение их осуществляется оксидами (ThO2) или карбидами (TiС), содержание которых для сохранения пластичности должно быть минимальным.
Дисперсно-упрочненные платиновые сплавы используются для изготовления нагревателей, термопар и термометров сопротивления.
Волокнистые композиционные материалы
Волокнистые композиционные материалы состоят из матрицы, которая содержит упрочняющие элементы в форме волокон (проволоки) или нитевидных кристаллов.
В волокнистых материалах матрица скрепляет волокна в единый монолит, защищая их от повреждений. Она является средой, передающей нагрузку на волокна, а в случае разрушения отдельных волокон перераспределяет напряжения.
Особенность волокнистой композиционной структуры заключается в равномерном распределении высокопрочных волокон в пластичной матрице. Объемная доля волокон может колебаться от 15 до 25%. Поверхности раздела в волокнистых композиционных материалах рассматриваются как самостоятельный элемент структуры в которой происходят процессы растворения, образования и роста новых фаз. Здесь формируется связь между упрочняющим волокном и матрицей. От совершенства такой связи зависит уровень свойств волокнистых композиционных материалов.
В качестве методов получения композиционных материалов используются горячее прессование, пропитку жидким металлом, электроосаждение, экструдирование и прокатку, сварку взрывом, эвтектическую кристаллизацию.
В настоящее время наиболее широко применяются волокнистые композиционные материалы на основе алюминия, магния, титана и никеля.
На основе алюминия можно получить волокнистые композиции алюминий-сталь, алюминий-молибден, алюминий-карбид кремния, алюминий-углерод и другие.
Композиционный материал алюминий-сталь получают сваркой взрывом или горячим прессованием. Упрочняющим материалом является высокопрочная стальная проволока.
Разработана технология получения композиционных материалов на основе алюминия, легированного магнием и кремнием, армированного нитевидными кристаллами.
Технология получения композиции алюминий-углерод состоит в пропитке волокон углерода жидким металлом. Для обеспечения смачивания и ограничения взаимодействия между матрицей и волокном используют покрытия из борида титана, никеля, меди, тантала и других соединений. Покрытые волокна протягивают через расплав. Композиционные материалы, полученные пропиткой волокон углерода, покрытые боридом титана имеют σВ=1120 МПа.
Композиционные материалы на магниевой основе получают методами горячего прессования или диффузионной сварки, непрерывного литья, пропитки жидким металлом, плазменного напыления с последующим прессованием, методом сварки взрывом.
Для армирования магния применяют высокопрочную стальную и титановую проволоку, волокна бора и углерода, нитевидные кристаллы карбида кремния.
Магниевые сплавы как матрицы композиционных материалов практически не реагируют с основными классами армирующих волокон, что позволяет применять для получения композиционных материалов жидкофазные технологии и является большим преимуществом этих сплавов.
Материал магний–бор (Mg–B), полученный методом непрерывного литья, заключающегося в пропускании армирующих волокон бора через ванну расплавленного магния и последующего формирования заготовки путем прохода пучка покрытых волокон через кристаллизатор-фильеру, имеет σВ=963 МПа при объемной доли волокон 0,30 и σВ=1330 МПа при объемной доли 0,75.
Титановые композиционные материалы изготавливаются при довольно высоких температурах (800–1000 °С). Наиболее распространенными упрочнителями для титановой матрицы являются волокна бора, молибдена, бериллия, карбида кремния, оксида алюминия.
Композиционный материал Ti–B, полученный методом диффузионной сварки при температуре 800–880 °С имеет σВ=900 МПа при объемной доли волокон 0,36.
Никелевые композиции изготавливают методами обработки давлением, пропитки раствором и порошковой металлургии.
В качестве матрицы чаще всего служат жаростойкие никелевые сплавы типа ХН60В и ХН77ТЮР, а упрочнителей – вольфрамовые волокна. Наиболее распространенным методом изготовления никелевых композиционных материалов является горячая прокатка.
ПОДЕЛИСЬ ИНТЕРЕСНОЙ ИНФОРМАЦИЕЙ
российские учёные создали самый огнеупорный материал в мире — РТ на русском
Материаловеды МИСиС создали керамический материал карбонитрид гафния, способный выдерживать рекордную температуру 4200 °C. Это подтверждают результаты компьютерного моделирования, предсказавшего огнеупорные свойства и высокую твёрдость такого материала. Ранее самым тугоплавким веществом с температурой плавления 3990 °C считался карбид тантала-гафния. После окончания пандемии коронавируса учёные планируют провести эксперимент, который определит температуру плавления нового материала.
Материаловеды Национального исследовательского технологического университета МИСиС создали самый огнеупорный в мире керамический материал карбонитрид гафния, способный выдержать температуру 4200 °C. Об этом сообщается в журнале Ceramics International.
До настоящего времени карбид тантала-гафния с температурой плавления 3990 °C считался самым огнеупорным соединением, созданным человеком. На идею создания более тугоплавкого вещества материаловедов МИСиС натолкнуло исследование американских коллег 2015 года, в котором с помощью компьютерного моделирования были предсказаны исключительные температурные свойства и высокая твёрдость композитного соединения гафния, углерода и азота. По расчётам исследователей из США, это вещество должно выдерживать примерно 4200 °C, отличаться высокой теплопроводностью и стойкостью к окислению.
«Для получения нового материала была использована тройная система гафний-углерод-азот. Методом самораспространяющегося высокотемпературного синтеза мы получили вещество карбонитрид гафния — насыщенный азотом карбид гафния», — сообщил в беседе с RT автор работы, директор научно-исследовательского центра конструкционных и керамических наноматериалов МИСиС Дмитрий Московских.
Также по теме
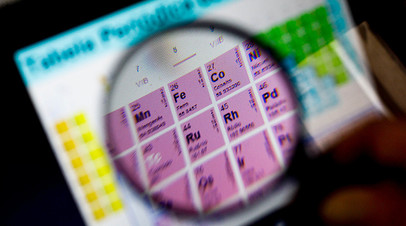
Сотрудники химического факультета Московского государственного университета открыли новые интерметаллиды — соединения из рения, галлия…
Далее учёные сравнили плавкость двух материалов: исходного карбида гафния (плавится при 3990 °C) и полученного карбонитрида гафния. С помощью аккумулятора и молибденовых электродов они провели в глубоком вакууме одновременный нагрев двух материалов. В результате карбид оплавился, а карбонитрид остался в неизменном виде. Однако на данный момент, отмечают учёные, конкретную температуру плавления нового материала выше 4000 °С им определить не удалось.
Чтобы подтвердить все свойства нового материала, предсказанные компьютерным моделированием, учёным необходимо провести дополнительные эксперименты. Для этого, по словам Дмитрия Московских, было заключено соглашение с Объединённым институтом высоких температур РАН о проведении пирометрического анализа, который был отложен из-за пандемии COVID-19.
После снятия ограничений намечено проведение исследования, во время которого карбонитрид гафния будет расплавлен лазером с одновременным измерением теплофизических свойств, включая температуру плавления.
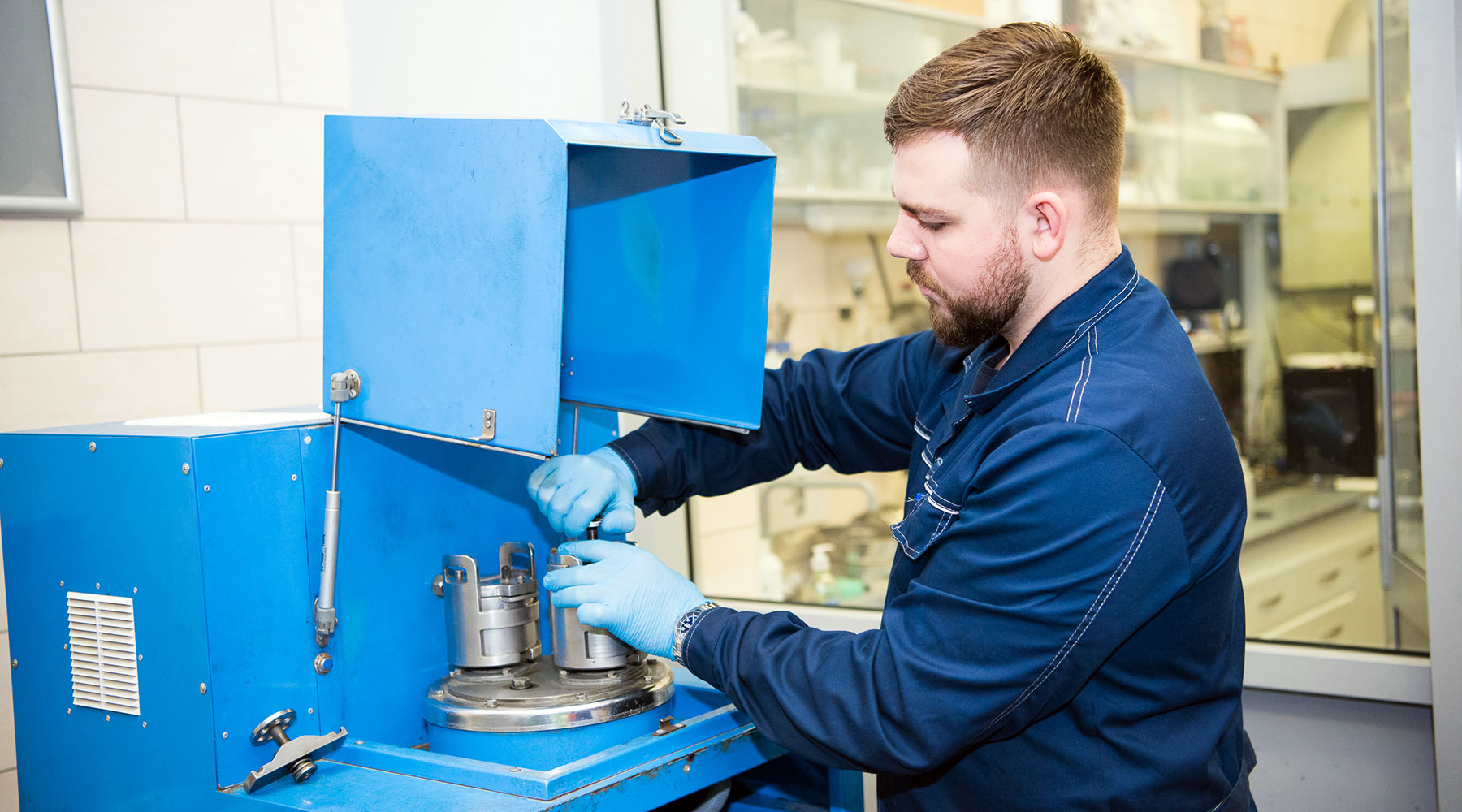
- Предварительные исследования показали, что карбонитрид гафния способен выдержать температуру 4200 °C
- © НИТУ МИСиС
По мнению учёных, разработка подобных высокотемпературных материалов будет востребована при создании авиационной, ракетно-космической и специальной военной техники. На гиперзвуковой скорости и при прохождении через атмосферу Земли двигатели, крылья и носовые обтекатели летательных аппаратов работают при температурах выше 2000 °С и должны быть защищены от воздействия внешней среды. В таких аппаратах применяется керамическая теплозащита с использованием наиболее прочных и тугоплавких композитных материалов.
В дальнейшем для проверки возможности применения карбонитрида гафния в аэрокосмической промышленности запланировано гиперзвуковое исследование для изучения абляции — испарения внешних слоёв материала.
асбестовые, базальтовые, кварцевые, кремнеземные и углеродные
Просмотров: 3 125
Негорючая ткань – это специальный тип материала, обеспечивающий эффективную защиту от действия высоких температур и открытого пламени.
Благодаря специальному составу она может относительно длительное время пребывать в огне или под тепловым излучением, не меняя своих характеристик, сохраняя защитные свойства.
Широкую популярность огнеупорные материалы получили в таких отраслях:
- металлургическая;
- энергетическая;
- химическая;
- нефтеперерабатывающая;
- производство спецодежды и пр.
Область применения огнеупорных тканей
Негорючая строительная ткань широкое практическое применение получила в роли теплоизоляционного материала, защищающего от пламени, теплового потока.
Благодаря тепловой и механической устойчивости она активно используется в роли прокладочного материала в разных промышленных отраслях.

Спецодежда для сталеваров
Область применения огнезащитного полотна также распространяется на отрасль по производству спецодежды. Из него выпускаются защитные костюмы пожарных, сталеваров, работников нефтеперерабатывающих заводов, химических лабораторий.
Огнеупорные ткани для спецодежды – это гарантированная защита человека от теплового воздействия в случае его пребывания в области возгорания, взрыва, сильного теплового облучения.
Виды негорючих тканей
Для решения перечисленных выше задач по защите от теплового излучения и открытого огня существует несколько типов огнеупорных материалов. Рассмотрим кратно их основные особенности.
Асбестовые
Для производства асбестовых спецтканей используют природные силикаты, которые отличаются очень тонкими волокнами и могут использоваться в качестве теплозащитного материала.

Огнеустойчивая асбестовая ткань
Асбест является устойчивым к температурам вплоть до +500ºС, характеризуется хорошими изоляционными свойствами и рассчитан для применения в качестве противопожарной кошмы и материала для придания огнеустойчивости строительным конструкциям.
Использовать огнеупорные асбестовые ткани для пошива одежды не рекомендуется, поскольку они выделяют асбестовые микрочастицы, которые вредны человеку при их вдыхании. Только дополнительная обработка может исключить этот недостаток, но это приведет к существенному удорожанию спецодежды.
Кварцевые
Для получения этого противопожарного полотна используют волокна, вытягиваемые из натурального кварца при высоких температурах.
Материал из кварцевых нитей выдерживает температурный режим в пределах до +1400ºС без изменения структуры, рабочих характеристик. При длительном пребывании в огне он может выдержать даже температуру в +2000ºС.

Кварцевая огнеупорная ткань
Кварцевая ткань получила широкое применение в энергетической и химической отрасли в качестве технического материала, а также для пошива огнезащитной одежды. Основным ее преимуществом является максимальная безопасность для человека.
Базальтовые
Эти спецткани производятся из волокон базальта, получаемых методом расплавления и вытягивания. Огнезащитное полотно с базальтовой основой способно выдерживать температуру до +700ºС.

Базальтовая огнезащитная ткань
Также выпускается и нетканый материал, который получил широкое применение в качестве огнезащиты различных металлоконструкций, а также в роли материала, которым заполняют пустоты противопожарных преград.
Кремнеземные
Кремнеземные негорючие ткани по своему составу напоминают кварцевые огнеустойчивые материалы. Отличие между ними заключается в том, что кремнеземное полотно содержит меньше диоксида кремния.
Вследствие этого оно способно выдерживать несколько меньшие температуры – до +1200ºС. Изменение характеристик материала и его разрушение начинается с температур +1800ºС.

Кремнеземная огнеустойчивая ткань
Кремнеземная спецткань полностью безопасна для человека. Она используется для огнеустойчивых и изоляционных покрытий, для создания защит из негорючей ткани для печей.
Углеродные
Спецткань этого типа производится с помощью классических ткацких технологий. Для этого используются длинные и короткие углеродные нити, получаемые из полиакрилонитрила и вискозы.
Углеволокно устойчиво к повышенным температурам, химическим препаратам и растяжению.

Углеродная огнеупорная ткань
Оно отличается небольшим весом, поэтому активно используется для пошива защитной одежды, которая будет эксплуатироваться при температурных режимах, не превышающих +370ºС.
Арамидные
Арамидная огнеупорная ткань производится из арамидных нитей, которые сплетают особым образом, создавая специальную структуру полотна. Нити могут переплетаться саржевым, полотняным, вафельным или атласным способом.

Армидная огнезащитная ткань
Благодаря такому сложному строению спецткани она характеризуется высокой устойчивостью к механическим повреждениям. Кроме этого, материал устойчив к высоким температурам – выдерживает нагревание в пределах +250…400°С, а кратковременно – температуру около +1000°С.
Полиэфирные
При добавлении соединений фосфора к волокну, синтезированному из полиэфиров, оно становится термоустойчивым и способным противостоять горению.
Для производства полиэфирных тканей используются разные плетения, в результате чего получается молескин, бархат, репс, жаккард и др.

Полиэфирная огнезащитная ткань
Эти материалы имеют приятный вид и хорошие защитные свойства от высокой температуры. При попадании изделий из полиэфирной ткани в область открытого пламени она не плавится, слегка обугливается, не выделяя вредных веществ.
Пропитка
Существует еще один подход к производству огнеустойчивых спецтканей, позволяющий любому материалу придать огнеустойчивость. Он основан на пропитывании волокон специальным веществом, не поддерживающим горение.
Этот метод технологически прост и не требует больших финансовых вложений.

Огнезащитная пропитка для ткани «Огнеза»
Единственным его недостатком является потеря со временем эффекта огнеустойчивости. Пропитки хватает приблизительно на год, после этого требуется дополнительная обработка.
Преимущества и недостатки
К основным преимуществам огнеупорных материалов относятся:
- защищают от теплового потока;
- не горят в открытом пламени;
- кратковременно выдерживают тепловой удар в несколько тысяч градусов;
- устойчивы к механическим повреждениям;
- защищают от химических веществ;
- имеют увеличенную биозащиту;
- устойчивы к воздействию влаги.
Кроме положительных сторон, огнезащитные материалы имеет несколько недостатков. Есть некоторые ткани, которые:
- при нагревании могут выделять токсичные вещества;
- меняют свои характеристики под воздействием прямых солнечных лучей;
- в процессе эксплуатации выделяют микрочастицы, опасные для дыхательной системы человека.
Если правильно применять огнеупорную спецткань для ее целевого предназначения, то действие всех перечисленных недостатков на организм человека можно полностью исключить.
Заключение
Большой выбор огнеупорных тканей с различными характеристиками позволит использовать их в разных отраслях деятельности человека.
Потребительский рынок насыщен предложениями огнезащитных тканей для спецодежды, бытового или промышленного применения.
Благодаря широкому распространению такого рода материалов обеспечивается эффективная защита от теплового излучения и прямого контакта с огнем живых организмов, увеличивается пожарная безопасность объектов.
Видео: Проверка огнестойкости базальтовой ткани
Огнестойкий материал в Набережных Челнах
Огнестойкий материал — описание
Огнестойкие материалы – изделия на основе минерального сырья, отличающиеся способностью сохранять свои свойства в условиях эксплуатации при высоких температурах, и которые служат в качестве конструкционных материалов и защитных покрытий.
Наименование материала в наличии
Кремнеземные высокотемпературные материалы
- ШНУРЫ БАЗАЛЬТОВЫЕ ТЕПЛОИЗОЛЯЦИОННЫЕ ШБТ-Б
- Шнур Вати корд 600 — крученный, безасбестовый, керамичемкий, негорючий. Температура применения до 1100С. Диаметр: 6, 10, 20 мм
- ЛЕНТА ЖАРОСТОЙКАЯ КРЕМНЕЗЕМНАЯ КЛ-11 + 1 200 С
- ТКАНЬ ЖАРОСТОЙКАЯ КРЕМНЕЗЕМНАЯ + 1 200 С
- ЦИЛИНДРЫ из каменной ваты PAROC + 750 С
- КАРТОН МКРК — 350 МУЛЛИТОКРЕМНЕЗЕМИСТЫЙ
Огнестойкий материал температура от +700 до +1300 С
- Маты прошивные PAROC
- ТКАНЬ ЖАРОСТОЙКАЯ БАЗАЛЬТОВАЯ + 700 С
- Фольмо – холст + 800 С
- Материал базал + фольга МБФ
- КЕРАБЛАНКЕТ
- ВОЙЛОК МКРВ — 200 огнеупорный
- КАРТОН гибкий МКРКГ — 400
- КАРТОН МКРК- 350 МУЛЛИТОКРЕМНЕЗЕМИСТЫЙ
- КАРТОН МКРКЛ-450
- ПЛИТА фиброцементная ФЛАММА
- Мастика клеящая жаростойкая
В Теплофирме Джоуль широкий ассортимент огнестойких материалов, жаростойкой изоляции. Ниже можно ознакомиться с продукцией, которая у нас в наличии по оптимальным ценам.
Сырье для огнестойких материалов — простые и сложные оксиды (например, SiO2, A12O3, MgO, ZrO2, MgO-SiO2), бескислородные соединения (например, графит, нитриды, карбиды, бориды, силициды), а также оксинитриды, оксикарбиды, сиалоны.
Для изготовления огнеупоров используют разнообразные технологии и процессы. Преобладающей является технология, включающая предварительную, тепловую обработку и измельчение компонентов, приготовление шихт с добавлением пластифицированных составляющих, формование из них изделий прессованием на механических и гидравлических прессах или экструзией с последующей допрессовкой или литьем, обжиг в туннельных, реже в периодических и газокамерных печах для получения заданных свойств материала.
Эксплуатационные свойства огнестойких материалов определяются комплексом химических, физико-химических и механических свойств.
Основное свойство огнеупорных изделий — огнеупорность, т.е. способность изделия противостоять, не расплавляясь, действию высоких температур. Огнестойкость характеризуется температурой, при которой стандартный образец из материала в форме трехгранной усеченной пирамиды высотой 30 мм и сторонами оснований 8 и 2 мм (конус Зейгера) размягчается и деформируется так, что его вершина касается основания. Определенная таким образом температура обычно выше максимально допустимой температуры эксплуатации огнеупорных материалов.
Волокнистые огнеупоры — теплоизоляционные, состоящие из волокон огнеупоры в виде формованных (плиты, блоки, листы и др.) с неорганической или органической связкой и неформованных (вата, войлок и др.) изделий. Волокнистые огнеупоры изготовляют преимущественно из высоко-глиноземного и глиноземного стекловолокна и из корундового, поликристалличического волокна, а также из ZrO2 и др. оксидов.
Волокнистые огнеупоры применяют для теплоизоляции и футеровки тепловых агрегатов, а также для заполнения компенсационных швов.
Динасовые огнеупоры — содержат > 93% SiO2 или 80-93% SiO2 (при изготовлении с добавками) и изготовливаются из кварцитов. В порошок кварцита добавляют известковое молоко и железистые добавки, формуют на прессах изделия задан, размеров и обжигают при 1430-1460°С.
Динасовые огнеупоры применяют для футеровки коксовых, стекловар, печей, воздухонагревателей, а также ряда плавильных агрегатов в ЦМ и др. Неформованные динасовые огнеупоры — мертели, материалы для обмазок и т.п. изготавливают из молотых боя динас, огнеупоров и кварцитов, применяют при выполнении и ремонте кладки.
ТЕРМО — Огнестойкие материалы
Пена монтажная противопожарная 750 мл |
Герметик жаростойкий 310 мл + 1500 С |
Клей жаростойкий тюб 17 мл + 1200 С |
ЦИНК Жаростойкий 400 мл + 300 С |
КРАСКА ЖАРОСТОЙКАЯ 400 мл + 800 С |
Характеристика кремнеземных материалов
Кремнеземные материалы имеют низкую теплопроводность, высокую стойкость к тепловому удару, обладают превосходными электроизоляционными свойствами при высоких температурах, могут длительно использоваться без изменения свойств при температуре 1000 0С и кратковременно при более высоких температурах (не плавятся, не испаряются при температурах до 1700 0С). Изделия из кремнеземного стекла чрезвычайно инертны к большинству химических реагентов, стойки к органическим и минеральным кислотам любых концентраций даже при повышенной температуре (за исключением плавиковой, фосфорной, соляной) и слабым щелочам расплавленных металлов (кроме Mg, Na, Si) и сплавам. Обладают высокой химической стойкостью к воде и пару высокого давления, способны поглощать влагу, но не расщепляются в присутствии воды, стабильны в вакууме.
Преимущества кремнеземных материалов
Кремнеземные материалы являются превосходными высокотемпературными теплоизоляционными материалами и применяются в качестве заменителя асбеста во многих отраслях промышленности.
- Высокотемпературные материалы — кремнеземные шнуры, ткани, ленты.
- Термостойкие ткани, кремнеземные сетки, термостойкие ленты
- Иглопробивные полотна, иглопробивные маты Supersil.
- Противопожарные и дымозащитные шторы, изделия для сварочных работ
- Нестандартные термостойкие изделия и материалы
Теплотехнические характеристики огнеупорных и теплоизоляционных материалов :: Огнеупорные материалы в металлургии
ТЕПЛОТЕХНИЧЕСКИЕ ХАРАКТЕРИСТИКИ ОГНЕУПОРНЫХ МАТЕРИАЛОВ
Огнеупорность определяется как температура Тогн, при которой происходит деформация стандартного образца в форме усеченной пирамиды при отсутствии механического и физико-химического воздействия. Огнеупорные изделия подразделяют на три группы: средней огнеупорности (огнеупорные) – Тогн до 1770 °С; высокой огнеупорности (высокоогнеупорные) Тогн от 1770 °С до 2000 °С, высшей огнеупорности – Тогн – выше 2000 °С. Предельная рабочая температура службы огнеупоров в условиях эксплуатации Tmax значительно ниже, чем Тогн.
В таблице 1 приведены свойства наиболее широко используемых печных огнеупоров. Все огнеупоры характеризуются такими важными эксплуатационными показателями, как термостойкость, шлакоустойчивость, строительная прочность, изменение объема при нагреве, которые определяют их применение для строительства элементов печей.
Термостойкостью называют способность огнеупоров выдерживать циклическое изменение температур при нагреве и охлаждении, так называемые теплосмены. Термостойкость характеризуют числом теплосмен до потери 20% первоначальной массы огнеупора в результате образования трещин и скалывания.
Шлакоустойчивость характеризует способность огнеупора выдерживать воздействие жидкого шлака и металла, окалины, газов.
Динас содержит более 93% SiO2 и относится к кремнеземистым, кислым огнеупорам. Обладает высокой строительной прочностью, высокой температурой начала деформации под нагрузкой и соответственно рабочей температурой службы 1650–1700 °С. Устойчив к воздействию кислых расплавов и газовых сред, но не выдерживает контакта с основными расплавами металлов и их оксидов. Термостойкость динаса по стандартной методике не превышает 1-2 водяных теплосмен. Однако, если колебания температуры происходят в области значений выше 300 °С и особенно выше 600 °С, то термостойкость динаса исключительно высока.
Динас широко применяют для изготовления высокотемпературной части насадки доменных воздухонагревателей и регенераторов нагревательных колодцев, которая не охлаждается ниже 600 °С, для кладки распорных сводов.
Таблица 1 – Свойства огнеупоров, наиболее широко используемых в печах
| Группа огнеупоров | Главные хим. компоненты в % (мас.) | Тогн, °С | Tmax, °С | Плотность – r, т/м3 | Коэф. теплопроводности – l, Вт/(м×К) при 100 °С | Уд. теплоемкость – с, кДж/(кг×К) при 100 °С |
1 | Динасовые | SiO2>93 | 1690-1720 | 1650-1700 | 1,84-1,97 | 1,3 | 0,86 |
2 | Шамотные | 30<Al2O3<45 | 1580-1750 | 1200-1400 | 1,83-1,95 | 0,9 | 0,9 |
3 | Муллитовые | 62<Al2O3<72 | 1600-1800 | 1600-1650 | 2,34-2,52 | 1,2 | 0,86 |
4 | Корундовые | Al2O3>90 | 1950-2000 | 1650-1800 | 2,89-3,12 | 2,1 | 0,83 |
5 | Смолодоломитовые | 50<MgO<85 | 1800-1900 | 1300-1400 | 2,7-2,8 | 3,4 | 0,96 при 1000°С |
6 | Периклазовые (магнезитовые) | MgO>85 | 2200-2400 | 1650-1700 | 2,6-2,8 | 4,5 | 1,08 |
7 | Периклазохромитовые | MgO>60 | 2000 | 1650-1700 | 2,95-3,04 | 2,5 | 1,0 |
8 | Хромитопериклазовые | 40<MgO<60 | 1920-2000 | 1700 | 2,9-3,15 | 2,0 | 1,8 ¸ 1,15 |
9 | Цирконовые | ZrO2>50, | 2000-2300 | 1900-2000 | 3,48-3,83 | 1,4 | 0,64 |
10 | Карбидкремниевые | SiC>70 | 2000 | 1800-2000 | 2,35-2,54 | 9,3 при 1000°С | 0,97 |
Шамот относится к алюмосиликатным огнеупорам, содержащим кроме SiO2 до 45% Al2O3. Обладает более высокой термостойкостью (10-20 водяных теплосмен), но низкой шлакоустойчивостью. Наиболее широко применяется в печестроении при температурах до 1350 °С для строительства стен, сводов, не контактирующих с оксидами металлов, для низкотемпературной части регенеративной насадки. Не выдерживает истирающего действия при высоких температурах.
Муллит и корунд относятся к высокоглиноземистым алюмосиликатным огнеупорам. По мере увеличения содержания Al2O3 повышается их рабочая температура службы, прочность и постоянство объема при разогреве. Термостойкость превышает 150 водяных теплосмен. Применяются вместо шамота в условиях более высоких температур: муллит – до 1650 °С, корунд – до 1800 °С. Плавленые корундовые изделия обладают высокой шлакоустойчивостью и выдерживают давление и истирающее действие металла и шихты. Применяются в установках внепечной обработки стали, в монолитных подинах методических нагревательных печей, в качестве насадки шариковых регенераторов.
Периклаз (или магнезит) содержит не менее 85% MgO. Температура начала размягчения под нагрузкой значительно ниже огнеупорности. Максимальная рабочая температура 1700 °С. Термостойкость изделий невысока и составляет 1-2 водяных теплосмены.
Шлакоустойчивость по отношению. к основным расплавам – металлам и шлакам, богатым оксидами металлов и известью, исключительно высока. Поэтому магнезитовые кирпичи используются для кладки элементов печей черной и цветной металлургии, которые контактируют с расплавами металлов и основных шлаков. Магнезитовый порошок используют для заполнения швов при кладке подин плавильных печей.
Периклазохромитовые и хромитопериклазовые огнеупоры содержат в качестве основы MgO и хромит Cr2O3. Свойства этих огнеупоров существенно отличаются от периклазовых и зависят от соотношения хромита и магнезита. Максимальная термостойкость соответствует отношению Cr2O3:MgO = 30:70. Шлакоустойчивость выше при содержании хромита 20 %. В сводах сталеплавильных печей наибольшую стойкость имеют изделия с содержанием хромита 20-30 %. Они изнашиваются из-за образования трещин и сколов, к которым приводят термические напряжения, возникающие при колебании температуры в рабочем пространстве печи.
Смолодоломитовые безобжиговые огнеупоры содержат в качестве основы MgO и СаО, а также углерод в виде смоляной связки в количестве 2-4 %. Они применяются для футеровки конвертеров. Известь СаО взаимодействует с силикатами конвертерного шлака, благодаря чему на поверхности футеровки образуется гарниссаж, препятствующий проникновению шлака в футеровку.
Углеродистые огнеупоры изготавливаются из доступного сырья – графита, кокса – с высокой температурой плавления ³ 3500 °С. Они не смачиваются расплавами и поэтому устойчивы против них, имеют высокую термостойкость, но начинают окисляться в продуктах горения топлива при температуре ³ 600 °С. Поэтому их используют для службы в восстановительной среде: в электрических печах для производства ферросплавов, алюминия, свинца, в лещади доменных печей, в качестве припаса для разливки металлов, для изготовления электродов дуговых плавильных печей.
Карбидкремниевые огнеупоры содержат в качестве главного компонента SiC – карборунд. Они покрыты защитной плёнкой SiO2, поэтому не окисляются как углеродистые. Имеют высокую прочность, износоустойчивость, термостойкость. Устойчивы против нейтральных и кислых расплавов, нестойки против основных. Применяются для изготовления трубок керамических рекуператоров, огнеупорных муфелей.
Неформованные огнеупоры применяют для изготовления монолитных футеровок из огнеупорного бетона и набивных масс. Огнеупорный бетон представляет собой смесь огнеупорного наполнителя (бой огнеупорных изделий) с размером частиц от 0,5 до 70 мм, вяжущего и добавок. В качестве вяжущего используют твердеющие в холодном состоянии огнеупорные цементы (глиноземистый, магнезиальный), жидкое стекло, фосфатные связки на основе ортофосфорной кислоты Н3РО4. Добавки могут регулировать скорость схватывания и твердения, улучшать пластические свойства, уменьшать усадку.
Широко распространены динасовые бетонные блоки и панели для стен нагревательных колодцев, глинистокварцитовые массы для набивной футеровки ковшей. Применяют монолитную футеровку стен и сводов нагревательных печей из жидкого (литого) бетона с креплением её к металлическому каркасу печи с помощью анкерных кирпичей, распределенных по площади стен и свода.
Защитные гарниссажи образуются на рабочей поверхности ограждения плавильных, шахтных и дуговых печей из спекающихся или расплавленных материалов при интенсивном охлаждении стен печи водой или воздухом. В плавильных печах цветной металлургии гарниссаж является эффективным средством защиты, а иногда и замены футеровки.
ТЕПЛОТЕХНИЧЕСКИЕ ХАРАКТЕРИСТИКИ ТЕПЛОИЗОЛЯЦИОННЫХ МАТЕРИАЛОВ
Для тепловой изоляции металлургических печей применяются три вида изделий: 1) легковесные пористые огнеупорные кирпичи: шамот-легковес, динас-легковес, диатомитовый и другие; 2) теплоизоляционные засыпки; 3) изделия в виде плит, ваты, войлока, картона, изготовленные на основе керамического волокна в смеси со связующим материалом, так называемые волокнистые огнеупоры. Волокнистые огнеупоры являются относительно новыми теплоизоляционными материалами.
Легковесные огнеупорные кирпичи обладают большой пористостью и поэтому меньшей плотностью и теплопроводностью, чем обычные огнеупорные кирпичи (табл. 2). Марка кирпича в табл. 2 расшифровывается так: Д – динас, Ш – шамот, Л – легковес, числа после тире означают плотность. Чем меньше плотность кирпича, тем лучше его теплоизоляционные свойства, но ниже максимальная рабочая температура.
По сравнению с обычными огнеупорами шамот-легковес и другие легковесы имеют более низкую прочность, шлакоустойчивость и термостойкость. Их можно применять не только для теплоизоляционного слоя футеровки, но и для рабочего слоя, в термических печах. Диатомитовый кирпич применяют только для наружного слоя тепловой изоляции стен и свода нагревательных печей.
Таблица 2 – Свойства легковесных огнеупорных изделий
№пп | Тип и марка изделия | Плотность – r, т/м3 | Т мах, раб, °С | Коэф. теплопроводности – l, Вт/(м×К) | Уд. теплоемкость – с, кДж/(кг×К) в интервале 0‑1400 °С |
1 | Динас ДЛ-1,2 | 1,2 | 1500 | 0,58+0,38×10-3×t | 1,19 |
2 | Шамот ШЛ-1,3 | 1,3 | 1350 | 0,47+0,14×10-3×t | 1,19 |
5 | Диатомитовый кирпич | 0,5 | 1000 | 0,15 (при t=350 °С) | 1,0 |
В качестве засыпок используются, в основном, естественные теплоизоляционные материалы: диатомит, инфузорная земля, трепел и вермикулит. Первые три материала имеют состав SiO2×nH2O.
Диатомит – продукт разложения водорослей, имеет рыхлую землистую структуру. Применяют в виде порошка или изделий, изготовленных на глинистой связке: плотность изделий 500, 600 и 700 кг/м3, коэффициент теплопроводности соответственно равен 0,18, 0,21, 0,27 Вт/(м×К). Коэффициент теплопроводности засыпки из диатомита колеблется в пределах 0,12-0,16 Вт/(м×К). Предельная температура применения диатомитовых изделий 1000 °С, засыпки 900 °С.
Инфузорная земля является продуктом разложения животных организмов; применяют чаще в виде порошка.
Трепел – продукт выветривания горных пород, пористый материал с низкой теплопроводностью; применяют в виде порошка или изделий. По свойствам изделия из трепела близки к диатомитовым.
Вермикулит — это разновидность слюды, имеющая способность при нагреве значительно увеличивать свой объем. Используют вермикулит в виде засыпки или в виде плит. Применяется до температуры 700-900 °С. В обожженном виде носит название – зонолит. Предельная температура применения зонолита 1000-1100 °С. Коэффициент теплопроводности вермикулита и зонолита 0,1 Вт/(м×К).
К неогнеупорным изоляционным материалам относится асбест. Асбест является водным силикатом магния состава 3MgO×2SiO2×2H2O, имеет волокнистое строение, пористый. Применяют в виде крошки для засыпки или в виде изделий – шнура, картона, плит, ткани и ваты.
НОВЫЕ МАТЕРИАЛЫ, КОТОРЫЕ ИСПОЛЬЗУЮТСЯ В МЕТАЛЛУРГИЧЕСКИХ ПЕЧАХ
В таблице 3 представлены некоторые виды волокнистых огнеупорных изделий и их свойства. Волокнистые плиты, как и шамот-легковес, применяют для изготовления не только изоляционного, но и рабочего слоя футеровки термических печей с целью снижения потерь теплоты в рабочем пространстве печи. При этом уменьшаются два вида потерь: на аккумуляцию теплоты футеровкой и теплопроводностью через футеровку в окружающую среду.
Таблица 3 – Виды волокнистых огнеупорных изделий
№ пп | Тип и марка изделия | Толщина, мм | Плотность – r, т/м3 | Т мах, раб, °С | Коэф. теплопроводности – l, Вт/(м×К) при 600 °С | Уд. теплоемкость – с, кДж/(кг×К) |
1 | Плита ШПГТ-450 | 100 | 0,45 | 1300 | 0,2 | 1,0 |
2 | Вата МКРР-130 | 15; 20 | 0,13 | 1250 | 0,22 | 1,0 |
3 | Войлок МКРВЦ-150 | 15; 20 | 0,15 | 1400 | 0,14 | 1,0 |
4 | Фетр МКРВЦФ-130 | 15; 20 | 0,13 | 1400 | 0,18 | 1,0 |
Термостойкие материалы для печей — огнеупоры для каминов
Реставрация и строительство каминов и печей
При открытых огнях, использующих газ или твердое топливо, продукт, называемый огнеупорным цементом, может использоваться для мелкого ремонта швов и трещин. Более крупный ремонт можно выполнить, используя штукатурку для камина или жаропрочную стяжку, продукты, способные выдерживать очень высокие температуры. Если вам нужно закрепить плитку в той части камина, которая подвергается воздействию тепла, вы можете использовать термостойкий клей для плитки.
Если вы строите новый камин или открываете каминную трубу, чтобы создать его, вы можете выложить проем огнеупорным кирпичом, установленным на месте с жаростойким раствором, или использовать каминную доску. Швы раствора должны быть тонкими: от 3 до 5 мм. Вообще говоря, на 10 кг жаростойкого раствора можно уложить 100 огнеупорных кирпичей стандартного размера. В качестве альтернативы вы можете выполнить рендеринг поверх существующей кирпичной кладки с помощью Fireplace Render до толщины примерно одного дюйма. Жаростойкая стяжка также может использоваться для создания основы для очага пожара.Отдельностоящие печи также могут быть облицованы средством Fireplace Render.
Кассетные камины (иногда называемые пожарами с «дырками в стене») должны иметь область вокруг отверстия для огня, облицованную термостойкой штукатуркой, которая предназначена только для этих типов каминов. Термостойкая штукатурка наносится на штукатурку камина. Его можно наносить толщиной до 5 мм.
Специальные продукты для каминов
Вы также можете приобрести ряд других термостойких продуктов для каминов.Специальные растворы и клеи с высоким содержанием кремнезема предназначены для использования с шамотным кирпичом, каминными плитами, керамическим волокном и изоляционным кирпичом. Также доступны огнеупорные растворы с высоким содержанием глинозема, используемые с кирпичами с высоким содержанием алюминия. Цементы и растворы с самым высоким содержанием глинозема также подходят для использования с магнезиальным или хромовым кирпичом.
Огнестойкие цементы премиум-класса выпускаются в бежевом / желтовато-коричневом или черном цвете и могут использоваться для различных целей как внутри страны, так и в промышленности.
Наиболее распространенные применения огнестойкого цемента:
- ремонт каминов,
- сборка чугунных печей.
Используемые продукты Vitcas
Полный набор продуктов, необходимых для постройки открытого камина.
Завод по производству термостойких материалов, OEM / ODM производственная компания по изготовлению термостойких материалов на заказ
Всего найдено более 2000 заводов и компаний по производству жаропрочных материалов, выпускающих более 6000 товаров. Выбирайте высококачественные термостойкие материалы на нашем большом количестве заводов по производству надежных термостойких материалов. Золотой членТип бизнеса: | Производитель / Завод |
Основные продукты: | Изоляция зданий, крышка от солнечных батарей для бассейна |
Mgmt.Сертификация: | ISO 9001, SEDEX |
Собственность завода: | Общество с ограниченной ответственностью |
Объем НИОКР: | Собственный бренд, ODM, OEM |
Расположение: | Циндао, Шаньдун |
Тип бизнеса: | Торговая компания |
Основные продукты: | Огнеупоры, теплоизоляция материалы , строительные материалы , керамические изделия |
Mgmt.Сертификация: | ISO 9001, ISO 9000 |
Собственность завода: | Общество с ограниченной ответственностью |
Объем НИОКР: | OEM, ODM |
Расположение: | Цзыбо, Шаньдун |
Тип бизнеса: | Производитель / Завод |
Основные продукты: | Пена XPE, пена IXPE, мат, доска для серфинга, спортивные товары |
Mgmt.Сертификация: | ISO9001: 2008 |
Собственность завода: | Общество с ограниченной ответственностью |
Объем НИОКР: | ODM, OEM |
Расположение: | Шэньчжэнь, Гуандун |
Тип бизнеса: | Производитель / Завод , Торговая компания |
Основные продукты: | Теплоизоляция, Излучающий барьер, Изоляция из алюминиевой фольги с пузырьками , материал , Ламинированная бумага, Упаковочные материалы |
Mgmt.Сертификация: | ISO9001: 2008, ISO14001: 2004 |
Собственность завода: | Общество с ограниченной ответственностью |
Объем НИОКР: | Собственный бренд, OEM |
Расположение: | Ханчжоу, Чжэцзян |
Тип бизнеса: | Производитель / Завод , Торговая компания |
Основные продукты: | Устойчивый к износу Керамическая футеровка, керамическая труба из глинозема, коленчатая плитка, глиноземная керамическая футеровка, керамический резиновый состав, керамическая резиновая сталь, керамическая футеровка Zta |
Mgmt.Сертификация: | ISO 9001, ISO 9000, ISO 14001, ISO 14000, OHSAS / OHSMS 18001 |
Собственность завода: | Общество с ограниченной ответственностью |
Объем НИОКР: | OEM, ODM, собственный бренд |
Расположение: | Пинсян, Цзянси |
Тип бизнеса: | Производитель / Завод |
Основные продукты: | Транспортная тележка |
Mgmt.Сертификация: | ISO9001: 2008 |
Собственность завода: | Общество с ограниченной ответственностью |
Объем НИОКР: | Собственный бренд |
Расположение: | Синьсян, Хэнань |